Designing High-Efficiency Heat Exchanger
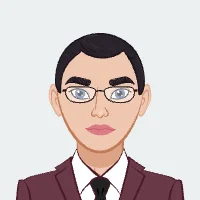
Designing a heat exchanger, particularly a shell-and-tube type for industrial applications, is a complex and rewarding engineering task that demands a deep understanding of thermal and hydraulic principles. This blog offers a comprehensive framework to assist students in effectively addressing similar engineering assignments. By following this structured approach, students can ensure that their analysis is thorough, their design choices are well-founded, and their solutions are both practical and academically robust.
Whether you are dealing with cooling systems for petrochemical plants or other high-demand industrial processes, the principles of heat exchanger design remain crucial. The assignment involves not just theoretical calculations but also practical considerations such as material selection, flow arrangements, and performance evaluation. A well-designed heat exchanger can significantly impact the efficiency and cost-effectiveness of industrial operations, making it a key component in many engineering projects.
In this blog, we will explore the essential steps involved in designing a heat exchanger, from initial problem definition to detailed performance analysis and reporting. We will cover how to calculate heat duty, select appropriate materials, and justify design choices, ensuring that you are well-prepared to handle the complexities of such assignments. Additionally, we will delve into the use of simulation tools to validate theoretical calculations and refine your design.
By adhering to this approach, students will be equipped to tackle assignments with confidence, applying both theoretical knowledge and practical skills to achieve effective and efficient heat exchanger designs. For additional support, students seeking heat transfer assignment help can benefit from expert resources to enhance their understanding and application of these critical concepts.

Understanding the Assignment
When approaching a heat exchanger design assignment, it’s essential to first grasp the core objectives and constraints of the task. Heat exchangers, especially shell-and-tube types used in industrial applications, play a crucial role in thermal management systems by transferring heat between fluids. The design process involves a multi-faceted analysis that integrates theoretical principles with practical engineering constraints. For those seeking additional support, mechanical engineering assignment help can provide valuable insights and guidance to navigate the complexities of heat exchanger design and ensure a successful outcome.
Introduction to the Task:
The primary goal of a heat exchanger design assignment is to create a system that meets specific thermal performance criteria while addressing real-world operational constraints. This typically includes cooling or heating fluids to desired temperatures, ensuring efficient heat transfer, and maintaining acceptable pressure drops. Understanding these goals is fundamental to developing a successful design.
Core Objectives:
- Heat Duty Calculation: Accurately determine the amount of heat that needs to be transferred between fluids. This involves calculating the required heat duty based on the temperature differences and flow rates, which directly influences the size and type of heat exchanger you select.
- Selection of Heat Exchanger Type: Choose the most suitable heat exchanger configuration for the given application. For many industrial processes, the shell-and-tube heat exchanger is a preferred choice due to its effectiveness in handling large flow rates and high pressures. Understanding why this type is appropriate involves considering factors like thermal performance, cost, and space constraints.
- Design Constraints: Address real-world constraints such as space limitations, material availability, and cost considerations. These factors will influence your design choices, including tube specifications, shell side design, and flow configuration.
Comprehensive Approach:
By thoroughly understanding the assignment’s objectives and constraints, you can systematically approach the design process. This involves integrating theoretical calculations with practical considerations, such as material selection and simulation analysis. The goal is to design a heat exchanger that not only meets the required performance criteria but also operates efficiently and cost-effectively within the given constraints.
Design Considerations
When designing a heat exchanger, particularly for industrial applications, several critical factors must be carefully considered to ensure optimal performance and efficiency. Here’s a detailed look at the key design considerations:
1. Tube Specifications
- Material Selection: Choose appropriate materials for the tubes based on thermal conductivity, corrosion resistance, and mechanical strength. Common materials include stainless steel, copper, and aluminum, each offering different advantages in terms of heat transfer efficiency and durability.
- Tube Dimensions: Determine the size and diameter of the tubes. Larger diameters can handle higher flow rates but may increase the overall size of the heat exchanger. The choice of diameter affects the heat transfer area and pressure drop.
- Tube Arrangement: Decide on the arrangement of the tubes within the heat exchanger. Options include square or triangular pitch arrangements. Triangular pitch typically provides better heat transfer efficiency but may complicate cleaning and maintenance.
