Dynamic Force Analysis for Crank-Connecting Rod Mechanisms Assignments
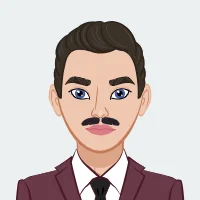
Dynamic force analysis is a crucial component of mechanical engineering, particularly when dealing with intricate systems such as crank and connecting rod mechanisms. This type of analysis is essential for gaining a comprehensive understanding of how these mechanical systems behave under dynamic conditions, which involve varying forces and movements over time. By examining the interaction between different components and their responses to applied forces, engineers can uncover detailed insights into system performance, stability, and efficiency.
Dynamic force analysis helps in identifying critical aspects of mechanical behavior, such as the impact of angular velocities, accelerations, and forces transmitted through the system. It enables engineers to assess how changes in design parameters, such as component masses, lengths, and input velocities, affect the overall dynamics of the system. This understanding is vital for optimizing mechanical designs, ensuring that they meet required performance specifications, and predicting potential issues before they arise in practical applications.
Furthermore, dynamic force analysis supports the validation of theoretical models by comparing predicted results with experimental or simulated data. This process helps in refining models and improving accuracy in engineering predictions. By integrating both analytical approaches and simulation tools, engineers can achieve a more holistic view of system behavior, making it possible to address complex challenges and enhance the reliability of mechanical systems.
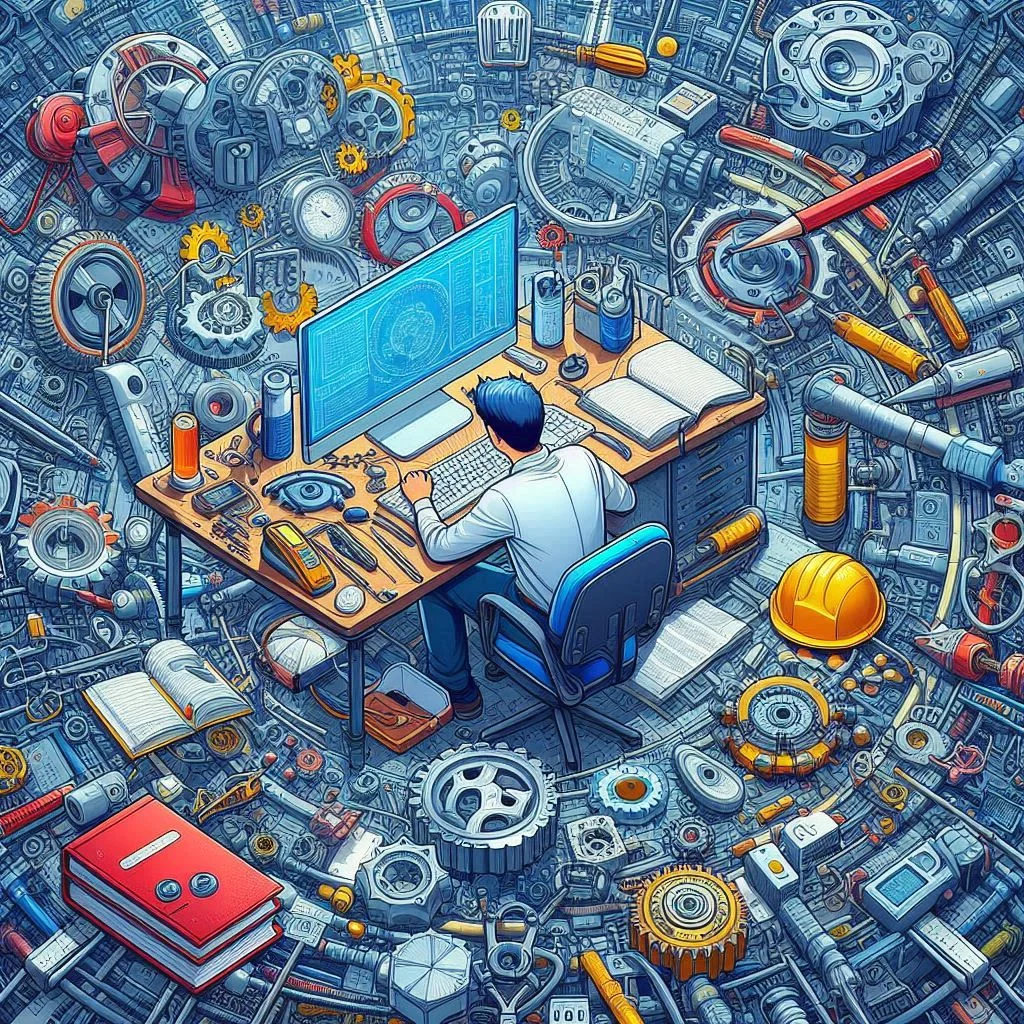
In essence, a thorough dynamic force analysis not only contributes to more effective and reliable engineering solutions but also plays a significant role in advancing the field of mechanical engineering through the development of innovative and efficient mechanical systems. Utilizing a dynamics assignment helper can further enhance this process by providing expert guidance and support.
