Coupled Field Analysis in ANSYS: Addressing Real-World Engineering Scenarios
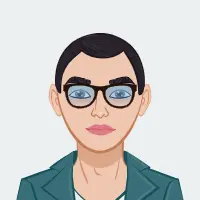
Coupled field analysis in ANSYS represents a sophisticated simulation technique that integrates multiple physical phenomena into a unified model. In essence, it allows engineers to assess the interplay between different fields such as structural mechanics, fluid dynamics, thermal analysis, and electromagnetic effects within a single simulation environment. The significance of coupled field analysis becomes apparent when considering real-world engineering scenarios that are inherently complex and interconnected. In practical terms, many engineering systems and components are subjected to a combination of forces, temperatures, and fluid flows, and understanding the mutual influences of these factors is crucial for designing robust and efficient solutions. If you find yourself in need of assistance with your ANSYS assignment, our experts are here to provide the support you need to navigate the complexities of coupled field analysis and excel in your engineering studies.
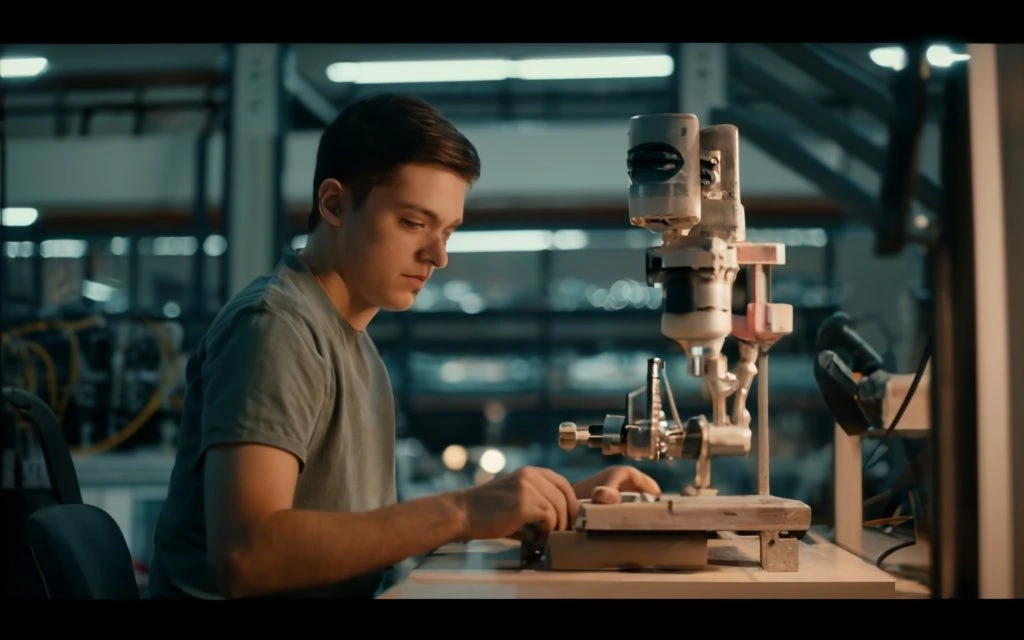
In the intricate landscape of real-world engineering, components rarely operate in isolation; rather, they function within dynamic and interdependent environments. For instance, an automotive brake disc experiences not only structural stresses during braking but also undergoes thermal fluctuations due to frictional heating. Coupled field analysis enables engineers to comprehend the intricate relationships between these various physical phenomena, offering a holistic view that goes beyond traditional single-field simulations. In the case of the brake disc, this would involve assessing how structural deformation impacts thermal behavior and vice versa, providing insights into potential failures or performance improvements.
The importance of understanding coupled field analysis in mechanical engineering lies in its ability to enhance the accuracy and reliability of simulations, ultimately leading to more effective designs. Traditional single-field analyses may overlook critical interactions that could significantly affect the performance or safety of a mechanical system. By incorporating coupled field analysis, engineers gain a comprehensive understanding of how different factors influence each other, allowing for the identification of potential weaknesses or optimization opportunities that might be overlooked in isolated analyses.
