Embracing Digital Prototyping in Mechanical Engineering with CATIA!
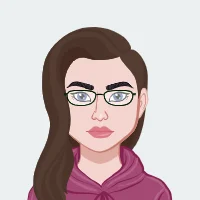
Digital prototyping has emerged as a transformative approach in the realm of mechanical engineering, redefining traditional methods of product development and design. At its core, digital prototyping involves the creation and simulation of a product's virtual model before physical prototypes are constructed. This revolutionary methodology has gained prominence for its ability to enhance efficiency, reduce costs, and accelerate the entire product development lifecycle. In the dynamic field of mechanical engineering, where precision and innovation are paramount, embracing digital prototyping has become more than just a trend—it's a necessity, offering assistance with your CATIA assignment and ensuring proficiency in this essential aspect of mechanical design.
In the fast-paced world of mechanical engineering, where rapid iterations and design modifications are commonplace, digital prototyping offers a paradigm shift from conventional, time-consuming practices. This approach involves the use of advanced computer-aided design (CAD) tools, such as CATIA, to create detailed three-dimensional models that simulate the behavior and functionality of the proposed product. Unlike traditional prototyping methods that rely on physical models for testing and validation, digital prototyping enables engineers to explore multiple design variations virtually, fostering a more iterative and agile design process.
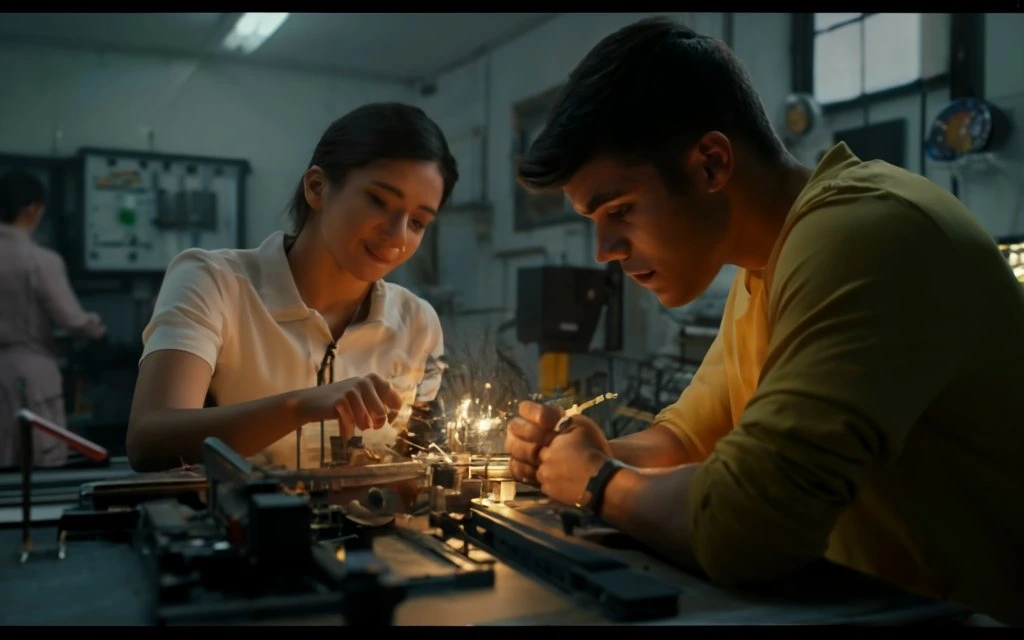
The importance of embracing digital tools like CATIA in the field of mechanical engineering cannot be overstated. CATIA, a leading CAD software, stands out as a robust solution that empowers engineers to translate their creative ideas into reality through comprehensive digital prototyping. Its extensive suite of features includes parametric modeling, simulation, and analysis tools, providing engineers with a holistic platform to design, visualize, and evaluate their concepts. By leveraging CATIA's capabilities, mechanical engineers can seamlessly transition from the conceptual phase to the detailed design stage, fostering a more streamlined and integrated workflow.
One key aspect of digital prototyping is the ability to conduct virtual testing and analysis, a crucial step in ensuring the robustness and reliability of mechanical designs. CATIA facilitates a range of simulations, including stress analysis, thermal analysis, and motion analysis, enabling engineers to identify potential flaws and optimize designs before physical prototypes are produced. This not only accelerates the product development timeline but also significantly reduces costs associated with material wastage and iterative physical prototyping.
