Expert Strategies for Tackling Machine Design Assignments in Mechanical Engineering
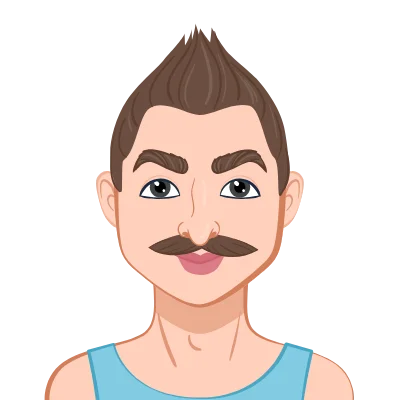
Machine design assignments play a pivotal role in shaping the competence of aspiring mechanical engineers, serving as a critical bridge between theoretical knowledge and practical application. Within the expansive domain of mechanical engineering, machine design assignments stand out as a cornerstone, demanding a comprehensive understanding of engineering principles, creative problem-solving skills, and adept utilization of various tools and software. These assignments not only assess students' grasp of theoretical concepts but also gauge their ability to apply this knowledge to real-world scenarios, mirroring the challenges they will encounter in their future careers.
However, the journey of completing mechanical engineering assignment is fraught with challenges that students often grapple with. One of the primary obstacles is the intricate nature of the assignments themselves. Machine design inherently involves complexities arising from factors like material selection, stress analysis, and the integration of various components. Students frequently find themselves navigating a maze of intricate details, needing to decipher complex instructions and simultaneously balance multiple design considerations. This complexity can be overwhelming, especially for those who are still developing their engineering skills.
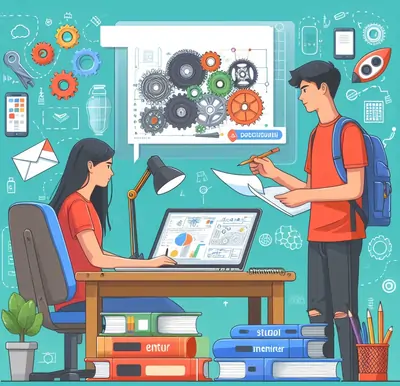
Furthermore, the need for extensive research adds another layer of difficulty. Machine design assignments often require students to delve into a plethora of engineering literature, gather relevant data, and stay abreast of the latest technological advancements. Navigating through this sea of information can be time-consuming and challenging, especially for students who are still in the early stages of their academic journey. The sheer volume of data available, coupled with the necessity to discern the most pertinent information, poses a significant hurdle.
Effective communication and collaboration are additional stumbling blocks. Many machine design assignments are undertaken in a team setting, mirroring the collaborative environment of professional engineering projects. Students, however, may find it challenging to navigate group dynamics, articulate their ideas effectively, and assimilate diverse perspectives. Learning to work harmoniously within a team is a crucial aspect of these assignments and an essential skill for future engineers.
Recognizing the multifaceted challenges that machine design assignments present, it becomes evident that students require effective strategies to navigate this terrain successfully. First and foremost, understanding the assignment's intricacies is paramount. Breaking down complex instructions, identifying key parameters, and establishing a clear understanding of the problem at hand form the foundation for a successful design process. This initial step lays the groundwork for subsequent stages, enabling students to approach the assignment with clarity and purpose.
Research and conceptualization emerge as essential pillars in the machine design process. Encouraging students to delve into relevant literature, explore case studies, and apply theoretical knowledge to practical scenarios fosters a holistic approach. Armed with a solid foundation, students can then proceed to identify and formulate the design problem, setting clear objectives and constraints. Practical application of theoretical concepts becomes more seamless when grounded in a well-researched and conceptualized framework.
In the following sections, we will explore additional strategies, encompassing the use of software tools, time management, peer collaboration, and the avoidance of common pitfalls. These strategies collectively provide a comprehensive roadmap for students to navigate the challenges posed by machine design assignments successfully. By adopting a strategic approach, students can not only overcome the hurdles but also excel in the intricate world of machine design within the realm of mechanical engineering.
