Integrating CAD Models with ANSYS: Seamless Workflow for Engineering Projects!
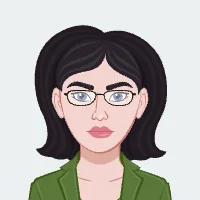
Computer-Aided Design (CAD) and Finite Element Analysis (ANSYS) stand as indispensable pillars in the field of mechanical engineering, revolutionizing the design and analysis processes. CAD serves as the cornerstone, enabling engineers to create precise and detailed digital representations of mechanical components and systems. Its significance lies in its ability to translate conceptual designs into three-dimensional models, fostering visualization and aiding in the iterative design process. CAD not only accelerates the design phase but also enhances accuracy, allowing engineers to scrutinize and refine their concepts before physical prototypes are ever manufactured. This virtual prototyping capability not only saves time and resources but also ensures that the final product meets stringent performance and safety standards. If you need assistance with your ANSYS assignment, understanding the integration of CAD and ANSYS is crucial for effective analysis and optimization of mechanical designs.
On the other hand, ANSYS, a powerful Finite Element Analysis (FEA) tool, empowers engineers to simulate and analyze the structural, thermal, and fluid dynamics behavior of their designs. This analytical prowess of ANSYS is critical in predicting how a mechanical system will perform under various conditions, identifying potential weaknesses, and optimizing for peak efficiency. The ability to subject virtual prototypes to a range of scenarios before physical testing is a game-changer, reducing the likelihood of design flaws and streamlining the engineering process.
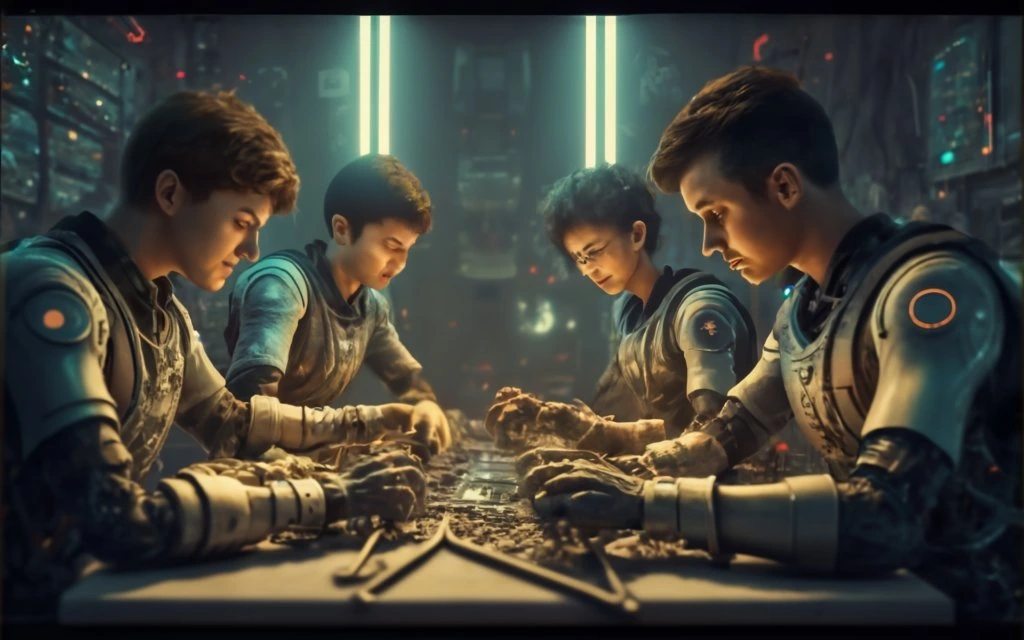
While both CAD and ANSYS individually offer immense benefits, integrating them seamlessly for engineering projects poses a set of challenges that engineers must navigate. One primary hurdle lies in the diversity of file formats used by CAD software and ANSYS. Ensuring compatibility between these systems becomes a meticulous task, often requiring conversions and adjustments to preserve the integrity of the design data. Engineers also grapple with the complexity of geometry representation; a CAD model may contain intricate details that ANSYS struggles to handle, leading to compromises in the accuracy of simulations.
Another challenge arises in the data transfer process between CAD and ANSYS. As these software tools are developed by different vendors, smooth data exchange is not always guaranteed. Engineers find themselves dealing with issues such as missing information, distorted geometry, or incorrect material properties during the transfer. These discrepancies can compromise the accuracy of simulations and, consequently, the reliability of the entire engineering analysis.
Furthermore, the dynamic nature of engineering projects introduces changes and updates to CAD models. Engineers often face the challenge of maintaining synchronization between the evolving CAD design and ANSYS simulations. This requires a careful management process to ensure that the simulation reflects the latest design iteration accurately.
