The Role of Computational Fluid Dynamics in Mechanical Engineering Assignment!
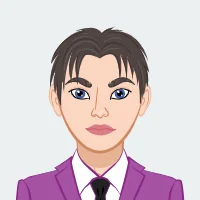
Computational Fluid Dynamics (CFD) is a powerful discipline within the realm of fluid mechanics and numerical analysis, employed to simulate and analyze the behavior of fluid flows. At its core, CFD leverages mathematical models and computational methods to solve complex fluid dynamics problems, allowing engineers and scientists to gain insights into fluid behavior without relying solely on expensive and time-consuming physical experiments. This virtual approach to fluid dynamics has become an indispensable tool in the field of mechanical engineering, revolutionizing the way engineers design and optimize systems involving fluid flow. If you find yourself in need of help with your mechanical engineering assignment, this acknowledgment of the significance of CFD in the field is designed to provide the support and insights required for success in your academic pursuits.
In the realm of mechanical engineering, CFD plays a pivotal role in understanding and predicting fluid behavior in a wide range of applications. Its significance lies in its ability to model and simulate intricate fluid dynamics scenarios, including airflow over aerodynamic surfaces, heat transfer in thermal systems, and combustion processes in engines. By providing a detailed analysis of fluid flow patterns, pressure distributions, and temperature variations, CFD enables engineers to optimize designs, improve efficiency, and ensure the reliability of mechanical systems. This transformative capability has elevated CFD to an essential aspect of the engineering design process.
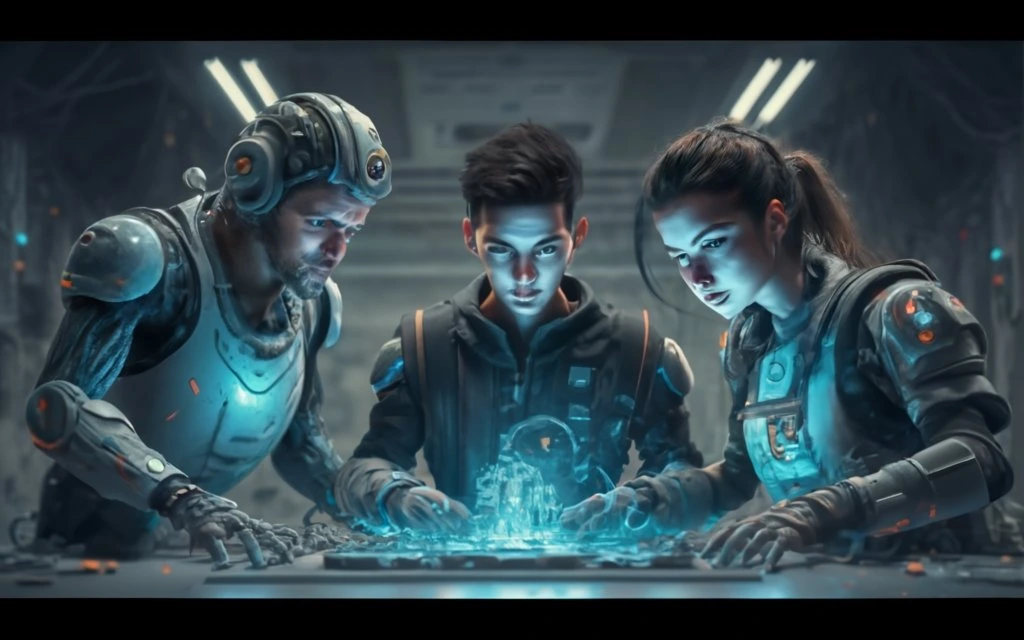
The applications of CFD are pervasive across various industries, further underlining its significance. In aerospace engineering, CFD is utilized to enhance the aerodynamic performance of aircraft, ensuring optimal lift and drag characteristics. In automotive design, CFD aids in shaping vehicles for improved fuel efficiency and reduced aerodynamic drag. The energy sector benefits from CFD simulations to optimize the performance of turbines and cooling systems in power plants. Additionally, the pharmaceutical and biomedical industries leverage CFD to model blood flow, simulate drug delivery, and design medical devices. The applications extend to environmental engineering, where CFD is employed to analyze air and water pollution dispersion, aiding in the design of effective mitigation strategies.
