The Role of Ansys in Stress Analysis: An Academic Perspective
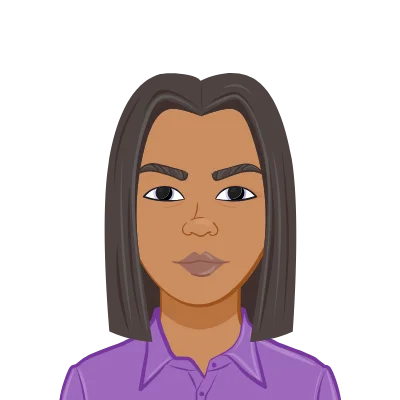
Stress analysis stands as a cornerstone in the field of electrical engineering, playing a pivotal role in ensuring the reliability, safety, and optimal performance of various electrical components and systems. At its core, stress analysis involves the assessment of how forces and loads affect materials, structures, and devices within the realm of electrical engineering. As electrical systems continue to advance in complexity and sophistication, the need for rigorous stress analysis becomes increasingly paramount. The intricate interplay between different components and the dynamic operational conditions to which electrical systems are subjected necessitates a deep understanding of how stress impacts materials and structures. Whether it's the structural integrity of a power transmission tower, the durability of electronic components in harsh environments, or the performance of microelectronic devices under thermal stress, a comprehensive grasp of stress analysis is indispensable.
In electrical engineering, the consequences of overlooking stress analysis can be profound. Failure to accurately predict and manage stresses within a system can result in a cascade of issues ranging from decreased reliability and efficiency to catastrophic failures. For instance, in power systems, where large forces and extreme conditions are commonplace, inadequate stress analysis could lead to structural failures in components like insulators or transmission lines, jeopardizing the stability of the entire electrical grid. Similarly, in electronic circuits and microelectronics, the impact of thermal stresses on the performance and lifespan of devices cannot be understated. Neglecting stress analysis in the design phase could result in premature failures, compromising the functionality of electronic systems critical to various industries.
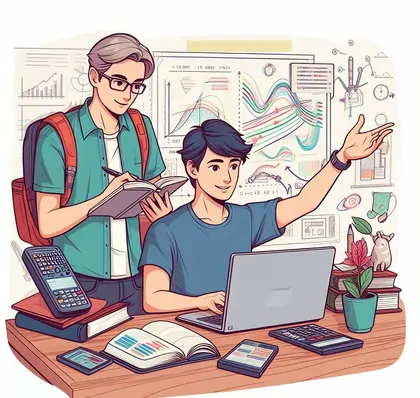
Moreover, stress analysis plays a vital role in guiding the design and optimization process in electrical engineering. Engineers must grapple with the challenge of developing systems that not only meet performance specifications but also withstand the myriad of mechanical, thermal, and environmental stresses they may encounter during their operational life. Through advanced simulation tools like Ansys, engineers can model and analyze these stresses in a virtual environment, allowing for iterative design improvements without the need for costly and time-consuming physical prototypes. This iterative process enables engineers to fine-tune designs, identify potential weaknesses, and optimize structures to enhance overall system performance and reliability. If you need assistance to complete your Ansys assignment, these advanced simulation tools can significantly aid in achieving accurate and efficient results.
In the academic sphere, stress analysis serves as a fundamental component of the electrical engineering curriculum. Students are introduced to the theoretical foundations and practical applications of stress analysis as they delve into coursework and projects. This exposure is not merely an academic exercise but a preparation for the real-world challenges that engineers face in industry. By understanding the principles of stress analysis, students are equipped with the skills necessary to address the complexities of modern electrical systems, contributing to innovation and the advancement of the field.
Furthermore, as technology continues to evolve, the role of stress analysis becomes even more nuanced. The miniaturization of electronic components, the development of smart materials, and the integration of electronics into diverse applications demand a deeper understanding of how stress influences the behavior of materials at the micro and nanoscales. Consequently, the academic exploration of stress analysis extends beyond traditional boundaries, encompassing emerging technologies and interdisciplinary collaborations that push the boundaries of electrical engineering.
