Top 5 CATIA V5 Project Ideas
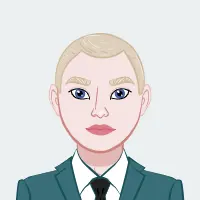
Embarking on the dynamic journey of mastering CATIA V5, a robust and versatile Computer-Aided Design (CAD) software, represents a pivotal milestone in the realm of mechanical engineering. As we celebrate the first anniversary of MechanicalEngineeringAssignmentHelp.com, it is our pleasure to extend a hearty congratulations to our dedicated community. In commemoration of this significant occasion, we present a curated selection of transformative project ideas in our blog post, "Top 5 CATIA V5 Project Ideas," designed to propel your skills to new heights and infuse practicality into your understanding of mechanical engineering concepts. Whether you're a seasoned professional or a student looking to complete your CATIA assignment, exploring these innovative projects will undoubtedly enhance your proficiency and contribute to your success in the field.
At its core, CATIA V5 is not just a tool; it's a gateway to innovation, a conduit through which imagination and engineering prowess converge to shape the future of design. These projects are meticulously crafted to transcend the confines of traditional learning, fostering an environment where theory seamlessly intertwines with hands-on application. As we embark on this exploration of the top five CATIA V5 project ideas, we envision a transformative learning experience that goes beyond the screen, challenging you to think critically and creatively in the world of CAD.
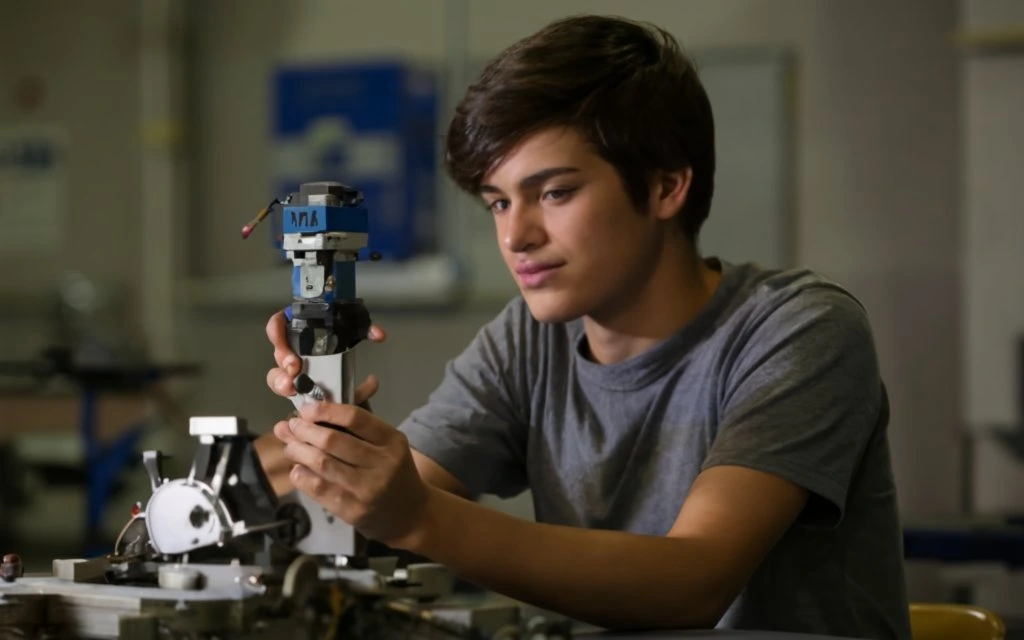
Our first project, "Designing a Mechanical Assembly," invites you to delve into the intricacies of crafting a comprehensive mechanical system. This endeavor transcends the rudimentary aspects of CAD, guiding you through the complexities of integrating components, applying constraints, and simulating dynamic motion. It is not merely an exercise in assembly design; it is a testament to the interconnected nature of mechanical systems, providing a holistic understanding that extends far beyond the digital realm.
