Transforming Gear Design and Simulation Skills with Creo
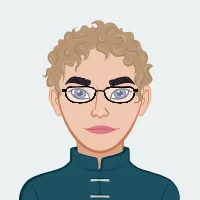
Complex gear assemblies are fundamental components in many mechanical systems, requiring a high level of precision and expertise to design, assemble, and simulate effectively. These assemblies are crucial in various applications, from automotive transmissions to industrial machinery, where accurate gear interaction ensures optimal performance and longevity. In this blog, we will explore the key steps and techniques to successfully create and analyze a complex gear design using Creo, a powerful CAD software widely used in the industry. Whether you're a student tackling an advanced assignment or a professional refining your skills, this comprehensive guide will help you understand the essential concepts, detailed methodologies, and best practices needed to achieve a fully functional and accurate gear assembly. By mastering these techniques, you can enhance your proficiency in mechanical design and simulation, ensuring your gear assemblies meet the highest standards of quality and reliability.
We will delve into the intricacies of designing various types of gears, such as bevel gears, helical gears, and worm gears, each with its unique specifications and challenges. Understanding the nuances of each gear type is crucial for creating a cohesive assembly where all components work seamlessly together. Additionally, we will cover the critical aspects of assembly constraints and how to apply them correctly to ensure proper alignment and interaction between the gears.
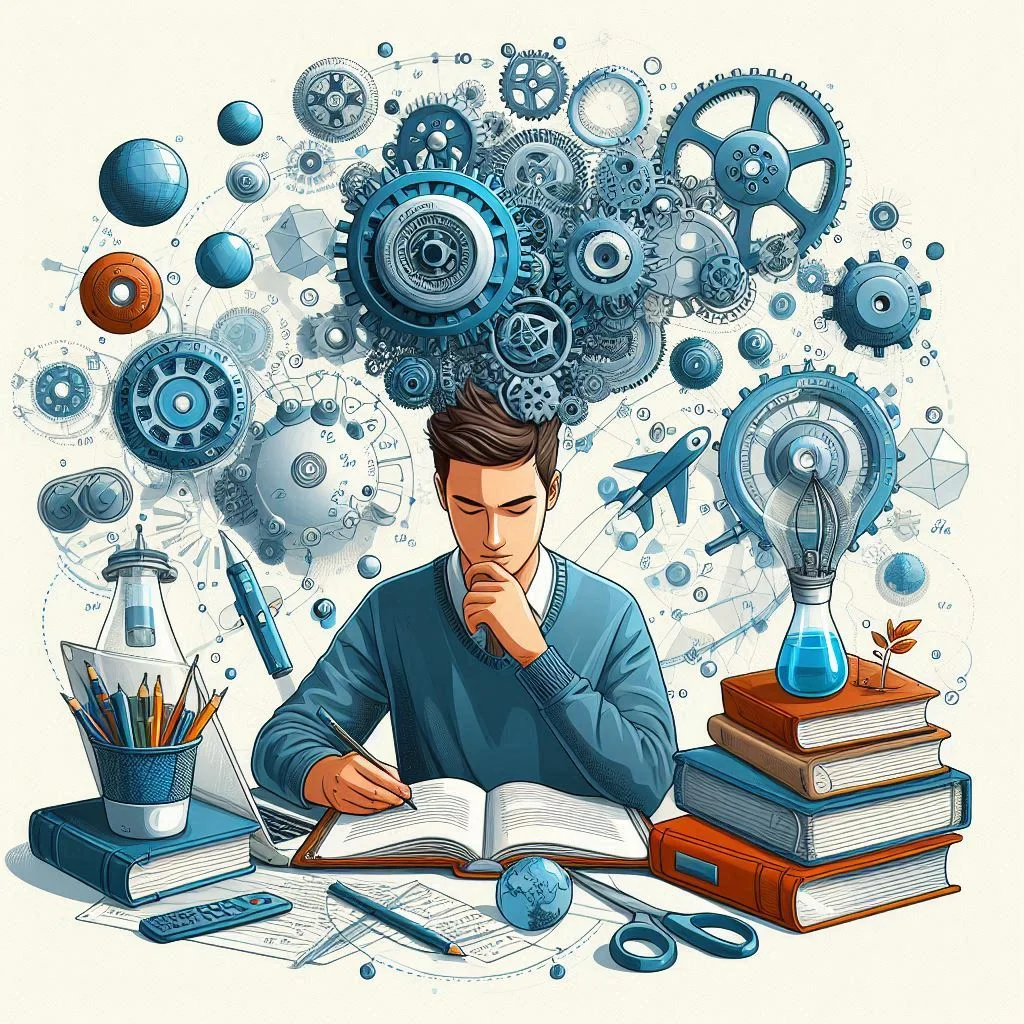
Motion analysis and simulation play a vital role in validating the design and functionality of the gear assembly. By setting up and running simulations in Creo, you can observe the behavior of the gears under different conditions, identify potential issues, and make necessary adjustments to optimize performance. This process not only enhances the accuracy of your designs but also provides valuable insights into the dynamics of gear interactions.
