Understanding Process Dynamics, Operations, and Control in Mechanical Engineering Assignments
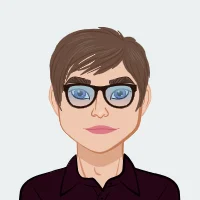
Process dynamics, operations, and control are foundational to the field of mechanical engineering, encompassing a diverse array of applications from aerospace propulsion systems to sustainable energy solutions. These concepts are pivotal for engineers striving to optimize efficiency, reliability, and safety in complex technological systems. In academic settings, assignments centered on process dynamics and control challenge students to not only comprehend theoretical frameworks but also to apply them creatively to solve practical engineering problems. By delving deep into these core principles, this article seeks to equip students with robust strategies and methodologies essential for tackling assignments effectively.
Mechanical engineers are tasked with understanding how systems respond to inputs and disturbances, a skill honed through the study of process dynamics. This field explores the behavior of systems over time, often represented through mathematical models that predict responses to different stimuli. Key to mastering process dynamics is the ability to sketch and interpret first-order step responses, visualizing how systems settle into steady-state conditions based on their time constants and initial conditions.
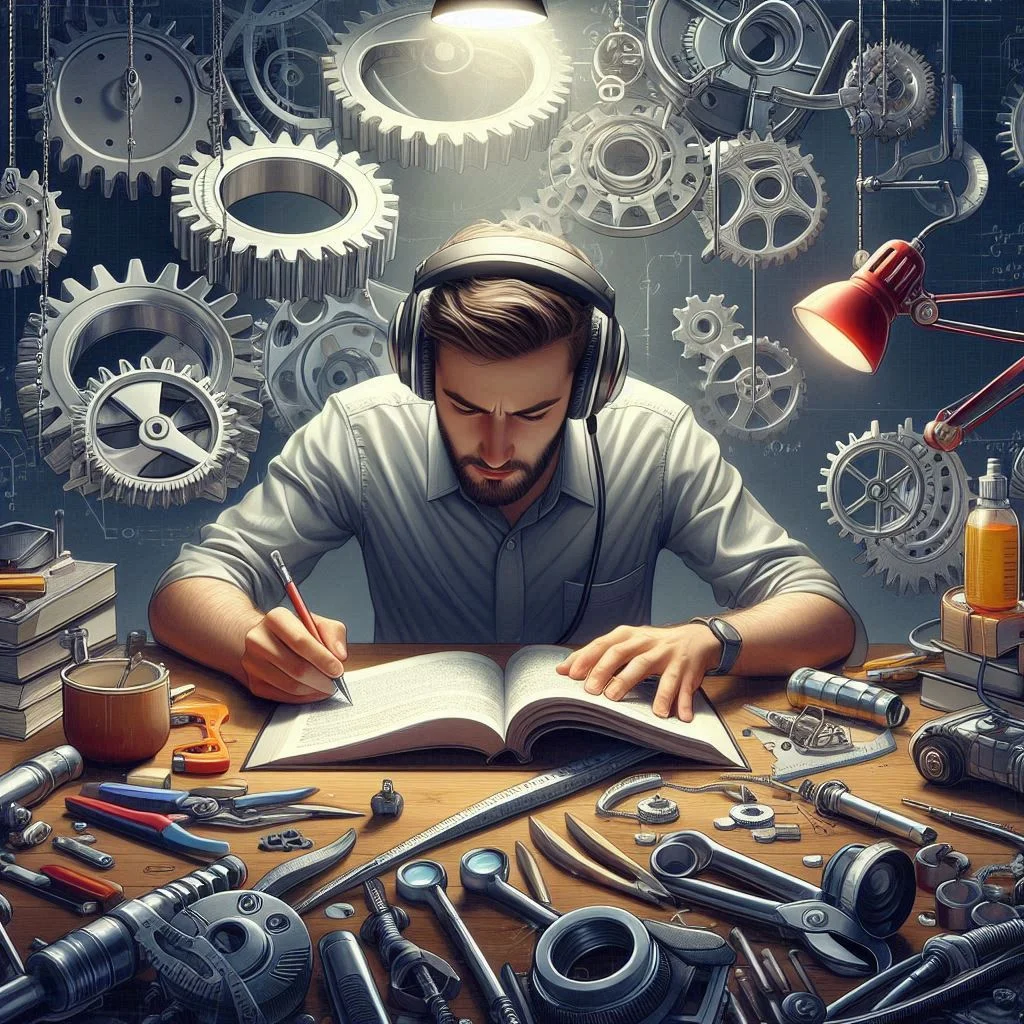
Operations and control complement process dynamics by focusing on the practical aspects of system management. Engineers must not only model system behavior but also implement strategies to regulate and optimize performance. Assignments in this area may involve designing controllers that maintain stability in systems subjected to varying inputs or developing models that predict how system variables, such as liquid levels in tanks, respond to changing conditions.