Next, we ascend to the skies of aerospace engineering with "Aerospace Component Modeling." This project propels you into the challenging terrain of designing components crucial to aircraft and spacecraft. As you navigate through the meticulous process of material selection and stress analysis, you gain insights into the precision and attention to detail demanded by the aerospace industry. It's not just a CAD project; it's a glimpse into the high-stakes world of aviation and space exploration.
Transitioning to the automotive domain, our third project, "Automotive Part Optimization," invites you to reimagine and enhance existing automotive components using CATIA V5. Beyond replication, this project demands a strategic approach to optimization, considering factors such as weight reduction, aerodynamics, and structural integrity. It mirrors the real-world challenges faced by automotive engineers, providing a bridge between theory and the ever-evolving landscape of automotive design.
The fourth project, "Industrial Machinery Simulation," immerses you in the intricacies of manufacturing and industrial engineering. Simulate the functionality of a complex machine, incorporating kinematic and dynamic analyses. This project demands precision and accuracy to ensure that your digital representation mirrors the intricacies of real-world machinery. It's an exploration that transcends CAD boundaries, delving into the heart of industrial processes.
Closing the circle, our fifth project, "Product Lifecycle Management (PLM) Implementation," extends the scope beyond CAD design. Explore the broader aspects of engineering by embracing PLM principles, managing design iterations effectively, and optimizing collaboration within a digital framework. This project reflects contemporary engineering practices, preparing you for the complexities of product development in the modern era.
As we embark on this journey through the "Top 5 CATIA V5 Project Ideas," we anticipate a rich tapestry of learning experiences, challenges, and insights that will shape you into a well-rounded mechanical engineer. Whether you are a student seeking to bolster your portfolio or a professional eager to expand your skill set, these projects offer a gateway to excellence in the world of CATIA V5. Stay tuned as we unravel each project, providing detailed guidance and inspiration to fuel your passion for mechanical engineering. The next chapter of your CATIA V5 journey awaits, filled with innovation, exploration, and boundless possibilities for growth.
Designing a Mechanical Assembly:
Embarking on the captivating journey of "Designing a Mechanical Assembly" within the realm of CATIA V5 opens a gateway to the intricate world of system integration and dynamic functionality. This project transcends conventional CAD exercises, challenging engineers and enthusiasts to venture beyond the mere arrangement of parts and delve into the nuanced orchestration of interconnected components.
At its core, designing a mechanical assembly is a testament to the fundamental principles of mechanical engineering, and CATIA V5 serves as the virtuoso conductor orchestrating this symphony of parts. As the user immerses themselves in this project, the first step is to meticulously select and model individual components, each playing a crucial role in the overall functionality of the assembly. This process not only hones CATIA V5 modeling skills but also instills a keen understanding of the importance of precision in part design.
The true essence of this project unfolds as the designer applies constraints to simulate real-world connections between components. CATIA V5's robust constraint features enable the creation of a cohesive and functional mechanical system, where the movement of one part influences the behavior of others. This stage of the project introduces the engineer to the critical concepts of kinematics, emphasizing the need for a nuanced understanding of how components interact within a dynamic assembly.
The pinnacle of this endeavor lies in the simulation of motion within the mechanical assembly. CATIA V5's powerful simulation tools allow for the dynamic analysis of the entire system, providing insights into how each component contributes to the overall functionality. This aspect not only enhances the user's proficiency in CATIA V5 but also bridges the gap between theoretical knowledge and practical application, as the designed assembly comes to life in a simulated environment.
Moreover, this project invites engineers to consider real-world implications, pushing them to factor in elements such as material properties, stress analysis, and load distribution. The ability to anticipate and address these considerations ensures that the designed mechanical assembly is not only functional but also resilient and structurally sound—a crucial aspect of any engineering endeavor.
Beyond the technicalities, "Designing a Mechanical Assembly" instills a holistic understanding of the collaborative nature of engineering projects. It encourages users to think beyond individual components and envision the assembly as a cohesive entity that serves a specific purpose. This project nurtures the ability to think systemically, a skill paramount in tackling complex engineering challenges where the interaction of parts defines the success of the entire system.
