Top Numerical Methods Every Mechanical Engineer Should Know
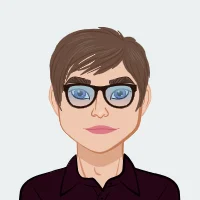
Numerical methods are a cornerstone of modern engineering practice, providing essential tools for solving complex mathematical problems that are often intractable through analytical methods. In solving mechanical engineering assignment, these methods enable the analysis and design of systems that are too complicated to be described with simple equations. From fluid dynamics to structural analysis, numerical methods are applied in various domains to predict behavior, optimize performance, and ensure reliability.
The use of numerical methods involves creating discrete models that approximate continuous systems, solving algebraic or differential equations, and interpreting the results to make informed engineering decisions. This process is crucial in scenarios where experimental methods are impractical or too costly. For mechanical engineers, mastering numerical methods is not just about understanding the theory but also about applying these techniques to real-world problems, enhancing their problem-solving toolkit.
In this blog, we will explore some of the top numerical methods that every mechanical engineer should know. We will delve into their principles, applications, and how they aid in the mathematical modeling of various processes such as casting and solidification, metal forming, and welding.
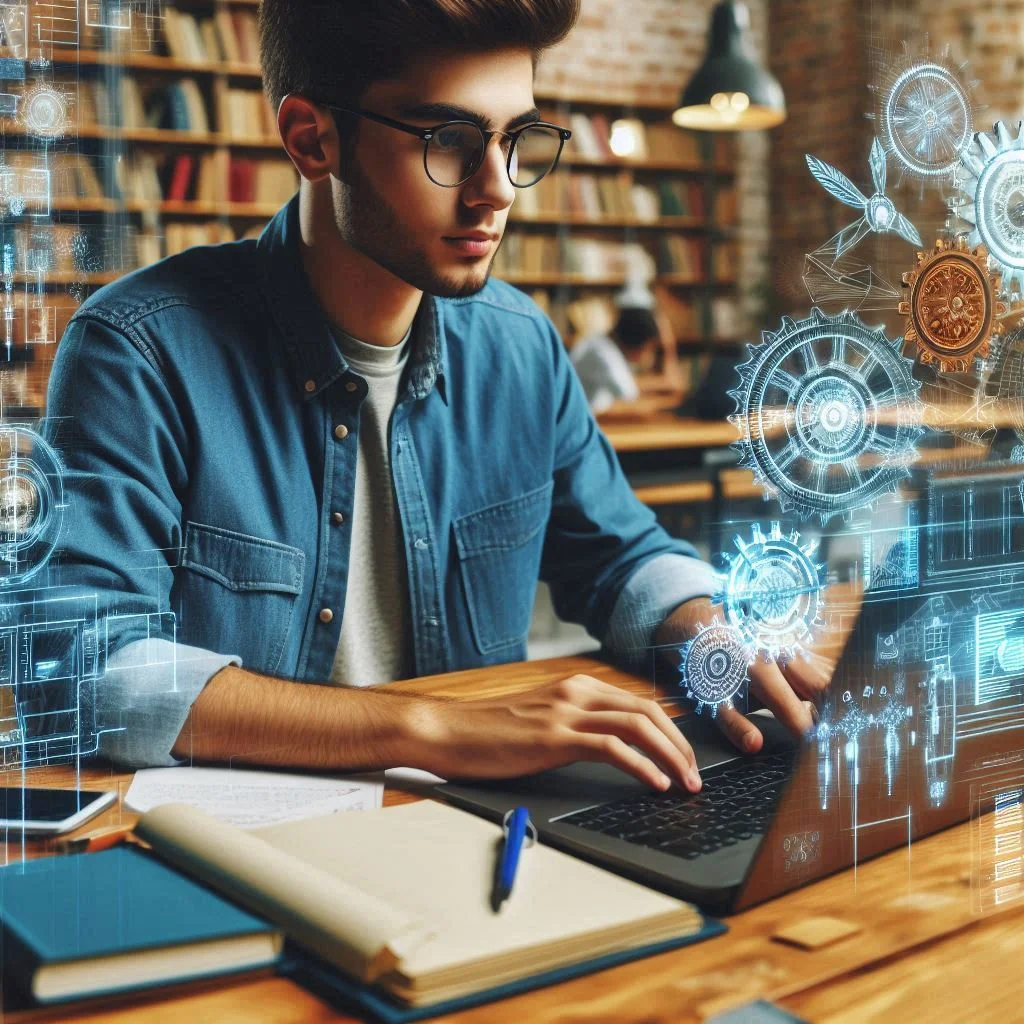
Mathematical Model Development
Mathematical model development is a fundamental aspect of engineering analysis and design, providing a systematic approach to represent complex physical systems through mathematical equations. These models serve as the foundation for numerical methods, enabling engineers to simulate, predict, and optimize the behavior of engineering systems under various conditions. This section delves deeper into the process of developing mathematical models, highlighting their importance, the steps involved, and their application in mechanical engineering.
