Approaching Multi-Scale System Design Engineering Assignments with Confidence
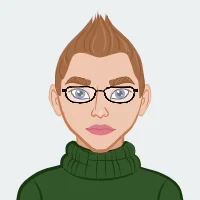
When tackling Multi-Scale System Design Engineering assignments, it’s essential to approach them methodically and understand the underlying principles. Given the complexity and the multi-faceted nature of these assignments, a systematic approach can greatly enhance your ability to analyze, comprehend, and solve the problems presented. These assignments often involve intricate interactions between different scales and components, requiring a deep understanding of both theoretical concepts and practical applications that you can use in system design assignment help. By breaking down the tasks into smaller, manageable steps and thoroughly examining each aspect, you can develop a comprehensive solution that addresses all the given requirements. Additionally, a methodical approach allows you to identify potential issues early in the process, enabling you to make necessary adjustments before they escalate. This not only saves time but also ensures a more accurate and robust outcome. Here's a structured approach to help you navigate through similar assignments effectively and efficiently, ensuring that you cover all bases, minimize errors, and build a strong foundation for tackling future engineering challenges.
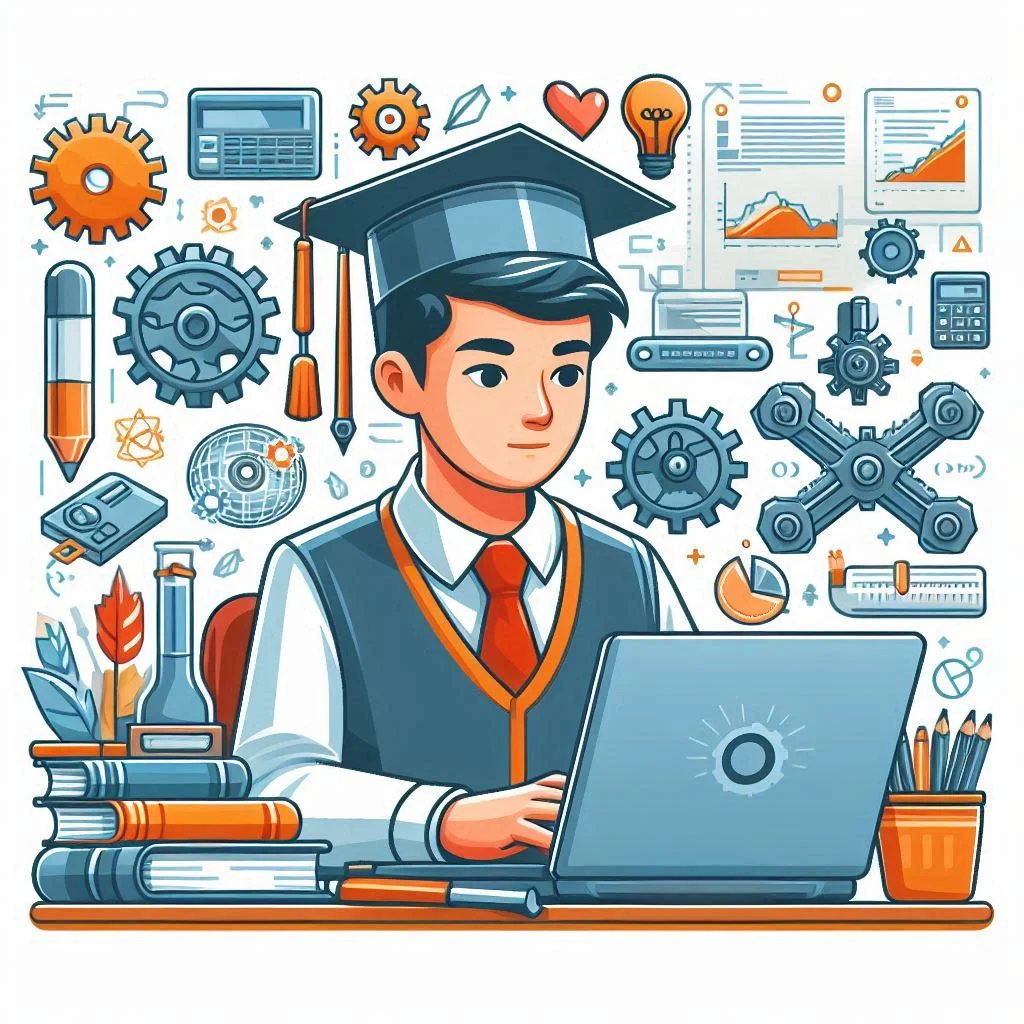
Understanding the Assignment Requirements
When faced with a Multi-Scale System Design Engineering assignment, the first and most crucial step is to thoroughly understand the assignment requirements. This understanding sets the stage for a successful and efficient problem-solving process. By grasping what the assignment entails, you can ensure that your efforts are directed toward meeting the specified goals and constraints. Here's a detailed approach to help you fully comprehend and analyze the assignment requirements:
- Read the Assignment Carefully: Begin by meticulously reading the assignment prompt multiple times. This helps in ensuring that you understand what the assignment is asking. Pay close attention to all the details, such as the system's dimensions, material properties, and specific parameters that need to be analyzed. Misinterpreting a single requirement can lead to significant errors in your entire solution. Highlight or note down critical points that will guide your approach. This initial step is fundamental in laying a strong foundation for your analysis and ensuring that you are on the right track from the very beginning.
