Exploring the Power of ANSYS Workbench: Tips for Effective Engineering Simulations
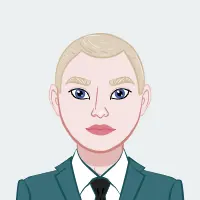
Engineering simulations are a cornerstone in the realm of mechanical engineering, serving as indispensable tools that bridge the gap between theoretical concepts and real-world applications. These simulations play a pivotal role in the field by allowing engineers to model and analyze complex systems, predict their behavior under varying conditions, and optimize their performance without the need for extensive physical prototypes. In the ever-evolving landscape of mechanical engineering assignments, simulations have emerged as a transformative force, enabling a more efficient and cost-effective approach to design, testing, and problem-solving. Whether you're exploring the applications of simulations in mechanical engineering or need assistance with your Ansys assignment, understanding the role of simulation tools like Ansys is essential for success in this dynamic and innovative field.
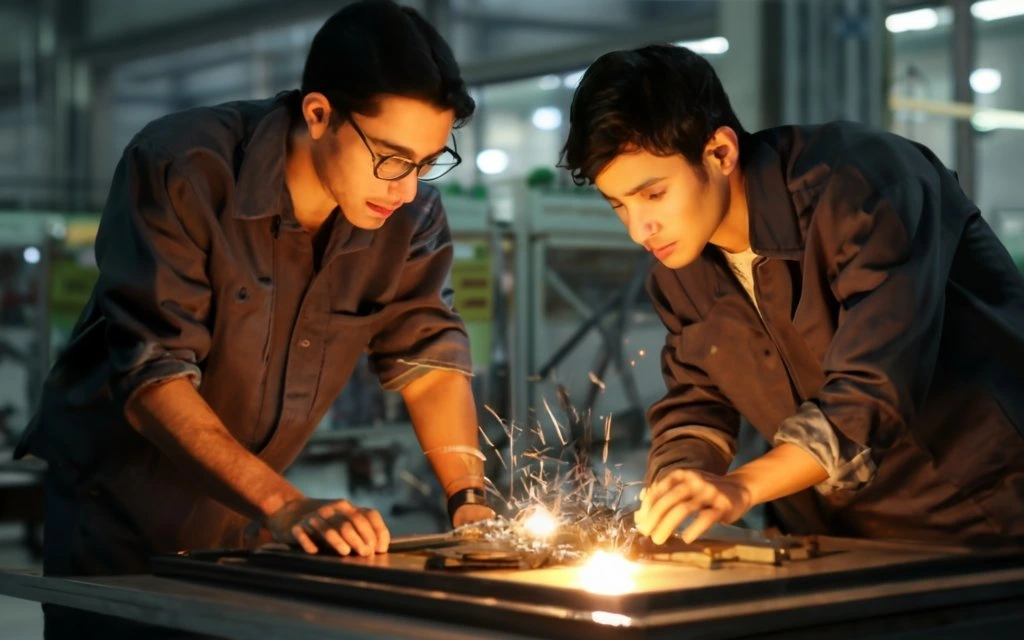
At the heart of this transformative process lies ANSYS Workbench, a powerful and comprehensive simulation platform that has become synonymous with excellence in the engineering domain. ANSYS Workbench stands out for its versatility, offering a wide array of simulation capabilities that cater to the diverse needs of mechanical engineering projects. From structural and thermal analyses to fluid dynamics and electromagnetics, ANSYS Workbench provides a unified environment where engineers can seamlessly integrate and conduct simulations across multiple disciplines. Its significance in the field is underscored by its ability to deliver accurate and reliable results, empowering engineers to make informed decisions at every stage of the product development lifecycle.
One of the key strengths of ANSYS Workbench is its versatility, making it a go-to solution for mechanical engineers facing a spectrum of challenges. The platform's capabilities extend beyond mere analysis, encompassing the exploration of design alternatives, optimization of parameters, and the assessment of a product's performance in real-world conditions. This versatility not only expedites the engineering process but also enhances the overall quality of the design by allowing engineers to iterate and refine their models with precision.
In the realm of mechanical engineering assignments, where students are tasked with solving complex problems and demonstrating a deep understanding of engineering principles, ANSYS Workbench becomes an invaluable companion. It offers students hands-on experience in tackling real-world engineering challenges, enabling them to apply theoretical knowledge to practical scenarios. By utilizing ANSYS Workbench, students can gain proficiency in simulation techniques, preparing them for the demands of a rapidly evolving engineering landscape.