Understand the Assignment Requirements
Before starting any analysis, it is crucial to fully understand the assignment requirements to ensure you address all aspects comprehensively. Utilizing a mechanical engineering assignment helper can provide additional guidance and clarity. Here’s how you can approach this step:
1. Review the Assignment Brief Thoroughly
Carefully read the assignment description to grasp the objectives and expectations. Identify key elements such as the type of analysis required, specific parameters to be evaluated, and any constraints or assumptions provided.
2. Identify Core Components and Objectives
Determine the primary components of the system under analysis. For example, in a crank-connecting rod mechanism, these components might include:
- Crank: The rotating part that drives the system.
- Connecting Rods: Linkages that transfer motion between the crank and the slider.
- Slider: The component that converts rotational motion into linear motion.
Understand the main objectives of the assignment, such as:
- Conducting a dynamic force analysis.
- Performing kinematic and kinetic analyses.
- Graphically illustrating results.
- Analyzing and varying different system parameters.
- Comparing results from different methods.
3. Define Key Parameters and Variables
Identify and list all key parameters that need to be considered. Common parameters in such assignments may include:
- Angular Velocities: The rate of rotation of each linkage.
- Angular Accelerations: The rate of change of angular velocities.
- Forces Transmitted: The forces acting through the system components.
- Input Torque: The torque required to maintain the prescribed angular velocity.
- Out-of-Balance Forces: Forces arising due to imbalances in the system.
Note any specific values or ranges provided in the assignment, such as masses, lengths, or angular velocities.
4. Understand the Methods and Tools Required
Determine the methods and tools required for the analysis. This might include:
- Software Packages: Such as MATLAB, Mathcad, or others approved by the course.
- Analytical Methods: Equations and theories provided in your course materials.
- Simulation Tools: Like Working Model 2D for comparison with theoretical results.
5. Clarify Assumptions and Constraints
Note any assumptions you need to make, such as:
- Neglecting Certain Forces: Like gravity or friction.
- Simplifications: Such as treating each linkage as a slender rod.
Understand any constraints that may affect your analysis, such as the plane of motion or limitations of the software tools.
6. Plan Your Approach
Develop a structured plan to tackle the assignment:
- Kinematic Analysis: Outline how you will determine angular velocities and accelerations.
- Kinetic Analysis: Plan how to calculate forces and torques.
- Graphical Representation: Decide on the type of graphs and plots needed.
- Parameter Variation: Plan how to vary parameters and what impact to observe.
- Comparative Analysis: Outline how you will compare different methods and discuss discrepancies.
By carefully understanding and organizing these elements, you can ensure a thorough and methodical approach to completing your dynamic force analysis assignment.
Performing Kinetic Analysis
Kinetic analysis involves evaluating the forces and torques acting on the crank-connecting rod mechanism, based on the kinematic results obtained earlier. This step is essential for understanding the internal and external forces within the system and ensuring that the system operates under desired conditions. Here’s how to conduct a thorough kinetic analysis:
1. Create Free Body Diagrams
Begin by drawing free body diagrams (FBDs) for each component of the mechanism:
- Crank: Identify the forces acting on the crank, including the applied torque and any reactive forces from the connecting rods.
- Connecting Rods: Show the forces transmitted through the connecting rods, including the forces from the crank and any reactions at the points where the rods connect to the slider and crank.
- Slider: Illustrate the forces acting on the slider, including the force exerted by the connecting rods and any other external forces.
2. Formulate Force and Torque Equations
Develop equations to describe the forces and torques acting on each component:
- Forces in Components: Write equations that express the forces in the crank, connecting rods, and slider based on the kinematic results. Consider factors such as the mass of the components and their accelerations.
- Torque Calculations: Determine the torque required to maintain the prescribed angular velocity of the crank. This involves calculating the input torque needed to overcome the forces and maintain consistent motion.
3. Calculate Forces and Torques
Use the formulated equations to compute the required forces and torques:
- Force Calculations: Calculate the forces transmitted through each component by substituting the kinematic results (such as velocities and accelerations) into your equations.
- Torque Calculations: Compute the input torque required to keep the crank rotating at the specified angular velocity. This involves determining the torque needed to balance out the forces acting on the crank.