In the marine industry, CFD supports the development of hydrodynamic designs for ships and offshore structures, optimizing their performance in varying sea conditions. Furthermore, the role of CFD extends into the realm of architecture, where it is utilized to assess natural ventilation and thermal comfort within buildings. The multifaceted applications of CFD underscore its adaptability and relevance across diverse sectors, making it a versatile and indispensable tool for engineers and researchers alike.
In conclusion, Computational Fluid Dynamics stands as a transformative discipline within the field of mechanical engineering. Its ability to numerically model and analyze fluid dynamics has revolutionized the design process, offering engineers unprecedented insights into complex flow phenomena. The significance of CFD in mechanical engineering lies in its capacity to optimize designs, improve efficiency, and ensure the reliability of various systems. As a cornerstone technology, CFD's applications extend beyond mechanical engineering into aerospace, automotive, energy, biomedical, environmental, marine, and architectural domains, showcasing its universal importance in shaping and advancing technological innovation across industries.
Understanding Computational Fluid Dynamics (CFD)
Computational Fluid Dynamics (CFD) is a specialized branch of engineering that employs numerical methods and algorithms to simulate and analyze fluid flow, heat transfer, and associated physical phenomena. Widely used in engineering disciplines, CFD serves as a virtual laboratory, allowing engineers and scientists to gain insights into complex fluid dynamics behaviors without the need for extensive physical experiments. It finds applications in diverse fields such as aerospace, automotive, energy, environmental engineering, and more, revolutionizing the design and optimization of systems involving fluid interactions.
The development of CFD can be traced back to the mid-20th century when computers started becoming more powerful and accessible. Early attempts at numerical fluid flow simulations were made in the 1960s, but it was in the 1970s and 1980s that CFD began to take shape as a distinct discipline. Pioneering efforts by researchers like Harlow and Welch, who introduced the concept of finite difference methods, and Patankar, who developed the SIMPLE algorithm for pressure-velocity coupling, laid the groundwork for modern CFD. As computing capabilities continued to advance, CFD methodologies evolved, incorporating finite volume and finite element methods, parallel computing, and sophisticated turbulence models.
The basic principles behind CFD simulations revolve around the fundamental equations governing fluid flow, known as the Navier-Stokes equations. These equations describe the conservation of mass, momentum, and energy for fluid flow. In CFD, these partial differential equations are discrete using numerical methods to approximate the continuous fluid domain into a finite set of discrete elements or cells. The simulation domain is then divided into a grid, and within each grid cell, the governing equations are solved iteratively to predict the fluid's behavior.
One of the key numerical methods used in CFD is the Finite Volume Method (FVM). In FVM, the simulation domain is discretized into small control volumes, and the integral form of the governing equations is applied to each volume. The values of flow variables (such as velocity, pressure, and temperature) are computed at the cell centers, and the fluxes between neighboring cells are calculated. This discretization allows for the representation of complex geometries and captures the spatial variations of fluid properties.
Furthermore, turbulence, a ubiquitous and challenging aspect of fluid flow, is addressed using turbulence models. These models predict the effects of turbulence on the flow, providing insights into phenomena like eddies and vortices. Common turbulence models include the Reynolds-Averaged Navier-Stokes (RANS) equations and Large Eddy Simulation (LES), each with its level of complexity and computational cost.
In summary, Computational Fluid Dynamics is a numerical approach used in engineering to simulate and analyze fluid flow and associated phenomena. Its development over the years has been marked by advancements in numerical methods and computing power. The basic principles involve discretizing the fluid domain, applying numerical methods to solve the governing equations, and addressing complexities such as turbulence. CFD has become an invaluable tool, enabling engineers to optimize designs, predict performance, and innovate across various industries.