- Identify Key Parameters and Variables: Extract all the important variables and parameters provided in the assignment. For example, in the provided assignment, parameters include dimensions (12”x12”x36”), material properties (Eball = 30 x 10^6 psi, νball = 0.3), and geometric factors (Rball, Rgroove1, Rgroove2, and Rcoupling). Understanding these parameters is crucial as they form the foundation of your analysis. Create a detailed list of these parameters and ensure you comprehend their significance and how they interact within the system. Identifying and understanding these key components will help you in developing accurate and effective solutions.
- Clarify the Objectives: Clearly define what the assignment aims to achieve. Are you required to perform a specific analysis, design a component, or evaluate certain behaviors under given conditions? Understanding the primary objectives helps in focusing your efforts on the most critical aspects of the task. This clarity will also assist in organizing your workflow and prioritizing tasks effectively. Knowing the end goals allows you to tailor your approach to meet the specific needs of the assignment and ensures that you are working towards the right outcomes.
- Identify Assumptions and Constraints: Identify any assumptions and constraints mentioned in the assignment. For example, assumptions might include ignoring certain parts of the system or considering ideal conditions. Constraints could involve material limitations, dimensional restrictions, or predefined loads. Recognizing these factors early on will guide your problem-solving approach and ensure that your solutions are practical and within the given boundaries. Clearly understanding the limitations and assumptions will prevent you from making unrealistic or incorrect assumptions in your analysis.
- Research Background Information: Conduct preliminary research to gather background information relevant to the assignment. This might include reviewing similar case studies, reading relevant literature, or understanding industry standards and practices. Building a strong foundational knowledge will enable you to approach the problem with a well-rounded perspective and draw upon various sources of information to enhance your analysis. This research can provide insights and methodologies that are applicable to your assignment, enriching your understanding and approach.
- Plan Your Approach: Develop a clear plan or roadmap for tackling the assignment. Outline the steps you will take, the tools and methods you will use, and the sequence of tasks. A well-structured plan not only keeps you organized but also ensures that you don’t overlook any critical components of the assignment. This planning stage is crucial for managing your time effectively and maintaining steady progress throughout the task. A detailed plan helps in tracking your progress and ensures that you remain focused on your objectives.
By following these steps, you will build a comprehensive understanding of the assignment requirements, which is essential for developing effective and accurate solutions. This thorough preparation phase ensures that you are well-equipped to tackle the challenges presented by the assignment and can approach the problem with confidence and clarity.
Compliance Error Analysis
Compliance error analysis is a critical step in Multi-Scale System Design Engineering assignments. It involves evaluating the deformations and potential errors in the system due to the compliance (flexibility) of various components. This analysis helps in understanding how different parts of the system respond to applied loads and forces, and how these responses might introduce errors or variations in the expected performance. Here’s a detailed approach to performing compliance error analysis:
- List Assumptions: Begin by clearly listing all the assumptions you need to make for the analysis. Assumptions simplify the problem and make the analysis more tractable. For instance, in the provided assignment, you might assume perfect kinematic coupling between components, ignore certain parts of the system, or consider material properties as constant. Clearly stating these assumptions helps in setting the boundaries for your analysis and ensures that the results are interpreted correctly.
