From Concept to Prototype: Designing with CREO!
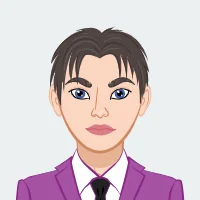
The design process holds paramount significance in the realm of mechanical engineering, serving as the intellectual backbone that transforms abstract concepts into tangible, functional realities. At its core, the design process represents the systematic and creative endeavor to conceptualize, plan, and execute the development of products, machinery, or systems. It is a comprehensive journey that spans from the initial ideation phase to the ultimate realization of a physical prototype. The meticulousness of this process is imperative, as it directly influences the efficiency, reliability, and performance of the end product. If you need assistance with your CREO assignment understanding the principles of the design process can provide a solid foundation for utilizing CREO effectively in conceptualizing, planning, and executing mechanical engineering designs.
In the multifaceted landscape of mechanical engineering, the role of computer-aided design (CAD) software emerges as a revolutionary force that has redefined and streamlined the traditional design and prototyping phases. CAD software is a technological marvel that empowers engineers and designers with tools to create, modify, analyze, and optimize designs with remarkable precision and efficiency. Gone are the days of manual drafting and tedious iterations; CAD software enables engineers to navigate through the intricate intricacies of design with unparalleled ease. This technology not only expedites the design process but also enhances the accuracy of geometric representations, ensuring that every component aligns seamlessly within the envisioned system.
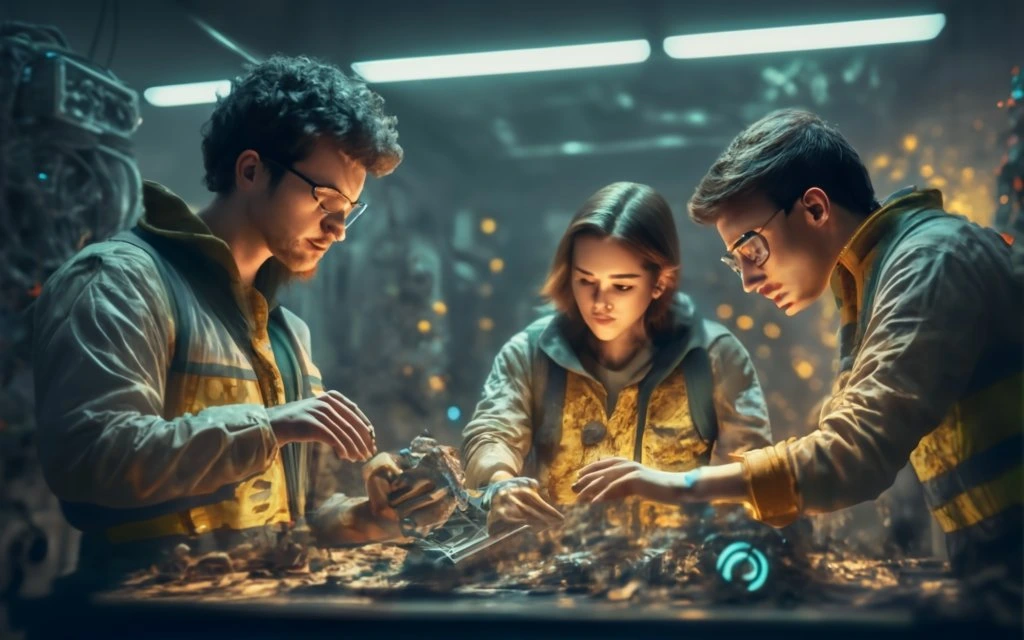
The integration of CAD software into the design workflow is transformative, offering a dynamic platform for engineers to explore and refine their ideas. One of the pivotal advantages lies in the virtual prototyping capabilities of CAD, allowing engineers to visualize and assess the functionality of their designs in a simulated environment. This not only mitigates the risks associated with physical prototyping but also accelerates the development cycle. CAD tools provide a sophisticated canvas for engineers to experiment with various design parameters, fostering innovation and enabling them to push the boundaries of conventional engineering.
Furthermore, the collaborative nature of CAD facilitates seamless communication among design teams, irrespective of geographical locations. This collaborative aspect is especially pertinent in today's globalized engineering landscape, where teams are often distributed across the globe. Real-time collaboration through CAD platforms ensures that the collective knowledge and expertise of a diverse team can be harnessed to create optimal designs. The ability to share and edit design files in a centralized digital environment promotes efficiency, accuracy, and synergy among team members.
