Navigating Structural Mechanics Challenges in Solid Mechanics Assignments
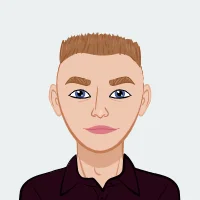
When approaching structural mechanics problems, especially those involving beam deflection and stress analysis, it’s crucial to follow a structured and systematic methodology to ensure accuracy, reliability, and comprehensiveness in your solutions. These types of mechanical engineering assignments often require a deep understanding of underlying principles, the application of various theories, and the use of specific equations. By adhering to a well-organized approach, you can effectively navigate through complex calculations, derive meaningful results, and ensure that all critical factors are considered. This methodology not only helps in simplifying and solving intricate problems but also aids in identifying potential issues and devising robust solutions.
Starting with a clear understanding of the problem statement, you need to meticulously identify the given data and the required outcomes. Simplifying the problem through reasonable assumptions and creating a precise model of the structure are essential steps. Applying relevant theories, such as beam theory or load distribution concepts, allows you to derive the necessary equations for deflection and stress analysis. Calculating maximum deflections and stresses involves using these equations accurately, ensuring the results are within acceptable safety margins.
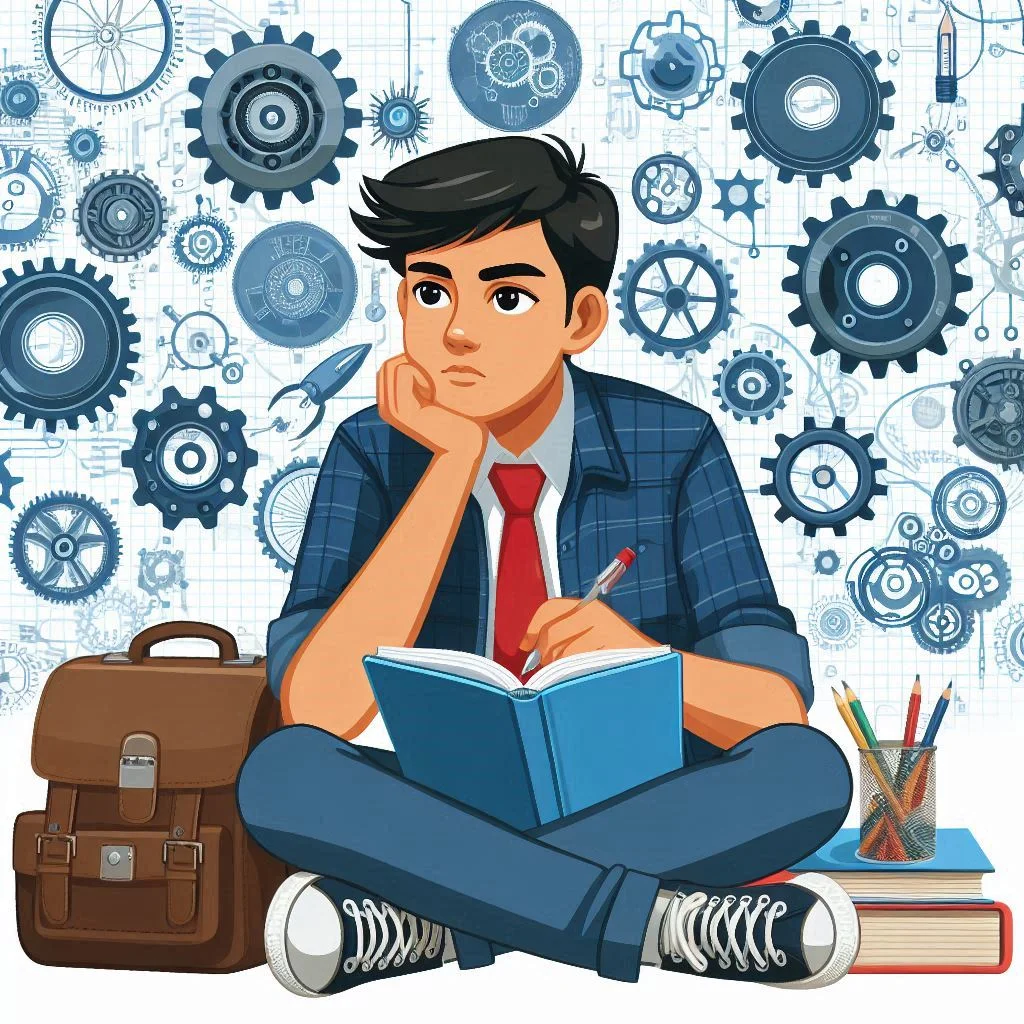
Evaluating the safety of your design is a critical step, often requiring the assessment of safety factors and proposing necessary modifications to meet stringent criteria. This might involve adjusting structural elements or applying additional forces to enhance stability. Comparing different design alternatives helps in selecting the most effective and feasible solution, considering factors like cost, performance, and practicality.