Importance of Mathematical Models
Mathematical models are essential tools in engineering for several reasons:
- Prediction and Simulation: Models allow engineers to predict the behavior of systems before physical prototypes are built. This capability is crucial for understanding how systems will perform under different conditions and for identifying potential issues early in the design process.
- Optimization: By providing a quantitative framework, mathematical models enable the optimization of system performance. Engineers can adjust parameters and assess their impact on performance, leading to designs that are more efficient, cost-effective, and reliable.
- Understanding Physical Phenomena: Models help in understanding the underlying physical principles governing a system's behavior. This understanding is essential for diagnosing problems, improving designs, and advancing technological innovations.
- Risk Mitigation: By simulating different scenarios, models can identify potential failure modes and help engineers develop strategies to mitigate risks, enhancing the safety and reliability of engineering systems.
Steps in Developing Mathematical Models
Developing a mathematical model involves several critical steps, each contributing to the accuracy and usefulness of the model. These steps include:
- Problem Definition: Clearly define the engineering problem, including the objectives, constraints, and the physical phenomena involved. This step sets the scope and direction for model development.
- Formulation of the Model: Based on the problem definition, develop mathematical equations that describe the system's behavior. These equations are typically derived from fundamental physical laws such as conservation of mass, momentum, and energy. For example, Newton's laws of motion, the Navier-Stokes equations for fluid flow, and Fourier's law for heat conduction are commonly used in formulating models.
- Simplifications and Assumptions: To make the model tractable, simplifications and assumptions are often necessary. These might include assuming steady-state conditions, neglecting minor forces, or considering idealized material properties. It is crucial to justify and document these assumptions, as they impact the model's accuracy and applicability.
- Discretization: Convert the continuous mathematical equations into discrete forms that can be solved numerically. This process involves breaking the domain into smaller elements or intervals and approximating the equations using finite difference, finite element, or finite volume methods. Discretization transforms differential equations into algebraic equations suitable for numerical solution.
- Solution of Equations: Apply appropriate numerical methods to solve the discretized equations. This step often involves iterative techniques to find approximate solutions, ensuring convergence and stability of the numerical algorithm. Computational tools and software, such as MATLAB, ANSYS, and COMSOL, are commonly used for solving these equations.
- Validation and Calibration: Compare the model predictions with experimental data or known benchmarks to validate its accuracy. Calibration involves adjusting model parameters to better match observed data. Validation and calibration are crucial steps to ensure that the model reliably represents the real-world system.
- Analysis and Optimization: Use the validated model to analyze the system's behavior under different conditions. Perform sensitivity analysis to understand the impact of various parameters. Optimization techniques can then be applied to identify the best design or operating conditions, improving system performance and efficiency.
Applications in Mechanical Engineering
Mathematical models are extensively used in various domains of mechanical engineering. Some notable applications include:
- Structural Analysis: In structural engineering, models are used to predict how structures will respond to loads, vibrations, and other physical effects. Finite element models, for example, allow engineers to analyze stress, strain, and displacement in complex structures, ensuring their integrity and safety.
- Thermal Analysis: Thermal models predict temperature distribution and heat transfer in engineering components. These models are crucial for designing thermal management systems, such as heat exchangers, cooling systems, and thermal insulation, ensuring efficient thermal performance and preventing overheating.