In conclusion, stress analysis stands as a linchpin in the edifice of electrical engineering, serving as both a safeguard against potential failures and a catalyst for innovation. Its importance resonates throughout the lifecycle of electrical systems, from the conceptualization and design stages to the operation and maintenance of these systems in real-world conditions. As the field continues to advance, stress analysis remains an indomitable force, guiding engineers and students alike toward a future where electrical systems not only meet functional requirements but also withstand the rigors of an ever-evolving technological landscape.
Ansys is a powerful simulation software
ANSYS, a veritable titan in the realm of engineering simulation software, stands as an indispensable tool for engineers and researchers across a multitude of disciplines. Renowned for its unparalleled capabilities in numerical simulation, ANSYS provides a comprehensive suite of tools for simulating and analyzing a diverse array of physical phenomena, ranging from structural mechanics and fluid dynamics to electromagnetics and thermal analysis. Originally developed in the 1970s, ANSYS has evolved into a sophisticated and versatile platform that empowers engineers to virtually prototype and test their designs before physical prototypes are manufactured. The software's strength lies not only in its ability to accurately model complex engineering problems but also in its user-friendly interface, making it accessible to both seasoned professionals and students alike.
At its core, ANSYS employs the finite element method (FEM) to discretize complex physical systems into smaller, more manageable elements. This numerical approach enables the software to simulate and analyze the behavior of structures and systems under various conditions, providing invaluable insights into their performance. The finite element method is particularly powerful as it allows for the representation of intricate geometries and material properties, making it well-suited for the diverse range of challenges encountered in engineering applications.
One of ANSYS's standout features is its versatility across different engineering domains. In structural analysis, ANSYS excels in predicting the behavior of components and systems under various loading conditions. Engineers can simulate the response of structures to forces, thermal effects, and other environmental factors, allowing for the optimization of designs to meet performance and safety criteria. In fluid dynamics, ANSYS provides a robust platform for analyzing the flow of liquids and gases, aiding in the design of efficient and aerodynamic structures. The software's electromagnetic capabilities enable engineers to model and analyze the behavior of electromagnetic fields, making it an invaluable tool for the design of electrical components and systems.
Furthermore, ANSYS is renowned for its thermal analysis capabilities, allowing engineers to simulate heat transfer and thermal stresses within a system. This is critical in applications where temperature variations can impact the performance and reliability of components, such as in electronic devices or industrial machinery. The software's ability to seamlessly integrate these diverse analyses into a unified platform sets it apart, providing engineers with a holistic understanding of how different physical phenomena interact within a given system.
ANYSYS's pre-processing capabilities are another facet that contributes to its acclaim. The software provides a robust environment for users to create detailed and accurate models of their designs, complete with complex geometries and material properties. The user-friendly interface facilitates the meshing process, where the model is discretized into smaller elements, a crucial step for accurate simulations. Additionally, ANSYS offers a wide range of material models, allowing users to simulate the behavior of materials under various conditions and loading scenarios.
The post-processing capabilities of ANSYS are equally impressive. Engineers can visualize and interpret simulation results through a variety of graphical representations, aiding in the identification of critical areas, potential failure points, or areas for design improvement. ANSYS also allows for parametric studies, enabling users to explore how changes in design parameters affect the overall performance of the system. This capability is particularly valuable in the design optimization process, where engineers seek to refine and enhance their designs iteratively.
Beyond its technical capabilities, the widespread adoption of ANSYS in academia further underscores its significance. Many educational institutions integrate ANSYS into their engineering curricula, exposing students to the software's intricacies and empowering the next generation of engineers with essential simulation skills. This educational emphasis on ANSYS reflects its prominence in industry, where proficiency in simulation tools is increasingly becoming a prerequisite for engineering roles.
The continuous evolution of ANSYS is evident in its commitment to staying at the forefront of technological advancements. The software undergoes regular updates and enhancements, incorporating the latest methodologies and algorithms to address emerging engineering challenges. This commitment to innovation ensures that ANSYS remains at the vanguard of simulation software, providing engineers with the tools they need to tackle the complexities of modern design and analysis.
In conclusion, ANSYS stands as a paragon of engineering simulation software, wielding a profound influence on the way engineers conceptualize, design, and validate their creations. Its robust capabilities, versatility across engineering domains, user-friendly interface, and educational significance collectively position ANSYS as an indispensable asset in the engineer's toolkit. As the landscape of engineering continues to evolve, ANSYS's legacy persists, driving innovation and serving as a stalwart companion for those navigating the intricacies of virtual prototyping and analysis.