For scenarios involving complex load conditions, such as wind loads on cables, deriving load intensity and resultant forces is crucial. Visualizing results through graphical analysis aids in understanding structural behavior under various loads, enabling a comparative analysis of different solutions.
By following these detailed steps and utilizing tips such as organizing your work, leveraging software tools, and consulting reliable resources, you can systematically approach and get help with solid mechanics assignment. This structured methodology not only ensures accuracy and reliability in your current assignments but also equips you with the skills and confidence to handle similar challenges in future assignments, fostering a deeper grasp of structural mechanics and significantly enhancing your problem-solving abilities.
Understanding the Problem Statement
When faced with a structural mechanics assignment, the first and most critical step is to thoroughly understand the problem statement. This foundational step sets the stage for all subsequent analysis and calculations. A clear and accurate comprehension of the problem ensures that you address the correct issues and apply the appropriate theories and equations. Here's how to effectively understand the problem statement:
Read Carefully
Start by reading the problem statement multiple times to ensure you fully grasp its content. Pay close attention to every detail, as even small pieces of information can significantly impact your approach and solutions.
Identify Given Data
Highlight and list all the given data and parameters in the problem statement. These might include:
- Dimensions: Lengths, spans, thicknesses, and any other relevant measurements.
- Loads: Types and magnitudes of loads, such as distributed loads, point loads, or axial forces.
- Material Properties: Young’s modulus, yield strength, and other relevant material constants.
- Boundary Conditions: Types of supports and constraints, such as fixed, simply supported, or free ends.
Determine the Required Outcomes
Clearly identify what the problem is asking you to find or analyze. This could involve:
- Deflections: Maximum deflection points, critical deflection values, or deflection profiles.
- Stresses: Calculations of tensile, compressive, or shear stresses in the structure.
- Safety Factors: Evaluations of existing safety factors and required modifications to meet safety criteria.
- Comparisons and Alternatives: Analysis of different design proposals or solutions and recommendations for the best approach.
Visualize the Problem
Sketching a diagram of the problem can greatly enhance your understanding. This visual representation helps in identifying relationships between different elements of the structure and clarifying complex load applications and support conditions.
Clarify Assumptions and Constraints
Identify any implicit or explicit assumptions in the problem statement. Assumptions might include idealized load distributions, negligible deformations in certain directions, or specific material behavior models. Recognize any constraints that limit your solutions, such as maximum allowable deflections or stress limits.
Formulate a Plan
Based on your understanding of the problem statement, start formulating a plan for your analysis. Outline the steps you will take, the equations you will use, and any specific methods or tools that will aid your calculations.
By investing time and effort in thoroughly understanding the problem statement, you lay a solid foundation for your analysis and solutions. This careful and methodical approach ensures that you accurately address the problem’s requirements and set yourself up for success in your structural mechanics assignments.
Simplify the Problem
After thoroughly understanding the problem statement in a structural mechanics assignment, the next step is to simplify the problem. Simplification involves making reasonable assumptions and approximations to make the problem more manageable without significantly compromising accuracy. Here’s how to effectively simplify the problem:
Identify Key Elements
Break down the problem into its fundamental components. Identify the primary elements that are crucial to the analysis, such as:
- Structural Elements: Beams, columns, trusses, cables, etc.
