Addressing Thermal-Structural Challenges in Electronic Packaging with ANSYS
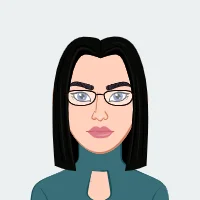
Electronic packaging systems are vital components across a wide range of applications, playing a crucial role in maintaining the reliability and performance of electronic devices. As technology advances, the demand for more compact, efficient, and powerful electronics grows, leading to increasingly complex packaging designs. One of the most significant challenges in designing these systems is the effective management of thermal stresses, which can severely compromise the structural integrity of the packaging. Inadequate thermal management can lead to issues such as overheating, material fatigue, and eventual failure of critical components.
In this blog, we will delve into a structured and methodical approach to tackling coupled thermal-structural analysis assignments using ANSYS, a powerful engineering simulation software. The specific assignment we're referencing involves the analysis of an electronic packaging system, which must endure various thermal loads while maintaining its structural integrity. However, the methodologies and principles discussed here are not limited to this particular example; they are broadly applicable to a wide array of thermal-structural analysis tasks in engineering.
By following the steps outlined in this blog, students and engineers alike will gain valuable insights into the process of analyzing complex systems where thermal and structural factors are interdependent. Whether you're working on electronic packaging, aerospace components, automotive parts, or any other system where thermal and structural interactions are critical, the strategies covered here will provide a robust framework for approaching these challenges effectively. Through careful modeling, precise meshing, thorough thermal and structural analysis, and strategic optimization, you can ensure that your designs meet performance requirements while minimizing the risks associated with thermal stresses. For further assistance, our ANSYS assignment help is available to guide you through intricate simulations and enhance your understanding of multiphysics analysis.
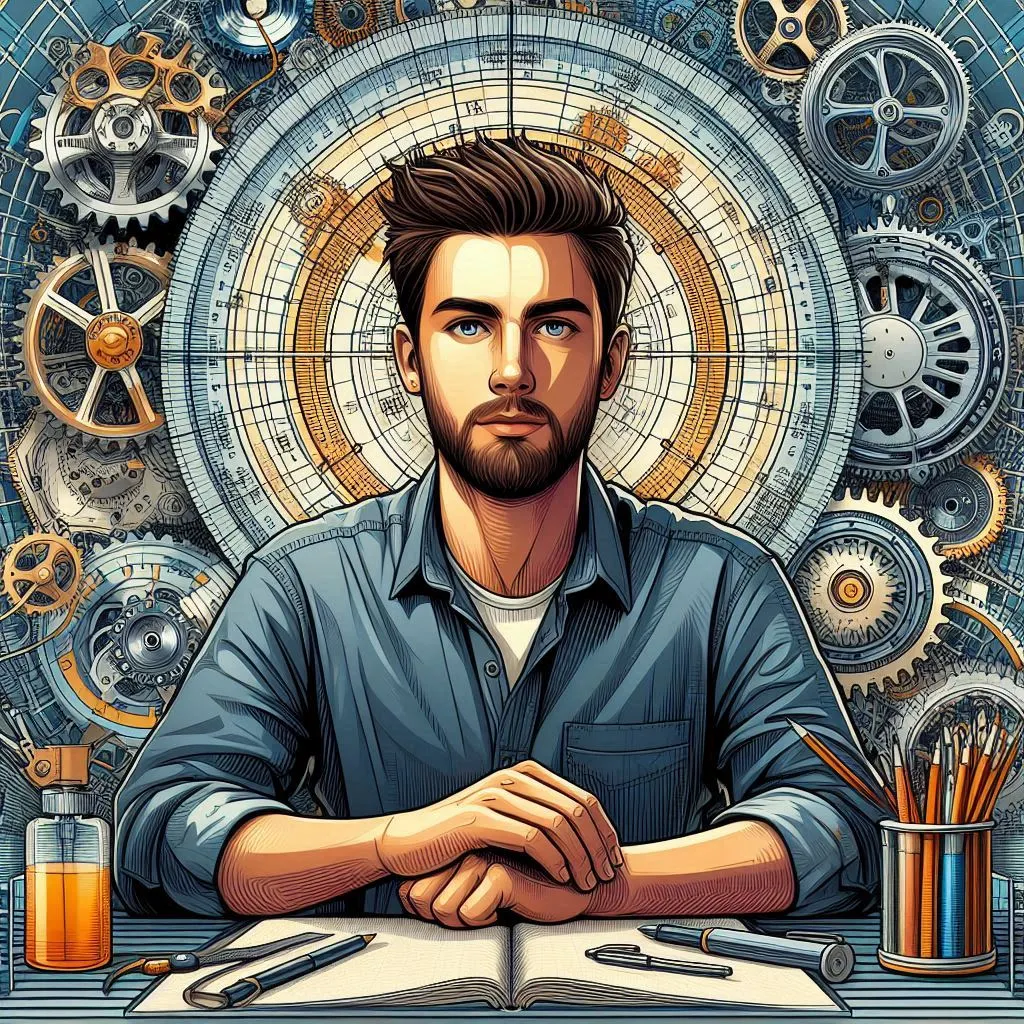
Understanding the Problem
The foundation of any successful engineering analysis begins with a clear and thorough understanding of the problem at hand. In the context of coupled thermal-structural analysis, particularly for electronic packaging systems, this step is crucial as it sets the stage for the entire simulation process. The problem must be defined with precision, identifying the key elements that contribute to both the thermal and structural behavior of the system. For those seeking further guidance, our mechanical engineering assignment help can provide expert support in defining and analyzing complex problems, ensuring a solid foundation for your simulations and analyses.