Practical applications of these concepts abound in industry. For instance, in chemical processing plants, understanding process dynamics is crucial for maintaining consistent product quality and maximizing throughput while minimizing energy consumption. Similarly, in robotics and automation, precise control algorithms ensure that machines perform tasks with accuracy and efficiency.
To excel in assignments related to process dynamics, operations, and control, students should focus on several key strategies. First, a thorough understanding of theoretical principles, such as differential equations and Laplace transforms, provides a solid foundation for modeling dynamic systems. Second, hands-on experience with simulation tools like MATLAB or Simulink allows students to validate theoretical models and explore different control strategies in a virtual environment. Third, critical thinking and problem-solving skills are essential for analyzing complex systems and devising innovative solutions to optimize performance.
In conclusion, mastering process dynamics, operations, and control systems prepares mechanical engineers to drive technological advancement and industry evolution. Embracing these concepts through study and application equips students to confidently complete their mechanical engineering assignments and excel in careers continually pushing innovation and efficiency boundaries.
Understanding First-Order Step Response-
Understanding the first-order step response is fundamental in the study of process dynamics within mechanical engineering. This concept provides engineers with crucial insights into how systems behave in response to sudden changes or inputs, which is essential for designing and optimizing various mechanical systems. By analyzing the step response, engineers can predict how a system will transition from one state to another over time, helping to ensure stability, efficiency, and safety in engineering applications.
In academic and professional settings, mastering the first-order step response involves not only grasping the mathematical principles behind it but also developing practical skills in visualizing and interpreting response curves. Engineers often sketch these responses, marking time constants on the x-axis and the fraction of the steady-state response on the y-axis, to understand how quickly and smoothly a system reaches its new equilibrium after a step input.
Moreover, understanding the first-order step response lays the groundwork for more advanced studies in control theory and system dynamics. It serves as a building block for analyzing higher-order systems and implementing control strategies that regulate and optimize system performance in real-time.
By focusing on the intricacies of the first-order step response, engineers can enhance their ability to design robust systems that meet stringent performance requirements across diverse industries, from automotive engineering to renewable energy. This foundational understanding not only supports academic success in assignments but also prepares engineers to tackle complex challenges in their careers, driving innovation and efficiency in mechanical systems worldwide.
Sketching the Response
Sketching the response of a system, particularly the first-order step response, is a fundamental skill in mechanical engineering. It involves visually representing how a system reacts to a sudden change or input, providing engineers with critical insights into its dynamic behavior over time.
To sketch the response effectively, engineers typically start by identifying key parameters such as the time constant (τ) and the steady-state value. The time constant τ determines how quickly the system approaches its new steady-state condition after the input, while the steady-state value represents the final value the system reaches over time.
On a graph, the x-axis usually represents time, while the y-axis represents the system's output or response. Engineers mark increments on the x-axis corresponding to multiples of the time constant (τ), which helps visualize how quickly the system reaches certain points in time. On the y-axis, they mark off the ordinate as a fraction of the long-term response, illustrating how the system's output approaches its final value over time.
By sketching the response, engineers gain a clearer understanding of the system's transient behavior—how it responds immediately after a change—and its steady-state behavior—how it settles over time. This visual representation not only aids in comprehending theoretical concepts but also assists in practical applications such as designing control systems or troubleshooting operational issues.
Mastering the skill of sketching response curves empowers engineers to predict and optimize system performance, ensuring that mechanical systems operate efficiently and reliably across various industrial applications. It forms the foundation for deeper studies in system dynamics and control theory, enabling engineers to innovate and advance technological solutions in the field of mechanical engineering.
Practicing Modeling Techniques
Practicing modeling techniques is a crucial aspect of mastering process dynamics and control within mechanical engineering. It involves applying theoretical knowledge to create mathematical models that accurately represent the behavior of real-world systems. These models serve as powerful tools for engineers to analyze, predict, and optimize system performance in diverse applications ranging from automotive systems to chemical processes.
In academic settings, practicing modeling techniques often begins with understanding fundamental equations and principles that govern system dynamics. For instance, engineers may start by deriving equations that describe the relationship between inputs, outputs, and system variables such as flow rates, pressures, or temperatures. This process helps in formulating differential equations or transfer functions that capture the dynamics of the system under study.