In conclusion, while CAD and ANSYS individually contribute significantly to the advancement of mechanical engineering, the process of integrating them for engineering projects is not without its challenges. Engineers must navigate file format disparities, complex geometry representations, and data transfer issues to ensure a seamless workflow. Addressing these challenges is crucial to unlocking the full potential of CAD-ANSYS integration, enabling engineers to deliver robust and optimized designs in an efficient and timely manner.
Understanding CAD Models:
Computer-Aided Design (CAD) is a transformative technology that plays a pivotal role in the field of mechanical engineering. It involves the use of specialized software to create, modify, and optimize detailed and precise two-dimensional (2D) and three-dimensional (3D) models of mechanical components and systems. CAD serves as the digital canvas for engineers, providing a virtual environment to conceptualize, design, and refine their ideas before they move into the physical realm. This technology significantly accelerates the design process, allowing engineers to visualize complex structures, assess geometric relationships, and make informed decisions that lead to the creation of robust and innovative mechanical systems.
Within CAD, various types of models are commonly used in engineering projects, each serving a specific purpose in the design and analysis process. Parametric models, for instance, enable engineers to create designs with parameters that can be modified dynamically, facilitating easy exploration of design variations. Surface models represent the outer boundary of an object and are particularly useful for aerodynamic and ergonomic considerations. Solid models, on the other hand, provide a comprehensive representation of the entire volume of an object, aiding in accurate visualization and analysis of internal structures. Assembly models bring together multiple parts or components, allowing engineers to assess the interactions and relationships between individual elements within a larger system. These diverse model types provide engineers with a versatile toolkit to address the multifaceted aspects of mechanical design.
The significance of accurate CAD models becomes particularly pronounced when transitioning to simulation and analysis using tools like ANSYS. Simulation software relies heavily on the fidelity of the CAD models to deliver reliable results. Accurate geometric representation ensures that simulations in ANSYS reflect the real-world behavior of mechanical systems, allowing engineers to predict how a design will perform under various conditions. This accuracy is critical for identifying potential structural weaknesses, thermal issues, or fluid dynamics challenges early in the design process. The ability to conduct virtual testing on precise CAD models in ANSYS not only enhances the reliability of engineering analyses but also reduces the need for costly physical prototypes and iterative testing.
In essence, CAD is the cornerstone of modern mechanical engineering, providing the digital foundation for design and innovation. The diverse range of CAD models caters to the specific needs of engineering projects, offering flexibility and precision. The accurate representation of these models is paramount when transitioning to simulation and analysis tools like ANSYS, ensuring that the virtual prototypes closely mirror the expected performance of the physical counterparts. This integration of CAD and simulation technologies is instrumental in optimizing designs, minimizing errors, and ultimately delivering efficient and robust mechanical systems.
Introduction to ANSYS:
ANSYS stands as a powerhouse in the realm of engineering simulation, offering a comprehensive suite of tools that empower engineers to conduct intricate Finite Element Analysis (FEA) across a broad spectrum of disciplines. At its core, ANSYS utilizes the finite element method, a numerical technique for solving complex engineering problems by dividing a structure into smaller, more manageable elements. This method enables engineers to simulate and analyze the behavior of structures and systems under various conditions, providing insights into factors such as stress, strain, heat transfer, and fluid flow.
The capabilities of ANSYS extend across multiple domains, including structural mechanics, fluid dynamics, electromagnetics, and thermal analysis. In structural analysis, ANSYS can assess the strength, stability, and deformation of mechanical components and assemblies. Fluid dynamics simulations allow engineers to predict and optimize the behavior of liquids and gases in a variety of scenarios. Electromagnetic analysis helps in understanding the interaction of electromagnetic fields with structures, while thermal analysis aids in evaluating the heat distribution and thermal performance of systems. This versatility makes ANSYS a go-to solution for engineers grappling with the complexity and interdependencies inherent in modern engineering challenges.
Simulation and analysis are integral components of the design and validation process in modern engineering. They serve as virtual testing grounds, allowing engineers to explore and refine designs before committing to physical prototypes. The importance of this virtual testing becomes evident in its ability to identify potential issues, validate performance expectations, and optimize designs—all without the need for costly and time-consuming physical testing. ANSYS, with its sophisticated simulation capabilities, enables engineers to predict how a design will behave under diverse conditions, providing crucial insights into the strengths and weaknesses of a proposed solution.