- Analyze the Interaction Between Components: Understand the interaction between different components in the system. For example, the kinematic coupling between steel parts A and B is crucial in the provided assignment. You need to analyze how the ball, grooves, and coupling interact under the given load conditions. This involves examining the contact points, force distribution, and the resulting deformations. Understanding these interactions is essential for identifying potential sources of compliance errors.
- Formulate the Governing Equations: Based on the physical and geometric properties, formulate the equations governing the system. This might involve deriving expressions for deformation, stress, or strain in the components. For example, you may need to use elasticity theory to derive the relationship between the applied load and the resulting deformation in the kinematic coupling. Formulating these equations provides a mathematical framework for analyzing the system's behavior.
- Conduct a Parametric Analysis: Perform a parametric analysis to understand how different parameters affect the system’s compliance. In the provided assignment, you might need to analyze the deformation (δD|A) in terms of various parameters like force (F), length (Li), moment of inertia (Ii), polar moment of inertia (Ji), shear modulus (Gi), modulus of elasticity (Ei), and coupling stiffness (kcoupling). Vary each parameter systematically to see how it influences the overall deformation and compliance of the system. This helps in identifying the most significant factors contributing to compliance errors.
- Quantify Compliance Errors: Calculate the percentage of error due to kinematic coupling compliance versus frame compliance. This involves comparing the deformation caused by the kinematic coupling (e.g., ball and grooves) to that caused by the frame or structure supporting the system. Use the derived equations and parametric analysis results to quantify these errors. Understanding the relative contribution of each component to the overall compliance error helps in pinpointing critical areas for improvement.
- Compare and Validate Results: Compare your analytical results with experimental data or numerical simulations if available. Validation ensures that your compliance error analysis is accurate and reliable. Use tools like finite element analysis (FEA) software to simulate the system and compare the results with your analytical predictions. Any discrepancies should be investigated and understood, leading to a more robust and validated compliance error analysis.
- Document Findings and Recommendations: Finally, document your findings in a clear and structured manner. Highlight the key sources of compliance errors, the most influential parameters, and any recommendations for minimizing these errors. Providing detailed documentation helps in communicating your analysis to others and serves as a reference for future work.
By following these steps, you can conduct a thorough compliance error analysis that provides valuable insights into the performance and reliability of Multi-Scale System Design Engineering systems. This analysis is crucial for identifying potential issues, optimizing the design, and ensuring the system meets the desired specifications and performance criteria.
Parametric Analysis
Parametric analysis is an essential process in Multi-Scale System Design Engineering that involves studying how the system's response changes with variations in key parameters. By systematically altering these parameters, engineers can understand the influence of each variable on the overall system behavior, identify critical factors, and optimize the design for better performance. Here’s a comprehensive guide to performing parametric analysis:
- Identify Key Parameters: Start by identifying the key parameters that influence the system's behavior. These could include geometric dimensions, material properties, load conditions, and boundary conditions. In the provided assignment, parameters such as force (F), length (Li), moment of inertia (Ii), polar moment of inertia (Ji), shear modulus (Gi), modulus of elasticity (Ei), and coupling stiffness (kcoupling) are critical.
- Formulate the Governing Equations: Develop the mathematical equations that describe the system's behavior in terms of the identified parameters. This may involve using principles of mechanics, such as elasticity, kinematics, and dynamics, to derive expressions for deformation, stress, strain, or other relevant quantities. These equations form the basis of the parametric analysis.
- Set Up the Analysis Framework: Establish a framework for systematically varying the parameters. Decide on the range and increments for each parameter based on realistic values and the assignment's requirements. For example, if analyzing the effect of force (F) on deformation, you might vary F from 100 lbf to 1000 lbf in increments of 100 lbf.
- Conduct Sensitivity Analysis: Perform a sensitivity analysis to determine how sensitive the system's response is to changes in each parameter. This involves calculating the partial derivatives of the governing equations with respect to each parameter. Sensitivity analysis helps identify which parameters have the most significant impact on the system's behavior, guiding further investigation and optimization efforts.
- Run Simulations or Analytical Calculations: Use analytical methods or simulation tools to calculate the system's response for each set of parameter values. If using simulation software, set up the model to reflect the real system accurately and run the simulations for each parameter variation. Analytical calculations may involve solving the governing equations for different parameter values.