2. Shell Side Design
- Number of Shell Passes: Choose the number of shell passes, which affects the heat transfer and pressure drop. Multiple passes can enhance heat transfer but may increase complexity and cost.
- Baffle Design: Design the baffles to direct the flow of the shell-side fluid, improving heat transfer by increasing the turbulence and ensuring that the fluid flows across the tubes. Proper baffle spacing and configuration are crucial to optimizing performance and minimizing pressure drops.
- Baffle Spacing: Determine the appropriate spacing between baffles to balance heat transfer efficiency with pressure drop. Closely spaced baffles increase turbulence but also the pressure drop across the shell side.
3. Flow Configuration
- Flow Arrangement: Select the flow arrangement (counterflow, parallel flow, or crossflow) based on the desired heat transfer efficiency. Counterflow arrangements are often preferred for their superior heat exchange capabilities, as they allow fluids to flow in opposite directions, maximizing the temperature gradient and heat transfer.
- Flow Distribution: Ensure uniform flow distribution across the heat exchanger to avoid areas of high or low performance. Proper distribution improves overall efficiency and reduces the risk of localized hot or cold spots.
4. Thermal and Hydraulic Performance
- Heat Transfer Coefficient: Calculate the overall heat transfer coefficient, which is crucial for determining the heat exchanger’s efficiency. This involves analyzing both the thermal conductivity of materials and the flow dynamics within the exchanger.
- Surface Area: Determine the required surface area for heat transfer based on the calculated heat duty. Adequate surface area ensures that the heat exchanger can handle the specified thermal loads without excessive temperature differences.
- Pressure Drop: Analyze the pressure drop on both the shell and tube sides. Excessive pressure drop can lead to higher energy consumption and operational costs. Optimize the design to maintain pressure drops within acceptable limits.
5. Fouling Considerations
- Fouling Factor: Account for potential fouling, which can reduce heat transfer efficiency over time. Incorporate a fouling factor into your design to estimate the impact of deposits or scaling on performance.
- Maintenance and Cleaning: Design the heat exchanger to facilitate easy maintenance and cleaning. Consider features such as removable baffles or clean-out ports to address fouling issues effectively.
6. Economic Analysis
- Cost of Materials: Estimate the cost of materials used in the heat exchanger construction. Balance material costs with performance requirements to achieve a cost-effective design.
- Fabrication and Operation Costs: Calculate the costs associated with fabrication, installation, and operation. Perform a cost-benefit analysis to ensure that the design offers good value for money while meeting performance criteria.
- Lifecycle Costs: Consider the total lifecycle costs, including maintenance and energy consumption. An efficient design should minimize long-term operational costs and provide a good return on investment.
By addressing these design considerations, students can develop heat exchanger systems that are efficient, reliable, and suited to their specific applications. A well-considered design not only meets performance requirements but also balances practical constraints and economic factors.
Performance Analysis
Conducting a thorough performance analysis is essential for evaluating the effectiveness of a heat exchanger design. This phase involves assessing various parameters to ensure that the heat exchanger operates efficiently and meets the specified requirements. Here’s a detailed breakdown of the key aspects of performance analysis:
1. Thermal Analysis
- Heat Transfer Coefficient Calculation: Determine the overall heat transfer coefficient (U), which reflects the effectiveness of heat transfer between the fluids. This involves calculating both the convective heat transfer coefficients on the shell and tube sides, as well as the thermal resistance of the tube material. The overall heat transfer coefficient is crucial for determining the heat exchanger’s performance.
- Required Surface Area: Calculate the surface area required for effective heat transfer. This is based on the heat duty, overall heat transfer coefficient, and the log mean temperature difference (LMTD) or the effectiveness-NTU method. Ensure that the heat exchanger surface area is sufficient to handle the thermal load without excessive temperature differences.
- Temperature Profiles: Analyze the temperature profiles of the fluids throughout the heat exchanger. Ensure that the temperature changes are consistent with the design requirements and that the outlet temperatures meet the desired specifications.