1. System Definition
Start by defining the electronic packaging system in detail. This includes identifying all components that will be part of the analysis. In the case of an electronic packaging system, these components typically include:
- Heat Sinks: These are crucial for dissipating heat away from sensitive electronic components. Their efficiency directly impacts the thermal management of the entire system.
- Printed Circuit Boards (PCBs): PCBs are the backbone of electronic systems, providing the physical platform for electrical connections. Their material properties, such as thermal conductivity and mechanical strength, are critical in the analysis.
- Solder Joints: These are small but significant components that connect the PCB to other elements in the system. Solder joints are particularly susceptible to thermal stresses, making them a focal point in any structural analysis.
- Electronic Components: Include processors, resistors, capacitors, and any other elements that generate heat during operation. Their placement and power consumption will influence the thermal distribution within the system.
2. Thermal Loads and Environmental Conditions
Understanding the thermal loads that the system will be subjected to is vital. This involves considering:
- Heat Generation: Calculate the amount of heat generated by each electronic component during operation. This is often provided in the component specifications or can be estimated based on power consumption.
- Ambient Conditions: The environmental conditions in which the system operates, such as ambient temperature and airflow, play a significant role in thermal management. Consider whether the system will be in a controlled environment or exposed to varying temperatures.
3. Material Properties and Interactions
Different materials within the electronic packaging system will respond to thermal loads in various ways. It's important to gather accurate material properties, including:
- Thermal Conductivity: This property determines how well a material can conduct heat. High thermal conductivity materials, like metals, are often used in heat sinks, while insulating materials are used in other parts of the system.
- Coefficient of Thermal Expansion (CTE): Different materials expand at different rates when heated. This can lead to thermal stresses, particularly at interfaces between materials with mismatched CTEs.
- Young’s Modulus and Poisson’s Ratio: These mechanical properties will influence how the material responds to the applied thermal stresses in the structural analysis.
4. Failure Criteria and Objectives
Clearly defining the objectives of the analysis and the criterion for success is essential. In the context of electronic packaging systems, this might include:
- Maximizing Reliability: The primary goal may be to ensure that the system can withstand the thermal stresses without failure over its expected lifespan.