Moreover, coupled field analysis is indispensable in tackling contemporary engineering challenges. As technology advances, products become more intricate, and demands for higher efficiency and performance escalate, the need for comprehensive simulations becomes paramount. Mechanical systems in aerospace, automotive, energy, and other industries are increasingly subject to multifaceted operational conditions. Coupled field analysis equips engineers with the tools to simulate and comprehend these intricate scenarios accurately, providing a foundation for innovation and ensuring that designs meet the stringent demands of the real world.
In conclusion, coupled field analysis in ANSYS serves as a pivotal tool for engineers seeking a deeper understanding of the interactions between various physical phenomena in complex systems. Its relevance to real-world engineering scenarios is evident in its capacity to unravel the intricacies of interconnected forces, temperatures, and fluid flows. Emphasizing the importance of understanding coupled field analysis in mechanical engineering is essential for fostering precise simulations, enabling engineers to design robust solutions that meet the evolving challenges of modern engineering. As industries continue to push the boundaries of innovation, coupled field analysis stands as a cornerstone in the pursuit of optimal, efficient, and reliable mechanical designs.
What is Coupled Field Analysis?
Coupled field analysis is a specialized simulation methodology that integrates and analyzes the interactions between multiple physical fields within a single computational model. In essence, it allows engineers to study the simultaneous effects of different physical phenomena, such as structural mechanics, fluid dynamics, thermal behavior, and electromagnetic interactions, on a given system or component. Unlike traditional single-field analyses that isolate one type of physical behavior, coupled field analysis considers the intricate relationships and feedback mechanisms between various fields, providing a more comprehensive understanding of complex engineering scenarios.
What sets coupled field analysis apart from other types of analyses is its ability to capture the mutual influence of diverse physical phenomena in a coupled manner. While structural analysis, fluid dynamics simulations, and thermal assessments are valuable on their own, they often fall short of capturing the real-world complexity where these phenomena coexist and interact. Coupled field analysis bridges these gaps by considering the interdependencies, ensuring a more accurate representation of how different forces and conditions affect each other simultaneously.
Crucially, coupled field analysis is indispensable in scenarios where the interaction between different physical fields significantly influences the behavior and performance of a system. One notable example is the thermal-structural coupling in electronic devices. As electronic components operate, they generate heat, which can, in turn, affect the structural integrity of the surrounding materials. Coupled field analysis in this context allows engineers to predict not only the thermal distribution within the device but also how the resulting temperature changes impact the structural reliability over time. Similarly, in the field of fluid-structure interaction, such as simulating the behavior of an aircraft wing in turbulent airflow, coupled field analysis becomes essential for understanding the dynamic relationship between the structural deformations induced by aerodynamic forces and the airflow patterns surrounding the structure.
Another critical application is found in the design of medical devices like artificial heart valves, where the interaction between fluid flow and structural response is paramount. By employing coupled field analysis, engineers can simulate the complex interaction between blood flow and the mechanical behavior of the valve, ensuring optimal design and functionality under realistic operating conditions. In essence, coupled field analysis serves as a powerful tool for addressing the multifaceted challenges present in numerous engineering domains, offering a more accurate representation of real-world conditions and enabling engineers to make informed decisions for improved system performance and reliability.
ANSYS and its Role
ANSYS stands as a preeminent name in the realm of engineering simulation software, renowned for its robust capabilities in modeling and analyzing complex physical behaviors across a diverse range of industries. As a comprehensive simulation platform, ANSYS provides engineers with a sophisticated toolkit to simulate and understand the intricate interactions between various physical fields within a single integrated environment.
Facilitating coupled field analysis is one of the standout strengths of ANSYS. The software allows engineers to seamlessly couple different physics modules, enabling the simulation of multidisciplinary interactions that occur simultaneously in real-world engineering systems. This capability is particularly valuable in scenarios where the effects of structural mechanics, fluid dynamics, thermal behavior, and electromagnetic phenomena are interdependent, such as in the design of cutting-edge electronic devices, automotive components, or aerospace systems.
ANSYS achieves this by providing a unified interface that allows users to define and couple different physics domains within a single simulation model. Engineers can set up complex coupled simulations, specifying how different fields interact and influence each other over time. This integrated approach ensures a holistic representation of the real-world conditions, allowing for a more accurate assessment of the performance, reliability, and efficiency of engineered systems.
