Expert Advice: Optimizing Your Mechanical Engineering Projects with Abaqus
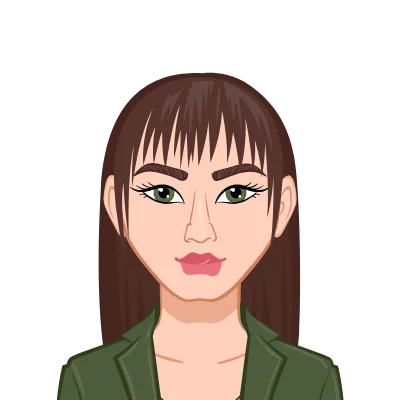
Optimization is a cornerstone in the realm of mechanical engineering projects, playing a pivotal role in enhancing efficiency, performance, and cost-effectiveness. At its core, optimization involves the systematic refinement of designs, processes, and components to achieve the best possible outcome within specified constraints. In the context of mechanical engineering, where precision and functionality are paramount, optimization is not merely a desirable aspect but a critical necessity. It is the key to achieving superior performance, minimizing material usage, reducing manufacturing costs, and ensuring the longevity and reliability of mechanical systems.
In this landscape, Abaqus emerges as a powerful and indispensable tool for simulation and analysis, seamlessly integrating itself into the optimization workflow of mechanical engineers. Developed by Dassault Systèmes, Abaqus is a robust finite element analysis (FEA) software suite that empowers engineers to simulate and analyze the behavior of structures and components under various conditions. Its versatility extends to simulating complex physical phenomena, such as mechanical, thermal, and multiphysics interactions, enabling engineers to gain deep insights into the performance of their designs.
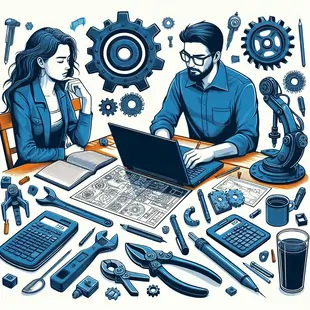
Abaqus facilitates a comprehensive understanding of how different factors impact the structural integrity and functionality of mechanical systems. Engineers can explore and analyze the effects of varying parameters, materials, and design configurations without the need for physical prototypes. This not only accelerates the product development cycle but also significantly reduces costs associated with experimental testing. The ability to conduct virtual experiments through Abaqus, including the capability to solve your Abaqus assignment, empowers engineers to iterate through design alternatives rapidly, fine-tuning and optimizing their projects before committing to physical production.
One of the standout features of Abaqus is its capability to handle nonlinear analysis, allowing engineers to simulate the real-world behavior of materials and structures under a wide range of conditions. This is particularly crucial in mechanical engineering, where components often experience nonlinear deformations, material yielding, and complex interactions. The software's advanced algorithms and simulation capabilities enable engineers to model these intricacies accurately, providing a realistic representation of how a design will perform in practical applications.
Furthermore, Abaqus excels in addressing challenges associated with structural optimization. Its integrated optimization tools enable engineers to systematically explore design spaces, identify optimal configurations, and refine their designs for improved performance. By leveraging Abaqus for optimization, mechanical engineers can fine-tune parameters such as geometry, material properties, and load conditions to achieve the desired outcome, whether it be maximizing strength, minimizing weight, or optimizing thermal performance.
In conclusion, optimization is the linchpin of success in mechanical engineering projects, driving innovation and efficiency in design and manufacturing processes. Abaqus stands as a formidable ally in this pursuit, providing engineers with a sophisticated platform for simulation and analysis. Its ability to navigate the complexities of nonlinear behavior, coupled with robust optimization tools, empowers mechanical engineers to push the boundaries of what is achievable. As the engineering landscape continues to evolve, Abaqus remains an indispensable tool, guiding the path toward optimized, resilient, and high-performing mechanical systems.