Moreover, embracing digital prototyping with tools like CATIA promotes enhanced collaboration among cross-functional teams. With the ability to create a shared virtual environment, engineers, designers, and other stakeholders can collaborate in real-time, fostering effective communication and synergy throughout the design process. This collaborative approach minimizes the likelihood of errors, encourages knowledge sharing, and ultimately results in a more cohesive and well-informed product development strategy.
In conclusion, the integration of digital prototyping, especially through powerful tools like CATIA, marks a pivotal advancement in the field of mechanical engineering. Beyond the realm of CAD, digital prototyping has become a cornerstone for innovation, providing engineers with the means to push the boundaries of design, conduct comprehensive analysis, and deliver high-quality products in a more efficient and cost-effective manner. Embracing this transformative approach is not just a technological leap; it's a strategic imperative for those seeking to thrive in the ever-evolving landscape of mechanical engineering.
Understanding Digital Prototyping:
Digital prototyping is a transformative approach in the product development process, revolutionizing the way engineers conceptualize, design, and iterate on new products. Unlike traditional prototyping methods that often involve physical models, digital prototyping leverages advanced computer-aided design (CAD) software and simulation tools to create a virtual representation of a product. This digital representation encompasses not only the product's physical form but also its behavior under various conditions and scenarios.
One of the key distinctions between digital and traditional prototyping lies in the tangible versus the virtual. Traditional prototyping typically involves the creation of physical models or prototypes, which can be time-consuming and resource-intensive. These models may only capture certain aspects of the product, and changes often require the production of entirely new physical prototypes. Digital prototyping, on the other hand, enables engineers to create, test, and refine designs in a virtual environment. This not only accelerates the design iteration process but also allows for more comprehensive exploration of design alternatives without the need for constant physical reconstruction.
The significance of digital prototyping in the product development process cannot be overstated. One of its major advantages is the substantial reduction in costs associated with physical prototyping. Traditional prototyping often involves the fabrication of multiple iterations, each incurring additional expenses for materials, labor, and time. Digital prototyping minimizes these costs by allowing engineers to make iterative changes to the virtual model without the need for constant physical reconstruction. This efficiency not only accelerates the design process but also significantly cuts down on the overall expenses associated with prototyping.
Moreover, digital prototyping contributes to improved efficiency throughout the product development lifecycle. The virtual nature of digital prototypes facilitates seamless collaboration among cross-functional teams. Designers, engineers, and other stakeholders can work concurrently on the same digital model, enabling real-time feedback and collaboration. This collaborative environment fosters better communication and alignment among team members, reducing the likelihood of errors and ensuring that all aspects of the design are thoroughly considered.
In conclusion, digital prototyping stands as a revolutionary paradigm in product development, providing a virtual canvas for engineers to ideate, design, and refine products with unprecedented efficiency. Its departure from traditional prototyping methods translates into cost savings, faster design iterations, and enhanced collaboration. As the manufacturing industry continues to evolve, embracing digital prototyping becomes not just a technological advancement but a strategic imperative for companies seeking to stay competitive and innovative in the ever-changing landscape of product development.
Introduction to CATIA:
CATIA (Computer-Aided Three-Dimensional Interactive Application) stands as a pinnacle in the realm of computer-aided design (CAD) and product lifecycle management (PLM) software. Its history traces back to the late 1970s when it was developed by the French company Dassault Systèmes. Initially designed for aerospace projects, CATIA has since evolved into a comprehensive suite of applications serving various industries, with a significant stronghold in the mechanical engineering sector.
CATIA's journey commenced with a focus on addressing the complex design and engineering needs of the aerospace industry. Over the years, it has expanded its capabilities to cater to diverse sectors, including automotive, industrial equipment, and consumer goods. Its versatility and adaptability have contributed to its widespread use, making it an integral part of the product development process for countless engineering projects.