- Fluid Dynamics: Computational fluid dynamics (CFD) models simulate the behavior of fluids in motion. These models are used in designing and optimizing systems involving fluid flow, such as pipelines, pumps, turbines, and aerodynamic components. CFD models help in understanding flow patterns, pressure distribution, and potential areas of turbulence or flow separation.
- Manufacturing Processes: Mathematical models are used to simulate and optimize manufacturing processes, such as casting, welding, and metal forming. These models help predict process outcomes, such as temperature profiles, residual stresses, and material deformations, leading to improved process control and product quality.
- Dynamic Systems: Models of dynamic systems describe how mechanical systems respond over time to external forces and control inputs. These models are essential for designing control systems, analyzing vibrations, and predicting the dynamic behavior of systems like automotive suspensions, robotic arms, and machinery.
Mathematical model development is a critical skill for mechanical engineers, enabling them to create accurate representations of complex systems. By following a systematic approach, engineers can develop models that predict system behavior, guide design decisions, and optimize performance. As computational tools and techniques continue to advance, the power and scope of mathematical modeling in engineering will expand, driving innovation and improving the efficiency and reliability of engineering solutions.
Modeling of Casting & Solidification Process
Casting is one of the oldest and most versatile manufacturing processes, involving the pouring of molten material into a mold where it solidifies into the desired shape. The process is widely used for making complex geometries in metals, plastics, and other materials. Solidification is a critical phase in the casting process, influencing the mechanical properties, dimensional accuracy, and overall quality of the final product. Proper control and understanding of casting and solidification are essential to minimize defects and enhance product performance.
Importance of Numerical Modeling in Casting and Solidification
Numerical modeling plays a crucial role in understanding and optimizing the casting and solidification process. It provides a powerful tool for predicting temperature distribution, solidification time, microstructure evolution, and potential defects such as porosity, shrinkage, and hot tearing. By simulating these aspects, engineers can improve mold design, optimize process parameters, and reduce the need for costly and time-consuming experimental trials.
Numerical Methods for Casting and Solidification
Several numerical methods are employed to model casting and solidification processes. These methods help solve the governing equations of heat transfer, fluid flow, and phase change, providing detailed insights into the process.
- Heat Transfer Analysis: Solidification involves the transfer of heat from the molten material to the mold. Numerical methods solve the heat conduction equation to predict temperature distribution and solidification time.
- Finite Difference Method (FDM): FDM approximates the heat conduction equation using finite difference equations. It is straightforward and easy to implement but may require fine grids for complex geometries.
- Finite Element Method (FEM): FEM divides the domain into smaller elements and solves the heat conduction equation over these elements. It is highly flexible and can handle complex geometries and boundary conditions effectively.
- Fluid Flow Simulation: During the casting process, the flow of molten material into the mold needs to be controlled to avoid defects. Numerical simulation of fluid flow helps in understanding the filling pattern and identifying potential issues such as turbulence and air entrapment.
- Finite Volume Method (FVM): FVM is commonly used to solve fluid flow equations. It conserves fluxes through a control volume, making it suitable for fluid dynamics problems in casting.
- Computational Fluid Dynamics (CFD): CFD techniques solve the Navier-Stokes equations governing fluid flow. CFD tools provide detailed insights into flow patterns, velocity fields, and pressure distribution during mold filling.
- Microstructural Evolution: Predicting the grain structure and phase transformations during solidification is essential for determining the mechanical properties of the cast product. Numerical methods model the evolution of microstructure to optimize process parameters and improve product quality.
- Phase Field Method: This method models the evolution of phase boundaries and grain structure during solidification. It provides a detailed understanding of microstructural changes over time.
- Cellular Automaton Method: This method simulates the growth of grains during solidification using a grid-based approach. It is computationally efficient and can handle complex solidification scenarios.
Advanced Modeling Techniques
In addition to basic finite element analysis, advanced modeling techniques can be applied to gain deeper insights into the casting and solidification process:
- Coupled Thermo-Mechanical Analysis: Integrate thermal and mechanical analysis to predict residual stresses and deformations resulting from non-uniform cooling and solidification shrinkage. This approach helps in understanding the formation of defects such as hot tears and cracks.