- Load Types: Distributed loads, point loads, axial forces, moments, etc.
- Support Conditions: Fixed, pinned, roller, or free supports.
Make Reasonable Assumptions
Assumptions help to reduce the complexity of the problem. Ensure that these assumptions are reasonable and do not significantly alter the accuracy of the solution. Common assumptions include:
- Linearity: Assuming linear behavior of materials and deflections, unless dealing with large deformations or non-linear materials.
- Small Deflections: Assuming small deflections for beams and other structural elements, making the equations simpler to handle.
- Uniform Material Properties: Assuming material properties are consistent throughout the structure unless specified otherwise.
Model the Structure
Create a simplified model of the structure that captures the essential behavior without unnecessary details. This could involve:
- Idealizing Supports: Representing complex supports as simple supports or hinges to ease calculations.
- Simplifying Load Distributions: Converting complex load distributions into equivalent simpler forms, such as replacing a varying distributed load with an average or uniform load.
Use Symmetry and Redundancy
Leverage symmetry in the structure to reduce the problem size. Symmetrical structures can be analyzed by focusing on a single symmetric portion and extrapolating the results. Additionally, eliminate redundant elements that do not significantly affect the overall behavior of the structure.
Approximate Complex Geometry
Simplify complex geometric shapes and dimensions into more manageable forms. For example, approximate a tapered beam with a prismatic beam if the taper is gradual and does not significantly impact the results.
Reduce Degrees of Freedom
Simplify the analysis by reducing the degrees of freedom. For instance, consider a 2D analysis instead of a 3D analysis if out-of-plane effects are negligible. This makes the calculations simpler and faster while maintaining reasonable accuracy.
Validate Simplifications
Ensure that the simplifications and assumptions made are valid for the problem at hand. Validate them by comparing with known solutions or through preliminary calculations to check if they hold true under the given conditions.
By simplifying the problem effectively, you make it more tractable and easier to solve. This step is crucial in structural mechanics as it allows you to focus on the core aspects of the problem, apply relevant theories, and derive meaningful solutions without getting bogged down by unnecessary complexities.
Apply Relevant Theories and Equations
Once the problem has been thoroughly understood and simplified, the next step in solving structural mechanics problems is to apply the appropriate theories and equations. This involves selecting the correct mathematical models and theoretical frameworks to analyze the problem accurately. Here’s how to effectively apply relevant theories and equations:
Identify Applicable Theories
Determine which theories are applicable to the problem at hand. This depends on the nature of the problem and the type of analysis required. Common theories in structural mechanics include:
- Beam Theory: For analyzing bending, shear, and deflection in beams. Use Euler-Bernoulli beam theory for small deflections and Timoshenko beam theory if shear deformation is significant.
- Plate and Shell Theory: For analyzing thin-walled structures like plates and shells under various load conditions.
- Cable Theory: For analyzing the behavior of cables under tension, such as in suspension bridges or aerial tramways.
- Column Theory: For stability analysis of columns under axial loads, including Euler’s critical load formula for buckling analysis.
Derive Governing Equations
Based on the identified theories, derive the governing equations that describe the behavior of the structure. These equations typically involve relationships between loads, moments, deflections, and material properties. For instance:
- Beam Deflection Equations: Use the differential equation of the elastic curve, d2ydx2=M(x)EI\frac{d^2y}{dx^2} = \frac{M(x)}{EI}dx2d2y=EIM(x), where yyy is the deflection, xxx is the position along the beam, M(x)M(x)M(x) is the bending moment, EEE is the modulus of elasticity, and III is the moment of inertia.
- Stress-Strain Relationships: Use Hooke’s Law, σ=E⋅ϵ\sigma = E \cdot \epsilonσ=E⋅ϵ, where σ\sigmaσ is the stress, EEE is the modulus of elasticity, and ϵ\epsilonϵ is the strain.