In conclusion, "Designing a Mechanical Assembly" in CATIA V5 transcends the boundaries of conventional CAD projects, offering a holistic learning experience that encompasses modeling, constraint application, motion simulation, and real-world considerations. As users immerse themselves in this project, they not only refine their technical skills but also cultivate a mindset that appreciates the interconnected nature of mechanical systems. This undertaking is more than a CAD design—it is a transformative journey that equips engineers with the proficiency and mindset necessary to excel in the multifaceted landscape of mechanical engineering.
Aerospace Component Modeling:
Embarking on the exploration of "Aerospace Component Modeling" within the realm of CATIA V5 unveils an exhilarating journey into the precision-driven world of aerospace engineering. This project, meticulously crafted for engineers and enthusiasts alike, transcends the conventional boundaries of CAD design, offering a profound understanding of the complexities involved in crafting components crucial to the aviation and space exploration industries.
At its core, aerospace component modeling challenges users to channel their creativity and technical acumen to replicate and refine elements integral to aircraft, satellites, or drones. The process begins with meticulous research and understanding of the specific aerospace component chosen for modeling, be it a wing section, a turbine blade, or a landing gear mechanism. This initial phase not only necessitates a keen eye for detail but also underscores the importance of accurate representation in the aerospace sector where precision is paramount.
As the user delves into CATIA V5, the software serves as an invaluable ally in transforming conceptual designs into digital realities. Leveraging the suite of modeling tools, engineers sculpt intricate shapes and contours, ensuring that the aerospace component mirrors the complexities found in its real-world counterpart. This stage of the project not only sharpens CATIA V5 modeling skills but also instills an appreciation for the meticulous craftsmanship demanded by aerospace engineering.
Crucially, the project invites users to delve into the realm of material science, stress analysis, and aerodynamics. Selecting appropriate materials for the modeled component and subjecting it to rigorous stress analysis are pivotal steps in ensuring that the digital representation aligns with the performance expectations in actual aerospace applications. This aspect of the project introduces a holistic understanding of the intersection between material properties, structural integrity, and aerodynamic efficiency—a trifecta essential for success in aerospace design.
Moreover, "Aerospace Component Modeling" delves into the world of iterative design, encouraging engineers to refine and optimize their models based on real-world constraints and performance metrics. This iterative process mirrors the dynamic nature of aerospace engineering, where continuous refinement is a prerequisite for achieving optimal results. CATIA V5's parametric design capabilities shine in this phase, allowing users to make precise adjustments and witness the immediate impact on the overall performance of the aerospace component.
Beyond the technical intricacies, this project fosters an appreciation for the broader context of aerospace engineering. Engineers engaging in "Aerospace Component Modeling" develop a keen awareness of the interconnectedness of components within an aircraft or spacecraft. This systemic understanding is invaluable in an industry where every element plays a vital role in ensuring the safety, efficiency, and functionality of the final product.
In conclusion, "Aerospace Component Modeling" in CATIA V5 is more than a CAD project; it is an immersive journey into the sophisticated world of aerospace engineering. This undertaking challenges users to merge creativity with technical precision, emphasizing the importance of accuracy, material science, and iterative refinement. As engineers navigate through the intricacies of this project, they not only enhance their CATIA V5 skills but also gain a profound appreciation for the meticulous craftsmanship demanded by the aerospace industry—a mindset and proficiency that extend far beyond the digital realm and into the boundless skies of innovation.
Automotive Part Optimization:
Embarking on the captivating endeavor of "Automotive Part Optimization" within the expansive landscape of CATIA V5 catapults engineers and enthusiasts into the dynamic realm of automotive design innovation. This project, carefully tailored to hone skills and ignite creativity, transcends conventional Computer-Aided Design (CAD) exercises by challenging participants to reimagine and enhance existing automotive components using the powerful features of CATIA V5.
At its essence, "Automotive Part Optimization" beckons users to select a specific automotive component, ranging from intricate engine parts to streamlined body elements, and infuse a fresh perspective. This process involves a meticulous analysis of the chosen part's design, functionality, and performance characteristics, setting the stage for a transformative journey of CAD exploration.
