Mastering 2-Stroke Engine Linkages: A Student's Guide
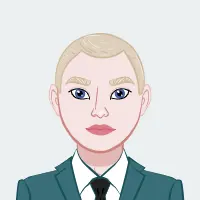
Internal combustion engines are marvels of engineering that power a wide range of vehicles and equipment, from motorcycles and chainsaws to lawnmowers and outboard motors. Among the various types of internal combustion engines, the two-stroke engine stands out for its simplicity, lightweight design, and efficient power delivery. Understanding the intricate mechanical linkages within a two-stroke engine is essential for engineering students and enthusiasts alike, as it unveils the secrets behind these remarkable machines. In this comprehensive guide, we will delve into the world of two-stroke engine linkages, providing students with valuable insights to aid them in solving Theory of Mechanics Assignments, gaining a deeper understanding of these engines, and even igniting their passion for automotive engineering.
Two-stroke engines have been a staple of small, lightweight engines for decades. They are commonly used in applications such as motorcycles, chainsaws, and outboard motors. Understanding the mechanical linkages within a two-stroke engine is crucial for engineering students and enthusiasts interested in the field of internal combustion engines. In this comprehensive guide, we will delve into the mechanical analysis of linkages in 2-stroke engines, providing students with valuable insights to aid them in solving assignments and gaining a deeper understanding of these fascinating machines.
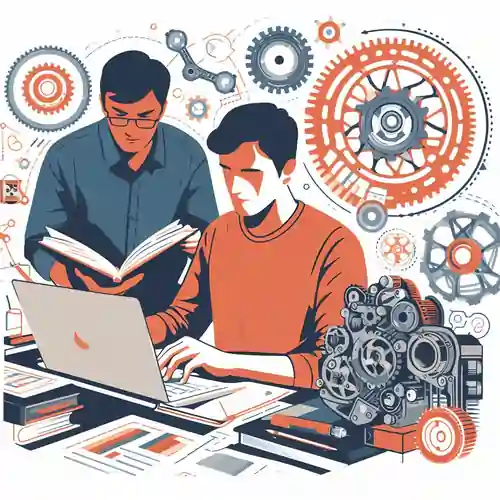
Two-Stroke Engine Basics
Before diving into the mechanical analysis of linkages, let's briefly review the fundamental principles of a two-stroke engine. These engines operate on a simple yet efficient cycle, consisting of two primary strokes: the intake-compression-exhaust stroke and the power stroke. Here's a simplified overview:
- Intake-Compression-Exhaust Stroke:
- The piston moves down, creating a vacuum in the crankcase.
- This vacuum draws in a fuel-air mixture through the intake port.
- The piston then begins to move upward, compressing the mixture in the crankcase.
- Power Stroke:
- As the piston approaches the top of the cylinder, a spark plug ignites the compressed mixture.
- This ignition forces the piston back down the cylinder, generating power.
- It's important to note that two-stroke engines require a specific mechanism to control the opening and closing of intake and exhaust ports. This is where linkages play a vital role.
- Crankshaft and Connecting Rod
- Piston and Cylinder
- Ports and Timing
- Crankcase Scavenging
- Transfer and Exhaust Port Linkages
- Crankshaft and Connecting Rod
- Piston and Cylinder
- Ports and Timing
- Crankcase Scavenging
- Transfer and Exhaust Port Linkages
- Geometry Modeling
- Kinematic Analysis
- Dynamic Analysis
- Simulation
The Role of Linkages in a 2-Stroke Engine
Linkages in a 2-stroke engine serve various functions, including valve timing, port opening and closing, and the coordination of various components. Let's explore the key linkages and their mechanical analysis:
The crankshaft and connecting rod are integral components of the engine's linkage system. The crankshaft converts the reciprocating motion of the piston into rotary motion, while the connecting rod connects the piston to the crankshaft. This linkage is vital for translating the piston's linear motion into the rotational motion required to drive the engine.
Mechanical analysis of the crankshaft and connecting rod involves understanding their lengths, angles, and the effects of these parameters on the engine's performance, such as the stroke length, piston speed, and torque characteristics.
The piston and cylinder form another critical linkage within the engine. The piston's movement inside the cylinder directly affects compression and power generation. The analysis here includes calculating parameters like piston displacement, compression ratio, and clearance volume. Students may need to solve assignments related to these calculations to understand the engine's behavior.