In essence, the marriage of the design process and CAD software in mechanical engineering marks a paradigm shift. It empowers engineers to navigate the intricate web of complexities inherent in design, fostering creativity, efficiency, and collaboration. As the technological landscape continues to evolve, the symbiotic relationship between the design process and CAD software stands as a testament to the ever-expanding possibilities within the realm of mechanical engineering. It not only streamlines the journey from concept to prototype but also catalyzes innovation, setting the stage for a future where the boundaries of what is conceivable in mechanical design continue to be pushed and redefined.
Understanding the Design Process:
The design process in mechanical engineering unfolds as a meticulously orchestrated series of stages, each playing a pivotal role in the journey from conceptualization to the realization of a functional prototype. The initial stage involves conceptualization, where engineers delve into problem identification and idea generation. It is here that the overarching goals and objectives of the design are defined, setting the foundation for subsequent phases. Following conceptualization, the design moves into the preliminary design stage, where rough sketches, basic layouts, and initial concepts take form. This phase is characterized by feasibility assessments, initial calculations, and a broad exploration of potential solutions.
The subsequent detailed design stage is a cornerstone of the process, where engineers delve into the nitty-gritty details of the chosen concept. Comprehensive and intricate CAD models are developed, incorporating specific dimensions, materials, and manufacturing considerations. The emphasis on precision and accuracy during this stage is paramount, as it lays the groundwork for the seamless transition from virtual design to physical reality. Additionally, thorough analyses, such as stress and thermal simulations, are conducted to ensure that the design not only meets but exceeds performance requirements and standards.
Once the detailed design is solidified, the focus shifts to prototyping, marking the transition from the digital realm to the tangible. Prototyping is a pivotal stage where engineers validate their designs through the creation of physical models or prototypes. This step allows for hands-on testing, iteration, and refinement, providing invaluable insights into the real-world performance of the design. Prototyping serves as a crucial feedback loop, enabling engineers to identify and rectify any unforeseen issues or inefficiencies that may have eluded detection in the virtual environment.
The importance of a systematic approach throughout these stages cannot be overstated. A systematic approach ensures that each stage builds upon the foundations of the previous one, minimizing the risk of oversights or design flaws. It promotes a seamless flow of information, allowing for effective collaboration among multidisciplinary teams involved in the design process. Moreover, a systematic approach instills a sense of discipline and order, preventing the project from deviating off course and ensuring that each decision is informed by a comprehensive understanding of the overall design objectives.
In essence, the different stages of the design process in mechanical engineering coalesce into a coherent and progressive journey, where each step is a building block for the next. The systematic approach from conceptualization to prototyping is not just a procedural formality; it is a strategic imperative that underlines the reliability, efficiency, and success of the final product. It is the thread that weaves together creativity, engineering acumen, and practicality into the intricate tapestry of mechanical design.
Introduction to CREO:
CREO, developed by PTC, stands as a cutting-edge parametric computer-aided design (CAD) software, offering a comprehensive suite of tools tailored for mechanical engineering and product design. Its versatility and robust feature set make it a stalwart companion throughout the product development lifecycle. CREO's core strength lies in its parametric modeling capabilities, allowing engineers to create and modify 3D models with parametric constraints, facilitating easy design changes and updates.
One of CREO's standout features is its parametric sketching, which enables engineers to define and control geometric shapes through parameters. This parametric approach ensures design flexibility and facilitates rapid iterations, a critical aspect in the dynamic landscape of mechanical engineering. Additionally, CREO incorporates advanced assembly management tools, allowing for the creation and manipulation of complex assemblies with ease. Its assembly features support efficient collaboration among design teams working on intricate projects.
The software's parametric surfacing capabilities are noteworthy, providing engineers with the tools to create complex, organic shapes and surfaces. This is particularly crucial in industries where aerodynamics or aesthetic considerations play a significant role, allowing for the design of sleek and efficient products. Furthermore, CREO offers integrated simulation and analysis tools, enabling engineers to evaluate the structural and thermal performance of their designs within the same environment, streamlining the validation process.
The significance of CREO in the realm of mechanical engineering lies in its ability to accelerate the design process while maintaining precision and accuracy. Its parametric modeling approach ensures that design changes are propagated seamlessly throughout the entire model, eliminating the need for manual adjustments and reducing the risk of errors. This efficiency is especially crucial in industries where time-to-market is a critical factor.
CREO's adoption is widespread in the industry due to its interoperability with other engineering software and its support for industry-standard file formats. This compatibility facilitates smooth collaboration between different teams and ensures that CREO seamlessly integrates into existing workflows. Moreover, the software's user-friendly interface and extensive online community contribute to its popularity, as engineers can easily access resources, tutorials, and support to enhance their proficiency with the tool.