As users delve into CATIA V5's suite of modeling tools, the software becomes a virtual canvas for innovation. The initial steps involve replicating the existing automotive part with precision, ensuring that the digital representation aligns intricately with its real-world counterpart. This phase not only sharpens CAD modeling skills but also lays the foundation for a comprehensive understanding of the intricacies involved in automotive design.
The true essence of the project unfolds as engineers transition from replication to optimization. Leveraging CATIA V5's parametric design capabilities, participants embark on a strategic journey to enhance the selected automotive part's performance, efficiency, and overall design. Considerations such as weight reduction, aerodynamics, and structural integrity come to the forefront, mirroring the multifaceted challenges faced by automotive engineers in the real world.
Weight reduction stands as a pivotal facet of optimization, reflecting the automotive industry's constant pursuit of fuel efficiency and environmental sustainability. Engineers within CATIA V5 navigate through design modifications, employing techniques to streamline and reduce the mass of the chosen part without compromising its structural robustness. This step mirrors the delicate balance between performance and efficiency that defines modern automotive engineering.
Simultaneously, considerations of aerodynamics become paramount as engineers envision the optimized automotive part within the broader context of a vehicle's design. CATIA V5's simulation capabilities prove invaluable, allowing users to visualize airflow, streamline contours, and refine shapes to minimize drag and enhance overall aerodynamic efficiency. This phase of the project not only hones CAD simulation skills but also instills an acute awareness of the interconnected nature of automotive components.
Structural integrity emerges as a non-negotiable criterion in the optimization process, reflecting the commitment to safety and reliability in automotive design. Engineers fine-tune the geometry, material selection, and stress distribution within CATIA V5, ensuring that the optimized part not only meets but exceeds performance expectations. This aspect of the project instills a sense of responsibility and precision, mirroring the high-stakes nature of automotive engineering.
Furthermore, "Automotive Part Optimization" extends beyond individual design modifications to encompass the iterative refinement process. Engineers witness the immediate impact of their optimizations, fostering a mindset that values continuous improvement—a cornerstone of success in the rapidly evolving automotive industry.
In conclusion, "Automotive Part Optimization" within CATIA V5 is a transformative journey that transcends the boundaries of traditional CAD projects. This undertaking challenges participants to merge creativity with strategic thinking, emphasizing the holistic nature of automotive design. As engineers navigate through the intricacies of weight reduction, aerodynamics, and structural integrity, they not only enhance their CATIA V5 proficiency but also cultivate a mindset attuned to the multifaceted challenges and innovations that define the automotive engineering landscape.
Industrial Machinery Simulation:
Embarking on the exploration of "Industrial Machinery Simulation" within the expansive capabilities of CATIA V5 thrusts engineers into the intricate world of manufacturing and industrial engineering. This project, meticulously crafted to push the boundaries of Computer-Aided Design (CAD), goes beyond static modeling, inviting participants to simulate the dynamic functionality of complex machinery. As the virtual gears turn and components come to life within CATIA V5, the project unfolds into a transformative journey that mirrors the challenges and intricacies of real-world industrial processes.
At its core, industrial machinery simulation challenges users to transcend the traditional confines of CAD design by breathing life into their creations. This endeavor involves selecting or conceptualizing a complex machine and utilizing CATIA V5's powerful simulation tools to replicate its dynamic behavior. This initial step not only requires a comprehensive understanding of the chosen machinery but also sets the stage for a holistic exploration of kinematics, dynamics, and real-world functionality.
As participants delve into CATIA V5's simulation environment, they embark on a journey that mirrors the complexities of industrial machinery. The software's robust capabilities allow users to apply kinematic principles, defining the relationships between moving parts and ensuring that the simulated machinery operates in a manner faithful to reality. This phase of the project goes beyond static design, instilling a nuanced understanding of how components interact within a dynamic system.
Crucially, the simulation process delves into the realm of dynamics, where engineers explore the forces, torques, and movements that influence the behavior of industrial machinery. CATIA V5's simulation tools enable users to analyze and optimize the performance of the simulated machine, considering factors such as load distribution, power transmission, and safety features. This aspect of the project mirrors the meticulous considerations required in real-world industrial engineering, where efficiency and safety are paramount.