- Equilibrium Equations: Apply the conditions of static equilibrium, ∑F=0\sum F = 0∑F=0 and ∑M=0\sum M = 0∑M=0, to solve for unknown forces and moments.
Apply Boundary Conditions
Incorporate the boundary conditions specific to the problem. Boundary conditions define the constraints and supports of the structure, such as fixed, pinned, or roller supports. They are crucial for solving the differential equations governing the structure’s behavior. For example:
- Simply Supported Beam: At a simply supported end, the deflection yyy is zero, and the moment is zero.
- Fixed Support: At a fixed end, both the deflection yyy and the slope dydx\frac{dy}{dx}dxdy are zero.
Solve the Equations
Use the derived equations and boundary conditions to solve for the unknowns. This might involve:
- Analytical Methods: For simple problems, use analytical techniques to solve the differential equations and obtain closed-form solutions.
- Numerical Methods: For more complex problems, use numerical methods such as finite element analysis (FEA) to approximate the solutions.
Validate the Results
After obtaining the solutions, validate them by checking against known solutions, experimental data, or simplified models. Ensure that the results are physically reasonable and consistent with the problem statement.
Consider Nonlinear Effects
For problems involving large deformations, nonlinear material behavior, or dynamic loading, consider the effects of nonlinearity. This might involve using nonlinear theories and equations, such as:
- Nonlinear Beam Theory: For large deflections where linear assumptions are not valid.
- Plasticity Theory: For material behavior beyond the elastic range.
By meticulously applying relevant theories and equations, you ensure that your analysis is grounded in solid scientific principles and mathematical rigor. This step is crucial for deriving accurate and reliable results in structural mechanics problems, laying the foundation for effective problem-solving and design.
Calculate Deflections and Stresses
After understanding the problem, simplifying it, and applying relevant theories and equations, the next crucial step in structural mechanics assignments is to calculate deflections and stresses. These calculations are essential for determining how a structure responds to applied loads and whether it meets safety and performance criteria. Here’s how to systematically calculate deflections and stresses:
Determine the Load Distribution
Identify and define the type of load acting on the structure. This could be point loads, distributed loads, or varying loads. For example:
- Point Load: A concentrated force applied at a specific point.
- Uniformly Distributed Load (UDL): A load spread evenly across a length of the structure.
- Varying Load: A load that changes in intensity along the length of the structure, such as a sinusoidal load.
Use Beam Deflection Formulas
For beams, use standard deflection formulas or the differential equation of the elastic curve to calculate deflections. Common formulas include:
- Simply Supported Beam with Central Point Load: δmax=PL348EI\delta_{\text{max}} = \frac{P L^3}{48 EI}δmax=48EIPL3, where δmax\delta_{\text{max}}δmax is the maximum deflection, PPP is the load, LLL is the span, EEE is the modulus of elasticity, and III is the moment of inertia.
- Simply Supported Beam with Uniform Load: δmax=5qL4384EI\delta_{\text{max}} = \frac{5 q L^4}{384 EI}δmax=384EI5qL4, where qqq is the uniformly distributed load.
For more complex load distributions, use the differential equation d2ydx2=M(x)EI\frac{d^2y}{dx^2} = \frac{M(x)}{EI}dx2d2y=EIM(x) and integrate as necessary, applying boundary conditions to solve for constants of integration.
Apply Superposition Principle
For structures subjected to multiple loads, use the principle of superposition. This principle states that the total deflection is the sum of deflections due to individual loads acting separately. Calculate the deflection for each load and sum them up.
Calculate Stresses
Determine the stresses in the structure using the following formulas:
- Bending Stress: σb=MyI\sigma_b = \frac{M y}{I}σb=IMy, where σb\sigma_bσb is the bending stress, MMM is the moment at the section, yyy is the distance from the neutral axis, and III is the moment of inertia.
- Shear Stress: τ=VQIb\tau = \frac{V Q}{I b}τ=IbVQ, where τ\tauτ is the shear stress, VVV is the shear force, QQQ is the first moment of area above the section where shear is calculated, and bbb is the width of the section.