- Optimizing Thermal Management: Another objective might be to design the system in such a way that it maintains optimal operating temperatures, thereby improving performance and longevity.
- Design for Manufacturability: Consider how the design can be optimized for manufacturing processes, balancing thermal and structural requirements with cost-effectiveness.
By fully understanding the problem, you can approach the coupled thermal-structural analysis with confidence, ensuring that all relevant factors are considered. This step lays the groundwork for creating a detailed and accurate simulation model, which will ultimately lead to more reliable and effective design solutions.
Modeling the System
After thoroughly understanding the problem, the next step in solving a coupled thermal-structural analysis assignment is to create an accurate and detailed model of the system in ANSYS. The modeling phase is critical because it forms the foundation upon which the entire analysis is built. A well-constructed model will ensure that the simulations provide meaningful and reliable results, allowing for effective decision-making and design optimization.
1. Component Identification and Selection
Begin by identifying all the key components of the electronic packaging system that will be included in the model. These components could include:
- Heat Sinks: Used to dissipate heat from high-temperature regions to cooler areas, usually made from materials with high thermal conductivity like aluminum or copper.
- Printed Circuit Boards (PCBs): These are layered boards that mechanically support and electrically connect electronic components. PCBs are typically composed of composite materials with varying thermal and mechanical properties.
- Solder Joints: These small, yet critical components connect the PCB to electronic components and are particularly sensitive to thermal stresses.
- Electronic Components: Include items such as microprocessors, resistors, capacitors, and other elements that generate heat and are susceptible to thermal and mechanical stress.
Each of these components must be represented accurately in the model, with appropriate consideration given to their material properties and interactions.
2. Geometry Creation
The next step is to create a 3D geometric model of the electronic packaging system within ANSYS. This geometry should be as accurate as possible to capture all the critical features that may affect thermal and structural behavior:
- Detailed Representation: Ensure that all relevant details of the components are included, such as the exact shape, dimensions, and positioning of heat sinks, PCBs, and solder joints.
- Simplification Where Necessary: While detail is important, it's also essential to simplify the model where possible to reduce computational load without sacrificing accuracy. For example, very small features that do not significantly impact the analysis could be excluded.
3. Assigning Material Properties
Material properties play a vital role in both thermal and structural analysis. It’s crucial to assign the correct material properties to each component within the model:
- Thermal Properties: Assign thermal conductivity, specific heat, and thermal expansion coefficients for each material. These properties will determine how heat is conducted through the system and how materials expand or contract in response to temperature changes.
- Mechanical Properties: Assign mechanical properties such as Young’s modulus, Poisson’s ratio, and yield strength. These will affect how materials deform under stress and how they interact at joints and interfaces.
Ensure that the material properties are accurate and reflective of the real-world materials used in the electronic packaging system.
4. Boundary Conditions and Load Applications
Setting up the correct boundary conditions is essential for accurate simulations:
- Thermal Boundary Conditions: Apply boundary conditions that replicate the real operating environment of the electronic packaging system. This might include ambient temperature, heat generation rates from electronic components, and cooling mechanisms like airflow or heat sinks.
- Structural Boundary Conditions: Define constraints and loads for the structural analysis. For example, fixed supports might represent where the PCB is mounted within a device, and thermal stresses derived from the thermal analysis should be applied to the structural model.
5. Meshing the Model
Meshing is one of the most critical steps in the modeling process, as it divides the geometry into small elements that ANSYS will use to perform the analysis:
- Refined Mesh in Critical Areas: Pay special attention to areas where high thermal gradients or stress concentrations are expected, such as around solder joints, heat sinks, and material interfaces. A finer mesh in these areas will increase the accuracy of the results.
- Balancing Mesh Density and Computational Efficiency: While a finer mesh can provide more detailed results, it also increases the computational load. It’s important to balance mesh refinement with the available computational resources to ensure efficient simulations without compromising on accuracy.