2. Pressure Drop Calculation
- Shell Side Pressure Drop: Calculate the pressure drop across the shell side of the heat exchanger. This involves evaluating the effects of baffle design, flow arrangement, and shell pass configuration. Excessive pressure drop can lead to higher pumping costs and reduced system efficiency.
- Tube Side Pressure Drop: Determine the pressure drop across the tube side by considering factors such as tube diameter, length, and flow arrangement. Ensure that the pressure drop remains within acceptable limits to maintain efficient operation.
- Total Pressure Drop: Calculate the total pressure drop for the entire heat exchanger system, which includes contributions from both the shell and tube sides. Assess whether the total pressure drop aligns with system requirements and operational constraints.
3. Fouling Factor Analysis
- Impact of Fouling: Consider the effect of fouling on heat exchanger performance. Fouling can lead to reduced heat transfer efficiency and increased pressure drop over time. Incorporate a fouling factor into your design to account for these potential issues.
- Design for Cleaning: Ensure that the heat exchanger design allows for regular maintenance and cleaning to manage fouling. This may include features such as removable baffles or access ports.
4. Economic Analysis
- Cost-Benefit Analysis: Perform a cost-benefit analysis to evaluate the economic feasibility of the heat exchanger design. This includes assessing the initial costs of materials and fabrication, as well as ongoing operational and maintenance costs.
- Lifecycle Costs: Consider the total lifecycle costs, including energy consumption, maintenance, and potential repairs. A cost-effective design should offer a good balance between performance and long-term operational expenses.
5. Simulation and Validation
- Simulation Results: Use simulation software to model the heat exchanger and validate your theoretical calculations. Tools such as HTRI, Aspen HYSYS, or ANSYS Fluent can provide detailed insights into thermal performance, pressure drops, and temperature profiles.
- Comparison with Theoretical Calculations: Compare the simulation results with your theoretical calculations to identify any discrepancies. Analyze the reasons for any differences and refine your design if necessary.
6. Reporting and Documentation
- Detailed Report: Compile a comprehensive report that includes all performance analysis results. Provide detailed calculations, simulation data, and performance metrics.
- Design Choices: Discuss the rationale behind design choices and how they impact performance. Explain how the heat exchanger meets the required specifications and operational constraints.
- Recommendations: Offer recommendations for potential improvements or adjustments based on your analysis. Highlight any areas where the design could be enhanced to achieve better performance or cost efficiency.
By conducting a rigorous performance analysis, students can ensure that their heat exchanger designs meet all operational and economic requirements. This thorough evaluation helps to confirm that the heat exchanger will perform effectively in its intended application and provides a solid foundation for any necessary adjustments or optimizations.
Simulation and Validation
Simulation and validation are crucial steps in the heat exchanger design process, providing a means to verify theoretical calculations and assess the practical performance of the design. These steps help ensure that the heat exchanger operates as intended and meets all performance criteria. Here’s a detailed approach to simulation and validation:
1. Simulation Modeling
- Choosing Simulation Software: Select appropriate simulation tools to model the heat exchanger. Popular software options include HTRI, Aspen HYSYS, ANSYS Fluent, and COMSOL Multiphysics. Each tool offers various features for thermal and hydraulic analysis, so choose one that aligns with your specific needs and design complexity.
- Developing the Model: Create a detailed model of the heat exchanger in the chosen simulation software. This involves inputting parameters such as:
- Geometric Details: Tube dimensions, shell configuration, baffle design, and flow arrangement.
- Material Properties: Thermal conductivity, specific heat capacity, and density of the fluids and construction materials.
- Operating Conditions: Inlet and outlet temperatures, flow rates, pressure conditions, and fouling factors.
- Defining Boundary Conditions: Set up boundary conditions for the simulation, including the inlet and outlet temperatures, flow rates, and pressure conditions. Ensure that these conditions accurately reflect the real-world operating environment of the heat exchanger.
2. Running the Simulation
- Performing the Analysis: Execute the simulation to analyze the heat exchanger’s thermal and hydraulic performance. The simulation will provide data on heat transfer rates, temperature profiles, pressure drops, and flow distribution.