Understanding the Assignment:
Thoroughly understanding the assignment requirements in machine design is a foundational step that significantly influences the overall success of the engineering endeavor. The importance lies in the fact that a comprehensive grasp of the assignment specifications serves as the guiding beacon for the entire design process. It ensures that the engineering solution aligns with the intended goals, meets specified constraints, and addresses the intricacies presented by the problem at hand. Without a clear understanding of the requirements, engineers risk veering off course, leading to suboptimal designs that may fall short of expectations.
To effectively understand the assignment, it is imperative to break down complex instructions and identify key components. The intricacies of machine design assignments often lie in the details, with multifaceted instructions requiring careful dissection. One practical tip is to start by deconstructing the assignment prompt into its constituent elements. By isolating individual components, students can discern the specific tasks, constraints, and objectives embedded in the assignment. This process facilitates a focused analysis, allowing for a more nuanced understanding of what is expected.
Additionally, it is beneficial to create a checklist of the assignment requirements. This checklist serves as a tangible roadmap, guiding students through each stipulation and ensuring that no crucial element is overlooked. By systematically addressing each item on the checklist, students can methodically work through the assignment, reinforcing their understanding of the requirements.
Moreover, seeking clarification when faced with ambiguity is a proactive strategy. If certain aspects of the assignment prompt are unclear or open to interpretation, reaching out to instructors or peers for clarification can provide valuable insights. Effective communication with stakeholders ensures that any potential misunderstandings are resolved early in the process, preventing the development of misguided solutions.
Another valuable tip is to consider the broader context of the assignment. Understanding how the machine design fits into the larger framework of mechanical engineering principles and industry standards provides a holistic perspective. This broader awareness aids in identifying the critical components that contribute to the success of the design, fostering a more informed and strategic approach.
In conclusion, the significance of thoroughly understanding machine design assignment requirements cannot be overstated. It forms the bedrock upon which the entire design process rests, influencing the quality and efficacy of the engineering solution. By breaking down complex instructions, creating checklists, seeking clarification when needed, and considering the broader context, students can navigate the intricacies of assignment requirements with confidence and precision. This foundational understanding sets the stage for subsequent stages in the machine design process, ensuring a robust and well-informed approach to engineering challenges.
Research and Conceptualization:
Emphasizing the significance of research in machine design assignments underscores the critical role that informed decision-making plays in the creation of successful engineering solutions. Research serves as the bedrock upon which the entire design process is built, providing the necessary insights, data, and context that inform intelligent decision-making. In the realm of machine design, where intricate details and precision are paramount, a well-researched foundation is essential for generating innovative and effective solutions.
Gathering relevant information is a pivotal aspect of the research phase, and it involves a strategic approach to acquiring knowledge. One effective strategy is to leverage a diverse range of sources, including academic journals, textbooks, industry publications, and online repositories. This multifaceted approach ensures that the information gathered is comprehensive and reflects both theoretical principles and practical applications in the field. Additionally, staying abreast of the latest advancements in machine design technology is crucial, as it enables engineers to incorporate cutting-edge concepts and methodologies into their assignments.
Conceptualizing the design is the natural progression of the research phase, where the synthesized information is transformed into a coherent and structured plan. This involves translating theoretical knowledge into practical applications, aligning the design with the identified objectives and constraints. An essential aspect of this process is to foster creativity and innovation. Encouraging engineers to think beyond conventional solutions and consider novel approaches ensures that the conceptualization phase is not bound by pre-existing paradigms. This mindset fosters the development of designs that push the boundaries of what is currently possible in the realm of machine design.
Guidance in this phase involves encouraging engineers to develop a clear vision of the end product, considering factors such as functionality, efficiency, and manufacturability. Creating conceptual sketches, flow diagrams, and mind maps can aid in visualizing the design and identifying potential challenges early in the process. Additionally, conducting feasibility studies and risk assessments at this stage allows engineers to anticipate and mitigate potential issues, contributing to a more robust and well-informed design concept.
Furthermore, collaboration with peers and mentors can enrich the conceptualization phase by incorporating diverse perspectives and insights. Engaging in discussions and seeking feedback during the early stages of design development can refine ideas, address potential shortcomings, and enhance the overall quality of the conceptualized solution.