By incorporating ANSYS into the design workflow, engineers can iterate more rapidly, explore a wider range of design alternatives, and make informed decisions early in the development process. This not only accelerates the overall product development timeline but also contributes to cost savings and enhanced product reliability. Simulation-driven design, facilitated by tools like ANSYS, has become a cornerstone in the quest for innovation and efficiency, allowing engineers to push the boundaries of what is possible while ensuring that designs meet or exceed performance and safety standards. In essence, ANSYS empowers engineers to bridge the gap between conceptualization and realization, providing a robust platform for simulation and analysis that is indispensable in the modern engineering landscape.
Challenges in Integration:
Engineers often encounter a set of challenges when striving to seamlessly integrate Computer-Aided Design (CAD) models with ANSYS for finite element analysis (FEA) and simulation. One prominent challenge lies in the diversity of file formats utilized by different CAD software and ANSYS. CAD tools generate models in various formats such as STEP, IGES, or native formats like SolidWorks or CATIA. ANSYS, while supporting a range of formats, may still face compatibility issues, requiring engineers to navigate through the intricacies of file conversion. This process can introduce errors, compromises in model fidelity, or loss of crucial information, making it imperative for engineers to meticulously manage file formats during the integration process.
Geometry representation poses another significant hurdle. CAD models often contain intricate details, curved surfaces, or complex features that may not seamlessly transfer into ANSYS. Discrepancies in geometry can lead to inaccuracies in the simulation results, potentially undermining the reliability of the entire analysis. Engineers must invest time in preparing CAD models for ANSYS, addressing issues such as gaps, overlaps, or overly detailed geometry that might impede the simulation process. This meticulous preparation ensures that the geometry is well-suited for the finite element analysis, avoiding errors that may arise due to poorly represented shapes or features.
Data transfer between CAD and ANSYS introduces additional challenges. As these software tools are developed by different vendors, establishing smooth communication can be a complex task. Incompatibilities may arise in terms of how data is interpreted and transferred between the two systems. Engineers often face issues like missing information, incorrect material properties, or distorted geometry during the transfer process. These discrepancies can lead to a misrepresentation of the original design intent, impacting the accuracy and reliability of the subsequent simulation in ANSYS.
Moreover, changes and updates to CAD models throughout the design process can pose synchronization challenges. When modifications are made to the CAD design, engineers must ensure that these changes seamlessly propagate to the ANSYS simulation model. Failure to maintain synchronization can lead to inconsistencies between the virtual prototype and the actual design, potentially compromising the accuracy of the analysis. Managing version control and ensuring a streamlined update process becomes crucial to maintaining the integrity of the CAD-ANSYS integration.
In conclusion, the integration of CAD models with ANSYS is not without its challenges. Engineers must grapple with issues related to file formats, geometry representation, and data transfer to ensure a seamless transition from the design phase to finite element analysis. Overcoming these challenges requires a combination of meticulous model preparation, effective data management, and a deep understanding of the intricacies involved in bridging the gap between CAD and ANSYS. Successfully addressing these challenges is pivotal to unlocking the full potential of simulation-driven design and ensuring the reliability of engineering analyses.
Best Practices for Seamless Integration:
Overcoming integration challenges between CAD models and ANSYS for finite element analysis (FEA) involves employing practical tips and best practices. One key strategy is to establish a standardized approach to file formats. Engineers should aim to use neutral file formats like STEP or IGES during the transfer from CAD to ANSYS to minimize compatibility issues. Understanding the intricacies of each format and selecting the one most suitable for the specific geometry and features of the CAD model can significantly ease the integration process. Additionally, staying updated with the latest software versions for both CAD and ANSYS ensures compatibility, as software developers often release updates to address file format issues and enhance interoperability.
For effective geometry representation, thorough preparation of CAD models is essential. Simplifying complex geometry, removing unnecessary details, and resolving issues such as gaps and overlaps contribute to a smoother integration process. CAD models should be thoroughly checked for irregularities or inconsistencies that might affect the accuracy of the simulation in ANSYS. Utilizing CAD functionalities for simplification or employing dedicated preprocessing tools can streamline the geometry and enhance compatibility with ANSYS, ultimately leading to more reliable simulation results.
Implementing a robust data management strategy is crucial for addressing issues related to data transfer. Engineers should maintain a clear record of the versions and revisions of both CAD models and ANSYS simulations. Establishing a well-defined workflow for updating models and synchronizing changes ensures that the simulation accurately reflects the most recent design iteration. Regular communication and collaboration between CAD and ANSYS users within a team can help identify and resolve data transfer issues promptly, preventing discrepancies from escalating.
Furthermore, investing in training and skill development for engineers involved in the integration process is fundamental. A deep understanding of both CAD and ANSYS functionalities allows engineers to navigate challenges more effectively. Training programs focused on best practices for integration, file handling, and model preparation can empower the team to troubleshoot and optimize the workflow, minimizing potential errors.