Moreover, practicing modeling techniques extends beyond mere mathematical derivations. It involves validating and refining models through simulation and experimental data, ensuring that they accurately reflect the behavior observed in real-world scenarios. Simulation tools like MATLAB, Simulink, or computational fluid dynamics (CFD) software play a crucial role in this process, allowing engineers to test different scenarios, analyze sensitivities, and optimize system parameters.
Furthermore, practicing modeling techniques encourages engineers to consider practical constraints and real-world complexities that may affect system behavior. This includes factors such as nonlinearities, delays, and uncertainties, which require advanced modeling approaches such as state-space modeling or stochastic modeling techniques.
By engaging in rigorous practice of modeling techniques, engineers develop the proficiency needed to tackle complex engineering challenges effectively. They become adept at translating theoretical concepts into actionable models that support decision-making, design improvements, and troubleshooting efforts in industry settings. Ultimately, mastering modeling techniques enhances engineers' ability to innovate and optimize mechanical systems, contributing to advancements in technology and engineering solutions worldwide.
Modeling the Overflow Tank:
Modeling the overflow tank involves more than just basic fluid dynamics. Engineers must consider scenarios where the outflow is directly proportional to the liquid level within the tank, which can significantly affect both the composition and overall material balance of the system. This dynamic relationship introduces complexities beyond those found in simple overflow tanks, where outflow is typically constant or determined by factors unrelated to liquid level.
To derive comprehensive balances for both inflow and outflow scenarios, engineers start by formulating equations that account for how changes in liquid level impact the rate at which liquid exits the tank. This approach allows for a more nuanced understanding of how system behavior varies with different operating conditions, such as varying inflow rates or changes in outflow dynamics based on liquid level.
Moreover, discussing how these dynamics differ from those of simpler overflow tanks involves analyzing the implications for system stability, efficiency, and control. Engineers must explore how variations in liquid level affect not only the immediate composition of the tank contents but also the overall stability of the system over time.
Stability Analysis:
Stability analysis in mechanical engineering involves assessing how well a system can maintain its intended operating conditions despite external disturbances or changes in input. In the context of blending tanks and similar systems, stability analysis becomes critical for ensuring reliable and predictable system performance under varying conditions.
Exploring stability concepts, as discussed in Section 3.7 and beyond, requires a thorough examination of both theoretical principles and practical implications. Engineers derive models that account for the dynamic interactions between system variables and external inputs, such as disturbances characterized by sine or step inputs.
By assessing stability to disturbances, engineers can predict how well a system will respond to unexpected changes and adjust control strategies accordingly. This analysis not only validates theoretical stability claims but also highlights practical considerations that may affect system operation in real-world applications.
Incorporating comprehensive stability analyses into modeling practices enhances engineers' ability to design robust systems capable of maintaining desired performance levels across diverse operating conditions. It underscores the importance of rigorous theoretical groundwork in ensuring the reliability and efficiency of mechanical systems in industrial settings.
Applying Theory to Tank Dynamics:
Applying theoretical principles to tank dynamics involves translating abstract concepts into practical solutions that address real-world challenges in mechanical engineering. Tanks, whether for storage, blending, or processing purposes, play a crucial role in various industries such as chemical processing, food production, and wastewater treatment. Understanding and modeling tank dynamics are essential for optimizing efficiency, ensuring safety, and meeting operational requirements.
Understanding System Behavior:
To effectively apply theory to tank dynamics, engineers begin by analyzing the fundamental principles that govern fluid dynamics within tanks. This includes understanding how factors such as inflow rates, outflow rates, tank geometry, and liquid properties influence the behavior of fluids within the tank. Theoretical frameworks such as differential equations and mass balance equations are utilized to model how these variables interact over time.
Modeling Approaches:
Engineers employ various modeling approaches to represent tank dynamics accurately. This includes developing differential equations or state-space models that describe how liquid levels, pressures, and concentrations change in response to inputs and disturbances. Advanced modeling techniques, such as computational fluid dynamics (CFD), may also be used to simulate complex flow patterns and optimize tank design for efficiency and performance.
Practical Applications:
The application of theory to tank dynamics extends beyond theoretical derivations to practical applications in engineering. Engineers use their understanding of tank dynamics to design systems that minimize energy consumption, maximize storage capacity, and ensure uniform mixing of contents. This involves considering factors such as agitation methods, baffling configurations, and control strategies to maintain desired operational conditions.