In conclusion, the significance of research and conceptualization in machine design assignments cannot be overstated. These phases serve as the intellectual groundwork for the entire design process, laying the foundation for informed decision-making and innovative problem-solving. By emphasizing the value of comprehensive research, guiding engineers in gathering relevant information, and fostering a creative approach to conceptualization, the machine design process becomes a dynamic and intellectually rewarding endeavor, producing solutions that reflect both theoretical rigor and practical applicability.
Problem Identification and Formulation:
The process of identifying and formulating the design problem in machine design assignments is a pivotal stage that requires a systematic approach to ensure a well-defined and purposeful engineering solution. The initial step involves a thorough analysis of the given scenario, which includes understanding the broader context, constraints, and the desired outcome. Engineers must scrutinize the problem statement to identify the specific challenges and opportunities inherent in the design task. This involves breaking down the problem into its constituent elements, discerning the key parameters, and recognizing the interdependencies among various factors.
Defining clear objectives is paramount in this process, as it establishes the overarching goals that the design solution seeks to achieve. Objectives should be specific, measurable, achievable, relevant, and time-bound (SMART). For instance, objectives may include optimizing the efficiency of a mechanical system, minimizing material costs, or enhancing the overall performance of a machine. Clear objectives act as guiding principles, steering the design process toward a targeted and purposeful outcome.
Simultaneously, the identification of constraints is integral to problem formulation. Constraints encompass the limitations and boundaries that impact the design solution, encompassing factors such as budgetary constraints, material availability, time restrictions, and regulatory requirements. Acknowledging these constraints early in the process is crucial, as it allows engineers to navigate the design landscape with a realistic understanding of the challenges they must address. Constraints serve as parameters within which the design must operate, shaping the decision-making process and ensuring the feasibility and viability of the final solution.
Insights into defining clear objectives and constraints lie in effective communication and collaboration. Engaging with stakeholders, including clients, end-users, and project managers, provides valuable perspectives that contribute to the formulation of meaningful objectives and identification of pertinent constraints. Moreover, leveraging interdisciplinary knowledge and seeking input from individuals with diverse expertise can enhance the comprehensiveness and accuracy of the problem definition.
Throughout this process, continuous iteration and refinement are essential. As engineers delve deeper into the intricacies of the design problem, they may uncover nuances that necessitate adjustments to the initially defined objectives and constraints. Flexibility in adapting to new information and insights ensures that the design process remains dynamic and responsive to evolving circumstances.
In conclusion, identifying and formulating the design problem in machine design assignments is a nuanced process that requires analytical rigor and strategic thinking. By breaking down the problem, defining clear objectives using the SMART criteria, acknowledging constraints, and fostering effective communication and collaboration, engineers can navigate the complexities of the design landscape with precision and purpose. This thoughtful approach sets the stage for the subsequent phases of the machine design process, laying the groundwork for innovative and successful engineering solutions.
Utilizing Software Tools:
The role of software tools in machine design is integral, revolutionizing the way engineers conceptualize, analyze, and optimize mechanical systems. These tools not only enhance the efficiency of the design process but also allow for a more accurate and sophisticated approach to solving complex engineering challenges. One primary function of software tools in machine design is facilitating the creation of detailed 3D models. Computer-Aided Design (CAD) software, such as AutoCAD, SolidWorks, and CATIA, enables engineers to digitally visualize and manipulate components, ensuring precise geometry and spatial relationships. This not only expedites the design phase but also provides a platform for iterative testing and refinement.
Simulation software plays a critical role in validating the performance and functionality of machine designs. Finite Element Analysis (FEA) tools, such as ANSYS and Abaqus, allow engineers to assess factors like stress, deformation, and thermal behavior under varying conditions. These simulations provide valuable insights into the structural integrity of components, aiding in the identification and mitigation of potential issues before physical prototypes are produced.
