Optimizing Aerodynamics in Mechanical Engineering: Designing a Competitive Race Car Rear Wing
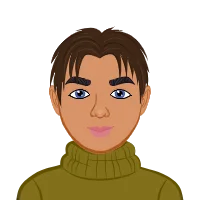
Engineering design and rapid prototyping play pivotal roles in the intricate development processes of components for competitive racing vehicles, exemplified by the rear wing design for Formula SAE race cars. This blog serves as a comprehensive guide, empowering students to navigate the multifaceted challenges of aerodynamics so that you can get help with aerodynamics engineering assignment similar to this one. By exploring the nuances of design optimization, rigorous testing methodologies, and efficient manufacturing practices, students gain invaluable insights into crafting solutions that not only meet but exceed specified functional requirements and constraints. Through this structured approach, students not only hone their technical skills but also cultivate a holistic understanding of how each design decision impacts overall performance and safety in high stakes racing environments. This foundational knowledge prepares them to tackle complex mechanical engineering assignments and projects with confidence and innovation, essential traits for future engineering professionals in competitive industries.
Understanding Functional Requirements
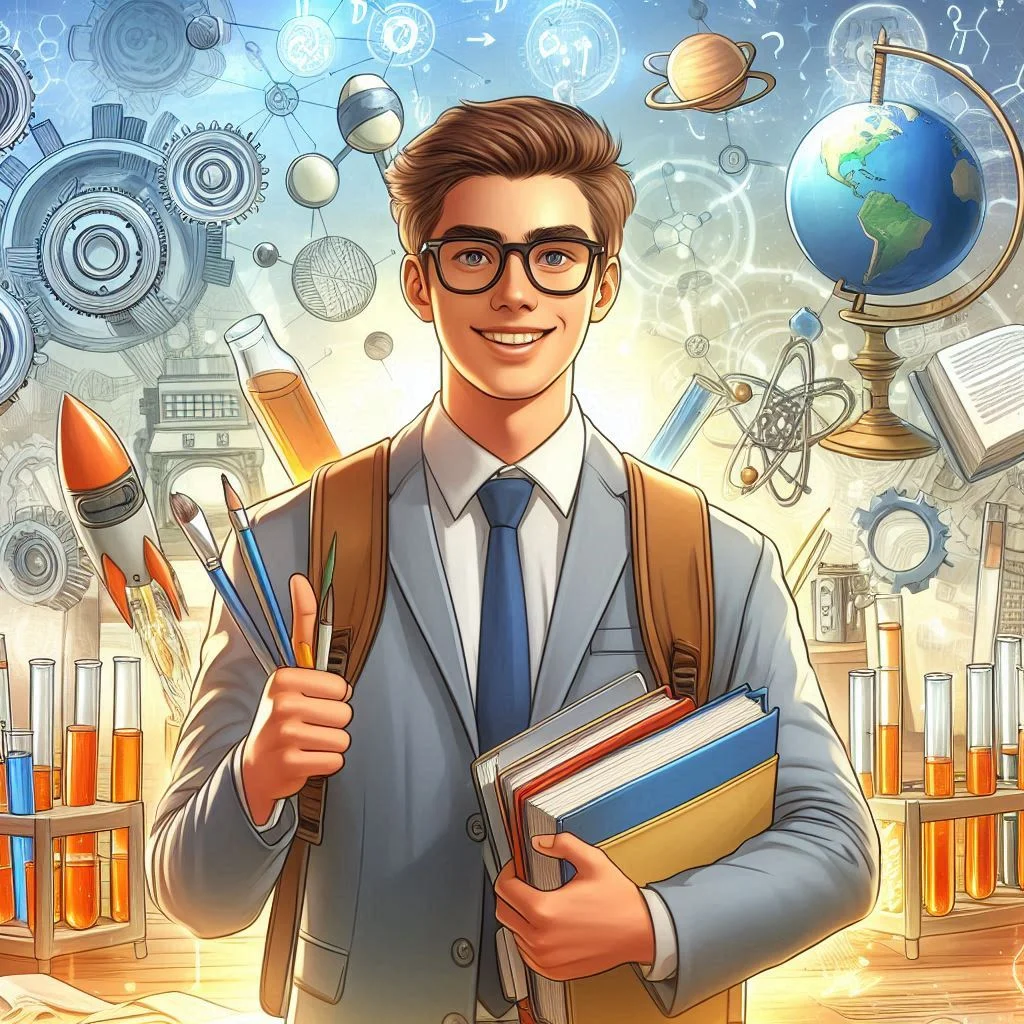
Understanding and meeting functional requirements is crucial in the design and development of components like the rear wing for Formula SAE race cars. These requirements serve as the foundation for ensuring that the designed solution not only performs optimally but also meets the specific needs of the application. By meticulously analyzing and addressing each functional requirement, students gain valuable insights into the complexities of engineering design and the importance of balancing performance objectives with practical constraints. This comprehensive approach not only enhances technical proficiency but also fosters critical thinking and problem-solving skills essential for tackling diverse challenges in mechanical engineering assignments and beyond.