Understanding Abaqus for Mechanical Engineering:
Understanding Abaqus in the context of mechanical engineering requires delving into its multifaceted capabilities, which make it an indispensable tool for engineers across various industries. Abaqus, developed by Dassault Systèmes, is a comprehensive finite element analysis (FEA) software suite renowned for its versatility and precision. At its core, Abaqus enables engineers to simulate and analyze the behavior of structures and components, offering a virtual laboratory for assessing the performance and integrity of mechanical systems.
One of the key strengths of Abaqus lies in its ability to handle complex and nonlinear analyses. In mechanical engineering, where components often experience nonlinear deformations, material yielding, and intricate interactions, this capability is paramount. Abaqus employs advanced algorithms to model and simulate real-world behaviors accurately, allowing engineers to predict how materials and structures will respond under various conditions. This capability is particularly crucial in scenarios where linear approximations fall short, providing a more realistic representation of the mechanical system's performance.
Abaqus offers a user-friendly interface coupled with a powerful solver, making it accessible to both novice and experienced users. Its intuitive modeling environment allows engineers to create detailed simulations of their designs, incorporating factors such as material properties, boundary conditions, and loading scenarios. The software supports a wide range of materials and allows for the incorporation of thermal, structural, and multiphysics analyses, enabling engineers to comprehensively study the behavior of their designs.
The software's versatility extends to dynamic simulations, enabling engineers to analyze the response of mechanical systems to transient loads, vibrations, and impact forces. This capability is invaluable in industries such as automotive and aerospace, where understanding how structures respond to dynamic conditions is critical for ensuring safety and reliability.
Abaqus also excels in providing a platform for parametric studies and design exploration. Engineers can systematically vary parameters such as geometry, material properties, and loading conditions to understand their impact on the overall performance of a design. This feature accelerates the design iteration process, allowing engineers to explore a multitude of design alternatives efficiently. The parametric capabilities of Abaqus make it an invaluable tool for optimization, enabling engineers to fine-tune designs for enhanced performance, cost-effectiveness, and efficiency.
Furthermore, Abaqus integrates seamlessly with other engineering software and tools, facilitating a cohesive workflow for engineers. Whether collaborating with CAD software for design input or exporting simulation results to visualization tools, Abaqus ensures compatibility and interoperability across the engineering ecosystem.
In conclusion, understanding Abaqus in the realm of mechanical engineering unveils a sophisticated and versatile tool that empowers engineers to simulate, analyze, and optimize their designs with precision. Its capabilities in handling nonlinear analyses, dynamic simulations, and parametric studies make it a cornerstone in the virtual testing and validation of mechanical systems. As industries continue to push the boundaries of innovation, Abaqus remains at the forefront, providing a robust platform for engineers to unravel the complexities of mechanical behavior and drive the advancement of engineering solutions.
Importance of Optimization in Mechanical Engineering:
Optimization stands as a cornerstone in the field of mechanical engineering, serving as a linchpin for achieving excellence in design, efficiency, and cost-effectiveness. At its essence, optimization in mechanical engineering refers to the systematic process of refining and fine-tuning designs, processes, and systems to attain the best possible outcomes within defined constraints. This critical aspect of the engineering discipline plays a pivotal role in addressing the multifaceted challenges faced by engineers, ranging from enhancing the performance of mechanical components to minimizing material usage and production costs.
The significance of optimization becomes evident in its ability to unlock unparalleled efficiency and functionality in mechanical systems. In a landscape where technological advancements continuously push the boundaries of what is achievable, optimizing mechanical designs becomes not only a desirable pursuit but a requisite for staying competitive and innovative. Through optimization, engineers aim to strike an optimal balance between conflicting design objectives, whether it be maximizing strength while minimizing weight, improving thermal performance, or achieving cost-effective manufacturing processes.
Moreover, optimization is intrinsically tied to resource utilization and sustainability in mechanical engineering. By systematically refining designs and processes, engineers can reduce the environmental impact of manufacturing and operation. This aligns with the growing global emphasis on sustainable practices, prompting the engineering community to seek solutions that not only meet performance criteria but also contribute to the broader goal of environmental responsibility.
