Essential Features in Creo For Options Aiding Construction of Parts
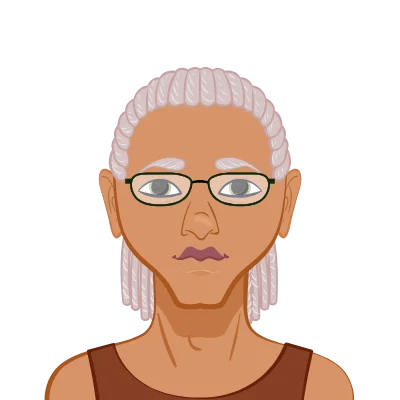
When it comes to 3D modeling and design, PTC Creo stands out as a powerful tool that offers a wide range of options to aid in the construction of parts. This versatile software enables users to create complex parts with precision and efficiency. In this blog post, we'll explore several important features within Creo that assist in the construction of parts, including creating holes, rounds, chamfers, understanding ribs, and various methods for editing features. If you need help with your Creo assignment, these features can be valuable resources to enhance your proficiency in utilizing this robust software.
Creating Holes
Holes are a fundamental element in many mechanical designs. Whether you're designing a simple bracket or a complex assembly, Creo provides the tools to create holes of various types and sizes.
The Hole Dashboard
Creo's Hole feature is a versatile tool that allows you to create a variety of hole types, including simple holes, counterbored holes, countersunk holes, and more. To access the Hole feature, you can use the "Hole" tool in the toolbar or the Hole Dashboard.
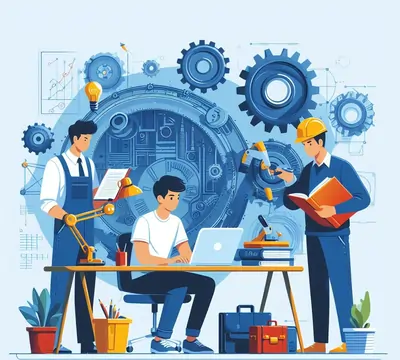
The Hole Dashboard provides a user-friendly interface for creating holes. It allows you to specify parameters such as hole type, size, placement, and depth. You can choose from standard hole sizes or create custom hole definitions to match your design requirements accurately.
Important Points to Remember While Creating a Hole
Creating holes in Creo is a fundamental aspect of part design, and it's essential to pay close attention to several key points to ensure your design aligns with your requirements. When creating holes in Creo, keep these points in mind:
- Hole Type Selection:
- Creo offers a variety of hole types to choose from, including:
- Simple Holes: These are basic, cylindrical holes with a uniform diameter and depth.
- Counterbored Holes: Counterbores are used when you need to create a larger-diameter hole at the opening, followed by a smaller-diameter hole that goes deeper into the part.
- Countersunk Holes: Countersinks involve a conical recess at the opening of the hole, allowing for flush mounting of screws or bolts.
- Selecting the appropriate hole type is crucial because it directly impacts the functionality and aesthetics of your design. Your choice should align with your specific design requirements.
- Placement Precision:
- The placement of a hole is crucial in ensuring the part's overall functionality and structural integrity. When positioning a hole, consider the following factors:
- Existing Surface: You can place a hole on an existing surface or face of the part. This is a common choice for holes that need to be aligned with a specific feature on the part.
- Reference Plane: Utilize reference planes when you need to establish a specific position relative to a plane or surface, especially when creating holes at non-standard angles or positions.
- Specific Dimensions: You can also position a hole by specifying exact dimensions, such as distance from edges or other features. This method ensures precise placement.
- Size and Depth Specification:
- Accurately defining the hole's diameter and depth is essential for manufacturing and assembly. Consider the following when specifying these parameters:
- Diameter: The hole's diameter is a critical dimension. It should match the size of the fastener, component, or other parts that will interact with the hole.
- Depth: The depth of the hole determines how far it penetrates into the part. Accurate depth is essential for ensuring the part's structural integrity and compatibility with other components.