- Downforce and Drag: The primary objective is to optimize the rear wing design to maximize downforce while minimizing drag. Downforce is crucial for enhancing traction and stability through corners, ensuring the vehicle maintains high speeds and adheres firmly to the track surface. Minimizing drag is equally essential to improve overall aerodynamic efficiency, reducing resistance and enhancing speed.
- Calculate Downforce: Utilize advanced aerodynamic principles and computational tools to determine the optimal wing shape, angle of attack, and airflow characteristics that will generate at least 250 N of downforce. This involves conducting detailed simulations and analyses to predict the aerodynamic forces acting on the wing under various operating conditions.
- Minimize Drag: Employ rigorous design optimization techniques to ensure the rear wing generates no more than 75 N of drag. This includes optimizing the wing profile, refining surface textures, and carefully selecting materials with favorable aerodynamic properties. Effective material selection and streamlined design can significantly reduce drag forces, thereby improving overall vehicle performance.
- Weight Constraints: The rear wing must adhere to strict weight limitations, not exceeding 2.5 kg. Achieving this requires careful consideration of material choices and structural design.
- Material Selection: Choose materials such as 6061 aluminum, blue construction insulation foam, fiberglass, and epoxy adhesive that offer a high strength-to-weight ratio. Each material must be evaluated for its mechanical properties, durability, and compatibility with manufacturing processes to ensure optimal performance under racing conditions.
- Structural Integrity: Ensure the rear wing maintains robust structural integrity across a wide range of operating conditions, including speeds and cornering forces below 100 mph. Implement a safety factor of 2 for all structural load cases to account for dynamic forces and ensure the wing withstands rigorous testing and racing conditions.
- Safety Factor Calculation: Apply rigorous engineering calculations and simulations to determine the appropriate safety margins for structural components. A safety factor of 2 ensures that the wing can withstand unexpected loads, impacts, and vibrations without compromising performance or safety.
- Deflection Limits: The rear wing must exhibit minimal deflection, not exceeding 10 mm at any point during operation below 100 mph. Conduct comprehensive deflection analysis using finite element analysis (FEA) and other advanced modeling techniques to predict and validate deflection behavior under different loading scenarios. This ensures that the wing maintains optimal aerodynamic efficiency and stability throughout its operational lifespan.
By meticulously addressing these functional requirements, students gain invaluable insights into the complexities of mechanical design, aerodynamics, structural analysis, and materials science. This comprehensive approach not only enhances technical proficiency but also fosters critical thinking and problem-solving skills essential for tackling diverse challenges in mechanical engineering assignments and real-world applications.
Navigating Constraints
Navigating the constraints inherent in designing a rear wing for a Formula SAE race car requires careful consideration of various factors, from operational conditions to material limitations. Each constraint plays a critical role in shaping the final design and ensuring the wing meets performance expectations while adhering to competition regulations and practical constraints.
- Operational Conditions: Understanding and defining the specific operational conditions under which the rear wing will perform is essential. For instance, the steady-state operating condition at 60 mph on flat terrain defines the baseline for aerodynamic performance and structural integrity testing. Detailed simulations and wind tunnel testing help validate the wing's performance under these conditions, ensuring it meets downforce and drag requirements effectively.