In conclusion, a systematic approach to integration challenges involves standardizing file formats, optimizing geometry representation, implementing robust data management practices, and investing in ongoing training for the engineering team. By following these practical tips and best practices, engineers can enhance the compatibility between CAD models and ANSYS, leading to a seamless integration process and more accurate finite element analysis results. This proactive approach not only minimizes errors but also maximizes the efficiency and effectiveness of the simulation-driven design process in the field of mechanical engineering.
Case Studies or Examples:
Real-world examples abound where the successful integration of CAD models with ANSYS has significantly enhanced engineering outcomes, impacting both project efficiency and accuracy. One notable case is in the aerospace industry, where a leading aircraft manufacturer employed CAD-ANSYS integration to optimize the design of critical components. By seamlessly transferring complex CAD models into ANSYS, engineers conducted sophisticated finite element analyses to assess structural integrity, aerodynamics, and thermal performance. The integrated approach enabled the identification of potential stress concentrations, allowing for precise modifications to mitigate structural vulnerabilities. The result was not only a reduction in design iterations but also a substantial decrease in physical prototyping requirements. This translated into a remarkable improvement in project efficiency, as the design cycle was expedited, and costly iterations were minimized. Moreover, the accuracy of simulations ensured that the final design not only met but exceeded performance and safety standards, contributing to enhanced aircraft reliability and operational efficiency.
In the automotive industry, a renowned car manufacturer leveraged CAD-ANSYS integration for optimizing crash simulations. By seamlessly transferring intricate CAD models of vehicle components into ANSYS, engineers conducted detailed finite element analyses to simulate and evaluate crash scenarios. The accuracy of the simulation allowed for precise prediction of structural deformations and impact forces, enabling engineers to refine the design for enhanced crashworthiness. This integration not only reduced the need for extensive physical crash testing but also accelerated the overall design validation process. The project efficiency gains were substantial, with the optimized design proving to be not only safer but also more cost-effective due to the reduced reliance on physical prototypes.
In both cases, the successful integration of CAD models with ANSYS played a pivotal role in achieving improved engineering outcomes. The impact on project efficiency was evident through streamlined design processes, reduced iteration cycles, and faster time-to-market. The accuracy of ANSYS simulations ensured that the final designs met stringent performance and safety criteria, contributing to enhanced product reliability. These real-world examples underscore how CAD-ANSYS integration can be a game-changer in diverse engineering domains, allowing for more informed decision-making, cost savings, and ultimately, the development of high-performance and reliable products.
Conclusion:
In this blog post, we delved into the crucial aspects of integrating Computer-Aided Design (CAD) models with ANSYS for seamless engineering projects. The significance of CAD and ANSYS in the realm of mechanical engineering was highlighted, emphasizing how CAD serves as the foundation for design, while ANSYS excels in finite element analysis and simulation. Challenges in integration were explored, focusing on issues related to file formats, geometry representation, and data transfer between the two systems. These challenges were seen as potential roadblocks that engineers must navigate to ensure a smooth workflow from design to simulation. Practical tips and best practices were provided to overcome integration challenges, emphasizing standardized file formats, meticulous CAD model preparation, and robust data management strategies.
A key takeaway is the crucial role of accurate CAD models in the success of finite element analysis using ANSYS. The accuracy of simulations heavily relies on the fidelity of CAD models, making it imperative for engineers to adopt meticulous preparation techniques. Successful integration was illustrated through real-world examples, such as in the aerospace and automotive industries, where CAD-ANSYS synergy led to improved project efficiency and accuracy. Streamlined design processes, reduced iteration cycles, and faster time-to-market were outcomes of successful integration, demonstrating the transformative impact on engineering outcomes.
To encourage readers, adopting best practices for integrating CAD models with ANSYS was emphasized. Standardizing file formats, simplifying complex geometry, and maintaining a well-defined workflow for data transfer were highlighted as essential steps. Training and skill development for engineers were underscored, recognizing the importance of deepening the understanding of both CAD and ANSYS functionalities. The call-to-action for readers is to embrace these best practices in their engineering projects, recognizing the potential for increased efficiency, accuracy, and innovation in the design and analysis processes. By aligning with these practices, engineers can optimize their workflow, mitigate integration challenges, and unlock the full potential of CAD-ANSYS integration in shaping robust and reliable mechanical systems.
In essence, the blog post serves as a comprehensive guide, covering the intricacies of CAD-ANSYS integration, providing insights into challenges, offering practical solutions, and showcasing real-world examples to underscore the transformative impact on engineering outcomes. The overarching message is clear: adopting best practices in CAD-ANSYS integration is not just a recommendation; it is a strategic imperative for engineers looking to elevate the efficiency, accuracy, and success of their engineering projects.