Applications of CFD in Mechanical Engineering:
Computational Fluid Dynamics (CFD) plays a crucial role in the design and analysis of fluid flow systems, offering engineers unparalleled insights into complex phenomena. In the realm of aerodynamics, CFD is extensively applied to optimize the design of aircraft, automobiles, and other vehicles. By simulating the airflow around these objects, engineers can analyze lift, drag, and pressure distribution, leading to aerodynamic profiles that enhance performance and fuel efficiency. Additionally, CFD aids in the design of wind turbines, optimizing blade shapes and tower configurations for maximum energy extraction in the field of renewable energy.
Heat transfer is another area where CFD proves invaluable. In thermal systems, CFD simulations allow engineers to predict temperature distributions, identify hotspots, and optimize heat exchanger designs. This is particularly critical in industries such as electronics, where efficient cooling is essential to prevent overheating and ensure the reliability of components. CFD also contributes to the design of HVAC systems in buildings, optimizing air circulation and temperature control for energy efficiency and occupant comfort.
The application of CFD extends to combustion processes in internal combustion engines and industrial furnaces. By modeling the combustion chamber, fuel injection, and exhaust systems, engineers can optimize combustion efficiency, reduce emissions, and enhance overall performance. In the field of propulsion systems, CFD is used to design rocket engines and optimize the combustion of propellants for space exploration.
Real-world applications of CFD in mechanical engineering projects are diverse and impactful. For instance, in automotive design, CFD is employed to simulate airflow over vehicle surfaces, improving fuel efficiency and minimizing drag. Formula 1 teams use CFD to optimize the aerodynamics of their racing cars, gaining a competitive edge in terms of speed and handling. In the aerospace industry, CFD is integral to the design of aircraft wings, fuselages, and engine nacelles, ensuring optimal performance and safety.
In the realm of renewable energy, CFD aids in the design of efficient wind farms. By simulating wind patterns and turbine interactions, engineers can determine the optimal layout for wind turbines, maximizing power generation and minimizing wake effects. CFD is also employed in the design of tidal and wave energy systems, analyzing the impact of fluid flow on underwater turbines and structures.
Moreover, CFD is applied in the oil and gas industry for the design of pipelines, drilling operations, and offshore platforms. By simulating fluid flow in pipelines and predicting pressure drops, engineers can optimize pipeline layouts and reduce energy consumption. In drilling operations, CFD assists in predicting the behavior of drilling fluids and optimizing drill bit designs. Offshore platform designs benefit from CFD simulations to analyze wave interactions and ensure structural integrity.
In conclusion, the application of CFD in the design and analysis of fluid flow systems is wide-ranging and impactful. Its role in optimizing aerodynamics, heat transfer, and combustion processes contributes to advancements in various industries. Real-world applications in automotive design, aerospace engineering, renewable energy, and the oil and gas sector showcase the versatility and effectiveness of CFD in addressing complex challenges and driving innovation in mechanical engineering projects.
Integration of CFD in Mechanical Engineering Assignment:
In academic settings, Computational Fluid Dynamics (CFD) is frequently incorporated into mechanical engineering assignments, offering students hands-on experience with this powerful tool. CFD assignments typically involve a combination of theoretical understanding, software application, and problem-solving skills. Students are often tasked with simulating and analyzing fluid flow scenarios, enabling them to gain practical insights into the complexities of real-world engineering challenges.
Specific CFD-related Assignment tasks may range from simulating airflow over specific geometries to analyzing heat transfer in intricate systems. For instance, students might be required to model the aerodynamics of an airfoil, investigating lift and drag characteristics under varying conditions. Another common task could involve simulating the heat dissipation in a complex electronic device to optimize its cooling system. Additionally, students may be challenged to analyze combustion processes in an internal combustion engine, considering factors such as fuel injection, turbulence, and emissions.