4. Analyze Out-of-Balance Forces
Examine the out-of-balance forces that arise due to the prescribed angular velocity of the crank:
- Identify Imbalances: Determine any forces that are not perfectly balanced, which may lead to vibrations or uneven loading on the system.
- Quantify Imbalances: Calculate the magnitude and direction of these out-of-balance forces to assess their impact on system performance.
5. Verify and Validate Results
Ensure the accuracy and consistency of your kinetic analysis results:
- Compare with Simulations: Cross-check your results with those obtained from simulation tools (e.g., Working Model 2D) to ensure they are consistent.
- Review Theoretical Predictions: Compare your findings with theoretical predictions from course materials or analytical equations.
6. Document Assumptions and Simplifications
Clearly outline any assumptions or simplifications made during the kinetic analysis:
- Neglected Effects: Note if certain effects, such as friction or external disturbances, were not considered in the analysis.
- Idealizations: Document any idealizations used, such as assuming frictionless components or neglecting minor forces.
By carefully performing these steps, you will gain a detailed understanding of the forces and torques in the crank-connecting rod mechanism. This analysis is crucial for ensuring that the system operates efficiently and reliably, and for making informed design decisions.
Graphical Representation
Graphical representation involves visualizing the results of your kinematic and kinetic analyses through various types of charts and plots. This step helps in interpreting and communicating the data effectively, allowing you to see trends, compare results, and understand system behavior more clearly. Here’s how to approach graphical representation:
1. Plot Kinematic Data
Create graphs to illustrate the motion of the components:
- Position vs. Time: Plot the position of key components, such as the crank and slider, against time. This helps visualize how the positions change over the course of the crank’s rotation.
- Velocity vs. Time: Graph the velocities of the crank, connecting rods, and slider over time. This provides insights into how quickly each component is moving and how their speeds vary during operation.
- Acceleration vs. Time: Show the accelerations of the crank and other components as a function of time. This helps in understanding the changes in speed and the forces acting on the system.
2. Plot Kinetic Data
Visualize the forces and torques involved in the system:
- Forces vs. Time: Create plots for the forces transmitted through the crank, connecting rods, and slider over time. This helps in understanding how the forces vary during operation and identifying any peak loads or fluctuations.
- Torque vs. Time: Graph the input torque required to maintain the crank’s angular velocity. This shows how the torque changes with time and helps in evaluating the energy requirements for the system.
3. Represent Out-of-Balance Forces
Visualize the out-of-balance forces that result from the system’s operation:
- Out-of-Balance Forces vs. Time: Plot these forces to understand their impact on the system. This can help identify any vibrations or instability issues caused by these forces.
- Magnitude and Direction: Use vector plots to show the direction and magnitude of out-of-balance forces, helping to visualize their impact on the system.
4. Compare Analytical and Simulation Results
Create comparative graphs to evaluate the accuracy of different methods:
- Analytical vs. Simulation Data: Plot results from analytical calculations alongside those from simulation tools (e.g., Working Model 2D). This allows you to compare theoretical predictions with simulated results and discuss any discrepancies.
- Different Scenarios: If the analysis includes varying parameters (e.g., mass, length), plot results for different scenarios to show how changes in design affect system performance.
5. Ensure Clarity and Accuracy
Make sure that your graphs are clear and accurately represent the data:
- Label Axes: Clearly label the axes with appropriate units and descriptions.
- Legend and Titles: Include legends and titles for each plot to explain what the graph represents.
- Data Points and Trends: Ensure that data points are plotted accurately and that trends are easily distinguishable.
6. Document the Graphical Analysis
Provide a comprehensive explanation of the graphs:
- Interpret Results: Explain what each graph shows and how it relates to the system’s behavior. Discuss any significant trends, peaks, or anomalies observed.
- Discuss Comparisons: If comparing different methods or scenarios, provide a detailed discussion of the results and any insights gained.
By effectively using graphical representation, you can visually communicate the results of your kinematic and kinetic analyses, making it easier to interpret the data, identify key trends, and make informed decisions about the system’s design and performance.
Parameter Variation
Adjusting key parameters in your system is essential for understanding how sensitive the system's performance is to changes in its design and operating conditions. This process helps to identify the critical parameters that significantly influence the system’s behavior and ensures robustness in various scenarios. Here’s how to approach parameter variation:
Mass Variations
- Crank Mass: Alter the mass of the crank and observe how it affects the system's dynamics. Increased mass may result in higher inertia, impacting the angular acceleration and required input torque.
- Connecting Rod Mass: Change the mass of the connecting rods, keeping in mind that heavier rods could lead to higher forces and altered dynamic behavior.