- Multiphysics Modeling: Combine heat transfer, fluid flow, and solidification models to capture the complete physics of the casting process. Multiphysics simulations provide a comprehensive view of the interactions between different physical phenomena.
- Inverse Modeling: Use inverse modeling techniques to identify optimal process parameters by comparing simulation results with experimental data. This approach helps in fine-tuning the model and achieving desired casting quality.
- Artificial Intelligence and Machine Learning: Incorporate AI and machine learning algorithms to predict casting outcomes based on historical data and simulation results. These techniques can enhance the accuracy of predictions and optimize process parameters more efficiently.
Numerical modeling of casting and solidification is an indispensable tool for mechanical engineers, enabling them to predict and control the outcome of the casting process. By applying methods such as finite element analysis, fluid flow simulation, and microstructural modeling, engineers can optimize mold design, improve process parameters, and reduce defects in cast products. As computational power and modeling techniques continue to advance, the capability to simulate and control casting processes will further enhance, leading to higher quality and more efficient manufacturing solutions.
Modeling of Metal Forming Processes
Metal forming is a crucial manufacturing process in which metals are plastically deformed to create desired shapes and geometries. This process is widely used in industries such as automotive, aerospace, and construction to produce components with specific mechanical properties and geometrical dimensions. Metal forming includes various techniques like forging, rolling, extrusion, and stamping, each with its unique characteristics and applications.
Numerical modeling of metal forming processes allows engineers to simulate and analyze these complex processes, predict outcomes, optimize parameters, and reduce the need for extensive experimental trials. By leveraging advanced computational methods, engineers can enhance the efficiency, accuracy, and quality of metal forming operations.
Importance of Numerical Modeling in Metal Forming
Numerical modeling provides several key benefits in the context of metal forming:
- Predicting Material Behavior: It helps predict the material flow, deformation, and stress distribution during forming processes, allowing for better control and optimization.
- Reducing Experimental Costs: Simulations reduce the need for costly and time-consuming experimental setups and trials by providing virtual testing environments.
- Optimizing Process Parameters: Engineers can optimize parameters such as force, temperature, and speed to achieve desired material properties and geometrical accuracy.
- Improving Product Quality: By predicting potential defects like wrinkling, tearing, and residual stresses, numerical models help improve the quality and performance of the final product.
Numerical Methods for Modeling Metal Forming
Several numerical methods are used to model metal forming processes. These methods solve the governing equations of continuum mechanics, considering material properties, boundary conditions, and process parameters.
- Finite Element Method (FEM): FEM is the most widely used numerical method in metal forming simulations. It divides the metal workpiece into smaller finite elements and solves the governing equations of elasticity and plasticity over these elements. FEM can handle complex geometries, non-linear material behavior, and large deformations, making it ideal for metal forming analysis.
- Finite Volume Method (FVM): FVM is another numerical technique used for modeling fluid flow and heat transfer in metal forming processes. It is particularly useful in processes involving significant temperature gradients and phase changes, such as hot forming and welding.
- Finite Difference Method (FDM): FDM approximates the governing equations using finite difference equations. While it is less flexible than FEM for complex geometries, it is simpler to implement and can be effective for certain metal forming problems.
- Mesh-Free Methods: These methods, such as the Smoothed Particle Hydrodynamics (SPH) and Element-Free Galerkin (EFG) methods, do not require a predefined mesh. They are useful for problems involving large deformations, fragmentation, and complex material behavior.
Key Aspects of Metal Forming Modeling
When modeling metal forming processes, several key aspects need to be considered:
- Material Properties: Accurate representation of material behavior, including elastic, plastic, and viscoelastic properties, is essential. Material models such as the Johnson-Cook model and the Gurson-Tvergaard-Needleman (GTN) model are commonly used to describe metal deformation and failure.
- Boundary Conditions: Defining appropriate boundary conditions, such as friction between the workpiece and the tools, heat transfer coefficients, and applied forces, is critical for accurate simulations.
- Process Parameters: Parameters such as temperature, strain rate, and forming speed significantly impact the outcome of the metal forming process. Numerical models must account for these parameters to provide realistic predictions.
