Fatigue Analysis in ANSYS: Understanding and Predicting Material Failure!
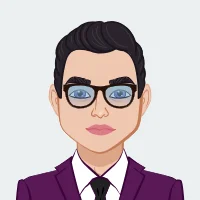
Fatigue analysis stands as a cornerstone in the realm of mechanical engineering, playing a pivotal role in ensuring the durability and reliability of structures and components. As materials and structures endure cyclic loading, whether from mechanical forces or environmental factors, they face the potential threat of fatigue failure. This type of failure is insidious, often occurring gradually over time through the accumulation of microscopic cracks, and can lead to catastrophic consequences if left unaddressed. Hence, the significance of fatigue analysis lies in its capacity to predict and prevent material failure, enabling engineers to design robust structures that can withstand the rigors of real-world applications, including assistance with your Ansys assignment.
In the dynamic field of mechanical engineering, where components experience a myriad of forces and environmental conditions, understanding the intricacies of fatigue is imperative. Fatigue analysis involves the assessment of how materials respond to repeated loading, identifying potential weak points and susceptibility to failure. This preemptive approach is crucial for designing structures with extended operational lifespans and minimizing the risk of unexpected breakdowns. By scrutinizing the effects of cyclic loading on materials, engineers gain insights into the potential initiation and propagation of cracks, allowing them to implement preventive measures before catastrophic failure occurs.
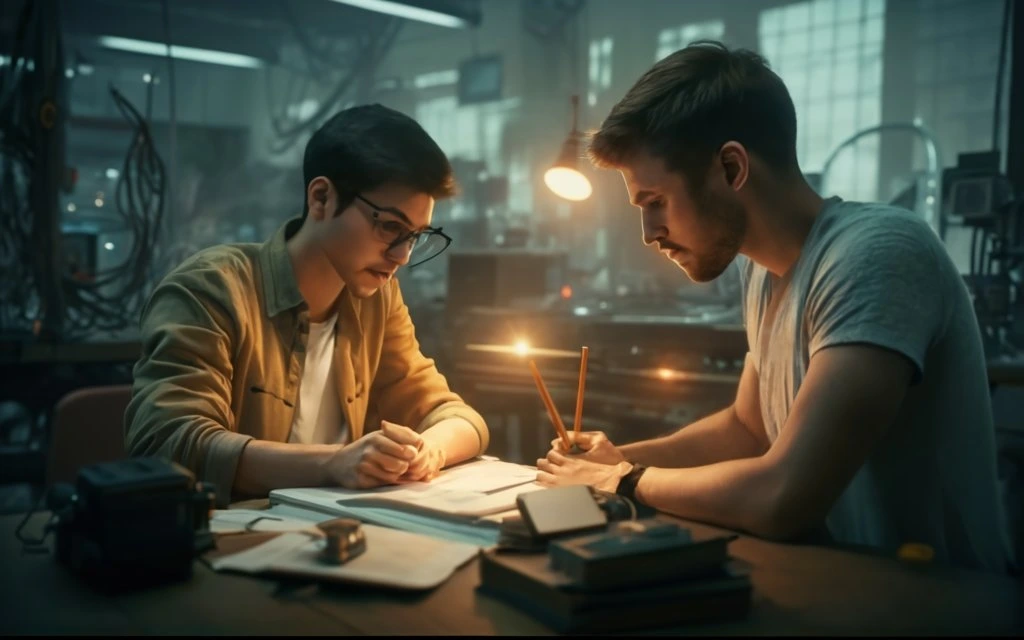
The ability to predict and prevent material failure through fatigue analysis is particularly vital in industries where safety and reliability are paramount. Aerospace, automotive, and civil engineering, among others, heavily rely on components that must endure a multitude of loading cycles without compromising structural integrity. Fatigue analysis acts as a proactive tool, empowering engineers to identify critical areas prone to fatigue-induced failure and make informed design decisions. This not only enhances the longevity of components but also reduces maintenance costs and, most importantly, safeguards against the potentially disastrous consequences of structural failures.
One of the primary advantages of fatigue analysis lies in its role as a predictive tool. By understanding how materials respond to repeated loading, engineers can extrapolate the expected lifespan of a structure and plan maintenance schedules accordingly. This predictive capability is instrumental in industries where downtime and unexpected failures can have severe financial and safety implications. Moreover, it facilitates the development of materials with enhanced fatigue resistance, pushing the boundaries of engineering innovation.