- Analyzing Results: Review the results to evaluate the performance of the heat exchanger. Key metrics to assess include:
- Heat Transfer Efficiency: Ensure that the heat transfer rate meets the design requirements and that the overall heat transfer coefficient aligns with theoretical predictions.
- Temperature Profiles: Analyze the temperature distribution across the heat exchanger to verify that the outlet temperatures are within the specified limits.
- Pressure Drops: Check the pressure drops on both the shell and tube sides. Ensure that they are within acceptable limits to maintain efficient operation.
3. Validation Against Theoretical Calculations
- Comparing Results: Compare the simulation results with theoretical calculations performed during the design phase. Look for discrepancies and analyze their causes. Common differences might arise from assumptions made during theoretical analysis or from simplifications in the model.
- Refining the Design: Based on the comparison, make any necessary adjustments to the design. This could involve changing tube dimensions, modifying baffle configurations, or adjusting flow arrangements to improve performance.
- Sensitivity Analysis: Perform sensitivity analyses to understand how variations in key parameters affect the heat exchanger’s performance. This helps in identifying critical factors that influence efficiency and stability.
4. Documenting and Reporting
- Compiling Results: Document the simulation results in detail, including all relevant data, graphs, and charts. Provide a clear explanation of how the results validate the design.
- Explaining Discrepancies: Discuss any discrepancies between theoretical and simulated results. Offer insights into potential causes and the steps taken to address them.
- Providing Recommendations: Based on the simulation and validation results, offer recommendations for design improvements or adjustments. Highlight any areas where the design can be optimized for better performance or cost efficiency.
- Final Report: Prepare a comprehensive report that includes:
- Introduction: Overview of the simulation objectives and methodology.
- Model Description: Details of the simulation model and boundary conditions.
- Results and Analysis: Presentation of simulation results, comparisons with theoretical calculations, and analysis of performance.
- Conclusions and Recommendations: Summary of findings and suggestions for any necessary design changes.
By rigorously applying simulation and validation techniques, students can ensure that their heat exchanger designs are both theoretically sound and practically feasible. This process not only helps in confirming design performance but also provides valuable insights into potential improvements and optimizations.
Reporting Your Findings
A well-structured report is crucial for communicating the results of your heat exchanger design project. It provides a comprehensive overview of the design process, performance analysis, and any insights gained from simulations. Here’s a guide to structuring and presenting your findings effectively:
1. Introduction
- Background and Objectives: Briefly describe the purpose of the heat exchanger design assignment, including the specific objectives and constraints. Explain why this design is important and what goals were set for the project.
- Problem Statement: Summarize the problem statement, detailing the industrial application and the performance requirements for the heat exchanger. This sets the context for the design and analysis.
2. Methodology
- Design Approach: Outline the approach taken for designing the heat exchanger. Include the key design considerations such as material selection, tube specifications, shell side design, and flow configuration.
- Calculation Methods: Describe the theoretical methods and formulas used for calculating heat duty, heat transfer coefficients, pressure drops, and other relevant parameters. Explain any assumptions made during the calculations.
- Simulation Procedure: Detail the simulation process, including the software used, model setup, boundary conditions, and any parameters specific to the simulation. Explain how the model was validated against theoretical calculations.
3. Design and Performance Analysis
- Design Details: Provide a detailed description of the heat exchanger design, including diagrams and specifications. Include:
- Heat Exchanger Type and Configuration: Explain the choice of the shell-and-tube design and any specific configurations used.
- Tube and Shell Side Design: Include details on tube materials, dimensions, baffle design, and flow arrangements.
- Thermal Performance: Present the results of the thermal analysis, including:
- Heat Transfer Coefficient: Show the calculated overall heat transfer coefficient and how it compares with design expectations.
- Temperature Profiles: Include temperature distribution graphs and explain how the heat exchanger meets the thermal requirements.
- Hydraulic Performance: Report on the pressure drop calculations, including:
- Pressure Drop on Shell and Tube Sides: Provide data and graphs showing the pressure drops and discuss whether they are within acceptable limits.
- Fouling Considerations: Discuss the impact of fouling on performance and any measures taken to address it.
4. Simulation Results
- Simulation Data: Present the results from the simulation software, including:
- Thermal Performance Metrics: Include graphs and tables showing simulated heat transfer rates, temperature profiles, and overall efficiency.