Furthermore, Computational Fluid Dynamics (CFD) software, such as Fluent and OpenFOAM, is instrumental in analyzing fluid flow patterns, heat transfer, and pressure distributions within machine components. This is particularly crucial in the design of systems involving pumps, fans, and heat exchangers, where optimizing fluid dynamics is paramount for efficient operation.
For motion analysis and kinematic studies, mechanisms and systems can be evaluated using tools like MATLAB and Simulink. These software solutions enable engineers to simulate and analyze the dynamic behavior of machine components, predicting how various parts will move and interact under different conditions. This is essential for optimizing performance, minimizing wear and tear, and ensuring the overall reliability of the system.
In academia, teaching and research benefit significantly from software tools that provide a hands-on and interactive learning experience. Software like MATLAB, ANSYS Student, and Fusion 360 is commonly used in educational settings to expose students to real-world engineering challenges and to equip them with the skills needed in industry.
In conclusion, the role of software tools in machine design is transformative, empowering engineers to navigate the intricacies of the design process with unparalleled precision and efficiency. CAD, FEA, CFD, and motion analysis software are indispensable in both industry and academia, shaping the way mechanical systems are conceived, analyzed, and optimized. As technology continues to advance, the integration of sophisticated software tools will likely become even more central to the evolution of machine design, pushing the boundaries of innovation in the field of mechanical engineering.
Practical Application of Theoretical Concepts:
Encouraging students to apply theoretical concepts to real-world scenarios is a cornerstone of effective learning in mechanical engineering, fostering a bridge between academic knowledge and practical problem-solving. Theoretical concepts serve as the foundation upon which innovative and practical solutions are built, and the application of these theories in real-world scenarios is instrumental in developing a deeper understanding of their relevance and impact.
One illustrative example of this application is in the realm of stress analysis. Theoretical concepts related to material properties, structural mechanics, and forces can be applied to real-world scenarios such as designing load-bearing structures. By translating theoretical knowledge into practical applications, students can analyze how different materials respond to various stressors, determine the optimal geometry for structural components, and ensure that safety margins are met in actual engineering projects.
Another pertinent example lies in the field of thermodynamics. Theoretical principles governing heat transfer, energy conversion, and thermodynamic cycles are crucial for designing efficient thermal systems. Students can apply these concepts to develop solutions for real-world challenges, such as designing heat exchangers for improved energy efficiency in HVAC systems or optimizing power cycles in engines for enhanced performance.
The application of control theory is yet another domain where theoretical concepts find practical utility. Understanding feedback systems, stability, and control mechanisms allows students to design control systems for real-world applications, such as creating autonomous vehicles, robotic systems, or industrial automation processes. Theoretical knowledge in control theory becomes the bedrock for developing algorithms and control strategies that can adapt to dynamic and unpredictable environments.
Moreover, fluid mechanics principles provide a rich source of theoretical concepts that can be translated into practical solutions. Whether it's designing efficient piping systems, optimizing aerodynamics for vehicles, or developing irrigation systems, the application of theoretical fluid dynamics concepts is essential for ensuring the desired performance and functionality in diverse engineering scenarios.
To facilitate this translation from theory to practice, hands-on projects, case studies, and internships can play a pivotal role. These experiences provide students with opportunities to apply theoretical knowledge in real-world settings, allowing them to see the direct impact of their academic learning on tangible engineering challenges. Engaging in such practical applications not only reinforces theoretical concepts but also nurtures problem-solving skills and critical thinking, essential attributes for success in the field of mechanical engineering.
In conclusion, encouraging students to apply theoretical concepts to real-world scenarios is paramount for their development as proficient and innovative mechanical engineers. The translation of theoretical knowledge into practical solutions not only reinforces academic learning but also prepares students to tackle the complexities and challenges they will encounter in their professional careers. By fostering this connection between theory and application, educators empower the next generation of engineers to contribute meaningfully to advancements in the field.
Collaboration and Peer Review:
The importance of collaboration and seeking peer feedback in the field of mechanical engineering cannot be overstated, as these practices are integral to fostering innovation, refining designs, and ensuring the success of complex projects. Collaboration brings together diverse perspectives, skills, and insights, creating a dynamic environment where the strengths of each team member can be leveraged to overcome challenges. Moreover, seeking peer feedback serves as a valuable quality control mechanism, allowing engineers to identify blind spots, correct errors, and refine their work through constructive criticism.