- Axial Stress: σa=NA\sigma_a = \frac{N}{A}σa=AN, where σa\sigma_aσa is the axial stress, NNN is the axial force, and AAA is the cross-sectional area.
Use Numerical Methods
For more complex structures and load conditions, use numerical methods such as finite element analysis (FEA). FEA software divides the structure into small elements and solves the equations numerically to provide detailed stress and deflection distributions.
Compare with Allowable Limits
Compare the calculated deflections and stresses with allowable limits to ensure the structure’s safety and performance. For deflections, check if they are within serviceability limits. For stresses, ensure they are below the material’s yield strength or allowable stress.
- Deflection Criteria: Typically, maximum deflections should not exceed limits such as L360\frac{L}{360}360L for beams, where LLL is the span.
- Stress Criteria: Ensure stresses are within allowable limits, such as σ<σallowable\sigma < \sigma_{\text{allowable}}σ<σallowable.
Document Results
Clearly document all calculations, assumptions, and results. Provide diagrams, equations, and steps taken to arrive at the final deflections and stresses. This documentation is essential for verifying the analysis and for future reference.
By following these steps, you can accurately calculate deflections and stresses in structural mechanics problems, ensuring that the structure meets safety and performance requirements. This systematic approach is vital for effective analysis and design in structural engineering.
Safety Factors and Design Modifications
In structural mechanics, ensuring that designs meet safety standards and perform reliably under various loads is paramount. This involves calculating safety factors and considering design modifications to enhance structural integrity. Here’s how to approach these tasks effectively:
Understand Safety Factors
A safety factor, also known as a factor of safety (FoS), is a measure of the load-carrying capacity of a structure beyond the expected loads. It accounts for uncertainties in load estimations, material properties, and potential imperfections in construction. The safety factor is calculated as:
FoS=Ultimate Load or StrengthDesign Load or Stress\text{FoS} = \frac{\text{Ultimate Load or Strength}}{\text{Design Load or Stress}}FoS=Design Load or StressUltimate Load or Strength
Calculate Safety Factors
To calculate the safety factor for a structure:
- Determine Ultimate Load or Strength: Identify the maximum load or stress the structure can withstand before failure. This can be based on material properties (yield strength, ultimate tensile strength) and failure criteria.
- Determine Design Load or Stress: Identify the expected maximum load or stress under normal operating conditions, including live loads, dead loads, environmental loads (wind, earthquake), and any other relevant factors.
- Compute FoS: Use the formula above to calculate the safety factor.
For example, if the yield strength of a steel beam is 250 MPa and the maximum expected stress is 50 MPa, the safety factor would be:
FoS=250 MPa50 MPa=5\text{FoS} = \frac{250 \, \text{MPa}}{50 \, \text{MPa}} = 5FoS=50MPa250MPa=5
Evaluate Safety Criteria
Check if the calculated safety factor meets the required standards. Different structures and components have different safety factor requirements depending on their use and the potential consequences of failure. Typical safety factors range from 1.5 to 3 for general structures, and higher for critical structures like bridges or earthquake-resistant buildings.
Design Modifications
If the safety factor does not meet the required criteria, design modifications are necessary to enhance the structural performance. Common modifications include:
- Increase Cross-Sectional Area: Increasing the cross-sectional area of beams, columns, and other structural elements reduces stress and increases load-carrying capacity.
- Change Material: Using materials with higher strength or better performance characteristics can improve the safety factor.
- Add Reinforcements: Adding reinforcements, such as steel bars in concrete or stiffeners in steel beams, can enhance strength and stiffness.
- Modify Geometry: Altering the geometry of the structure, such as reducing spans or adding supports, can reduce deflections and stresses.
- Introduce Pre-Stressing: Pre-stressing techniques, such as applying tensile forces to beams, can improve the load-carrying capacity and reduce deflections.
Example Design Modifications
Consider a simply supported beam with an inadequate safety factor. Here are two potential design modifications:
- Increase Overhang Length: By increasing the overhang length, the load distribution changes, potentially reducing deflection and increasing the safety factor.