Moreover, ANSYS Workbench contributes significantly to time and cost savings, a critical consideration in any engineering endeavor. Traditional prototyping and testing methods are not only resource-intensive but also time-consuming. ANSYS Workbench streamlines this process by allowing engineers to conduct virtual tests and analyses, minimizing the need for physical prototypes and accelerating the product development cycle. This efficiency is particularly advantageous in meeting tight project timelines and budget constraints, making ANSYS Workbench an indispensable asset in the toolbox of mechanical engineers.
In conclusion, the importance of engineering simulations, especially with the focus on ANSYS Workbench, cannot be overstated in the context of mechanical engineering assignments. These simulations empower engineers and students alike to explore, analyze, and optimize designs with unparalleled accuracy and efficiency. As a catalyst for innovation and problem-solving, ANSYS Workbench continues to shape the landscape of mechanical engineering, providing a robust platform for engineers to push the boundaries of what is possible in the world of simulation and design.
What is ANSYS Workbench?
ANSYS Workbench stands as a pinnacle in the realm of engineering simulation, offering a comprehensive and integrated platform that has revolutionized the way engineers approach design and analysis. Developed by ANSYS Inc., a global leader in engineering simulation software, ANSYS Workbench serves as a unified environment where engineers can seamlessly perform a wide spectrum of simulations, spanning structural, thermal, fluid dynamics, electromagnetic, and multiphysics analyses. It goes beyond being a mere simulation tool; rather, it is an ecosystem that empowers engineers to navigate the complexities of product development with unprecedented efficiency and accuracy.
At its core, ANSYS Workbench is distinguished by its versatility, providing engineers with a diverse set of simulation tools to address the multifaceted challenges encountered in the field of engineering. The platform enables users to create virtual prototypes of their designs, allowing for the exploration of different scenarios and the assessment of how a product will behave under varying conditions. This versatility is particularly crucial in an era where interdisciplinary collaboration is becoming the norm, as ANSYS Workbench facilitates the seamless integration of simulations across different engineering disciplines within a single, intuitive interface.
One of the standout features of ANSYS Workbench is its parametric modeling capabilities, allowing engineers to explore design alternatives by varying parameters and dimensions. This parametric approach enhances the optimization process, enabling users to iteratively refine their designs based on simulation results. By providing insights into the sensitivity of a design to various factors, ANSYS Workbench empowers engineers to make informed decisions that lead to more robust and efficient products.
The platform's meshing capabilities are another critical aspect that contributes to its prowess. ANSYS Workbench employs advanced meshing algorithms that generate high-quality meshes, a crucial element for obtaining accurate simulation results. The meshing process is automated and user-friendly, reducing the complexity traditionally associated with this crucial step in the simulation workflow. This ensures that even users with limited experience in mesh generation can obtain reliable results, democratizing the simulation process and making it accessible to a broader audience.
Furthermore, ANSYS Workbench fosters collaboration and knowledge sharing through its consistent and standardized interface. Engineers can easily transfer projects and data between different simulation tools within the Workbench environment, streamlining workflows and promoting a cohesive approach to simulation-driven design. This interoperability is essential in an engineering landscape where projects often require a combination of various simulation disciplines.
ANSYS Workbench's significance extends beyond the desktop, as it supports cloud computing for simulation tasks. This not only enhances the scalability of simulations but also allows for more efficient use of computational resources, particularly beneficial for large-scale simulations and parametric studies.
In conclusion, ANSYS Workbench stands as a testament to the evolution of engineering simulation, offering a powerful and versatile platform that has become synonymous with innovation and efficiency. Its ability to seamlessly integrate various simulation disciplines, automate complex processes, and democratize simulation for a broad user base makes it an invaluable asset in the toolkit of engineers across industries. As technology continues to advance, ANSYS Workbench remains at the forefront, shaping the future of engineering simulation and contributing to the development of cutting-edge, high-performance products.
Key Benefits of Using ANSYS Workbench.
ANSYS Workbench, a powerhouse in engineering simulation, unfolds a myriad of key benefits that have positioned it as an industry leader and an indispensable tool for engineers across diverse disciplines. One of its foremost advantages lies in its versatility, offering a comprehensive suite of simulation tools that span structural, thermal, fluid dynamics, electromagnetic, and multiphysics analyses. This breadth enables engineers to address complex engineering challenges within a unified environment, eliminating the need for disparate software and streamlining the simulation workflow.