The core features of CATIA are designed to empower engineers and designers in creating, simulating, and optimizing 3D models. Its parametric modeling capabilities allow for the creation of intricate and customizable designs, ensuring precision and efficiency in the engineering process. CATIA's extensive range of tools encompasses sketching, part design, assembly design, and drafting, providing a holistic environment for engineers to bring their ideas to life.
In the field of mechanical engineering, CATIA has emerged as an industry standard for digital prototyping and product design. The software excels in facilitating the entire product development lifecycle, from conceptualization to manufacturing. One of its standout features is its robust digital prototyping capabilities, which enable engineers to simulate and analyze the behavior of complex mechanical systems in a virtual environment. This functionality proves invaluable in identifying potential issues, refining designs, and optimizing performance before any physical prototypes are created.
CATIA's prowess in digital prototyping extends to finite element analysis (FEA), enabling engineers to assess the structural integrity and mechanical behavior of components under various conditions. This not only accelerates the design iteration process but also contributes to cost savings by minimizing the need for physical prototypes and extensive testing.
Moreover, CATIA's collaborative features foster teamwork by allowing multiple engineers to work on the same project simultaneously. This real-time collaboration enhances efficiency and ensures that all team members are working with the latest design data.
In conclusion, CATIA's rich history, versatile features, and widespread adoption in the mechanical engineering industry underscore its significance in shaping the future of product design and development. Its commitment to providing a comprehensive suite of tools for digital prototyping and product design cements CATIA as an indispensable asset for engineers and companies striving for innovation and excellence in the ever-evolving landscape of mechanical engineering.
Key Features of CATIA for Digital Prototyping:
CATIA (Computer-Aided Three-Dimensional Interactive Application) stands out as a powerhouse in the realm of digital prototyping, offering an array of tools and features that significantly enhance the mechanical engineering design process. At the forefront of CATIA's capabilities is its robust 3D modeling functionality. Engineers can create intricate and detailed 3D models of mechanical components with precision, facilitating a comprehensive visualization of the product. This capability is invaluable in understanding the spatial relationships and interactions between different parts, contributing to the development of more accurate and efficient designs.
Furthermore, CATIA excels in simulation, enabling engineers to subject their designs to various virtual scenarios. The software provides a diverse range of simulation tools, including stress analysis, thermal analysis, and dynamic simulations. Engineers can assess how different factors impact the performance of a product under various conditions, allowing for informed design decisions. This not only accelerates the product development cycle but also minimizes the need for physical prototypes, reducing costs and enhancing overall efficiency.
CATIA's prowess extends to analysis, offering sophisticated tools that aid engineers in evaluating the structural integrity, durability, and performance of their designs. The software's finite element analysis (FEA) capabilities empower engineers to simulate and analyze the behavior of complex structures, identifying potential issues and optimizing designs before they reach the physical prototyping stage. This ensures that the final product meets high standards of quality and reliability.
In real-world applications, CATIA has played a pivotal role in the aerospace industry. For instance, Boeing extensively used CATIA in the design and development of the 787 Dreamliner. The software facilitated the creation of intricate 3D models of the aircraft components, allowing engineers to simulate various flight conditions and optimize the design for fuel efficiency and aerodynamics. This application of CATIA contributed to the Dreamliner's success as a fuel-efficient and technologically advanced aircraft.
Another noteworthy example comes from the automotive sector, where companies like BMW utilize CATIA for designing and prototyping their vehicles. The software aids in creating detailed 3D models of car components, simulating crash tests, and analyzing the structural integrity of the vehicle. This not only streamlines the design process but also enhances safety and performance.
In conclusion, CATIA's contribution to digital prototyping in mechanical engineering is unparalleled. Its 3D modeling, simulation, and analysis features empower engineers to create, test, and refine designs with remarkable precision. Real-world success stories in aerospace and automotive industries underscore CATIA's role in revolutionizing product development, making it an indispensable tool for those seeking excellence in the field of mechanical engineering.
Benefits of Embracing CATIA in Mechanical Engineering:
In the dynamic realm of mechanical engineering, the incorporation of Computer-Aided Three-Dimensional Interactive Application (CATIA) into the workflow offers multifaceted advantages that transcend traditional design methodologies. One key area where CATIA shines is in fostering collaboration among engineering teams. By providing a centralized platform for design, analysis, and simulation, CATIA facilitates seamless communication and coordination. This collaborative environment not only enhances the exchange of ideas but also ensures that all team members are working with the most up-to-date information, reducing the likelihood of errors and miscommunications.