- Apply Tensile Force: Applying an external tensile force can increase the transverse stiffness of the beam, reducing central deflection and improving safety.
Validate Design Modifications
After implementing design modifications, recalculate deflections, stresses, and safety factors to ensure the new design meets the required criteria. Use both analytical methods and numerical simulations to validate the modified design.
Consider Alternative Solutions
Always explore multiple design solutions and compare their effectiveness. For example, in addition to increasing overhang length or applying tensile force, you might consider using composite materials or implementing advanced construction techniques.
By systematically evaluating safety factors and considering appropriate design modifications, you ensure that structural designs are robust, reliable, and meet all safety and performance requirements. This approach is critical for the successful and safe completion of engineering projects.
Compare Design Alternatives
When dealing with structural mechanics problems, it’s essential to compare different design alternatives to ensure the best solution is chosen. This involves evaluating the effectiveness, feasibility, cost, and performance of each option.
Analyze Alternatives
Start by analyzing the impact of each proposed design modification. For instance:
- Increasing Overhang Length: Evaluate how increasing the overhang length affects the deflection and stress distribution in the structure. Determine if this modification meets the required safety factor and if it is practical in terms of construction and material usage.
- Applying Tensile Force: Assess how introducing a tensile force enhances the transverse stiffness and reduces central deflection. Calculate the required tensile force and its impact on the overall stability and safety of the structure.
Consider the benefits and drawbacks of each approach. Increasing the overhang might be straightforward but could require additional materials, while applying a tensile force could involve more complex engineering and construction processes.
Optimal Solutions
After evaluating each alternative, select the most practical and efficient solution. Consider factors such as:
- Feasibility: Can the modification be easily implemented given the current construction capabilities and resources?
- Cost: What are the financial implications of each design modification? Does it fit within the budget constraints?
- Performance: Which solution provides the best performance in terms of reducing deflection, increasing load capacity, and meeting safety requirements?
Choose the design that balances these factors effectively, ensuring a robust and economical solution to the problem.
Complex Load Scenarios
Structural mechanics problems often involve complex load scenarios, such as wind loads on cables. Addressing these requires a thorough analysis of the load intensity and resultant forces.
Wind Load Analysis
For scenarios like wind loads on a cable, start by deriving the load intensity from the given parameters. For example, if the wind intensity is sinusoidally distributed, use the appropriate equations to express this load mathematically:
q(x)=q0sin(πxL)q(x) = q_0 \sin\left(\frac{\pi x}{L}\right)q(x)=q0sin(Lπx)
Where q0q_0q0 is the peak load intensity and LLL is the length of the cable. This provides a clear mathematical representation of how the wind load varies along the cable.
Calculate Resultant Forces
Next, calculate the resultant forces and deflections under these load conditions. Use formulas that consider the specific nature of the load and the structure. For a cable subjected to wind load, determine the tension and stress using:
- Resultant Load Intensity: Integrate the load distribution to find the total load acting on the cable.
- Tension in the Cable: Use equilibrium equations and deflection formulas to calculate the tension.
- Tensile Stress: Determine the stress based on the cross-sectional area and the calculated tension.
Ensure that the calculated stresses are within allowable limits to maintain the safety and integrity of the structure.
Graphical Analysis
Visualizing the results of your calculations can provide valuable insights into the behavior of the structure under various loads. Graphical analysis helps in understanding and comparing different design solutions.
Plot Results
Create graphs to visualize key results, such as plotting dimensionless deflections versus load. For example:
w0L vs. qL2EI\frac{w_0}{L} \text{ vs. } \frac{qL^2}{EI}Lw0 vs. EIqL2
These plots can show how deflection varies with different load intensities, helping to identify critical points and trends in the structural response.
Comparative Analysis
Use graphical analysis to compare different solutions, such as bending versus membrane solutions. Plot the dimensionless deflections for both solutions and identify the conditions where they are equivalent:
At what dimensionless deflections do the bending and membrane solutions intersect?\text{At what dimensionless deflections do the bending and membrane solutions intersect?}At what dimensionless deflections do the bending and membrane solutions intersect?