- Contact Mechanics: Metal forming involves significant interaction between the workpiece and the forming tools. Accurate modeling of contact mechanics, including friction and wear, is essential for predicting material flow and surface finish.
Numerical modeling of metal forming processes is a powerful tool for mechanical engineers, enabling them to predict and optimize the outcomes of complex forming operations. By applying advanced numerical methods, engineers can simulate material behavior, optimize process parameters, and reduce defects in metal formed products. As computational tools and techniques continue to evolve, the capabilities of numerical modeling in metal forming will expand, leading to more efficient, accurate, and high-quality manufacturing solutions.
Modeling of Welding Processes
Metal forming is a crucial manufacturing process in which metals are plastically deformed to create desired shapes and geometries. This process is widely used in industries such as automotive, aerospace, and construction to produce components with specific mechanical properties and geometrical dimensions. Metal forming includes various techniques like forging, rolling, extrusion, and stamping, each with its unique characteristics and applications.
Numerical modeling of metal forming processes allows engineers to simulate and analyze these complex processes, predict outcomes, optimize parameters, and reduce the need for extensive experimental trials. By leveraging advanced computational methods, engineers can enhance the efficiency, accuracy, and quality of metal forming operations.
Importance of Numerical Modeling in Metal Forming
Numerical modeling provides several key benefits in the context of metal forming:
- Predicting Material Behavior: It helps predict the material flow, deformation, and stress distribution during forming processes, allowing for better control and optimization.
- Reducing Experimental Costs: Simulations reduce the need for costly and time-consuming experimental setups and trials by providing virtual testing environments.
- Optimizing Process Parameters: Engineers can optimize parameters such as force, temperature, and speed to achieve desired material properties and geometrical accuracy.
- Improving Product Quality: By predicting potential defects like wrinkling, tearing, and residual stresses, numerical models help improve the quality and performance of the final product.
Numerical Methods for Modeling Metal Forming
Several numerical methods are used to model metal forming processes. These methods solve the governing equations of continuum mechanics, considering material properties, boundary conditions, and process parameters.
- Finite Element Method (FEM): FEM is the most widely used numerical method in metal forming simulations. It divides the metal workpiece into smaller finite elements and solves the governing equations of elasticity and plasticity over these elements. FEM can handle complex geometries, non-linear material behavior, and large deformations, making it ideal for metal forming analysis.
- Finite Volume Method (FVM): FVM is another numerical technique used for modeling fluid flow and heat transfer in metal forming processes. It is particularly useful in processes involving significant temperature gradients and phase changes, such as hot forming and welding.
- Finite Difference Method (FDM): FDM approximates the governing equations using finite difference equations. While it is less flexible than FEM for complex geometries, it is simpler to implement and can be effective for certain metal forming problems.
- Mesh-Free Methods: These methods, such as the Smoothed Particle Hydrodynamics (SPH) and Element-Free Galerkin (EFG) methods, do not require a predefined mesh. They are useful for problems involving large deformations, fragmentation, and complex material behavior.
Numerical modeling of metal forming processes is a powerful tool for mechanical engineers, enabling them to predict and optimize the outcomes of complex forming operations. By applying advanced numerical methods, engineers can simulate material behavior, optimize process parameters, and reduce defects in metal formed products. As computational tools and techniques continue to evolve, the capabilities of numerical modeling in metal forming will expand, leading to more efficient, accurate, and high-quality manufacturing solutions.
Conclusion
Numerical methods are a cornerstone of modern mechanical engineering, transforming how engineers design, analyze, and optimize manufacturing processes. By harnessing the power of these methods, engineers can predict outcomes, optimize processes, reduce costs, and enhance product quality. As technology continues to advance, the capabilities of numerical methods will only grow, offering even more sophisticated tools for tackling complex engineering challenges.
For students and professionals alike, mastering numerical methods opens up a world of possibilities in mechanical engineering. It equips them with the skills and knowledge to innovate, solve problems, and contribute to the advancement of the field. Whether you are developing new materials, designing advanced manufacturing processes, or optimizing existing systems, numerical methods will play a crucial role in your success. Embrace these powerful tools and leverage their potential to drive engineering excellence and innovation.