Effective communication within a team is a linchpin for successful collaboration. One fundamental tip is to establish clear and transparent channels for communication from the outset. Clearly defined roles, responsibilities, and expectations help streamline workflows and minimize misunderstandings. Utilizing project management tools and communication platforms can enhance real-time information sharing, facilitating seamless collaboration even in geographically dispersed teams.
Active listening is another crucial aspect of effective communication within a team. Encouraging team members to listen attentively to each other's ideas, concerns, and feedback promotes a culture of mutual respect and understanding. This practice not only improves the quality of communication but also fosters an inclusive environment where everyone feels heard and valued.
Constructive feedback mechanisms should be incorporated into the team's workflow. Creating a culture that views feedback as an opportunity for improvement, rather than criticism, promotes continuous learning and refinement of ideas. Peer reviews and regular check-ins provide structured avenues for team members to share insights, identify potential issues, and collectively brainstorm solutions.
Setting clear communication protocols is vital, especially in the context of large and interdisciplinary teams. Clearly defining how information is disseminated, how decisions are communicated, and how updates are shared ensures that everyone is on the same page. Regular team meetings, status reports, and collaborative documentation platforms contribute to this clarity, preventing miscommunication and promoting a cohesive team dynamic.
Moreover, recognizing and appreciating diverse perspectives within the team is essential for effective collaboration. Embracing different viewpoints, experiences, and expertise levels contributes to well-rounded problem-solving and encourages a culture of innovation. This diversity can be harnessed to approach challenges from various angles, leading to more robust and creative solutions.
In conclusion, collaboration and effective communication within a team are cornerstone principles in the field of mechanical engineering. By emphasizing the importance of these practices and offering tips such as establishing clear communication channels, fostering active listening, promoting constructive feedback, and appreciating diversity, engineers can cultivate a collaborative environment that maximizes the potential of each team member and drives success in complex engineering projects.
Conclusion:
In summary, the strategies outlined in this blog—understanding assignment requirements, conducting thorough research and conceptualization, identifying and formulating the design problem, leveraging software tools, and emphasizing collaboration and effective communication—are essential components for successfully tackling machine design assignments in the field of mechanical engineering.
Understanding assignment requirements serves as the foundational step, guiding engineers to decipher complex instructions, break down key components, and grasp the intricacies of the design task. Thorough research and conceptualization enhance the depth of the design process by incorporating a wealth of knowledge and fostering creative problem-solving. Identifying and formulating the design problem ensures that engineers set clear objectives and acknowledge constraints, creating a roadmap for a purposeful and feasible solution.
The role of software tools in machine design cannot be overstated, providing powerful platforms for 3D modeling, simulation, and analysis. Software tools such as CAD, FEA, and CFD empower engineers to visualize, test, and refine designs with precision, streamlining the design process and minimizing the risk of errors.
Furthermore, collaboration and effective communication within a team are cornerstones for success in the engineering landscape. By actively seeking peer feedback, engineers can refine their work, identify blind spots, and ensure the quality of their designs. Effective communication, both within the team and with stakeholders, establishes clear expectations, fosters a culture of innovation, and prevents misunderstandings.
Readers are encouraged to apply these strategies in their own work to enhance their effectiveness in machine design assignments. By approaching assignments with a clear understanding of requirements, conducting thorough research, and leveraging software tools, engineers can optimize their design processes. Formulating the design problem with clear objectives and constraints ensures a purposeful approach, while collaboration and effective communication amplify the collective intelligence of the team.
It is imperative for readers to recognize the interconnectedness of these strategies and view them as a holistic framework. Incorporating these strategies into their workflow empowers engineers to not only meet the challenges posed by machine design assignments but also to excel in the dynamic and innovative field of mechanical engineering. By adopting these key principles, readers can navigate the complexities of machine design with confidence, producing solutions that are not only theoretically sound but also practically viable and impactful in real-world applications.