In conclusion, CREO stands as a preferred choice in the mechanical engineering industry due to its parametric modeling capabilities, advanced assembly management, parametric surfacing, integrated simulation tools, and widespread industry adoption. Its ability to streamline the design process, promote collaboration, and ensure accuracy makes it an indispensable tool for engineers engaged in designing a wide array of mechanical products and systems.
Key Features and Tools in CREO:
CREO encompasses a myriad of features and tools that play a pivotal role in enhancing the efficiency and effectiveness of the design process in mechanical engineering. One notable feature is the parametric modeling capability, which allows engineers to define design parameters and constraints. This enables the creation of flexible designs, facilitating swift adjustments and iterations without the need for extensive manual modifications. The parametric approach in CREO ensures that changes made at any stage of the design are automatically reflected throughout the entire model, promoting consistency and reducing the likelihood of errors. This feature significantly contributes to the efficiency of the design process by enabling designers to respond promptly to design iterations, modifications, or changing requirements.
Another key asset is the advanced assembly management tools within CREO. These tools enable engineers to model and manipulate complex assemblies with ease, facilitating the creation of intricate products composed of numerous components. The software provides a hierarchical structure for assembling parts, allowing for efficient visualization and management of the entire assembly. This feature streamlines collaboration among design teams working on different parts of a project, as each team can focus on specific components without sacrificing the integrity of the overall design. The result is a more organized and efficient design process, with seamless coordination between various elements of the assembly.
CREO's parametric surfacing capabilities contribute significantly to the effectiveness of the design process, particularly in industries where complex, freeform shapes are prevalent. The software allows for the creation of intricate surface geometries, vital in the design of aerodynamic components or aesthetically pleasing products. This feature empowers designers to explore innovative and unconventional design concepts, ensuring that the final product meets both functional and aesthetic requirements. By providing the tools to easily manipulate and refine surfaces, CREO fosters a design environment where creativity is not limited by technical constraints, ultimately resulting in more effective and visually appealing products.
Integrated simulation and analysis tools within CREO add another layer of efficiency to the design process. Engineers can perform structural and thermal analyses directly within the CAD environment, allowing for real-time feedback on the performance of the design. This integration eliminates the need for separate simulation software, reducing the time and effort required to validate and refine the design. The ability to simulate and analyze designs within the same platform ensures that potential issues are identified early in the process, minimizing the risk of costly modifications during later stages of development.
In conclusion, the specific features and tools within CREO, such as parametric modeling, advanced assembly management, parametric surfacing, and integrated simulation, collectively contribute to a design process characterized by efficiency and effectiveness. By streamlining tasks, fostering collaboration, and providing real-time feedback, CREO empowers engineers to navigate the complexities of mechanical design with agility and precision, ultimately leading to the creation of high-quality products in a timely manner.
Real-world Applications:
CREO has played a pivotal role in numerous successful projects across various mechanical engineering applications, showcasing its versatility and effectiveness in the design and prototyping phases. One notable example is in the automotive industry, where CREO has been instrumental in designing complex vehicle components. In a case study involving a leading automaker, CREO's parametric modeling capabilities were utilized to create intricate 3D models of engine components, ensuring precise geometric representations. The software's ability to handle large assemblies and intricate designs allowed the engineering team to efficiently iterate through various design alternatives, leading to the development of high-performance and reliable automotive components.
In the aerospace sector, CREO demonstrated its prowess in the design of aircraft structures and components. In a project involving the development of a new aircraft wing, CREO's advanced assembly management tools were crucial in integrating numerous parts and ensuring the structural integrity of the entire assembly. The parametric surfacing capabilities of CREO were employed to model aerodynamic surfaces with precision, contributing to the overall efficiency of the design process. The ability to simulate and analyze the structural performance of the wing within the same software platform allowed for rapid validation and refinement, ultimately leading to the successful prototyping of an aerodynamically optimized and structurally sound aircraft wing.
In the consumer electronics industry, CREO has been employed in the design of innovative and compact electronic devices. In a project focused on developing a portable medical device, CREO's parametric modeling features facilitated the creation of a compact and ergonomic design. The software's parametric sketching capabilities allowed for quick adjustments to accommodate changes in device specifications, ensuring adaptability throughout the design process. The resulting prototype not only met stringent design criteria but also highlighted the versatility of CREO in addressing the unique challenges posed by the consumer electronics sector.
Furthermore, in the machinery manufacturing domain, CREO has proven its effectiveness in designing intricate machinery components. A case study involving the creation of a precision machining tool showcased CREO's ability to model complex geometries and ensure the seamless integration of moving parts. The advanced assembly management tools facilitated the assembly of intricate components, while parametric surfacing capabilities allowed for the creation of precision surfaces critical for the tool's functionality. The integrated simulation tools in CREO enabled engineers to validate the performance of the machining tool, ensuring that it met the required tolerances and efficiency standards.