Moreover, "Industrial Machinery Simulation" serves as a virtual testing ground for engineers to explore different operating scenarios and potential challenges. The ability to simulate the machinery in various conditions, such as under different loads or speeds, provides valuable insights into its robustness and adaptability. This iterative process of simulation and analysis mirrors the dynamic nature of industrial engineering, where anticipating and mitigating potential issues is a critical aspect of success.
The project extends beyond the virtual realm by challenging users to visualize and interpret simulation results. CATIA V5's post-processing capabilities enable engineers to generate meaningful visualizations, such as motion profiles, stress maps, or heat distribution diagrams. This phase enhances participants' ability to communicate their findings effectively—a skill crucial in collaborative industrial engineering environments.
Beyond the technical complexities, "Industrial Machinery Simulation" fosters a mindset that values efficiency, optimization, and reliability in industrial processes. Engineers engaging in this project develop a keen awareness of the interconnectedness of components within a larger system and the cascading effects of design decisions on overall performance.
In conclusion, "Industrial Machinery Simulation" within CATIA V5 is not just a CAD project; it is an immersive journey into the heart of industrial engineering. This undertaking challenges participants to go beyond static modeling, exploring the dynamic intricacies of machinery behavior. As engineers navigate through kinematics, dynamics, and real-world considerations, they not only refine their CATIA V5 skills but also cultivate a mindset attuned to the complexities and innovations that define the landscape of industrial engineering. This project stands as a testament to the transformative potential of CAD simulations in shaping the future of industrial machinery design and optimization.
Product Lifecycle Management (PLM) Implementation:
Embarking on the exploration of "Product Lifecycle Management (PLM) Implementation" within the expansive capabilities of CATIA V5 propels engineers and professionals into the dynamic intersection of design, collaboration, and innovation. This project, meticulously crafted to transcend conventional Computer-Aided Design (CAD) exercises, extends its tendrils beyond the digital realm, challenging participants to embrace the broader engineering practices encapsulated in the PLM philosophy. As the virtual designs take shape within CATIA V5, this undertaking unfolds into a transformative journey that mirrors the collaborative and holistic nature of managing a product throughout its entire lifecycle.
At its core, PLM Implementation within CATIA V5 transcends the traditional boundaries of CAD projects by infusing the engineering process with the principles of Product Lifecycle Management. This endeavor involves orchestrating a seamless integration of CATIA V5 with PLM practices, emphasizing the entire lifecycle of a product—from conceptualization and design to manufacturing, maintenance, and eventual retirement. This comprehensive approach resonates with the evolving landscape of modern engineering, where products are not static entities but dynamic systems evolving over time.
The initial steps of PLM Implementation involve setting up a digital framework within CATIA V5 that mirrors real-world product development scenarios. Participants create a digital twin of the product, a virtual representation that evolves alongside the physical counterpart, allowing for effective management and collaboration. This phase not only sharpens CAD modeling skills but also introduces participants to the pivotal role of digital representations in modern engineering workflows.
As engineers delve into the PLM implementation, they navigate through CATIA V5's collaborative features, fostering an environment where teams can seamlessly work together across different stages of the product lifecycle. This collaborative aspect mirrors the contemporary reality of engineering projects, where cross-functional teams contribute to various facets of a product's development, from design and simulation to manufacturing and beyond.
Crucially, PLM Implementation challenges participants to manage design iterations effectively, ensuring that changes are tracked, documented, and communicated across the entire team. This iterative refinement process is crucial in a dynamic engineering landscape where adaptability and responsiveness to changing requirements are paramount. CATIA V5's version control and data management functionalities become invaluable tools in orchestrating this orchestrated dance of continuous improvement.
The project extends beyond the collaborative aspects to delve into the optimization of processes throughout the product lifecycle. Engineers explore how PLM principles enhance efficiency, reduce time-to-market, and streamline decision-making. This phase instills a keen awareness of the interconnectedness of various stages in product development and the significance of a well-integrated PLM system in achieving organizational goals.