Fundamentals of stress analysis in electrical engineering
Stress analysis in electrical engineering encompasses a set of fundamental principles aimed at understanding and predicting the mechanical behavior of materials and structures under various loads and conditions. At its core, stress analysis involves the assessment of forces and stresses within electrical components and systems, ensuring that they can withstand the mechanical demands imposed during operation. The fundamental concepts revolve around key parameters such as force, stress, strain, and material properties.
Force is a fundamental aspect of stress analysis, representing the action applied to a particular object or structure. In electrical engineering, forces can arise from various sources such as mechanical loads, thermal expansion, or electromagnetic interactions. Understanding the magnitude, direction, and distribution of these forces is crucial for predicting how a component or system will respond under different conditions.
Stress is the measure of internal resistance within a material to deformation caused by external forces. It is a critical parameter in stress analysis as it indicates how materials react to applied loads. Stress can manifest in different forms, including tensile stress (stretching or pulling), compressive stress (squeezing or pushing), and shear stress (sliding or tearing). The distribution of stress within a material is essential for evaluating its structural integrity and durability.
Strain is the measure of deformation experienced by a material under stress. It quantifies the change in shape or size of a material due to applied forces. Strain is typically expressed as a ratio and is instrumental in understanding how materials respond to external loads. The relationship between stress and strain is characterized by material properties such as Young's Modulus, which describes the stiffness or rigidity of a material.
Material properties play a pivotal role in stress analysis, influencing how materials deform and respond to applied forces. Electrical components and systems often involve a variety of materials with different properties, including metals, polymers, ceramics, and composites. Each material exhibits unique characteristics under stress, such as elasticity, plasticity, and ductility, which must be considered in the analysis to ensure the accuracy of predictions.
Stress analysis also involves the study of the mechanical behavior of structures and components under different loading conditions. Electrical systems experience a diverse range of loads, including static loads (constant forces or moments), dynamic loads (varying forces over time), and thermal loads (due to temperature changes). Understanding how these loads interact with the geometry and material properties of electrical components is essential for designing reliable and robust systems.
Finite element analysis (FEA) is a widely used technique in stress analysis that discretizes complex structures into smaller, more manageable elements. This numerical method allows engineers to simulate the behavior of structures under various conditions, providing detailed insights into stress distribution and deformation. FEA is particularly valuable in electrical engineering for modeling and analyzing the structural integrity of components like circuit boards, housings, and support structures.
In electrical systems, thermal stress analysis is of paramount importance. The heating and cooling cycles that electrical components undergo can lead to thermal expansion and contraction, inducing stresses that may affect the performance and longevity of the system. Understanding how materials respond to temperature changes and predicting thermal stresses is crucial for designing components that can withstand the thermal conditions encountered in real-world applications.
Furthermore, stress concentrations in specific regions of electrical components, such as joints, connectors, and interfaces, demand special attention. These localized areas can experience higher stress levels than the surrounding regions, potentially leading to fatigue and failure. Identifying and mitigating stress concentrations is a key aspect of stress analysis to ensure the reliability and durability of electrical systems.
In summary, the fundamentals of stress analysis in electrical engineering revolve around comprehending the interplay between forces, stresses, strains, and material properties within components and systems. The application of these principles enables engineers to predict how electrical structures will behave under different loads and conditions, facilitating the design of robust and reliable systems. Whether through analytical methods or advanced numerical simulations like finite element analysis, stress analysis is an integral part of the design and optimization process in electrical engineering, ensuring that components can withstand the mechanical challenges posed by real-world applications.
Applications in Electrical Engineering
ANSYS, a versatile and powerful simulation software, finds extensive real-world applications in the realm of electrical engineering, playing a transformative role in the design, analysis, and optimization of a myriad of electrical components and systems. In the domain of power systems, ANSYS is instrumental in simulating and analyzing the structural and thermal behavior of critical components such as power transmission towers and insulators. Engineers leverage the software to model the impact of wind loads, dynamic forces, and thermal cycling on these structures, ensuring their integrity and reliability under various operating conditions. This application is particularly crucial for optimizing the design of power transmission infrastructure, where the ability to predict and mitigate stress-related issues is paramount for maintaining the stability of the electrical grid.