In conclusion, the importance of fatigue analysis in mechanical engineering cannot be overstated. It serves as a proactive mechanism for predicting and preventing material failure, ensuring that structures are not just strong but durable over their intended lifespan. By integrating fatigue analysis, engineers contribute to the creation of reliable, long-lasting components that meet the stringent demands of modern applications. In the intricate dance between materials and forces, fatigue analysis emerges as the guiding light, illuminating the path to designing structures that stand the test of time.
What is Fatigue Analysis?
Fatigue analysis is a critical aspect of structural engineering that focuses on understanding and predicting the behavior of materials subjected to repeated loading conditions. In engineering, materials are often exposed to cyclic or fluctuating loads, which can lead to the gradual development of cracks and fractures over time. This phenomenon is known as fatigue, and it poses a significant threat to the structural integrity of various components in mechanical systems. Unlike a one-time load that may cause immediate failure, fatigue failure occurs due to the accumulation of damage caused by repeated loading and unloading cycles.
The role of fatigue analysis is paramount in assessing and mitigating the risks associated with material fatigue. Engineers must consider fatigue because many structures and components in industries such as aerospace, automotive, and civil engineering experience cyclic loading during their operational life. Ignoring fatigue considerations can result in unexpected and catastrophic failures, even in structures that seem to meet static strength requirements. Fatigue failures often occur at stress levels significantly lower than the material's ultimate strength, making them particularly challenging to predict without a thorough analysis.
Fatigue analysis involves studying the response of materials to cyclic loading, considering factors such as stress amplitude, mean stress, and the number of loading cycles. The goal is to estimate the number of cycles a material can endure before failure occurs. This is typically represented by an S-N curve, which illustrates the relationship between stress levels and the corresponding number of cycles to failure. Understanding this relationship is crucial for engineers to design structures with adequate fatigue resistance.
Considering fatigue in designs is essential for several reasons. Firstly, it helps engineers identify potential weak points in a structure that may not be evident through traditional static analysis. Secondly, it allows for the estimation of a structure's expected fatigue life, enabling the implementation of preventive measures or maintenance schedules. Thirdly, by incorporating fatigue analysis, engineers can optimize designs to enhance durability and reliability, reducing the likelihood of unexpected failures during the operational life of a product. Ultimately, accounting for fatigue ensures that structures and components can withstand the rigors of real-world, cyclic loading conditions, contributing to the overall safety and longevity of engineering systems. In summary, fatigue analysis is a fundamental tool that safeguards the structural integrity of materials, offering a proactive approach to engineering design that is indispensable in various industries.
Introduction to ANSYS:
ANSYS, a leading engineering simulation software, stands as a pinnacle in the realm of structural analysis, offering a comprehensive platform for engineers to simulate and evaluate the behavior of structures under various conditions. At its core, ANSYS employs the finite element method (FEM), breaking down complex structures into smaller, more manageable elements for analysis. This enables engineers to gain insights into the performance of components and systems, ensuring they meet design requirements and industry standards.
In the context of fatigue analysis, ANSYS plays a pivotal role by allowing engineers to predict and understand how materials respond to repeated loading over time, a critical consideration in designing durable and reliable structures. Fatigue analysis in ANSYS involves the simulation of cyclic loading conditions, which may include alternating stress, strain, or thermal cycles. The software provides a sophisticated set of tools and algorithms to model the intricate behavior of materials subjected to these cyclic loads, predicting potential points of failure and determining the lifespan of a structure.
One of ANSYS' strengths lies in its ability to handle a wide range of materials and loading scenarios. Engineers can input material properties, load magnitudes, and loading frequencies into the software, allowing for a detailed analysis of how fatigue accumulates over time. ANSYS utilizes advanced fatigue models, such as the fatigue life prediction based on stress-life (S-N) curves, to estimate the number of cycles a material can endure before failure. This level of precision is vital in industries where safety and reliability are paramount, such as aerospace, automotive, and heavy machinery.
Furthermore, ANSYS provides a user-friendly interface that enables engineers to set up and execute fatigue analyses with relative ease. The software allows for the customization of simulation parameters, ensuring that the analysis aligns with the specific requirements of a given project. Engineers can visualize and interpret results through intuitive graphical representations, aiding in the identification of potential fatigue-prone areas within a structure.
In essence, ANSYS serves as a virtual testing ground, empowering engineers to explore the effects of cyclic loading on materials and structures without the need for physical prototypes. This not only accelerates the design and development process but also minimizes the risk of unexpected failures in real-world applications. By offering a robust and versatile platform for fatigue analysis, ANSYS stands as an indispensable tool for engineers seeking to enhance the reliability and longevity of mechanical components and systems.