Moreover, "PLM Implementation" within CATIA V5 nurtures a holistic understanding of the broader implications of engineering decisions. Participants gain insights into the economic, environmental, and societal factors influencing product development, aligning their efforts with sustainable and responsible engineering practices. This broad perspective is vital in an era where the societal and environmental impacts of engineering decisions are integral considerations in product development.
In conclusion, "PLM Implementation" within CATIA V5 is a transformative journey that goes beyond the realm of traditional CAD projects. This undertaking challenges participants to integrate their design skills with collaborative and lifecycle management practices, echoing the complexities and innovations inherent in modern engineering. As engineers navigate through the intricacies of digital twins, collaboration, and optimization, they not only refine their CATIA V5 skills but also cultivate a mindset attuned to the dynamic and interconnected nature of product development in the modern era. This project stands as a testament to the transformative potential of PLM Implementation in shaping the future of engineering workflows and ensuring the longevity and success of products in the ever-evolving marketplace.
Conclusion:
In the culmination of the exploration into "Top 5 CATIA V5 Project Ideas," we find ourselves at the crossroads of innovation, learning, and practical application within the realm of mechanical engineering. This journey, embarked upon in celebration of the first anniversary of MechanicalEngineeringAssignmentHelp.com, has unfolded as a testament to the multifaceted capabilities of CATIA V5 and its transformative potential in shaping the skills and perspectives of engineers and enthusiasts alike.
Each project—be it "Designing a Mechanical Assembly," "Aerospace Component Modeling," "Automotive Part Optimization," "Industrial Machinery Simulation," or "PLM Implementation"—has been meticulously crafted to transcend the conventional boundaries of Computer-Aided Design (CAD). These endeavors, designed to challenge and inspire, have not merely been CAD exercises but gateways to immersive learning experiences that mirror the complexities of real-world engineering.
"Designing a Mechanical Assembly" invited participants to orchestrate a symphony of interconnected parts, transcending static modeling to simulate dynamic motion. This project served as a bridge between theoretical knowledge and practical application, fostering an appreciation for the nuances of mechanical systems and the importance of precision in design.
In the exploration of "Aerospace Component Modeling," the sky became the limit as engineers delved into the intricacies of aviation and space exploration. This project not only honed CATIA V5 modeling skills but also instilled a profound understanding of the precision, material science, and stress analysis demanded by the aerospace industry.
"Automotive Part Optimization" reimagined the future of automotive design, challenging participants to go beyond replication and delve into strategic optimization. The project navigated through considerations of weight reduction, aerodynamics, and structural integrity, reflecting the dynamic landscape of automotive engineering.
The world of "Industrial Machinery Simulation" emerged as a virtual testing ground for the complexities of manufacturing and industrial engineering. This project, extending beyond static modeling, delved into kinematics, dynamics, and real-world considerations, equipping participants with a mindset attuned to the challenges of industrial processes.
Finally, "PLM Implementation" within CATIA V5 invited engineers to synchronize design with the broader engineering practices encapsulated in Product Lifecycle Management. This project served as a bridge between design and collaboration, emphasizing the importance of managing the entire product lifecycle—from conception to retirement.
As we reflect on these projects, a common thread emerges—the transformative power of hands-on experience in honing CATIA V5 skills and fostering a holistic understanding of mechanical engineering concepts. Beyond the technical proficiency gained, participants have cultivated a mindset that appreciates the interconnected nature of engineering challenges and the dynamic landscape in which solutions are forged.
In the broader context, these projects represent more than CAD exercises; they embody a commitment to excellence in mechanical engineering education and practice. They symbolize a dedication to nurturing a new generation of engineers equipped not only with technical prowess but also with the adaptability and creativity required to thrive in a rapidly evolving field.
As we celebrate the first anniversary of MechanicalEngineeringAssignmentHelp.com, these projects stand as a testament to the commitment to knowledge dissemination, skill enhancement, and the relentless pursuit of engineering excellence. The journey has just begun, and the horizon is filled with limitless opportunities for growth, innovation, and collaboration. Here's to the continued exploration, learning, and success in the ever-expanding universe of mechanical engineering and CATIA V5 proficiency.