To approach CFD assignments effectively, students should follow a structured process. First and foremost, a solid theoretical understanding of fluid dynamics principles is crucial. This includes grasping the fundamentals of the Navier-Stokes equations, boundary conditions, and turbulence models. Practical familiarity with the CFD software being used is equally essential. Students should be comfortable with mesh generation, defining physical properties, setting boundary conditions, and interpreting simulation results.
A step-by-step approach is recommended. Begin by clearly defining the problem and objectives of the CFD assignment. Understand the geometry and boundary conditions, and choose an appropriate simulation methodology. Building a high-quality mesh is a critical step, as it directly influences the accuracy of the results. Students should pay attention to mesh refinement in areas of interest and ensure convergence is achieved during the simulation.
Interpretation of results is a key aspect of CFD assignments. Students should analyze flow patterns, pressure distributions, and temperature profiles to draw meaningful conclusions. Visualization tools within CFD software packages can aid in comprehending complex fluid dynamics phenomena. It is important for students to communicate their findings effectively, both in writing and visually, often requiring the generation of plots, graphs, and reports.
Furthermore, seeking guidance and feedback from professors or instructors is encouraged. CFD assignments can be intricate, and mentors can provide valuable insights, helping students navigate challenges and refine their approach. Collaboration with peers is another effective strategy, fostering a supportive learning environment where students can share experiences, troubleshoot issues, and enhance their collective understanding.
Time management is crucial when tackling CFD assignments, as simulations can be computationally intensive. Starting early, breaking down tasks, and allocating sufficient time for troubleshooting and refinement contribute to a more successful completion of assignments. Regular practice, engaging with relevant literature, and exploring additional CFD applications outside of assignments contribute to a deeper and more comprehensive understanding of this powerful engineering tool.
In conclusion, the incorporation of CFD into academic assignments in mechanical engineering provides students with valuable practical experience in simulating and analyzing fluid flow scenarios. Specific tasks often involve aerodynamics, heat transfer, and combustion simulations. Approaching CFD assignments effectively requires a solid theoretical foundation, practical familiarity with software tools, a structured step-by-step process, effective interpretation of results, seeking guidance, collaboration, and disciplined time management. These assignments not only reinforce theoretical concepts but also equip students with valuable skills that are highly relevant to the field of mechanical engineering.
Challenges and Solutions:
Students grappling with Computational Fluid Dynamics (CFD) Assignment often encounter a spectrum of challenges that can be both daunting and intricate. One common hurdle lies in the complexity of the CFD software itself. The multitude of features and settings, coupled with the necessity for meticulous attention to detail, can overwhelm students, especially those who are relatively new to the software. Additionally, the selection and generation of an appropriate mesh, a critical aspect of CFD simulations, poses a significant challenge. Poor mesh quality can lead to inaccurate results and difficulties in convergence, thereby affecting the overall success of the assignment. Furthermore, interpreting CFD results requires a nuanced understanding of fluid dynamics, and students may find it challenging to connect theoretical knowledge with simulation outcomes.
To overcome these challenges, students should begin by building a strong foundational understanding of fluid dynamics principles. This involves a comprehensive grasp of the governing equations, boundary conditions, and the underlying physics of fluid flow. Taking the time to thoroughly familiarize themselves with the chosen CFD software is crucial. Many software packages offer tutorials and documentation, and students should make the most of these resources to enhance their proficiency. Breaking down complex simulations into manageable steps and focusing on mastering one aspect at a time can make the overall process more approachable.
Mesh generation, a common stumbling block, can be addressed by emphasizing the importance of mesh quality over quantity. Students should focus on refining the mesh in areas of interest, ensuring a balance between computational efficiency and accuracy. Seeking guidance from professors, instructors, or peers who have experience with CFD can provide valuable insights and shortcuts to navigating these challenges. Collaborating with classmates to troubleshoot issues and share strategies can create a supportive learning environment.