This comparative analysis helps in understanding the relative advantages and limitations of each approach, guiding you towards the most effective design solution.
By following these steps, you ensure a comprehensive analysis of structural mechanics problems, enabling you to choose the best design modifications and effectively address complex load scenarios. This structured approach enhances the accuracy and reliability of your solutions, leading to safer and more efficient structural designs.
Tips for Solving Structural Mechanics Problems
Structural mechanics problems often require a systematic approach to ensure accurate analysis and reliable solutions. Here are some essential tips to help you effectively solve these types of problems:
1. Understand the Problem Statement
- Read Carefully: Begin by thoroughly understanding the problem statement, including the type of structure, loading conditions, and required outputs (deflection, stress, etc.).
- Identify Assumptions: Clarify any assumptions needed for analysis, such as material properties, boundary conditions, and geometric dimensions.
2. Sketch and Visualize
- Draw Diagrams: Sketch the structure and loading conditions to visualize the problem. Include dimensions, supports, applied loads, and any additional details provided.
- Free-Body Diagrams: Create free-body diagrams to isolate components and analyze forces acting on each part of the structure.
3. Apply Relevant Theories and Equations
- Use Fundamental Equations: Apply equations of equilibrium (Newton's laws), kinematics (motion), and constitutive relations (stress-strain) as applicable.
- Beam Deflection Equations: Utilize standard beam deflection formulas (e.g., for simply supported beams, cantilevers) and stress formulas (bending, shear, axial).
4. Consider Boundary Conditions
- Boundary Conditions: Incorporate boundary conditions such as supports (fixed, pinned), constraints (roller supports), and their implications on structural behavior.
- Compatibility Conditions: Ensure that deformations and rotations at interfaces are compatible with adjacent structural elements.
5. Simplify the Problem
- Idealizations: Simplify complex geometries or loading conditions to manageable forms while maintaining essential aspects of the problem.
- Assume Symmetry: Exploit symmetry in structures and loading to reduce the complexity of analysis without compromising accuracy.
6. Systematic Calculation Steps
- Step-by-Step Approach: Break down the problem into smaller, manageable parts. Solve each part sequentially, considering the impact of one step on subsequent calculations.
- Numerical Methods: Use numerical methods (e.g., finite element analysis) for complex geometries or nonlinear material behavior where analytical solutions are challenging.
7. Verify and Validate Results
- Check Units and Dimensions: Ensure consistency of units throughout calculations and final results.
- Comparison with Standards: Compare calculated results with design standards, codes, or previous validated solutions to verify accuracy.
8. Document and Present Findings
- Document Calculations: Maintain clear documentation of assumptions, equations used, calculations performed, and final results.
- Presentation: Clearly present findings with diagrams, tables, and graphs where applicable to enhance clarity and understanding.
9. Iterative Approach
- Iterate if Necessary: If initial results are not satisfactory, reassess assumptions, revisit calculations, and consider alternative approaches or modifications.
10. Continuous Learning and Improvement
- Stay Updated: Keep abreast of advancements in structural analysis techniques, materials, and design methodologies.
- Practice and Review: Regular practice and review of different types of structural problems enhance problem-solving skills and efficiency.
By following these tips, you can approach structural mechanics problems methodically and confidently, ensuring accurate analysis and effective solutions. Each step contributes to a thorough understanding of the problem and facilitates the creation of safe and optimized structural designs.
Conclusion
In conclusion, mastering structural mechanics problem-solving requires a combination of understanding fundamental principles, applying appropriate theories and equations, and employing systematic analysis techniques. By following a structured approach—from comprehending the problem statement and sketching diagrams to applying relevant equations and verifying results—you can effectively navigate complex scenarios. Remember, continuous practice, staying updated with industry standards, and embracing iterative learning are key to honing your skills in structural engineering. With these strategies, you can tackle challenges confidently, ensuring robust and efficient solutions that meet safety, performance, and design criteria.