Documentation is another key element we will emphasize. Thoroughly documenting each step of the design, assembly, and simulation process is essential for communicating your work effectively, whether for academic purposes, professional development, or project collaboration. Detailed sketches, dimensioned drawings, and comprehensive reports ensure that every aspect of the project is well-documented and easy to understand.
By the end of this blog, you will have a solid foundation in the principles and practices of complex gear assembly design and simulation using Creo. Whether you are working on a specific Creo assignment or seeking to broaden your mechanical engineering skills, the knowledge and techniques shared here will be invaluable.
Step 1: Designing Individual Gears
Designing individual gears is a crucial first step in creating a complex gear assembly. Each gear must be meticulously designed to ensure it meets the required specifications and functions correctly within the assembly. In this section, we will focus on the design process for three types of gears: bevel gears, helical gears, and worm gears. Understanding the unique characteristics and requirements of each gear type is essential for creating a cohesive and efficient gear assembly. For those seeking mechanical engineering assignment help, mastering these design principles will be vital in delivering high-quality results.
Bevel Gear Design:
Specifications:
- Module: 4 mm
- Number of teeth: 20
- Pressure angle: 20°
- Face width: 15 mm
- Material: Steel
Design Process: Bevel gears are used to transmit power between intersecting shafts, typically at a right angle. To design a bevel gear in Creo, start by creating a detailed sketch that outlines the gear's basic profile. Use Creo’s parametric modeling tools to define the gear's dimensions precisely, ensuring the module, number of teeth, pressure angle, and face width are accurately represented. Material selection is also critical; steel is commonly chosen for its strength and durability.
Tips:
- Pay close attention to the gear’s pressure angle and module, as these parameters significantly affect the gear's meshing and performance.
- Use Creo’s gear design tools to automate part of the design process, ensuring accuracy and efficiency.
- Regularly check the gear's profile against the specifications to ensure all dimensions are correct.
Helical Gear Design:
Specifications:
- Module: 3 mm
- Number of teeth: 30
- Helix angle: 25°
- Face width: 20 mm
- Material: Aluminum
Design Process: Helical gears are known for their angled teeth, which provide smoother and quieter operation compared to spur gears. When designing a helical gear in Creo, the helix angle is a critical parameter. Start by sketching the gear’s base profile and then apply the helix angle to the teeth using Creo’s advanced modeling features. Define the module, number of teeth, and face width accurately. Aluminum is often chosen for helical gears due to its lightweight and corrosion-resistant properties.
Tips:
- The helix angle requires precise calculation and application to ensure the gears will mesh correctly with mating gears.
- Utilize Creo’s 3D modeling capabilities to visualize the gear and make adjustments as needed.
- Ensure the material properties are set correctly in Creo to simulate the gear’s performance accurately.
Worm Gear Design:
Specifications:
- Module: 2 mm
- Number of teeth on worm wheel: 40
- Lead angle of worm: 15°
- Material: Brass
Design Process: Worm gears are used to transmit motion between non-intersecting shafts that are typically at right angles. The design process for a worm gear and worm wheel in Creo involves creating the worm gear's helical thread and the mating worm wheel. Begin by designing the worm gear, focusing on the lead angle and thread profile. Next, design the worm wheel with the appropriate number of teeth. Brass is a preferred material for worm gears due to its good wear resistance and ability to reduce friction.