- Analyze and Interpret Results: Examine the results to understand how the system's behavior changes with varying parameters. Plot the results using graphs or charts to visualize the relationships. For example, plot deformation (δD|A) against force (F) to see how deformation changes with increasing force. Look for trends, patterns, and any non-linearities that might indicate complex interactions between parameters.
- Identify Critical Parameters: Based on the analysis, identify the parameters that have the most significant influence on the system's performance. These are the critical parameters that need careful consideration in the design and optimization process. Understanding these parameters helps prioritize efforts to improve the system's reliability and efficiency.
- Optimize the Design: Use the insights gained from the parametric analysis to optimize the design. Adjust the critical parameters to achieve the desired performance while considering practical constraints. For example, if increasing the shear modulus (Gi) significantly reduces deformation, explore material options with higher shear modulus to enhance the system's stiffness.
- Validate Findings: Validate the findings from the parametric analysis through experiments or more detailed simulations. Comparing the analytical or simulation results with experimental data ensures the reliability of the analysis and helps refine the model for better accuracy.
- Document and Communicate Results: Document the parametric analysis process, findings, and recommendations in a clear and structured manner. Include detailed descriptions of the parameter variations, analysis methods, results, and interpretations. Effective communication of the results helps stakeholders understand the analysis and supports informed decision-making in the design process.
By following these steps, you can conduct a thorough parametric analysis that provides valuable insights into the behavior of Multi-Scale System Design Engineering systems. This analysis is crucial for optimizing designs, improving performance, and ensuring that the system meets the required specifications and performance criteria.
Error Analysis
Error analysis is a crucial aspect of Multi-Scale System Design Engineering assignments. It involves identifying, quantifying, and understanding the sources of errors in the system to ensure accuracy and reliability in the design and analysis processes. Here’s a detailed approach to conducting error analysis:
- Identify Potential Sources of Error: Begin by identifying all potential sources of error in the system. These sources can include measurement inaccuracies, material property variations, assumptions and simplifications made during modeling, numerical approximations in simulations, and environmental factors. For example, in the provided assignment, errors could arise from assumptions about perfect kinematic coupling or ignoring certain parts of the system.
- Categorize Errors: Categorize the identified errors into different types, such as systematic errors (consistent and repeatable errors) and random errors (unpredictable and varying errors). Systematic errors might include consistent deviations due to material property assumptions, while random errors could arise from fluctuating environmental conditions.
- Quantify Individual Errors: Quantify the magnitude of each identified error source. This may involve using experimental data, literature values, or sensitivity analysis to estimate the impact of each error on the system. For example, if the assignment involves kinematic coupling, you might quantify the error due to the compliance of the coupling components by comparing theoretical predictions with experimental measurements.
- Combine Errors: Use appropriate methods to combine individual errors to estimate the overall error in the system. Common methods include root sum square (RSS) for combining independent errors and direct summation for dependent errors. The combined error gives an overall measure of the uncertainty in the system's response.
- Analyze Compliance Errors: Specifically analyze compliance errors, which are errors due to the deformation or flexibility of components under load. Compare the compliance of different parts of the system, such as the kinematic coupling versus the frame. For example, calculate the deformation due to kinematic coupling compliance and frame compliance separately and determine their relative contributions to the total error.
- Calculate Error Percentages: Determine the percentage of error attributed to different sources. This helps in understanding the dominant sources of error and prioritizing efforts to mitigate them. For instance, if the error due to kinematic coupling compliance is significantly higher than frame compliance, focus on improving the coupling design.
- Perform Sensitivity Analysis: Conduct a sensitivity analysis to see how changes in key parameters affect the overall error. This involves varying parameters such as material properties, geometric dimensions, and load conditions to see how sensitive the system's response is to these changes. Sensitivity analysis helps identify which parameters most significantly influence the error.
- Validate Error Estimates: Validate your error estimates by comparing them with experimental results or high-fidelity simulations. Validation ensures that your error analysis is accurate and reliable. If discrepancies are found, investigate the causes and refine your error analysis accordingly.
- Document and Communicate Findings: Document your error analysis process, findings, and conclusions in a detailed report. Clearly explain the sources of errors, their magnitudes, and their combined effect on the system's performance. Use visual aids such as graphs and charts to illustrate the error analysis results. Effective communication ensures that stakeholders understand the potential uncertainties and limitations of the design.