Key features and capabilities make ANSYS particularly well-suited for coupled field analysis. Firstly, its extensive library of physics models covers a wide spectrum of disciplines, providing users with the flexibility to incorporate various physical phenomena into their simulations. This inclusivity extends to structural mechanics, fluid dynamics, heat transfer, and electromagnetics, among others. Secondly, ANSYS employs advanced numerical algorithms and solvers, ensuring the accuracy and efficiency of simulations even in highly complex coupled scenarios.
Furthermore, ANSYS offers robust post-processing tools, enabling engineers to extract meaningful insights from simulation results. Visualization tools, data manipulation capabilities, and customizable output formats empower users to interpret and communicate their findings effectively. Additionally, the software's parametric capabilities facilitate optimization studies, allowing engineers to iteratively refine designs based on the insights gained from coupled field analyses.
In essence, ANSYS plays a pivotal role in advancing coupled field analysis by providing engineers with a powerful and versatile platform that seamlessly integrates various physics domains. Its intuitive interface, extensive physics library, advanced solvers, and post-processing capabilities collectively make ANSYS an indispensable tool for engineers seeking to comprehensively understand and optimize the complex interactions present in real-world engineering scenarios.
Real-World Engineering Applications
Coupled field analysis finds wide-ranging applications in real-world engineering scenarios across industries such as automotive, aerospace, and energy, where intricate interactions between various physical fields significantly impact the performance and reliability of systems. In the automotive sector, thermal-structural coupling is crucial in simulating the behavior of braking systems during heavy use. As a vehicle decelerates, the brake components experience both structural stresses and intense frictional heating, necessitating coupled field analysis to understand how thermal changes influence structural integrity. Engineers employ ANSYS, for instance, to model these interactions accurately, ensuring that the brakes can withstand repeated thermal cycles without compromising safety.
In the aerospace industry, the aerodynamic performance of aircraft wings represents another complex scenario demanding coupled field analysis. As an aircraft maneuvers through turbulent airflow, fluid-structure interaction becomes paramount. The wings experience structural deformations due to aerodynamic forces, while simultaneously influencing the surrounding airflow patterns. Coupled field analysis helps engineers predict the dynamic relationship between structural response and aerodynamic effects, leading to more efficient wing designs and improved overall aircraft performance.
In the energy sector, the design and optimization of gas turbines for power generation exemplify the necessity of coupled field analysis. The combustion process within a turbine involves a combination of fluid flow, heat transfer, and structural dynamics. By employing ANSYS or similar tools, engineers can simulate the intricate coupling between these fields, addressing challenges such as thermal stress on turbine blades and ensuring optimal energy conversion efficiency. This integrated approach enhances the accuracy of predictions related to component fatigue, contributing to the longevity and reliability of the turbine.
Challenges in these scenarios stem from the complexity of the interactions between different physical fields, making it difficult to capture the full range of behaviors with isolated analyses. For instance, in automotive braking systems, overlooking the thermal effects on structural components might lead to premature failures that compromise vehicle safety. In aerospace, neglecting the interplay between aerodynamics and structural deformation could result in suboptimal wing designs with reduced fuel efficiency. In the energy sector, failure to consider the coupled effects of fluid dynamics, heat transfer, and structural dynamics in gas turbine simulations may lead to inaccurate predictions of component lifetimes and compromise overall system reliability.
Coupled field analysis addresses these challenges by providing a holistic simulation approach, where the intricate interdependencies between different physical phenomena are accounted for. By capturing the mutual influences between structural mechanics, fluid dynamics, thermal behavior, and electromagnetic effects, coupled field analysis enables engineers to gain a more accurate understanding of real-world engineering scenarios. This, in turn, empowers them to design robust, efficient, and reliable systems that meet the stringent demands of diverse industries, ultimately advancing the forefront of engineering innovation.
Benefits and Challenges
The utilization of coupled field analysis in ANSYS presents a plethora of benefits that significantly enhance the accuracy and efficiency of engineering simulations. Firstly, this approach allows engineers to capture complex interactions between multiple physical fields, such as fluid dynamics, structural mechanics, thermal behavior, and electromagnetic effects, providing a holistic understanding of real-world scenarios. By considering these interdependencies, coupled field analysis enables more accurate predictions of system behavior, leading to improved designs and optimized performance. Additionally, ANSYS provides a user-friendly interface and a comprehensive library of physics models, offering flexibility to engineers in defining and coupling various physical domains seamlessly. The ability to assess multiple phenomena simultaneously within a single simulation environment reduces the need for separate analyses, streamlining the design process and saving valuable time and resources.