Tips:
- The lead angle is crucial for the worm gear’s proper functioning; calculate and apply it with precision.
- Use Creo’s thread creation tools to model the worm gear accurately.
- Verify that the worm wheel’s teeth mesh correctly with the worm gear by conducting preliminary checks in Creo.
Designing individual gears with precision is the foundation of a successful gear assembly. By understanding the specifications and utilizing Creo’s powerful design tools, you can create detailed and accurate gear models. Paying attention to the nuances of each gear type and following best practices in gear design will ensure that your gears will perform optimally within the assembly. In the next step, we will explore how to assemble these gears into a cohesive and functional system.
Step 2: Assembling the Gears
Assembling individual gears into a cohesive and functional gear assembly is a critical step in the design process. This phase involves creating a new assembly file in Creo, placing the gears in the appropriate configuration, and applying the necessary assembly constraints to ensure proper alignment and interaction. Proper assembly ensures that the gears will function as intended, transmitting motion smoothly and efficiently. Here, we will detail the process of assembling bevel, helical, and worm gears, focusing on key aspects and best practices.
Assembly Configuration:
Procedure:
1. Create a New Assembly File:
- Open Creo and create a new assembly file. This will serve as the workspace where you will bring together the individual gears designed in Step 1.
2. Import Individual Gear Models:
- Import the previously designed bevel gear, helical gear, and worm gear into the assembly workspace. Ensure that each gear is correctly oriented and positioned relative to the others.
3. Arrange Gears in Configuration:
- Position the bevel, helical, and worm gears in a configuration that demonstrates their interaction. This typically involves placing the gears at the correct angles and distances from each other to mimic their real-world applications.
Tips:
- Use Creo’s visualization tools to check the spatial arrangement of the gears, ensuring that they are placed in a realistic and functional configuration.
- Pay attention to the relative positions of the gears to ensure they will mesh correctly without interference.
Constraints and Connections:
Procedure:
1. Apply Assembly Constraints:
- Use Creo’s assembly constraints to align and position the gears accurately. Common constraints include coincident, parallel, perpendicular, and distance constraints. These constraints ensure that the gears are properly aligned and interact as intended.
2. Mating Constraints:
- Apply mating constraints to position the gears with the correct rotational and translational freedom. For example, use a coincident constraint to align the faces of two gears or a distance constraint to set the separation between gear centers.
Tips:
- Verify that the gears have the correct degrees of freedom. For instance, a gear should rotate about its axis without translating along it, unless specifically required.
- Double-check all constraints to ensure there are no conflicts or redundancies that could lead to misalignment or improper gear meshing.
Finalizing the Assembly:
Procedure:
1. Check Interferences:
- Use Creo’s interference check tool to identify any overlapping or conflicting parts within the assembly. Resolving these issues is crucial for the proper functioning of the gear assembly.
2. Refine Alignment:
Make any necessary adjustments to the assembly constraints to refine the alignment and interaction of the gears. Small tweaks may be required to achieve perfect meshing and smooth motion.
Tips:
- Regularly save your progress to avoid losing any work.
- Utilize Creo’s simulation tools to visualize the gear interactions dynamically, ensuring that they rotate and mesh as expected.
Assembling individual gears into a cohesive system requires careful planning, precise application of constraints, and thorough checking for interferences. By following these steps and utilizing Creo’s powerful assembly tools, you can create a functional and accurate gear assembly that performs as intended. Proper assembly not only ensures the gears will transmit motion smoothly but also sets the stage for successful motion analysis and simulation in the next step.
In the next part, we will dive into performing motion analysis and simulation to validate the design and ensure that the gears function correctly under various conditions.
Step 3: Performing Motion Analysis and Simulation
Motion analysis and simulation are vital steps in validating the design and functionality of your gear assembly. By setting up and running simulations in Creo, you can observe how the gears interact under different conditions, identify potential issues, and make necessary adjustments to optimize performance. This process ensures that your gear assembly will operate smoothly and efficiently in real-world applications. In this section, we will outline the steps to perform motion analysis and simulation, including setting up the simulation, running it, and analyzing the results.