- Material Limitations: The choice of materials is constrained by factors such as weight limitations, manufacturing capabilities, and cost considerations. Opting for materials like 6061 aluminum, insulation foam, fiberglass, and epoxy adhesive not only meets strength and weight criteria but also ensures compatibility with manufacturing processes like waterjet cutting. Balancing material properties with design requirements is crucial to achieving an optimal balance of performance and cost-efficiency.
- Geometric and Design Constraints: The rear wing's design must adhere to specific geometric constraints, such as dimensional limits and attachment point specifications. The design process involves creating a streamlined 2D wing section without taper or dihedral, optimizing aerodynamic performance within the defined dimensional envelope. Compliance with these constraints ensures the wing integrates seamlessly with the vehicle's aerodynamic profile and support structure.
- Energy and Environmental Constraints: The rear wing design prohibits the use of external energy sources, requiring a passive design approach that harnesses aerodynamic principles to generate downforce efficiently. This constraint promotes innovation in aerodynamic shaping and surface treatment to minimize drag and maximize performance without relying on additional energy inputs.
- Manufacturing Constraints: Manufacturing constraints, including machining capabilities and cost-effectiveness, influence the production feasibility of the rear wing design. Utilizing advanced manufacturing techniques like waterjet cutting at a specified rate ensures precise fabrication of complex wing profiles while managing production costs within budgetary limits.
Navigating these constraints requires a systematic approach that integrates theoretical knowledge with practical application. By addressing each constraint strategically, students not only develop technical proficiency in mechanical design and aerodynamics but also cultivate problem-solving skills essential for overcoming challenges in real-world engineering projects. This holistic understanding prepares students to excel in competitive environments, where innovation and adherence to constraints are paramount to success.
Design Interface
The interface design of the rear wing for a Formula SAE race car involves critical considerations to ensure seamless integration with the vehicle's structure and aerodynamic performance. This section outlines key aspects of designing the interface, focusing on dimensional compatibility, attachment points, and structural integrity.
- Dimensional Compatibility: The rear wing must adhere to specific dimensional constraints to fit within the vehicle's overall design envelope. Design parameters such as width, height, and span are defined to optimize aerodynamic efficiency while maintaining structural stability. Ensuring the wing's dimensions align with these specifications is essential for enhancing vehicle performance and stability during racing conditions.
- Attachment Points: The interface design includes detailed specifications for attachment points that secure the rear wing to the vehicle's chassis. These attachment points must align precisely with the structural framework of the Formula SAE car, accommodating standardized bolt hole patterns and support brackets. Designing robust attachment mechanisms ensures that the wing remains securely mounted during high-speed maneuvers, minimizing vibrations and maximizing downforce transfer to the track surface.
- Structural Integrity: Structural integrity is paramount in the interface design to withstand dynamic loads and aerodynamic forces encountered during racing. Applying engineering principles such as stress analysis and load testing ensures that the attachment points and supporting structure can endure the rigors of competition without compromising safety or performance. Implementing a safety factor of 2 in structural calculations reinforces the design's reliability and resilience under varying operating conditions.
- Manufacturability and Assembly: Considerations for manufacturability and assembly influence interface design decisions. Utilizing materials like 6061 aluminum and fiberglass that offer high strength-to-weight ratios facilitates lightweight yet durable components. Designing components for compatibility with manufacturing processes such as waterjet cutting and epoxy bonding streamlines production while maintaining cost-effectiveness and precision.
- Testing and Validation: Rigorous testing and validation procedures verify the interface design's performance and reliability. Wind tunnel testing and structural load tests simulate real-world conditions to assess aerodynamic efficiency, stability, and structural integrity. Data-driven analysis from these tests informs iterative design improvements, ensuring that the interface design meets or exceeds performance expectations and regulatory requirements.
By addressing these aspects comprehensively, students gain practical insights into the complexities of interface design for competitive racing vehicles. This integrated approach not only enhances technical proficiency in mechanical engineering but also fosters innovation and critical thinking essential for tackling engineering challenges in diverse applications.
Verification and Testing
Verification and testing are critical phases in the development of a rear wing for a Formula SAE race car, ensuring that the design meets performance specifications and safety standards. This section outlines key aspects of verification and testing, emphasizing the importance of comprehensive testing methodologies and validation procedures.