In the realm of product development, optimization significantly accelerates the design iteration cycle. Traditional trial-and-error methods are replaced by virtual simulations and analyses that allow engineers to explore a multitude of design alternatives rapidly. This iterative approach empowers engineers to uncover the most efficient and effective solutions, leading to shorter development cycles and quicker time-to-market for new products. As a result, optimization becomes an enabler of innovation, fostering the creation of cutting-edge technologies and solutions in the competitive landscape of mechanical engineering.
Cost considerations play a pivotal role in any engineering endeavor, and optimization is a key driver in achieving cost-effectiveness. By minimizing material usage, reducing manufacturing complexities, and enhancing energy efficiency, engineers can contribute to substantial cost savings throughout the product lifecycle. Optimization strategies extend beyond the design phase, encompassing manufacturing processes, supply chain logistics, and the overall lifecycle management of mechanical systems.
Furthermore, optimization is crucial in ensuring the reliability and safety of mechanical components and systems. Rigorous analysis and fine-tuning of designs help engineers identify potential weaknesses, vulnerabilities, and failure points, allowing for preemptive adjustments to enhance robustness and durability. This proactive approach not only mitigates risks but also contributes to the creation of highly reliable and resilient mechanical solutions.
In conclusion, the importance of optimization in mechanical engineering cannot be overstated. It is the driving force behind the quest for excellence, pushing engineers to continuously refine and elevate their designs to meet ever-evolving challenges. Optimization not only enhances performance but also aligns engineering practices with sustainability goals, accelerates innovation, and ensures cost-effective solutions that stand the test of time. As the engineering landscape evolves, the role of optimization remains central in shaping the future of mechanical engineering.
Key Strategies for Optimizing Mechanical Engineering Projects with Abaqus:
Optimizing mechanical engineering projects with Abaqus involves a strategic approach that harnesses the powerful capabilities of this finite element analysis (FEA) software suite. Abaqus, developed by Dassault Systèmes, offers a versatile platform for simulation and analysis, enabling engineers to fine-tune designs and achieve superior project outcomes. Several key strategies can be employed to optimize mechanical engineering projects effectively using Abaqus.
One pivotal strategy is the incorporation of parameterization and design exploration. Abaqus allows engineers to define and manipulate parameters within their models, facilitating the exploration of various design alternatives systematically. By varying parameters such as geometric dimensions, material properties, and loading conditions, engineers can conduct parametric studies to understand the impact of these variations on project performance. This iterative process empowers engineers to identify optimal configurations, refine designs, and achieve superior outcomes without the need for extensive physical prototyping.
Material selection and property optimization represent another critical aspect of optimizing mechanical engineering projects with Abaqus. The software provides sophisticated tools for modeling a wide range of materials and accurately simulating their behavior under different conditions. Engineers can leverage Abaqus to explore material options, assess their performance, and optimize material properties to meet specific project requirements. This strategy is particularly valuable in industries where the selection of materials significantly influences the overall performance and reliability of mechanical components.
Abaqus excels in topology and shape optimization, offering advanced features that enable engineers to optimize the form and structure of their designs. Topology optimization involves systematically redistributing material within a given design space to achieve the best structural performance. Abaqus facilitates this process by iteratively evaluating and refining the topology of the model, resulting in designs that are both structurally efficient and lightweight. Shape optimization, on the other hand, allows engineers to fine-tune the geometry of components for optimal performance. These optimization strategies are instrumental in creating designs that meet stringent performance criteria while minimizing material usage, contributing to efficiency and sustainability in mechanical engineering projects.
Case studies serve as a valuable strategy for showcasing the practical application of Abaqus in optimizing mechanical engineering projects. By presenting real-life examples of successful optimization efforts, engineers can illustrate the software's efficacy in solving complex challenges. These case studies can cover a spectrum of industries, ranging from automotive and aerospace to energy and manufacturing. In-depth analyses of the challenges faced, the optimization strategies employed, and the positive outcomes achieved provide valuable insights for other engineers seeking to leverage Abaqus for their own projects.