These diverse case studies exemplify CREO's adaptability and effectiveness in addressing the unique challenges posed by various mechanical engineering applications. Whether in automotive design, aerospace engineering, consumer electronics, or machinery manufacturing, CREO consistently proves to be a versatile and indispensable tool, contributing to the success of projects through efficient design and prototyping processes.
Tips and Best Practices:
Effectively utilizing CREO in the design process requires adherence to practical tips and best practices that enhance productivity and streamline workflows. First and foremost, it is crucial to invest time in mastering the parametric modeling capabilities of CREO. Engineers should become proficient in defining parameters, constraints, and relationships to create flexible designs that can easily adapt to changes. Regularly updating design intent and ensuring a clear understanding of parametric relationships will prevent issues during modifications.
Additionally, organization plays a pivotal role in using CREO effectively. Establishing a systematic approach to naming conventions, file structures, and version control is essential. This promotes collaboration within design teams and ensures that files are easily locatable and identifiable. Regularly saving incremental versions allows for easy rollback in case modifications lead to undesired outcomes, maintaining a robust project history.
When dealing with large assemblies, efficient use of CREO's advanced assembly management tools becomes crucial. Utilizing simplified representations, LOD (Level of Detail) functionality, and grouping related components aids in improving system performance and accelerates the design process. Managing the complexity of assemblies by using modular design principles and subassemblies ensures a more streamlined and organized workflow.
Parametric surfacing tools in CREO are powerful but require careful consideration. Engineers should invest time in understanding surface continuity, curvature, and manipulation tools to create aesthetically pleasing and functionally efficient designs. Continuous refinement and validation through simulations and analyses contribute to the overall success of the design process.
Common challenges in using CREO include dealing with software updates, system compatibility issues, and the potential for file corruption. To mitigate these challenges, it is advisable to stay informed about software updates and ensure compatibility with the operating system and hardware. Regularly backing up files, employing version control, and utilizing backup and recovery features within CREO can safeguard against data loss and file corruption.
Collaboration is key in many engineering projects, and CREO provides features to facilitate this. Using collaborative tools, such as product data management (PDM) systems, ensures that design changes are tracked, and multiple team members can work concurrently on different aspects of a project. Effective communication within the team is essential, and utilizing CREO's annotation and commenting features fosters clear communication of design intent and revisions.
In conclusion, effective utilization of CREO in the design process involves mastering parametric modeling, maintaining organizational discipline, optimizing assembly management, and addressing common challenges through proactive measures. By incorporating these practical tips and best practices, engineers can harness the full potential of CREO to streamline their design workflows, enhance collaboration, and overcome challenges encountered during the design process.
Conclusion:
In the blog post "From Concept to Prototype: Designing with CREO," we delved into the significance of the design process in mechanical engineering and highlighted how computer-aided design (CAD) software, specifically CREO, plays a crucial role in streamlining this process. We explored different stages of the design process, emphasizing the importance of a systematic approach from conceptualization to prototyping. CREO's key features, such as parametric modeling, advanced assembly management, parametric surfacing, and integrated simulation, were discussed in detail, showcasing their contribution to efficient and effective design across diverse applications like automotive, aerospace, consumer electronics, and machinery manufacturing. Several case studies underscored CREO's versatility and success in real-world projects, exemplifying its adaptability in addressing unique challenges within various engineering domains. Practical tips and best practices for using CREO effectively were also shared, covering aspects like parametric modeling mastery, organization, assembly management, parametric surfacing, and integrated simulation. Challenges such as software updates and system compatibility were addressed, providing solutions for a smoother design workflow.
Looking ahead, the future of mechanical engineering design is likely to witness trends such as the integration of AI and machine learning for automated design tasks, increased emphasis on cloud-based collaboration, augmented and virtual reality technologies for immersive design experiences, and a heightened focus on sustainability. These trends align with broader technological advancements shaping the field of engineering design.
In conclusion, we encourage readers to explore CREO for their own mechanical engineering projects. Whether you're an aspiring engineer or a seasoned professional, CREO's features and capabilities provide a powerful toolkit for realizing innovative designs. Its versatility in handling complex assemblies, parametric surfacing, and integrated simulation makes it a go-to solution for a wide range of industries. By incorporating CREO into your design process, you can enhance efficiency, foster collaboration, and navigate the complexities of modern engineering challenges. Stay updated on the latest developments from CREO, as advancements in CAD technology continue to push the boundaries of what is achievable in mechanical design. Embrace CREO to unlock your creative potential and streamline your journey from concept to prototype in the dynamic world of mechanical engineering.