Accuracy stands as a hallmark of ANSYS Workbench, with its robust solvers and algorithms delivering reliable and precise results. The platform's ability to model real-world behaviors with a high degree of fidelity empowers engineers to make informed decisions during the design and optimization processes. Whether simulating the structural integrity of a component under varying loads or analyzing the fluid dynamics of a complex system, ANSYS Workbench excels in providing accurate insights that contribute to the creation of robust and reliable products.
Time and cost savings emerge as significant benefits of ANSYS Workbench, revolutionizing traditional product development cycles. The platform enables engineers to conduct virtual tests and analyses, minimizing the need for physical prototypes. This not only accelerates the design iteration process but also reduces the overall time-to-market. Additionally, the elimination of costly physical testing and prototyping translates into substantial cost savings, making ANSYS Workbench an economically viable solution for engineering projects with budget constraints.
Parametric modeling within ANSYS Workbench represents a powerful feature that enhances the design exploration and optimization process. Engineers can easily manipulate parameters and dimensions, allowing for the rapid assessment of various design alternatives. This capability facilitates the identification of optimal solutions and empowers engineers to iteratively refine their designs based on simulation results. The parametric approach within ANSYS Workbench not only expedites the design process but also contributes to the development of more efficient and innovative solutions.
Meshing, a critical step in the simulation process, is seamlessly integrated into ANSYS Workbench with advanced algorithms that automate and optimize the mesh generation process. The platform's user-friendly meshing capabilities ensure that even users with limited expertise can generate high-quality meshes, a crucial factor for obtaining accurate simulation results. By simplifying and automating meshing, ANSYS Workbench removes a significant barrier to entry for engineers new to simulation, democratizing access to powerful simulation capabilities.
Collaboration is fostered through ANSYS Workbench's standardized and consistent interface, enabling engineers to easily share projects and data across different simulation disciplines. This interoperability promotes a cohesive approach to simulation-driven design and facilitates interdisciplinary collaboration. Whether working on structural simulations, fluid dynamics analyses, or electromagnetics studies, teams can seamlessly exchange information within the ANSYS Workbench environment, fostering a collaborative and efficient engineering ecosystem.
Furthermore, ANSYS Workbench embraces the era of cloud computing, allowing users to leverage the power of the cloud for simulation tasks. This not only enhances scalability for large-scale simulations but also provides flexibility in utilizing computational resources. The cloud capability within ANSYS Workbench contributes to the platform's adaptability to evolving technological landscapes and ensures that engineers have access to state-of-the-art computing resources.
In summary, the key benefits of using ANSYS Workbench are rooted in its versatility, accuracy, time and cost savings, parametric modeling capabilities, user-friendly meshing, collaborative interface, and cloud compatibility. As a multifaceted simulation platform, ANSYS Workbench continues to redefine the standards for engineering simulation, empowering engineers to innovate, optimize, and bring cutting-edge products to market with unparalleled efficiency and reliability.
Tips for Effective Engineering Simulations.
Effective engineering simulations are crucial for gaining valuable insights into the behavior and performance of complex systems. Here, we explore key tips to ensure that engineering simulations are not only accurate but also contribute meaningfully to the design and optimization process.
Firstly, a foundational aspect of successful engineering simulations is a clear understanding of the problem at hand. Before delving into the simulation process, engineers must define the objectives, boundary conditions, and desired outcomes. This initial step lays the groundwork for a focused and purpose-driven simulation, ensuring that the results obtained align with the specific goals of the engineering analysis.Proper meshing techniques play a pivotal role in the accuracy of simulations. The mesh serves as a discretized representation of the geometry, and the quality of the mesh directly influences the reliability of the results. Engineers should pay meticulous attention to mesh generation, ensuring that it is fine enough to capture intricate details while avoiding unnecessary refinement that could lead to computational inefficiencies. Striking a balance in mesh density is essential for achieving accurate and efficient simulations.
Boundary conditions represent another critical aspect of engineering simulations. Accurately defining the conditions at the boundaries of the system under study is imperative for obtaining realistic results. Whether simulating structural behavior, fluid flow, or thermal dynamics, ensuring that boundary conditions mimic real-world scenarios is essential. Engineers should consider external forces, constraints, and environmental factors that could impact the system's behavior.