6. Verification of the Model
Before proceeding with the analysis, verify the model to ensure that it accurately represents the system and that all components, materials, and boundary conditions are correctly defined:
- Check for Geometric Errors: Ensure there are no overlaps, gaps, or other issues in the geometry that could affect the analysis.
- Material Assignments: Double-check that the correct material properties are assigned to each component.
- Boundary Condition Validity: Verify that all thermal and structural boundary conditions are appropriately applied.
7. Model Documentation
Documenting the modeling process is important for both current and future reference:
- Detailed Notes: Keep a detailed record of all the steps taken during the modeling process, including any assumptions made and the rationale behind them.
- Screenshots and Diagrams: Include visual representations of the model, such as screenshots of the geometry, mesh, and boundary conditions, to aid in understanding and communication.
By carefully following these steps to model the system, you'll be well-prepared to carry out a thorough and accurate coupled thermal-structural analysis. A well-built model is essential for reliable simulation results, which are crucial for making informed design decisions and optimizing the electronic packaging system for both thermal management and structural integrity.
Developing the Mesh
Meshing is one of the most critical stages in the simulation process, as it directly influences the accuracy, efficiency, and reliability of your analysis results. The mesh is essentially a discretization of your model into smaller elements, which allows ANSYS to solve the equations governing thermal and structural behavior across the entire domain. Here’s how to ensure that your meshing is effective:
Mesh Refinement
Mesh refinement is particularly crucial in areas with high thermal gradients or stress concentrations. These regions are typically found:
- Around Heat Sinks: Heat sinks are designed to manage thermal loads by dissipating heat away from critical components. The effectiveness of a heat sink depends on how well the mesh captures the thermal gradients in this area. A finer mesh around the heat sinks ensures that the thermal behavior is accurately modeled.
- At Solder Joints: Solder joints are small, yet they play a significant role in the structural integrity of the electronic packaging system. These joints often experience high stress due to thermal expansion and contraction. Mesh refinement in these areas helps capture the stress concentrations that could lead to failure.
- Interfaces Between Different Materials: Where materials with differing thermal and mechanical properties meet, the mesh needs to be fine enough to accurately model the interactions at these boundaries. This is essential for capturing the thermal expansion mismatches that can generate significant stresses.
Quality Check
A high-quality mesh is essential for obtaining accurate results from your thermal-structural analysis. Here are some key quality aspects to consider:
- Element Shape and Size: Ensure that elements are well-shaped (preferably hexahedral or tetrahedral) and appropriately sized for the regions they represent. Avoid overly distorted or skewed elements, as they can lead to numerical inaccuracies.
- Aspect Ratio: Maintain a good aspect ratio for the elements. Elements with a high aspect ratio (very elongated or flat) can lead to convergence issues and inaccurate results, especially in complex simulations involving coupled physics.
- Mesh Independence: Conduct a mesh independence study to ensure that the results do not significantly change with further mesh refinement. This step helps to strike a balance between accuracy and computational efficiency, ensuring that your mesh is fine enough to capture all critical behaviors without unnecessarily increasing computational costs.
Thermal Analysis
Once the model and mesh are ready, the next step is to perform the thermal analysis. This stage involves applying thermal loads and boundary conditions to simulate the real-world operating environment of the electronic packaging system. The thermal analysis provides insight into how heat is distributed throughout the system, which is crucial for understanding potential issues related to overheating and thermal stress.
Load Application
Thermal loads need to be applied accurately to reflect the operating conditions of the system:
- Heat Generation from Components: Identify the heat sources within the electronic packaging system, typically the electronic components such as processors, resistors, and capacitors. Apply the heat generation rate to these components based on their power consumption and operational characteristics.
- Ambient Temperature: Consider the environmental conditions where the electronic packaging system will operate. This includes the ambient temperature and any cooling mechanisms, such as forced air or liquid cooling. Properly applied boundary conditions ensure that the thermal analysis reflects real-world scenarios.