- Implement Error Mitigation Strategies: Based on the error analysis, develop and implement strategies to mitigate significant sources of error. This might involve using more accurate measurement techniques, selecting materials with more consistent properties, refining assumptions, or enhancing the design to reduce compliance. Mitigating errors improves the overall reliability and performance of the system.
By following these steps, you can conduct a thorough error analysis that provides valuable insights into the sources and magnitudes of errors in Multi-Scale System Design Engineering systems. This analysis is essential for ensuring the accuracy and reliability of the design and analysis processes, leading to more robust and trustworthy engineering solutions.
Practical Tips for Students
Navigating Multi-Scale System Design Engineering assignments can be challenging, but with the right approach, you can effectively tackle these tasks and achieve successful outcomes. Here are practical tips to help you excel in your assignments:
- Understand the Assignment Requirements: Begin by thoroughly reading and understanding the assignment prompt. Clarify any ambiguities or uncertainties with your instructor before proceeding. Pay attention to details such as dimensions, material properties, and specific parameters to be analyzed.
- Break Down the Problem: Divide the assignment into smaller, manageable tasks. This approach helps in focusing on each component or aspect of the system separately, making the overall analysis more structured and systematic.
- Research and Gather Information: Conduct background research to gather relevant information and resources. Review textbooks, academic papers, and online resources to deepen your understanding of Multi-Scale System Design principles and methodologies.
- Use Software Tools: Leverage engineering software tools such as MATLAB, ANSYS, or SolidWorks for simulations, parametric studies, and analysis. These tools can provide valuable insights, visualization capabilities, and accurate calculations to support your analysis.
- Verify Assumptions and Simplifications: Clearly state and validate any assumptions or simplifications made during your analysis. Understand the implications of these assumptions on your results and consider their validity in real-world scenarios.
- Collaborate and Seek Guidance: Engage in discussions with classmates, professors, or online forums to exchange ideas and seek guidance. Collaborative learning can provide new perspectives and help clarify concepts or approaches.
- Document Your Work: Maintain organized notes and documentation of your analysis process, including equations, assumptions, calculations, and results. Clear documentation not only helps in understanding your own work but also facilitates communication and review by others.
- Conduct Sensitivity Analyses: Perform sensitivity analyses to understand how variations in parameters affect the system's response. Identify critical parameters that significantly influence performance and prioritize efforts accordingly.
- Validate Results: Validate your analysis results through comparison with theoretical predictions, experimental data, or validated simulations. Validation ensures the accuracy and reliability of your findings and helps in refining your approach if discrepancies arise.
- Review and Revise: Before submitting your assignment, review your work thoroughly. Check for errors, logical consistency, and completeness. Revise as necessary to ensure clarity and coherence in your analysis and conclusions.
- Continuous Learning and Improvement: Treat each assignment as an opportunity to learn and improve your skills. Reflect on feedback received and identify areas for further development in Multi-Scale System Design Engineering.
By applying these practical tips, you can approach Multi-Scale System Design Engineering assignments with confidence and proficiency. Each step contributes to a thorough and well-executed analysis, ultimately leading to enhanced learning outcomes and academic success.
Conclusion
Mastering Multi-Scale System Design Engineering assignments requires a methodical approach and a deep understanding of engineering principles. By following the practical tips outlined above, you can navigate these assignments effectively and achieve robust solutions:
- Understanding Assignment Requirements: Begin by thoroughly comprehending the assignment prompt, identifying key parameters, and clarifying any uncertainties.
- Systematic Problem Solving: Break down complex tasks into manageable steps, ensuring each aspect of the system is analyzed methodically.
- Research and Utilize Tools: Utilize engineering software and research resources to enhance your understanding and support your analysis.
- Validation and Documentation: Validate your results through simulations, experiments, or literature reviews, and maintain detailed documentation of your process.
- Continuous Improvement: Learn from each assignment to refine your skills, address challenges, and expand your knowledge base.
By integrating these strategies into your approach, you not only enhance your academic performance but also develop critical skills applicable to real-world engineering challenges. Embrace each assignment as an opportunity to grow and innovate in Multi-Scale System Design Engineering, ensuring your solutions are accurate, efficient, and reliable.