Two-stroke engines rely on ports in the cylinder walls for the intake and exhaust processes. These ports must be opened and closed at precise times to ensure efficient engine operation. The mechanical analysis of port timing includes studying the geometry of the ports, their positions, and their relation to the piston's position in the cylinder.
Assignments may require students to calculate port timing angles, considering factors such as engine speed and performance requirements.
Crankcase scavenging is a crucial process in two-stroke engines. It involves using the motion of the piston to create pressure differences that facilitate the intake and exhaust processes. Students may need to analyze the design of the crankcase and the piston's movement to ensure effective scavenging.
The opening and closing of transfer and exhaust ports are controlled by linkages like the piston, rotary valves, or reed valves. Assignments related to these components may involve calculating the timing of port events and optimizing them for better engine performance.
Mathematical Modeling and Simulation
To solve assignments related to the mechanical analysis of linkages in 2-stroke engines, students often employ mathematical modeling and simulation techniques. Here's an overview of the steps involved:
Geometry Modeling:
Students create a geometric representation of the engine components and their linkages, including the crankshaft, piston, connecting rod, and ports.
Kinematic Analysis:
Kinematic analysis involves studying the motion of these components in relation to each other. This analysis helps determine key parameters like piston speed, crankshaft angular velocity, and valve timing.
Dynamic Analysis:
Dynamic analysis considers forces, torques, and inertial effects during engine operation. Students may need to solve equations of motion to understand how these factors impact engine behavior.
Simulation:
Using specialized software or tools, students can simulate engine operation based on their mathematical models. Simulations allow for the testing of different configurations and design changes to optimize engine performance.
Linkages in Detail
Let's explore each linkage component in greater detail to provide students with a more comprehensive understanding of their mechanical analysis:
Crankshaft:
The crankshaft is the heart of the engine's mechanical system. It converts the reciprocating motion of the piston into rotary motion, which ultimately drives the vehicle or equipment. Analyzing the crankshaft involves several key aspects:
Stroke Length: The stroke length is the distance the piston travels between the top dead center (TDC) and the bottom dead center (BDC) positions. This parameter directly affects an engine's displacement and performance. It can be calculated using the following formula:
Stroke Length = BDC - TDC
Crankshaft Angular Velocity: The angular velocity of the crankshaft determines the engine's speed. It's crucial to understand how this velocity changes throughout the engine cycle and how it relates to the piston's movement.
Torque Generation: The crankshaft generates torque that powers the vehicle or equipment. Analyzing torque characteristics is essential for optimizing engine performance.
Connecting Rod:
The connecting rod links the piston to the crankshaft and plays a critical role in converting linear motion to rotary motion. Its mechanical analysis includes:
Length and Geometry: The length and geometry of the connecting rod affect the engine's stroke, piston motion, and compression ratio. Students may need to calculate these parameters and their impact on engine performance.
Stress Analysis: Connecting rods are subjected to significant mechanical stresses during engine operation. Analyzing stress distribution and ensuring the rod's structural integrity is essential.
The piston-cylinder linkage is central to the engine's operation, as it controls compression, power generation, and exhaust. Detailed mechanical analysis includes:
Piston:
Displacement: The piston displacement is the volume swept by the piston as it moves within the cylinder. It's a fundamental parameter for calculating engine displacement and efficiency.
Compression Ratio: The compression ratio is the ratio of the cylinder's volume when the piston is at BDC to its volume when the piston is at TDC. It impacts engine efficiency, power output, and thermal efficiency.
Clearance Volume: Clearance volume is the space remaining in the cylinder when the piston is at TDC. It influences compression and combustion dynamics.
Cylinder:
Cylinder Diameter and Stroke: These parameters, in combination with piston characteristics, determine the engine's displacement and overall design.
Heat Transfer Analysis: Analyzing heat transfer within the cylinder helps optimize cooling and thermal efficiency.
Two-stroke engines rely on ports in the cylinder wall to control the flow of air and exhaust gases. Mechanical analysis of ports and timing involves:
Port Geometry: Students need to understand the geometry and dimensions of intake, transfer, and exhaust ports. This includes port areas, widths, and shapes.
Port Timing: Port timing determines when these ports open and close relative to the piston's position. Calculations and analysis are essential to optimize engine performance.