- Wind Tunnel Testing: Wind tunnel testing is integral to evaluating the aerodynamic performance of the rear wing under controlled conditions. Testing the wing across a range of speeds, from 10 to 100 mph in 20 mph increments, allows engineers to measure and analyze critical aerodynamic parameters such as lift, drag, and side force. Data obtained from wind tunnel tests validates the design's aerodynamic efficiency and confirms its ability to generate the required downforce while minimizing drag within specified limits.
- Structural Load Testing: Structural load testing assesses the rear wing's structural integrity and durability under dynamic conditions. Applying loads representative of racing scenarios, such as cornering forces and vehicle vibrations, ensures that the wing can withstand operational stresses without deformation or failure. Laser distance measurement equipment and bonded strain gauges monitor deflection and stress distribution, providing quantitative data to validate the design's safety factor and structural robustness.
- Static Load Testing: Static load testing verifies compliance with deflection limits and safety factors established during the design phase. Using calibrated equipment and precise measurement techniques, engineers apply static loads to the wing to simulate maximum operating conditions. This testing ensures that the wing maintains dimensional stability and meets deflection criteria, crucial for maintaining aerodynamic performance and vehicle stability at high speeds.
- Performance Validation: Performance validation involves comparing test results against initial design specifications and performance requirements. Data analysis from wind tunnel tests, structural load tests, and static load tests validates the wing's ability to meet or exceed downforce, drag, and structural integrity targets. Any deviations or discrepancies discovered during validation prompt design refinements and iterative improvements to optimize overall performance and reliability.
- Safety and Compliance: Ensuring compliance with safety regulations and competition rules is paramount throughout the verification and testing phases. Adhering to established safety standards and guidelines minimizes risks associated with structural failure or aerodynamic instability during racing events. Compliance checks and certification processes validate that the rear wing design meets all regulatory requirements, guaranteeing safe and reliable operation on the race track.
- Iterative Design Improvement: Iterative design improvement based on verification and testing results enhances the rear wing's overall performance and reliability. Analyzing test data, identifying design weaknesses, and implementing corrective measures foster continuous improvement in aerodynamic efficiency, structural strength, and operational durability. This iterative approach ensures that the final design achieves optimal performance while meeting the evolving demands of Formula SAE competition and real-world racing applications.
By integrating rigorous verification and testing processes into the design and development cycle, engineers and students alike gain valuable insights into the complexities of aerospace engineering, aerodynamics, and structural mechanics. This holistic approach not only enhances technical proficiency but also cultivates innovation and problem-solving skills essential for success in competitive engineering environments.
Conclusion
Designing a rear wing for a Formula SAE race car demands a meticulous blend of engineering principles, innovative thinking, and rigorous testing. Throughout this process, engineers and students encounter multifaceted challenges and opportunities to push the boundaries of performance and efficiency.
From defining functional requirements and navigating constraints to designing interfaces and conducting comprehensive verification and testing, every phase of the design cycle plays a pivotal role in shaping the final product. By leveraging advanced aerodynamic simulations, structural analysis tools, and practical manufacturing techniques, engineers optimize the wing's design to achieve optimal downforce, minimize drag, and uphold structural integrity under demanding racing conditions.
Wind tunnel testing validates the wing's aerodynamic efficiency, while structural load and static tests ensure its robustness and reliability. Performance validation against stringent criteria confirms that the design not only meets but exceeds expectations, enhancing vehicle performance and safety on the track.
Moreover, adherence to safety standards and compliance with competition regulations underscore the design's reliability and suitability for competitive racing environments. Continuous iteration based on testing feedback enables engineers to refine and improve the design, driving innovation and excellence in Formula SAE vehicle development.
In conclusion, designing a rear wing for a Formula SAE race car is not just about meeting technical specifications; it's about pushing the limits of engineering innovation and preparing students for future challenges in the dynamic field of automotive and aerospace engineering. By embracing these challenges with creativity, diligence, and a commitment to excellence, engineers and students contribute to the advancement of vehicle technology and uphold the spirit of innovation in motorsports.