Interpreting CFD results requires a deep understanding of fluid dynamics, and students can enhance this by engaging in hands-on experiments, studying real-world applications, and referring to literature in the field. Visualization tools within CFD software can assist in making sense of complex flow patterns and phenomena. Moreover, students should not hesitate to ask questions during class or seek clarification on concepts that may be unclear.
Recognizing the importance of time management is crucial when dealing with CFD Assignment. Starting assignments early allows for ample time to troubleshoot issues, refine simulations, and ensure convergence. Regular practice, not just confined to Assignment assignments, is essential. Students can explore additional CFD applications and simulations beyond the scope of their coursework to deepen their understanding.
In instances where students find themselves overwhelmed or stuck, seeking professional assistance is a prudent choice. Online forums, CFD communities, and professional tutoring services can provide valuable guidance and support. Professional assistance not only aids in troubleshooting specific issues but also offers a broader perspective on effective problem-solving approaches. Recognizing the limits of one's knowledge and seeking help when needed is a sign of resilience and proactive learning.
In conclusion, students facing challenges in CFD Assignment can navigate these obstacles by building a strong theoretical foundation, familiarizing themselves with the software, and approaching assignments in a systematic manner. Mesh generation issues can be addressed through a focus on quality, and interpreting results requires a deep understanding of fluid dynamics principles. Collaboration, time management, and seeking professional assistance when necessary are key strategies to overcome challenges and succeed in mastering the intricacies of Computational Fluid Dynamics.
Conclusion:
The blog post delves into the multifaceted role of Computational Fluid Dynamics (CFD) in the realm of mechanical engineering Assignment. It commences by defining CFD as a numerical approach that utilizes mathematical models and computational methods to simulate and analyze fluid flow, heat transfer, and associated physical phenomena. A brief historical overview traces CFD's development from its inception in the mid-20th century to its current sophistication, marked by advancements in numerical methods and computing power.
The discussion progresses to highlight the integral significance of CFD in mechanical engineering assignments, emphasizing its transformative impact on the design and optimization of fluid flow systems. In particular, CFD proves instrumental in optimizing aerodynamics, heat transfer, and combustion processes across various industries. Real-world applications illustrate its versatility, spanning automotive design, aerospace engineering, renewable energy, and the oil and gas sector. The post underscores how CFD has become an indispensable tool, shaping innovations and advancements in mechanical engineering projects.
The incorporation of CFD into academic assignments emerges as a crucial aspect of student learning. Specific CFD-related Assignment tasks and projects are explored, ranging from simulating airflow over aerodynamic surfaces to analyzing heat transfer in complex systems and optimizing combustion processes in engines. The narrative provides insights into how students can approach these assignments effectively, stressing the importance of a solid theoretical foundation, practical familiarity with CFD software, a step-by-step methodology, and effective interpretation of results.
Common challenges faced by students in CFD Assignment are addressed, including the complexity of CFD software, mesh generation issues, and the interpretation of results. Tips and solutions are offered to overcome these challenges, encouraging students to focus on mastering one aspect at a time, seeking guidance from professors and peers, and recognizing the importance of time management. The post emphasizes the value of collaboration, hands-on experimentation, and regular practice to enhance proficiency in CFD.
Crucially, the narrative reiterates the significance of CFD in the context of mechanical engineering Assignment. CFD's ability to simulate and analyze fluid flow scenarios provides students with invaluable practical experience, reinforcing theoretical concepts and equipping them with skills highly relevant to the field. The post concludes by encouraging students to explore CFD further, not only within the confines of their assignments but also by engaging in additional simulations and real-world applications. Importantly, it advocates for seeking professional assistance when needed, acknowledging that CFD assignments can be intricate, and guidance from experienced individuals or tutoring services can provide valuable insights and support.
In essence, the blog post serves as a comprehensive guide, emphasizing the transformative role of CFD in mechanical engineering Assignment, providing practical tips for effective completion of assignments, and instilling a proactive approach to learning by encouraging students to delve deeper into CFD and seek assistance when faced with challenges.