Basics of Material Failure:
Material failure is a critical consideration in mechanical engineering, and understanding the fundamental concepts of stress, strain, and the S-N curve is essential for predicting and preventing fatigue failure. Stress, defined as the force applied per unit area, is a primary factor influencing material behavior. When subjected to repeated loading, materials experience cyclic stresses, leading to the phenomenon of fatigue failure. Strain, the deformation caused by stress, plays a crucial role in assessing a material's ability to withstand repeated loading cycles.
The S-N curve, also known as the fatigue or endurance limit curve, is a graphical representation that illustrates the relationship between the number of loading cycles (N) and the stress level (S) at which fatigue failure occurs. This curve helps engineers predict the material's fatigue life under different stress conditions. Understanding the S-N curve aids in designing structures that can endure cyclic loading without experiencing premature failure.
Several factors contribute to fatigue failure, and comprehending these elements is paramount in preventing catastrophic consequences. Firstly, cyclic loading induces microstructural changes within the material, leading to the initiation and propagation of cracks. These cracks, if not detected and addressed, can grow over time, compromising the structural integrity. Secondly, material defects and imperfections, even at a microscopic level, can act as stress concentration points, accelerating the onset of fatigue failure.
Environmental factors also play a role; exposure to corrosive environments can significantly reduce a material's fatigue life. Additionally, temperature fluctuations can affect material properties, influencing its response to cyclic loading. Lubrication and surface finish are critical considerations, as inadequate lubrication or rough surfaces can exacerbate fatigue.
In conclusion, a comprehensive understanding of stress, strain, and the S-N curve is crucial for grasping the intricacies of material failure and fatigue analysis in mechanical engineering. Engineers must consider these fundamental concepts to design structures that withstand repeated loading cycles and ensure long-term durability. By acknowledging the factors contributing to fatigue failure, engineers can implement preventive measures, employ effective materials, and utilize advanced tools like ANSYS for accurate fatigue analysis, ultimately enhancing the reliability and safety of mechanical components.
The Importance of Fatigue Analysis in Mechanical Engineering:
Fatigue analysis plays a pivotal role in averting catastrophic failures across various industries, safeguarding product safety, and enhancing longevity. One poignant example of the consequences of neglecting fatigue analysis can be found in the aerospace industry. The infamous incident of the De Havilland Comet in the 1950s serves as a stark reminder. The aircraft, considered revolutionary in its design, experienced catastrophic failures due to metal fatigue, leading to multiple crashes. Had fatigue analysis been applied diligently, identifying stress concentrations and potential failure points, the tragedies could have been averted, underscoring the critical need for meticulous assessment.
In the realm of automotive engineering, fatigue analysis has proven instrumental in enhancing the durability of vehicle components. Consider the suspension systems subjected to incessant road vibrations and dynamic loads. Without a thorough understanding of material fatigue, suspension components may succumb to repeated stress cycles, compromising safety and performance. Fatigue analysis in this context ensures the longevity of critical components, preventing unexpected failures that could have dire consequences for drivers and passengers alike.
Moreover, in the field of civil engineering, fatigue analysis is indispensable for infrastructure projects. Take, for instance, the collapse of the Tacoma Narrows Bridge in 1940, attributed to aeroelastic flutter induced by wind. A modern-day parallel can be drawn to the importance of fatigue analysis in designing and maintaining wind turbines. The constant exposure to cyclic loading from wind forces necessitates a meticulous fatigue assessment to guarantee the structural integrity of turbine components over their operational lifespan. Implementing such analyses avoids catastrophic failures, ensuring the sustainability of renewable energy infrastructure.
In the manufacturing sector, particularly in heavy machinery production, fatigue analysis is a linchpin for preventing equipment breakdowns. A case in point is the failure of crane components due to fatigue-induced cracks. By employing advanced simulation tools like ANSYS for fatigue analysis, manufacturers can identify potential weak points, optimize designs, and select materials resilient to cyclic loading. This proactive approach not only averts costly downtimes but also enhances the overall safety and reliability of industrial machinery.
In conclusion, fatigue analysis stands as an indispensable tool across diverse industries, with real-world examples showcasing its potential to prevent catastrophic failures. From aviation and automotive engineering to civil infrastructure and manufacturing, the meticulous assessment of material fatigue is paramount for ensuring product safety, longevity, and the overall reliability of critical components. As technology advances, incorporating fatigue analysis methodologies becomes not only a best practice but a moral imperative in the pursuit of engineering excellence and public safety.
Conducting Fatigue Analysis in ANSYS:
Performing fatigue analysis using ANSYS involves several key steps, ensuring accurate predictions of material failure and enhancing structural reliability. Here is a step-by-step guide, accompanied by explanations, screenshots, and tips to assist students in their mechanical engineering assignments.