Reed Valve or Rotary Valve Analysis: In some two-stroke engines, reed valves or rotary valves control port openings. Understanding their operation and optimizing their design can be part of assignments.
Crankcase scavenging is the process by which the movement of the piston creates pressure differences in the crankcase, facilitating the intake and exhaust processes. Students may analyze:
Scavenging Efficiency: Calculations and simulations can determine how effectively the scavenging process occurs and how it impacts engine performance.
Crankcase Design: The design of the crankcase and its ability to maintain proper pressure differentials are crucial for efficient scavenging.
The opening and closing of transfer and exhaust ports are often controlled by specific linkages. Here's a closer look at these components:
Transfer Ports: These ports allow the fresh fuel-air mixture to enter the combustion chamber. Mechanical analysis involves determining the timing of transfer port openings and optimizing their design.
Exhaust Ports: Proper exhaust port design and timing are essential for the efficient evacuation of exhaust gases. The analysis includes calculating when exhaust ports should open and close to maximize engine performance.
Valve Systems: Some engines use rotary valves or reed valves to control port openings. Assignments may require students to analyze the operation and timing of these valve systems.
Mathematical Modeling and Simulation
As students delve into the mechanical analysis of linkages in 2-stroke engines, mathematical modeling, and simulation play a pivotal role in gaining insights and solving assignments. Here's a deeper dive into these crucial aspects:
Geometry modeling involves creating accurate representations of the engine components and their linkages. This includes using CAD (Computer-Aided Design) software to generate 3D models or simpler 2D sketches to visualize the engine's components and their interactions. Geometry modeling helps students establish a baseline for their analysis and simulation work.
Kinematic analysis focuses on understanding the motion of various engine components in relation to each other. Key aspects of kinematic analysis include:
Piston Motion: Calculating and visualizing the piston's motion within the cylinder, including its velocity and acceleration profiles.
Crankshaft Rotation: Determining the angular displacement, velocity, and acceleration of the crankshaft throughout the engine's cycle.
Valve and Port Timing: Analyzing when intake and exhaust ports open and close and how this timing relates to piston position.
Kinematic analysis provides critical insights into engine behavior and allows students to optimize parameters like valve timing and piston speed.
The dynamic analysis delves deeper into the forces, torques, and inertial effects that occur during engine operation. Here's what students might explore:
Force on the Piston: Calculating the forces acting on the piston due to combustion pressure and friction.
Torque on the Crankshaft: Determining the torque generated by the engine and how it varies throughout the cycle.
Inertial Effects: Understanding how the mass and motion of engine components affect dynamic behavior.
Dynamic analysis is vital for evaluating engine performance, reliability, and structural integrity.
Simulation is a powerful tool that allows students to test and refine their mathematical models in a virtual environment. Here are some simulation-related considerations:
Software Tools: There are specialized simulation software packages available for internal combustion engine analysis. Examples include GT-Power, AVL Fire, and Ricardo Wave.
Parameter Variation: Students can use simulations to explore the effects of changing parameters like piston geometry, valve timing, and compression ratio on engine performance.
Optimization: Simulations enable students to optimize engine configurations for specific goals, such as maximizing power output or improving fuel efficiency.
Simulation is a valuable step in the learning process, as it provides practical insights into the theoretical concepts covered in assignments.
Conclusion
In the world of internal combustion engines, the mechanical analysis of linkages in 2-stroke engines is a complex and fascinating field. By understanding the role of linkages, such as the crankshaft, piston, ports, and timing mechanisms, students can gain valuable insights into how these engines operate and how to optimize their performance.
Assignments in this area often involve mathematical modeling and simulation, which provide hands-on experience and reinforce theoretical knowledge. As students dive into the mechanical intricacies of 2-stroke engines, they not only enhance their problem-solving skills but also contribute to the ongoing development of efficient and environmentally friendly engine designs.
Mastering the mechanical analysis of linkages in 2-stroke engines is not only valuable academically but also opens doors to careers in engine design, automotive engineering, and other related fields. As technology continues to advance, the knowledge gained in this area will remain highly relevant, making it an exciting and rewarding field of study for engineering students.
With this comprehensive guide, students are well-equipped to tackle assignments related to the mechanical analysis of linkages in 2-stroke engines and embark on a journey of exploration and innovation in the field of internal combustion engines. As they delve deeper into the intricacies of engine design and analysis, they contribute to the ever-evolving landscape of engine technology.