Transient Analysis
In many cases, a transient thermal analysis is necessary to capture the time-dependent behavior of the system:
- Temperature Variation Over Time: Perform a transient thermal analysis to understand how temperatures change over time within the system. This is particularly important for systems that experience varying loads or operate in environments with fluctuating temperatures.
- Identification of Hotspots: Analyze the results to identify any hotspots—areas where temperatures exceed safe operating limits. Hotspots can lead to thermal degradation or failure, making their identification critical for subsequent structural analysis and design optimization.
Structural Analysis
After completing the thermal analysis, the next step is to evaluate the structural integrity of the electronic packaging system under the influence of the thermal loads. This involves assessing how the thermal stresses generated by temperature changes affect the mechanical behavior of the system.
Thermal Stress Application
The thermal results from the previous step must be accurately transferred to the structural analysis setup:
- Importing Thermal Results: Import the temperature distribution obtained from the thermal analysis into the structural analysis module of ANSYS. This data serves as the basis for calculating thermal stresses.
- Application of Thermal Stresses: Apply the thermal stresses to the structural model. These stresses are caused by the expansion and contraction of materials as they heat up and cool down, and they can lead to significant deformation or even failure in critical areas.
Static Structural Analysis
Performing a static structural analysis allows you to evaluate the effects of thermal stresses on the system’s components:
- Evaluation of Stress Distribution: Analyze the stress distribution across the electronic packaging system, with a focus on critical components such as solder joints and PCBs. This analysis helps identify areas that are prone to mechanical failure due to thermal stresses.
- Displacement and Deformation: Examine the displacements and deformations that occur due to thermal expansion. Understanding how the system deforms under thermal loads is essential for ensuring that it maintains its structural integrity and functional performance.
Coupled Analysis for Comprehensive Insight
To gain a complete understanding of how the electronic packaging system behaves under thermal loads, it is necessary to perform a coupled analysis. This approach integrates the results of the thermal and structural analyses to simulate the combined effects of temperature and mechanical stresses.
Integration
A coupled analysis allows you to combine the thermal and structural behaviors into a single, comprehensive simulation:
- Multiphysics Simulation: By integrating thermal and structural analyses, you can perform a multiphysics simulation that accounts for the complex interactions between thermal and mechanical phenomena. This simulation provides a more accurate and holistic view of the system's behavior under real-world conditions.
Reliability Assessment
The coupled analysis enables you to assess the reliability and performance of the electronic packaging system in a more detailed and realistic manner:
- Identifying Potential Failure Points: Evaluate the combined effects of temperature-induced stresses on the system’s reliability. This includes identifying potential failure points, such as areas where thermal and mechanical stresses overlap or reinforce each other, leading to a higher risk of damage or failure.
- Performance Evaluation: Assess how well the system performs under the combined thermal and structural loads. This evaluation helps determine whether the current design meets the necessary performance criteria or if modifications are needed to enhance reliability.
Optimization for Enhanced Performance
Optimization is a crucial aspect of engineering analysis, allowing you to improve the design of the electronic packaging system to better manage thermal stresses and enhance overall performance. Through optimization studies, you can explore various design configurations and identify the most effective solutions.
Design Modifications
Based on the insights gained from the analysis, propose design modifications aimed at improving the system's thermal and structural performance:
- Heat Sink Placement: Consider adjustments to the placement of heat sinks to improve thermal management. Optimizing the location and design of heat sinks can help dissipate heat more effectively, reducing the risk of overheating and thermal stress.
- Material Selection: Explore the use of different materials with better thermal or mechanical properties for critical components, such as solder joints. Selecting materials with a lower coefficient of thermal expansion or higher thermal conductivity can significantly reduce thermal stresses.