Setting Up the Simulation:
Procedure:
1. Define Input Motion Parameters:
- Determine the input motion for the driving gear. This could be an angular velocity (e.g., revolutions per minute) or torque (e.g., Newton-meters). In Creo, you can specify these parameters in the simulation setup.
2. Establish Contacts and Constraints:
- Define the contacts between the gears to simulate realistic interactions. This includes specifying the type of contact (e.g., frictional, non-frictional) and ensuring that the gears will mesh correctly during motion.
- Reaffirm the assembly constraints applied during the gear assembly process. These constraints will dictate how the gears move relative to one another.
Tips:
- Double-check the input motion parameters to ensure they reflect the intended operating conditions of the gear assembly.
- Use Creo’s contact definition tools to accurately model the interactions between gear teeth.
Running the Simulation:
Procedure:
1. Set Up Motion Analysis:
- In Creo, navigate to the motion analysis module and set up the simulation environment. This involves selecting the gears involved in the analysis and applying the defined input motion parameters and contacts.
2. Perform the Simulation:
- Run the motion analysis to observe the interaction between the gears. Creo will simulate the gear assembly’s operation, showing how the gears rotate and mesh under the specified conditions.
Tips:
- Start with a low-speed simulation to identify any immediate issues, such as interferences or misalignments.
- Gradually increase the complexity of the simulation by adjusting the input parameters and observing the effects on gear interactions.
Analyzing Results:
Procedure:
1. Observe Gear Interactions:
- Carefully observe the motion of the gears during the simulation. Check for smooth rotation, proper meshing, and absence of interferences.
2. Check for Interferences:
- Use Creo’s interference detection tools to identify any collisions or overlaps between gears. Resolving these issues is crucial for ensuring the assembly’s functionality.
3. Validate Motion:
- Ensure that the gears transmit the intended motion accurately. Check that the driven gears rotate as expected, without slipping or jamming.
Tips:
- Document any issues encountered during the simulation and make necessary adjustments to the gear designs or assembly constraints.
- Re-run the simulation after making adjustments to verify that the changes have resolved any identified issues.
Refining the Design:
Procedure:
1. Make Adjustments:
- Based on the simulation results, adjust the gear designs or assembly constraints as needed. This could involve refining the gear profiles, modifying constraints, or altering input parameters.
2. Re-Simulate:
- After making adjustments, re-run the motion analysis to validate the changes. Repeat this process iteratively until the simulation results are satisfactory.
Tips:
- Keep a detailed record of each adjustment and its impact on the simulation results. This documentation will help in troubleshooting and refining the design.
- Use Creo’s advanced simulation tools to explore different scenarios and optimize the gear assembly’s performance.
Performing motion analysis and simulation is an essential part of the gear assembly design process. By setting up and running detailed simulations in Creo, you can validate your design, identify and resolve issues, and optimize the performance of your gear assembly. This process ensures that your gears will operate smoothly and efficiently in real-world applications, meeting the highest standards of quality and reliability. In the next step, we will discuss how to document the entire process, from design to simulation, ensuring clear and comprehensive communication of your work.
Step 4: Documenting the Process
Documenting the entire process of designing, assembling, and simulating a complex gear assembly is crucial for effective communication, future reference, and evaluation. A comprehensive report ensures that every aspect of the project is clearly understood, from the initial design to the final simulation results. In this section, we will outline the key elements that should be included in your documentation, providing a detailed guide on how to present your work clearly and professionally.
Design Documentation:
Procedure:
1. Detailed Sketches and Screenshots:
- Include detailed sketches of each gear design, highlighting key dimensions and features. Use Creo’s drawing tools to generate accurate and clear sketches.
- Provide high-quality screenshots of the gear models from various angles to give a complete view of the designs.
2. Dimensioned Drawings:
- Create dimensioned drawings for each gear, specifying all critical measurements. Ensure that the drawings are to scale and include necessary details such as module, number of teeth, pressure angle, helix angle, face width, and material.
3. Brief Descriptions:
- Write brief descriptions of each gear, explaining its purpose and key specifications. Include information on the design considerations and any challenges encountered during the design process.