- Hole Tolerances: Hole tolerances define the allowable variations in hole dimensions during manufacturing. By specifying tolerances, you ensure that the hole meets the required precision standards.
- Customization for Unique Requirements:
- Creo understands that not all design projects fit into standard parameters. In cases where your design calls for non-standard hole sizes or shapes, Creo empowers you to create custom hole definitions.
- Custom holes can be defined with unique shapes, such as polygons or complex contours, to accommodate specific design needs.
- Custom hole creation enables you to maintain precision and adherence to design standards while accommodating the uniqueness of your project.
In summary, creating holes in Creo involves careful consideration of the hole type, precise placement, accurate sizing, and customization options. These key points are crucial for achieving the desired functionality, compatibility, and precision in your part design. By mastering these aspects, you can leverage Creo's capabilities to create parts that meet your exact specifications and design goals.
Creating Rounds
Rounding edges and corners is a common practice in mechanical design. Rounds enhance the aesthetic appeal of a part while reducing stress concentrations. Creo provides two main types of rounding options: Basic Rounds and Variable Radius Rounds.
Creating Basic Rounds
Basic Rounds are simple fillets applied uniformly to all edges or corners selected. Here's how you can create them:
- Select the Edges or Corners to Round:
- Edge Selection: You can select one or more edges on the part that you wish to round. These edges can be interior edges, external edges, or any combination that suits your design. Ensure that you select all the edges that require filleting for a uniform appearance.
- Corner Selection: In addition to edges, you can also select corners, which are the points where two or more edges intersect. Filleting corners can help smooth out sharp angles in your design, making it more visually appealing and safer.
- Specify the Radius for the Fillet:
- Radius Selection: Creo allows you to enter a specific radius value or select a radius interactively by clicking on the edge or corner. When entering a numerical value, consider the design requirements and constraints to ensure the fillet size is appropriate.
- Radius Uniformity: One of the defining characteristics of Basic Rounds is that they apply the same radius uniformly to all selected edges and corners. This consistency ensures a cohesive appearance throughout your model and maintains structural integrity by eliminating sharp angles.
- Creo Automatically Applies the Fillet Uniformly:
To begin creating Basic Rounds in Creo, you need to select the specific edges or corners of your 3D model that you want to round. Here are some important considerations:
After selecting the edges or corners to round, you need to specify the radius for the fillet. The radius determines the size of the rounded portion, and it plays a crucial role in the aesthetics and functionality of your design. Here's how to specify the radius:
Once you've selected the edges or corners and specified the radius, Creo will automatically apply the fillet uniformly to all the selected features. The fillet blends the edges or corners by creating a smooth, curved transition between them. This process significantly contributes to the visual appeal of your model while reducing stress concentrations and improving durability.
Points to Remember when Creating Basic Rounds:
When working with Basic Rounds in Creo, there are some additional considerations:
- Balancing Design Goals: The radius of the fillet should align with your design goals. While larger fillets provide a more substantial, softer appearance, smaller fillets are more subtle. The choice of radius should balance aesthetics and functionality.
- Effect on Assembly: When designing parts for assembly, consider how Basic Rounds may affect the interaction between parts. Roundings can ensure a smooth fit and ease of assembly.
- Aesthetic Enhancement: Beyond functionality, Basic Rounds have a significant impact on the aesthetics of your part. They soften harsh edges and corners, making the design more visually appealing.
- Stress Distribution: Basic Rounds help distribute stress more evenly, reducing stress concentrations at edges and corners. This can improve the durability and strength of the part.
Creating Basic Rounds in Creo is a versatile tool that simplifies the process of rounding edges and corners in your 3D models. By selecting edges or corners, specifying the desired radius, and allowing Creo to uniformly apply the fillet, you can enhance the visual appeal and functionality of your designs. Basic Rounds are a valuable feature for creating parts that not only look good but also perform optimally.
Creating a Variable Radius Round
In some cases, you might need rounds with varying radii. Variable Radius Rounds offer a more advanced way to achieve this:
- Select the edges or corners you want to round.
- Specify different radii for each selected edge or corner.