- Pressure Drop Analysis: Provide simulated pressure drop data and compare it with theoretical predictions.
- Comparison with Theoretical Results: Analyze any discrepancies between the simulation results and theoretical calculations. Discuss possible reasons for these differences and their implications for the design.
- Sensitivity Analysis: If conducted, present the results of sensitivity analyses and explain how variations in key parameters affect performance.
5. Conclusions and Recommendations
- Summary of Findings: Summarize the key findings from the design and performance analysis. Highlight how well the design meets the specified objectives and any notable achievements or shortcomings.
- Recommendations for Improvement: Offer suggestions for potential design improvements based on the analysis and simulation results. Address any issues identified during the project and propose solutions or optimizations.
- Future Work: Suggest areas for further research or development. This could include exploring alternative designs, refining simulation models, or addressing additional constraints.
6. Supporting Documentation
- Diagrams and Charts: Include all relevant diagrams, charts, and tables that support your analysis. Ensure these are clearly labeled and referenced in the text.
- Appendices: Provide detailed calculations, additional simulation results, and any other supplementary information in the appendices. This allows readers to review the supporting data in detail if needed.
By following this structure, you can create a comprehensive and well-organized report that effectively communicates your heat exchanger design and performance analysis. A clear and detailed report not only demonstrates your understanding of the design process but also provides valuable insights and recommendations for future improvements.
Conclusion
In conclusion, the design and analysis of the shell-and-tube heat exchanger have demonstrated a thorough approach to meeting the industrial requirements for cooling a hot process fluid. This project successfully addressed key objectives, including efficient heat transfer, manageable pressure drops, and economic feasibility. Here’s a summary of the findings and insights:
1. Design Achievements
The chosen shell-and-tube heat exchanger design effectively fulfills the specified requirements for cooling the process fluid from 200°C to 80°C while using water as the coolant. The design parameters, including tube material, dimensions, and shell-side configuration, were selected to optimize thermal performance and pressure drop, ensuring that the cooling water temperature does not exceed 70°C at the outlet.
2. Performance Evaluation
The performance analysis confirmed that the heat exchanger design meets the necessary thermal and hydraulic criteria. The calculated heat transfer coefficient and the required surface area align with the design goals, showing that the heat exchanger can handle the specified heat duty efficiently. Pressure drop calculations were within acceptable limits, ensuring that the design does not impose excessive energy costs on the pumping system. The temperature profiles across the heat exchanger indicated that the design effectively achieves the desired cooling of the process fluid.
3. Simulation Insights
Simulation results provided valuable validation of the theoretical calculations. The comparison between simulated and theoretical results revealed some discrepancies, which were analyzed and addressed. The simulation also helped refine the design by highlighting areas for potential improvement. The accuracy of the simulation model was validated against theoretical predictions, confirming that the design is robust and capable of performing as expected in real-world conditions.
4. Lessons Learned
Several challenges were encountered during the design and analysis phases, including managing the trade-offs between heat transfer efficiency and pressure drop. These challenges were addressed through careful design adjustments and iterative simulations. Effective strategies included optimizing tube arrangements and baffle designs to balance performance and cost. The project underscored the importance of detailed performance analysis and simulation in validating design choices and ensuring reliability.
5. Recommendations
Based on the analysis and simulation results, the following recommendations are proposed:
- Design Optimization: Further optimization of tube dimensions and baffle configurations could enhance heat transfer efficiency and reduce pressure drops. Exploring alternative tube materials or coatings might also improve performance and longevity.
- Fouling Management: Implementing design features that facilitate easier cleaning and maintenance can mitigate the impact of fouling and maintain performance over time.
- Future Research: Investigating alternative heat exchanger configurations or materials could provide additional insights into improving efficiency and reducing operational costs.
6. Final Thoughts
The heat exchanger design project has achieved its primary goals by delivering a solution that meets the required thermal and hydraulic performance criteria. The thorough analysis and validation process has ensured that the design is both effective and feasible for the specified application. This project highlights the critical role of detailed performance analysis and simulation in engineering design, providing a solid foundation for future improvements and advancements in heat exchanger technology.