Tips:
- Ensure that all drawings and sketches are clear, with legible text and precise measurements.
- Use consistent formatting and labeling throughout the documentation for easy reference.
Assembly Process:
Procedure:
1. Assembly Screenshots:
- Provide screenshots of the assembled gears, showing the overall configuration and individual gear placements. Include different views to illustrate the spatial arrangement and alignment of the gears.
2. Descriptions of Assembly Steps:
- Document each step of the assembly process in detail. Explain how the gears were imported, positioned, and constrained within the assembly. Include information on the specific constraints used and their purposes.
3. Highlight Key Constraints:
- Emphasize the key assembly constraints applied to ensure proper alignment and interaction of the gears. Use diagrams or annotated screenshots to illustrate how the constraints were applied.
Tips:
- Use Creo’s annotation tools to add notes and labels directly to the screenshots for better clarity.
- Provide a logical sequence of assembly steps, ensuring that the documentation follows a clear and easy-to-understand flow.
Simulation Analysis:
Procedure:
1. Simulation Setup Screenshots:
- Include screenshots of the simulation setup, showing the input motion parameters, contacts, and constraints. Ensure that the screenshots clearly illustrate how the simulation environment was configured.
2. Simulation Results:
- Provide screenshots of the simulation results, highlighting the motion of the gears and any observed interactions. Include graphs or charts if applicable to show key performance metrics such as angular velocity, torque, or contact forces.
3. Detailed Analysis:
- Write a detailed analysis of the simulation results. Discuss any issues encountered, such as interferences or misalignments, and explain how they were resolved. Include observations on the gear interactions and overall performance of the assembly.
Tips:
- Use visual aids such as arrows, labels, and highlighted areas in the screenshots to emphasize important details.
- Present the simulation data in a clear and concise manner, using tables or charts where appropriate.
Conclusion:
Procedure:
1. Summary of Findings:
- Summarize the key findings from the design, assembly, and simulation processes. Highlight the successes and challenges encountered throughout the project.
2. Reflection on Challenges:
- Reflect on the challenges faced during the project and how they were overcome. Discuss any lessons learned and how they can be applied to future projects.
3. Suggestions for Improvement:
- Provide suggestions for improving the design, assembly, or simulation processes. This could include recommendations for alternative design approaches, better assembly techniques, or more efficient simulation setups.
Tips:
- Keep the conclusion concise and focused, summarizing the most important points from the documentation.
- Use bullet points or numbered lists to organize suggestions and reflections for easy readability.
Submission Requirements:
Procedure:
1. Creo Part and Assembly Files:
- Ensure that all Creo part files (.prt) for each gear and the assembly file (.asm) are saved and organized in a clear file structure.
2. Comprehensive Report:
Compile all the documentation elements into a comprehensive report in PDF format. Include a cover page, table of contents, and appropriate section headings for easy navigation.
3. Simulation Results and Analysis:
- Include all relevant simulation results and analysis in the report, ensuring that they are clearly presented and easy to interpret.
Tips:
- Review the entire report for consistency and completeness before submission.
- Use a professional layout and formatting style to enhance the report’s presentation and readability.
Documenting the process of designing, assembling, and simulating a complex gear assembly is essential for effective communication and evaluation. By following the steps outlined in this section, you can create a comprehensive and professional report that clearly presents your work and findings. Thorough documentation not only demonstrates your proficiency in mechanical design and simulation but also serves as a valuable reference for future projects and collaborations.
Conclusion
In this project, we have successfully designed, assembled, and simulated a complex gear assembly using Creo. The process involved precise gear design, careful assembly with appropriate constraints, and thorough motion analysis to ensure smooth operation. We documented each step meticulously, providing a clear and comprehensive record of our work.
The project presented several challenges, such as ensuring accurate gear dimensions and achieving proper alignment. Overcoming these obstacles enhanced our understanding and proficiency in mechanical design.
Future improvements could include advanced simulation techniques, optimized workflows, and comprehensive testing to further enhance the quality and performance of the gear assembly.
This project demonstrates the importance of precision, iterative problem-solving, and detailed documentation in mechanical engineering design, providing a strong foundation for tackling similar assignments.