- Piston Mass: Adjust the mass of the pistons to see how it influences the overall system. Heavier pistons could affect the slider's motion and the forces transmitted through the connecting rods.
Analysis of Impact: Document how variations in mass affect key parameters like forces, torques, and accelerations. Determine whether increased mass leads to higher forces or changes in the system’s stability and performance.
Length Variations
- Crank Length: Modify the length of the crank and examine how this impacts the motion of the system. Longer cranks can increase the stroke length but may also alter the torque requirements and dynamic forces.
- Connecting Rod Length: Adjust the length of the connecting rods to analyze how this affects the kinematic and kinetic behavior. Changes in rod length can influence the system’s range of motion and force transmission.
Analysis of Impact: Evaluate how changes in length affect the angular velocities, accelerations, and forces within the system. Look for any significant changes in performance or behavior due to these adjustments.
Velocity Adjustments
- Angular Velocity of the Crank: Modify the constant angular velocity of the crank and analyze how it affects the dynamic forces and torques. Different velocities can lead to varying levels of force and acceleration, impacting the overall system performance.
Analysis of Impact: Assess how changes in the crank’s angular velocity influence the system’s dynamics. Determine whether higher or lower velocities result in significant differences in the forces, torques, and stability of the system.
Comparative Analysis
Comparing your findings with results from simulation tools and theoretical predictions is crucial for validating your analysis and ensuring the accuracy of your results. Here’s how to perform a thorough comparative analysis:
Simulation Comparison
- Software Results: Compare the results obtained from simulation tools like Working Model 2D with your numerical results. This helps in verifying the accuracy of your calculations and understanding how well your analytical model aligns with practical simulations.
- Simulation Data: Evaluate the consistency between simulated results and your analytical findings. Look for patterns or discrepancies that might indicate areas for improvement or further investigation.
Analysis of Differences: Discuss any variations observed between simulation results and analytical results. Consider factors such as model assumptions, boundary conditions, or numerical approximations that may contribute to discrepancies.
Analytical Comparison
- Theoretical Predictions: Compare your results with theoretical predictions based on established equations or course materials. This helps in validating your analytical approach and ensuring that your results are consistent with theoretical expectations.
- Analytical Data: Review the theoretical results alongside your calculated data to check for agreement. Identify any deviations and investigate potential reasons for these differences.
Analysis of Differences: Explain any discrepancies between theoretical predictions and your findings. Discuss possible reasons such as simplifications, assumptions, or errors in the analysis that could account for differences.
Discuss Differences
- Identify Discrepancies: Clearly outline and discuss any differences observed between the various methods of analysis. Provide a detailed explanation of why these discrepancies might occur.
- Possible Reasons: Consider potential reasons for differences, including variations in assumptions, modeling approaches, or computational methods. Address any limitations in your analysis or simulation that might have contributed to the observed discrepancies.
Conclusion
In summary, conducting a dynamic force analysis of mechanical systems, such as crank-connecting rod mechanisms, involves a comprehensive approach that integrates kinematic and kinetic analysis with graphical representation and parameter variation. Each step is crucial for understanding the system’s behavior and ensuring its optimal performance.
Key Takeaways:
- Kinematic Analysis: By examining the motion of the system, you establish a foundation for understanding how different components interact. Accurate position, velocity, and acceleration data are essential for subsequent kinetic analysis.
- Kinetic Analysis: This step involves evaluating the forces and torques acting on the system. Calculating forces transmitted through the crank, connecting rods, and slider, as well as determining the input torque and out-of-balance forces, helps ensure that the system can operate efficiently and reliably.
- Graphical Representation: Visualizing data through graphs and plots enhances your ability to interpret results. Position, velocity, acceleration, force, and torque graphs provide insights into the system’s dynamics and performance. Comparative graphs allow you to validate results against simulations and theoretical predictions.
- Parameter Variation: Adjusting key parameters such as mass, length, and angular velocity helps assess the system’s sensitivity to changes. Understanding how variations affect the system’s behavior is crucial for optimizing design and ensuring robust performance under different conditions.
- Comparative Analysis: Comparing results from simulations, theoretical predictions, and analytical calculations helps verify the accuracy of your analysis. Identifying and explaining any discrepancies ensures that the results are reliable and that any differences are understood and addressed.
Overall, a thorough and systematic approach to dynamic force analysis not only helps in solving specific assignments but also builds a deeper understanding of mechanical systems' behavior. This knowledge is vital for designing, analyzing, and optimizing complex mechanical systems, ensuring that they perform effectively and meet design specifications. By following these steps and continuously comparing results with simulations and theoretical models, you can achieve a comprehensive understanding of the system and make informed decisions about its design and operation.