In addition to specific optimization strategies, it's essential to highlight general tips and best practices when using Abaqus for mechanical engineering projects. This includes guidance on setting up accurate and efficient simulations, selecting appropriate analysis types, and interpreting results effectively. Tips for overcoming common challenges and pitfalls in the optimization process can empower engineers to navigate complexities seamlessly and achieve optimal results.
In conclusion, optimizing mechanical engineering projects with Abaqus involves a holistic approach that encompasses parameterization, material optimization, topology and shape optimization, and the presentation of relevant case studies. By employing these key strategies, engineers can leverage the full potential of Abaqus to create innovative, efficient, and reliable mechanical designs that meet and exceed performance expectations. This strategic integration of Abaqus into the optimization workflow contributes to the advancement of mechanical engineering practices and the realization of optimal project outcomes.
Conclusion:
In the realm of mechanical engineering, the conclusion of any project is marked not by the cessation of efforts but by the realization of optimal outcomes through meticulous planning, strategic execution, and the integration of advanced tools. As the curtain falls on the journey of optimizing mechanical engineering projects with Abaqus, the overarching theme is one of empowerment and innovation. Abaqus, the powerful finite element analysis (FEA) software suite from Dassault Systemes, emerges as a catalyst for transformative change in the industry, offering engineers a comprehensive platform to navigate the complexities of design, simulation, and analysis.
The strategies outlined for optimizing mechanical engineering projects with Abaqus represent a roadmap that engineers can follow to unlock the full potential of their designs. The incorporation of parameterization and design exploration is akin to opening a treasure trove of possibilities. By systematically varying design parameters, engineers embark on a journey of discovery, uncovering the configurations that yield optimal performance. Abaqus, with its intuitive interface and robust solver, becomes the compass guiding engineers through the intricate landscape of design alternatives. The result is a streamlined and efficient design process that not only accelerates the development cycle but also ensures that the final product is finely tuned to meet and exceed performance expectations.
Material selection and property optimization take center stage as engineers delve into the intricacies of their projects. Abaqus, with its advanced material modeling capabilities, transforms the way engineers approach material choices. The ability to simulate and analyze the behavior of diverse materials under different conditions empowers engineers to make informed decisions that directly impact project performance. This strategy is a testament to the pivotal role Abaqus plays in aligning engineering practices with the ever-evolving landscape of material science, ensuring that projects are not only optimized for performance but also for sustainability and environmental responsibility.
Topology and shape optimization represent a paradigm shift in design philosophy, transcending traditional boundaries and embracing efficiency. Abaqus facilitates this shift by providing tools that redefine the structural form and geometry of components. Engineers, armed with the capability to systematically optimize the distribution of material and fine-tune shapes, create designs that are not only structurally efficient but also inherently innovative. The resulting designs are a testament to the synergy between human ingenuity and the computational prowess of Abaqus, fostering a culture of continuous improvement and advancement in mechanical engineering.
As the strategies culminate in the optimization of mechanical engineering projects with Abaqus, the broader implications of these endeavors become apparent. Beyond the tangible benefits of enhanced performance, cost savings, and efficient designs, there lies a narrative of evolution. The integration of Abaqus into the optimization workflow signals a paradigm shift in how mechanical engineering projects are conceived, developed, and brought to fruition. It symbolizes a departure from conventional methods, ushering in an era where virtual simulations and analyses pave the way for groundbreaking designs and solutions.
In this conclusion, the spotlight inevitably turns to the engineers, the architects of this transformation. Their commitment to excellence, coupled with the capabilities of Abaqus, propels the field of mechanical engineering into new frontiers. As the journey continues, the conclusion becomes a prelude to the next chapter, where engineers armed with Abaqus continue to explore, innovate, and optimize, forging a path towards a future where mechanical designs seamlessly blend efficiency, sustainability, and ingenuity.