- Creo will apply variable radius rounds as per your specifications.
Points to Remember While Creating Rounds
When using Creo to create rounds, remember the following:
- Uniformity vs. Variable Radius: Choose between Basic Rounds and Variable Radius Rounds based on your design needs.
- Radius Selection: Select an appropriate radius that complements the part's design and functional requirements.
- Visual and Structural Impact: Rounds not only affect aesthetics but also play a role in stress distribution. Consider both aspects when applying rounds.
Creating Chamfers
Chamfers are another essential feature for parts design. They serve to break edges, reduce sharp angles, and make parts more comfortable to handle. Creo provides two types of chamfers: Corner Chamfer and Edge Chamfer.
Corner Chamfer
Corner chamfers are applied to the intersections of two adjacent edges. To create a corner chamfer in Creo:
- Select the edges forming the corner.
- Specify the chamfer size and angle.
- Creo will apply the chamfer to the selected edges.
Edge Chamfer
Edge chamfers are applied to individual edges. To create an edge chamfer in Creo:
- Select the edge you want to chamfer.
- Specify the chamfer size and angle.
- Creo will apply the chamfer to the selected edge.
Chamfers, like rounds, contribute to both the visual appeal and functionality of a part. They can improve ergonomics and ease of assembly.
Understanding Ribs
Ribs are features that add strength and rigidity to parts. They are typically used to reinforce walls or create structural support. Creo offers two main types of ribs: Trajectory Ribs and Profile Ribs.
Creating Trajectory Ribs
Trajectory Ribs are created along a specified trajectory or path. Here's how you can create them:
- Select the trajectory or path along which you want to create the rib.
- Define the rib's width, depth, and other parameters.
- Creo will generate the rib along the chosen path, reinforcing the part accordingly.
Creating Profile Ribs
Profile Ribs are created based on a profile sketch. To create a profile rib in Creo:
- Create a sketch that represents the rib's cross-sectional profile.
- Select the sketch as the profile for the rib.
- Specify parameters like width and depth.
- Creo will generate the rib based on your profile sketch.
Ribs are crucial for designing robust parts, and Creo's rib features make it easy to add strength where needed.
Editing Features of a Model
In the design process, it's common to encounter the need for feature modifications. Creo provides various tools and options for editing features within a model, allowing you to refine your design as necessary.
Editing Definition or Redefining Features
Redefining a feature means changing its parameters or geometry without deleting and recreating it. Creo allows you to redefine features by selecting them and adjusting their properties. This is a powerful tool for making design changes while preserving the feature's history.
Reordering Features
The order in which features are created can impact the design. Creo lets you reorder features within the model tree, ensuring you have full control over the feature sequence.
Rerouting Features
Rerouting features involves changing their references to different edges, surfaces, or planes. This can be useful when the initial references need to be updated due to design changes or constraints.
Suppressing Features
Suppression allows you to temporarily deactivate features in your model. This can be handy for design exploration, as it lets you assess the impact of a specific feature without permanently deleting it.
Deleting Features
When a feature is no longer needed, you can delete it from the model. However, use caution when deleting features, as it can affect downstream features and dimensions. Always review the consequences of deletion before proceeding.
Modifying Features
In addition to editing features directly, Creo offers various tools for modifying and customizing features:
- Pattern Features: Use the Pattern tool to create arrays of features, such as holes, rounds, and more.
- Mirror Features: The Mirror tool allows you to create symmetrical copies of features.
- Scaling Features: You can scale features to change their size proportionally.
- Editing Sketches: Modify the underlying sketches of features to make changes at the sketch level.
Conclusion
PTC Creo is a powerful software tool for part design, and it provides a wide array of features and options to aid in the construction of parts. Whether you're creating holes, rounds, chamfers, ribs, or making feature modifications, Creo's robust capabilities empower you to design with precision and efficiency. Mastering these features will undoubtedly enhance your ability to create intricate, functional, and visually appealing parts. So, next time you're working on a part design, remember the diverse options that Creo offers to make your job easier and your designs better. Happy modeling!