Case Studies and Analysis:
By examining case studies and real-world examples, engineers gain insights into how theoretical principles translate into actionable solutions. They analyze past projects to identify best practices, troubleshoot potential issues, and refine their approach to modeling tank dynamics for future applications.
Continuous Improvement:
Applying theory to tank dynamics is an iterative process that involves continuous improvement and adaptation to new technologies and industry standards. Engineers stay abreast of advancements in materials, sensors, and control systems to enhance the accuracy and efficiency of tank designs and operations over time.
By applying theory effectively to tank dynamics, engineers can design and optimize systems that meet stringent performance requirements, ensure environmental compliance, and contribute to sustainable development in various industrial sectors. This integration of theoretical knowledge with practical application underscores the critical role of tank dynamics in advancing mechanical engineering solutions globally.
Tips for Success in Mechanical Engineering Assignments:
Mastering mechanical engineering assignments, especially those involving process dynamics, operations, and control, requires a combination of theoretical knowledge, practical skills, and effective problem-solving strategies. Here are some tips to help you succeed:
1. Understand Fundamental Concepts:
Build a solid foundation by thoroughly understanding key concepts such as system dynamics, differential equations, and control theory. This foundational knowledge will support your ability to analyze and solve complex engineering problems.
2. Practice Modeling and Simulation:
Regularly practice creating mathematical models and simulating system behaviors using tools like MATLAB, Simulink, or computational fluid dynamics (CFD) software. Hands-on experience will enhance your ability to predict and optimize system performance.
3. Visualize System Responses:
Develop the skill to sketch and interpret response curves, particularly first-order step responses. Visualizing how systems react to inputs over time will deepen your understanding of dynamic behaviors and help in designing effective control strategies.
4. Apply Theory to Real-World Scenarios:
Bridge the gap between theory and practice by applying theoretical principles to practical engineering problems. Consider real-world constraints and factors that impact system performance, such as environmental conditions and material properties.
5. Emphasize Stability and Control:
Pay special attention to stability analysis and control design. Understand how disturbances, such as sine or step inputs, affect system stability and practice designing controllers that maintain desired system responses.
6. Collaborate and Seek Feedback:
Engage with peers, professors, or industry professionals to discuss assignments, share insights, and seek feedback on your work. Collaboration can provide fresh perspectives and enhance learning outcomes.
7. Stay Organized and Manage Time Effectively:
Break down assignments into manageable tasks, set deadlines for each task, and prioritize based on importance and complexity. Effective time management ensures you stay on track and deliver high-quality work.
8. Review and Reflect:
After completing assignments, take time to review your solutions, reflect on your approach, and identify areas for improvement. Continuous learning and self-reflection are key to mastering challenging engineering concepts.
9. Stay Updated with Industry Trends:
Keep abreast of advancements in mechanical engineering, including new technologies, methodologies, and industry standards. This knowledge will enrich your understanding and help you apply the latest innovations to assignments.
10. Seek Support When Needed:
Don't hesitate to seek assistance from tutoring services, online resources, or academic support centers if you encounter challenges or need clarification on concepts. Asking for help demonstrates proactive learning and commitment to academic excellence.
By following these tips, you can enhance your performance in mechanical engineering assignments focused on process dynamics, operations, and control. Developing a strong theoretical foundation, practicing practical skills, and adopting effective problem-solving strategies will empower you to excel in your studies and future career endeavors.
Conclusion
In conclusion, mastering process dynamics, operations, and control is essential for aspiring mechanical engineers seeking to excel in both academic assignments and practical applications. These foundational concepts not only form the backbone of mechanical engineering education but also play a crucial role in designing, analyzing, and optimizing complex systems across various industries.
By delving into topics such as first-order step responses, modeling techniques for tanks and other systems, stability analysis, and practical applications, engineers develop the skills necessary to tackle real-world engineering challenges effectively. The ability to apply theoretical knowledge to practical scenarios, visualize and interpret system responses, and design robust control strategies are key attributes that distinguish successful engineers.
Furthermore, success in mechanical engineering assignments requires continuous learning, hands-on practice with simulation tools, collaboration with peers and mentors, and a commitment to staying updated with industry trends and advancements. These elements collectively contribute to a comprehensive understanding of mechanical systems dynamics and prepare engineers to innovate and contribute meaningfully to technological advancements and societal needs.
As you embark on your journey in mechanical engineering, remember that each assignment presents an opportunity to deepen your knowledge, refine your skills, and prepare for future professional challenges. By embracing these principles and applying them rigorously, you will not only excel academically but also lay a strong foundation for a successful career in mechanical engineering, driving innovation and progress in the field.