Parameterization of the model adds a layer of flexibility to engineering simulations. By parameterizing key dimensions and variables, engineers can explore a range of design alternatives efficiently. This approach facilitates sensitivity analyses, allowing users to understand how changes in specific parameters influence the overall performance of the system. Parameterization not only contributes to a more comprehensive exploration of the design space but also aids in the optimization process.
Effective post-processing is crucial for extracting meaningful insights from simulation results. Engineers should carefully analyze and interpret the data to draw relevant conclusions about the system's performance. Visualization tools within simulation software, such as ANSYS Workbench, can assist in creating informative plots, graphs, and animations that aid in the interpretation of complex data sets. Thorough post-processing enhances the value of the simulation results, guiding engineers toward informed decisions and design modifications.
Validation against experimental data or benchmarks is a prudent practice in engineering simulations. While simulations provide a powerful tool for virtual testing, validating the results against real-world data ensures the accuracy and reliability of the simulation model. By comparing simulation outcomes with experimental observations or established benchmarks, engineers can gain confidence in the predictive capabilities of their simulation setup.
Documentation throughout the simulation process is essential for reproducibility and knowledge transfer. Engineers should maintain detailed records of simulation setup, parameters, and results. Well-documented simulations not only support internal knowledge sharing within teams but also facilitate collaboration and enable future users to understand and reproduce the analyses.
Continuous learning and staying abreast of advancements in simulation techniques and tools contribute to the effectiveness of engineering simulations. As technology evolves, new methodologies and features are introduced, providing engineers with enhanced capabilities. Engaging in professional development and leveraging resources such as online forums, tutorials, and training programs ensures that engineers remain proficient in utilizing the latest simulation tools and methodologies.
In summary, effective engineering simulations require a thorough understanding of the problem, careful consideration of meshing techniques and boundary conditions, parameterization for design exploration, meticulous post-processing for result interpretation, validation against experimental data, comprehensive documentation, and a commitment to continuous learning. By adhering to these tips, engineers can harness the full potential of simulation tools to drive innovation, optimize designs, and address complex engineering challenges.
Conclusion:
In the dynamic landscape of engineering, where precision and efficiency are paramount, the exploration of the power of ANSYS Workbench in engineering simulations has proven to be a transformative journey. The tips discussed for effective engineering simulations serve as guiding principles, underlining the importance of a meticulous approach to ensure the reliability and accuracy of simulation results.
At the core of successful simulations lies a crystal-clear understanding of the engineering problem. By defining objectives and boundary conditions with precision, engineers set the stage for simulations that are purposeful and aligned with project goals. The emphasis on proper meshing techniques further underscores the commitment to achieving accurate results. The delicate balance between mesh refinement and computational efficiency is an art that engineers master, ensuring that simulations capture intricate details without sacrificing performance.
Boundary conditions, often the bridge between simulation and reality, are acknowledged as a critical component. Accurate representation of real-world scenarios ensures that simulations mirror practical conditions, enhancing the reliability of the results. Parameterization emerges as a powerful tool, providing engineers with the flexibility to explore diverse design alternatives efficiently. This approach not only broadens the scope of design exploration but also facilitates sensitivity analyses, empowering engineers to make informed decisions.
Post-processing, a sometimes overlooked but essential step, is highlighted for its role in extracting meaningful insights. Visualization tools become the lens through which complex data is interpreted, guiding engineers toward a deeper understanding of the system's behavior. Validation against experimental data remains a cornerstone, affirming the credibility of simulations and reinforcing the bridge between the virtual and the physical.
The call for meticulous documentation echoes through the narrative, emphasizing the importance of transparency and knowledge transfer. Well-documented simulations not only serve as a record of analyses but also foster collaboration and pave the way for continuous improvement.
In this exploration of ANSYS Workbench and the tips for effective engineering simulations, the synthesis of theory and practice emerges as the key to unlocking the platform's full potential. As engineers embark on the path of innovation and problem-solving, armed with a comprehensive understanding of simulation intricacies, they are poised to redefine the boundaries of what is achievable in the realm of mechanical engineering. The journey is not just about simulations; it is about the empowerment of engineers to shape a future where precision and efficiency converge to drive groundbreaking advancements in the field.