Furthermore, CATIA's robust suite of tools significantly streamlines the design processes within mechanical engineering projects. Its intuitive 3D modeling capabilities empower engineers to create intricate designs with precision and efficiency. The parametric modeling feature allows for easy modification of design parameters, enabling quick iterations and adaptations. This not only accelerates the design phase but also empowers engineers to explore various design alternatives with agility. The integration of simulation and analysis tools within CATIA further optimizes the design process, enabling engineers to evaluate the performance and behavior of their designs in a virtual environment before physical prototypes are produced.
Several industry studies and case studies underscore the tangible benefits of incorporating CATIA into the mechanical engineering workflow. According to a survey conducted by a leading engineering association, teams using CATIA reported a significant reduction in design errors and iterations compared to those relying on traditional design methods. This reduction not only saves time but also minimizes the overall project costs associated with rectifying errors during later stages of development.
A compelling case study involves a prominent aerospace engineering firm that adopted CATIA for the design of a complex aircraft component. The firm reported a remarkable 30% reduction in design time, attributing this efficiency gain to CATIA's parametric modeling and simulation capabilities. The virtual prototyping facilitated by CATIA allowed the engineering team to identify potential issues early in the design phase, leading to fewer design modifications during the later stages of development. Consequently, the project was completed ahead of schedule, showcasing the tangible impact of CATIA on project timelines and outcomes.
In conclusion, the advantages of incorporating CATIA into the mechanical engineering workflow are manifest in enhanced collaboration, streamlined design processes, and improved overall project outcomes. With its robust features and proven track record, CATIA emerges as a pivotal tool for modern mechanical engineering endeavors, empowering teams to innovate, iterate, and succeed in an ever-evolving technological landscape.
Conclusion:
In the realm of mechanical engineering, the adoption of digital prototyping has emerged as a transformative force, revolutionizing traditional design and development processes. This blog explores the pivotal role of Computer-Aided Three-Dimensional Interactive Application (CATIA) in advancing digital prototyping and underscores its significance in contemporary mechanical engineering projects.
Digital prototyping, a paradigm shift from conventional methods, has become integral to product development. Its advantages are manifold, encompassing cost reduction, increased efficiency, and enhanced collaboration. CATIA, a prominent player in the digital design arena, stands out for its robust features and widespread use in the industry. Offering a comprehensive suite of tools, CATIA empowers engineers to navigate the intricate landscape of 3D modeling, simulation, and analysis with unparalleled precision.
Delving into CATIA's key features, the blog demystifies the software's capabilities for readers unfamiliar with its intricacies. From its seamless 3D modeling to sophisticated simulation capabilities, CATIA emerges as a versatile companion in the engineer's toolkit. Real-world examples and success stories further illustrate how CATIA contributes to elevating design processes, streamlining workflows, and ultimately enhancing project outcomes.
The post also illuminates the manifold benefits of integrating CATIA into mechanical engineering projects. Beyond the tangible advantages, such as improved efficiency and reduced development costs, CATIA fosters a collaborative environment that nurtures innovation. With a focus on facilitating cross-disciplinary collaboration, the software enables engineers to converge their expertise, leading to holistic and well-rounded project outcomes.
To drive these points home, the blog provides a compelling case study or practical example, showcasing the tangible impact of CATIA in a specific mechanical engineering project. By elucidating the challenges faced, the solutions derived through CATIA, and the positive outcomes achieved, readers gain a firsthand insight into the software's transformative potential.
In conclusion, the blog reinforces the key takeaways: the indispensability of digital prototyping in modern mechanical engineering and the pivotal role that CATIA plays in this paradigm. Readers are encouraged to not merely understand these concepts but to actively embrace them in their professional endeavors. A call to action urges readers to explore the possibilities that CATIA unlocks and consider integrating it into their own projects. The narrative extends beyond the confines of the blog, inviting comments and fostering discussions among the audience. This engagement is crucial, as it catalyzes a community of learning, sharing, and evolving within the dynamic realm of digital prototyping and mechanical engineering.