- Step 1: Model Geometry in ANSYS Workbench Begin by importing or creating your model geometry in ANSYS Workbench. Use the Geometry module to define your structure, ensuring accurate representation. For simplicity, let's consider a basic example—a cantilever beam subjected to cyclic loading.
- Step 2: Apply Boundary Conditions and Loads Define the boundary conditions and loads on your model. In fatigue analysis, cyclic loading is particularly important. Apply dynamic or static loads based on your specific case. Ensure proper constraints are in place to represent real-world scenarios accurately.
- Step 3: Material Properties and Fatigue Data Specify the material properties of your structure within ANSYS. Input relevant information such as Young's Modulus, Poisson's Ratio, and, most importantly, fatigue data. Provide the S-N curve, representing the material's response to cyclic loading, a crucial factor in fatigue analysis.
- Step 4: Set Up Fatigue Analysis in ANSYS Access the ANSYS Mechanical module from the Workbench. Create a new analysis system and select "Fatigue" as the analysis type. Define the fatigue settings, including the number of cycles, loading conditions, and relevant criteria for failure. This step configures ANSYS for fatigue-specific simulations.
- Step 5: Mesh Generation Generate a suitable mesh for your model. Use the Meshing module in ANSYS Workbench to divide your structure into elements. A finer mesh captures detailed stress variations, providing more accurate fatigue predictions. Balance mesh density to ensure efficient computation.
- Step 6: Apply Fatigue Loading Define the loading history for fatigue analysis. Utilize ANSYS tools to specify loading conditions over time, mimicking cyclic loading patterns. This step is crucial for predicting material behavior under repeated stress cycles.
- Step 7: Solve and Evaluate Results Run the fatigue analysis by solving the system. ANSYS will provide results in terms of stress, strain, and fatigue life predictions. Evaluate the results to identify potential fatigue failure locations and understand the overall structural response.
Tips:
- Regularly save your work to prevent data loss during the analysis process.
- Perform a convergence study to ensure mesh independence and solution reliability.
- Understand the significance of the S-N curve and how variations impact fatigue life predictions.
- Experiment with different loading scenarios and boundary conditions to assess their impact on fatigue behavior.
By following these steps and tips, students can gain a comprehensive understanding of fatigue analysis using ANSYS, enabling them to apply this knowledge to real-world engineering challenges. The accompanying screenshots and detailed explanations aim to make the process accessible and applicable in the context of mechanical engineering assignments.
Conclusion:
In this blog post titled "Fatigue Analysis in ANSYS: Understanding and Predicting Material Failure," we explored the critical role of fatigue analysis in ensuring the structural integrity of mechanical components. The blog began by introducing the concept of fatigue analysis and its significance in the field of mechanical engineering, emphasizing the need to predict and prevent material failure under repeated loading conditions. ANSYS, a powerful engineering simulation software, was introduced as a key tool for conducting detailed fatigue analysis.
The importance of fatigue analysis in mechanical engineering was underscored in the subsequent sections. The post delved into the basics of material failure, explaining concepts such as stress, strain, and the S-N curve. These foundational aspects were crucial for readers to understand the factors contributing to fatigue failure, making it clear why engineers must consider fatigue in their designs. Real-world examples were cited to illustrate the devastating consequences of neglecting fatigue analysis, highlighting its relevance across various industries and emphasizing its impact on product safety and longevity.
The heart of the blog focused on the practical application of ANSYS for fatigue analysis. A detailed guide was provided, offering step-by-step instructions accompanied by screenshots and explanations to help readers navigate the process. Case studies were presented to showcase successful applications of fatigue analysis in ANSYS, demonstrating how the software influenced design decisions and contributed to the prevention of catastrophic failures.
Acknowledging the challenges and limitations of fatigue analysis in ANSYS added a realistic dimension to the discussion. Common issues that engineers might face were addressed, and recommendations or alternative approaches were provided to enhance the effectiveness of the analysis. The blog aimed to equip readers with a comprehensive understanding of both the capabilities and constraints of fatigue analysis in ANSYS.
In conclusion, the blog reiterated the overarching importance of fatigue analysis in ensuring the structural integrity of mechanical components. By leveraging the capabilities of ANSYS, engineers can predict and prevent material failure, ultimately contributing to the creation of robust and reliable structures. The call-to-action encouraged readers to explore additional resources on the website, positioning it as a valuable destination for those seeking assistance with their mechanical engineering assignments. Through this blog post, the website not only educated its audience but also established itself as a go-to platform for insights and support in the field of mechanical engineering.