Despite its myriad benefits, coupled field analysis in ANSYS comes with certain challenges and limitations. One common challenge is the computational intensity associated with solving coupled problems, as integrating multiple physics domains can increase simulation complexity and runtime. Engineers may face difficulties in managing computational resources and achieving acceptable simulation times, especially for highly intricate systems. Another challenge lies in accurately defining and validating the coupling parameters between different fields, as errors or uncertainties in these parameters can lead to inaccurate results. Additionally, obtaining real-world experimental data for validation purposes can be challenging, particularly in scenarios where comprehensive physical testing is impractical or costly.
To overcome the challenges associated with coupled field analysis, engineers can adopt several best practices. Firstly, careful model simplification and optimization are crucial to managing computational intensity. This involves strategically reducing the complexity of the simulation model without compromising the accuracy of the results. Furthermore, engineers should conduct thorough sensitivity analyses to understand the influence of different coupling parameters on the simulation outcomes. Validation efforts should leverage available experimental data, and where such data is lacking, conservative assumptions should be made and validated against simplified cases. Collaborative efforts among interdisciplinary teams, involving experts in fluid dynamics, structural mechanics, and other relevant fields, can contribute to a more accurate and comprehensive understanding of the coupled phenomena. Continuous advancements in computational hardware and software, along with regular updates and improvements from ANSYS, provide opportunities for addressing computational challenges and expanding the capabilities of coupled field analysis.
In conclusion, the benefits of coupled field analysis in ANSYS far outweigh the challenges, and by adopting best practices, engineers can leverage this powerful simulation tool to gain deeper insights into complex engineering problems and make informed design decisions.
Conclusion
In conclusion, this blog post has delved into the realm of coupled field analysis in ANSYS, showcasing its significance in addressing complex real-world engineering challenges. Coupled field analysis represents a sophisticated simulation methodology that integrates multiple physical fields, such as structural mechanics, fluid dynamics, thermal behavior, and electromagnetic effects, into a unified model. The importance of this approach lies in its ability to capture the intricate interactions between these fields, offering engineers a holistic understanding of multifaceted engineering scenarios that traditional single-field analyses often overlook.
Throughout the discussion, ANSYS emerged as a powerful simulation software, providing a comprehensive platform for coupled field analysis. Its extensive library of physics models, advanced numerical algorithms, and post-processing tools enable engineers to simulate, analyze, and interpret the interdependencies between different physical phenomena within a single integrated environment. Case studies in industries like automotive, aerospace, and energy underscored the practical applications of coupled field analysis, demonstrating its efficacy in optimizing designs, improving reliability, and addressing the challenges posed by complex system interactions.
The benefits of employing coupled field analysis in ANSYS are evident in its ability to enhance accuracy, streamline the design process, and provide insights that lead to optimized engineering solutions. However, challenges such as computational intensity and the accurate definition of coupling parameters exist. By adopting best practices, including model simplification, sensitivity analyses, and interdisciplinary collaboration, engineers can overcome these challenges and harness the full potential of coupled field analysis.
Emphasizing the importance of this methodology, coupled field analysis stands as a cornerstone in advancing engineering innovation. Its application ensures that engineered solutions are not only robust and efficient but also reflective of the dynamic and interconnected nature of real-world scenarios. The impact is far-reaching, from designing reliable electronic cooling systems and optimizing aircraft wings for enhanced aerodynamic performance to addressing thermal stress in gas turbines for improved energy conversion. As industries evolve and demand increasingly sophisticated solutions, coupled field analysis becomes an indispensable tool for engineers seeking to stay at the forefront of innovation.
To the readers, the invitation is extended to explore further into the realm of coupled field analysis and consider its incorporation in their projects. ANSYS, with its user-friendly interface and powerful simulation capabilities, provides a versatile platform for tackling the intricate challenges posed by coupled physical phenomena. By embracing this methodology, engineers can elevate their understanding of complex engineering scenarios, leading to more informed decision-making, optimized designs, and ultimately, the advancement of engineering excellence.