- Geometric Adjustments: Modify the geometry of components or the overall system to minimize stress concentrations and improve thermal dissipation. For example, adding fillets to sharp corners can reduce stress concentrations, while increasing surface area can enhance heat dissipation.
Optimization Studies
Leverage ANSYS’s optimization tools to systematically explore different design options and identify the best solution:
- Parametric Studies: Conduct parametric studies to evaluate how changes in design parameters, such as material properties, component placement, or cooling strategies, impact the system's performance. This approach allows you to test multiple configurations quickly and efficiently.
- Objective Functions: Define objective functions, such as minimizing thermal stress or maximizing thermal dissipation, to guide the optimization process. These functions help focus the analysis on achieving the most critical design goals.
- Iterative Process: Use an iterative process to refine the design based on the results of the optimization studies. Each iteration should bring the design closer to meeting the performance criteria while minimizing risks.
Reporting and Documentation
The final step in the analysis process is to compile your findings into a comprehensive report. This report should document the entire analysis process, including the modeling, meshing, thermal analysis, structural analysis, coupled analysis, and optimization efforts.
Documentation
Detailed documentation ensures that the analysis process is transparent and can be reviewed or replicated by others:
- Modeling Process: Include a step-by-step description of the modeling process, highlighting key decisions such as material selection, boundary condition application, and mesh refinement.
- Analysis Results: Present the results of the thermal, structural, and coupled analyses, including temperature distributions, stress maps, and displacement fields. Use visual aids, such as graphs and contour plots, to clearly communicate the findings.
- Design Recommendations: Provide a detailed explanation of the design modifications proposed during the optimization phase. Explain how these changes are expected to improve the system's performance and reliability.
Conclusions
Summarize the key takeaways from the analysis, emphasizing how the findings can enhance the reliability and performance of the electronic packaging system:
- Impact of Thermal Stresses: Highlight the critical areas where thermal stresses were found to be most significant and how these stresses could potentially lead to failure.
- Effectiveness of Design Modifications: Discuss the effectiveness of the proposed design modifications in reducing thermal stresses and improving thermal management.
- Future Work: Suggest areas for further analysis or testing, such as experimental validation of the simulation results or exploring additional design options.
By following these steps, you can ensure that your coupled thermal-structural analysis is both thorough and effective, providing valuable insights that lead to better-performing electronic packaging systems.
Conclusion
In this blog, we've walked through a comprehensive approach to solving coupled thermal-structural analysis assignments using ANSYS, with a focus on electronic packaging systems. These systems, being critical to the reliability and performance of modern electronics, demand a detailed and methodical analysis to manage the thermal stresses that can compromise structural integrity.
We began by understanding the problem, which is crucial for setting up any simulation. A clear grasp of the objectives, material properties, and operating conditions lays the groundwork for accurate modeling. Next, we discussed the importance of system modeling and meshing, highlighting how careful mesh refinement and quality checks ensure that the simulations yield reliable results.
Thermal analysis allowed us to simulate the heat distribution and identify potential hotspots within the system, setting the stage for the subsequent structural analysis. By importing thermal data into a structural framework, we were able to assess how thermal stresses impact the system’s components, particularly the solder joints and PCBs. The integration of thermal and structural results through a coupled analysis provided a more comprehensive insight into the system’s behavior under operational conditions.
Optimization played a key role in refining the design to better manage thermal stresses, ultimately enhancing the system’s performance and reliability. Finally, the importance of thorough documentation and reporting was emphasized, ensuring that the analysis is transparent, reproducible, and informative.
By following this structured approach, you can tackle similar thermal-structural analysis tasks with confidence, ensuring that your electronic packaging systems are designed to withstand the rigors of their operating environments. This method not only helps in identifying potential failure points but also provides a pathway to optimizing designs for better performance and longevity. Whether you are dealing with electronic packaging or other applications involving coupled thermal-structural challenges, the principles and techniques discussed here will be invaluable in achieving reliable and robust solutions.