Electronic devices, a ubiquitous part of modern life, undergo rigorous stress analysis using ANSYS to ensure their performance and longevity. In the design of printed circuit boards (PCBs), ANSYS aids in simulating the mechanical and thermal stresses that arise from factors like component placement, soldering, and temperature variations during operation. By virtually testing different configurations and materials, engineers can optimize the PCB design to enhance structural integrity, thermal management, and overall reliability. ANSYS's ability to model and analyze the thermal behavior of electronic components is particularly valuable in predicting potential hotspots and ensuring that devices operate within safe temperature ranges.
In the aerospace industry, ANSYS plays a crucial role in the design and analysis of avionics components and systems. The software is used to simulate the impact of aerodynamic forces, vibrations, and thermal conditions on electrical systems embedded within aircraft. This includes the stress analysis of components like antennas, sensors, and wiring harnesses, ensuring their resilience to the demanding conditions of flight. Engineers utilize ANSYS to optimize the design of these electrical systems for weight, durability, and performance, contributing to the safety and efficiency of aviation technology.
The automotive sector leverages ANSYS for stress analysis in the design of electric vehicles (EVs) and their associated components. ANSYS is employed to model the structural integrity of the vehicle's chassis, battery housing, and electrical systems under dynamic loads, including road-induced vibrations and acceleration forces. This enables engineers to identify potential weaknesses and optimize the design for safety and performance. Additionally, ANSYS's thermal analysis capabilities are crucial for predicting and managing the heat generated by electric drivetrains and batteries, ensuring the reliability and efficiency of EVs in real-world driving conditions.
In the field of renewable energy, ANSYS is employed in the stress analysis of components within solar photovoltaic (PV) systems and wind turbines. Solar panels are subjected to environmental forces such as wind and snow loads, and ANSYS helps engineers' model and analyze the structural response of PV modules and support structures. Similarly, in wind energy, ANSYS aids in simulating the mechanical stresses on turbine components, including blades, towers, and drivetrains, under varying wind conditions. This stress analysis ensures the robustness of renewable energy infrastructure, contributing to the sustainability and reliability of clean energy technologies.
The telecommunications industry benefits significantly from ANSYS in the design and analysis of antennas and communication systems. Engineers use the software to model the structural and electromagnetic behavior of antennas, considering factors like wind loading, thermal effects, and electromagnetic interference. This ensures the optimal performance and durability of antennas in diverse environmental conditions. Moreover, ANSYS facilitates the stress analysis of communication towers and supporting structures, helping engineers design resilient infrastructure for the deployment of wireless networks.
In the realm of microelectronics and semiconductor manufacturing, ANSYS is a critical tool for stress analysis at the nanoscale. As electronic devices continue to shrink in size, the mechanical stresses induced during manufacturing processes become increasingly significant. ANSYS enables engineers to model and analyze the impact of fabrication techniques, such as photolithography and etching, on the structural integrity of microelectronic components. This level of precision in stress analysis is vital for ensuring the reliability and functionality of integrated circuits, microprocessors, and other semiconductor devices.
The oil and gas industry leverages ANSYS for stress analysis in electrical systems associated with exploration, drilling, and extraction processes. Subsea cables and connectors, crucial for transmitting power and data in offshore environments, undergo rigorous simulation using ANSYS to assess their resilience to underwater conditions, including pressure, temperature, and mechanical stresses. This application ensures the reliability of electrical systems in challenging and corrosive environments, contributing to the efficiency and safety of offshore operations.
In conclusion, the real-world applications of ANSYS in electrical engineering projects span a diverse array of industries and technologies. From power systems and electronics to aerospace, automotive, renewable energy, telecommunications, and semiconductor manufacturing, ANSYS serves as an indispensable tool for engineers seeking to understand and optimize the mechanical behavior of electrical components and systems. By providing a virtual environment for comprehensive stress analysis, ANSYS accelerates the design process, reduces the need for physical prototypes, and ultimately contributes to the development of robust, reliable, and innovative electrical engineering solutions across various sectors.
Conclusion
In conclusion, delving into "The Role of Ansys in Stress Analysis: An Academic Perspective" illuminates the transformative impact this powerful simulation software has had on the landscape of academic exploration and practical applications within the realm of electrical engineering. As we navigate through the intricacies of stress analysis, it becomes abundantly clear that Ansys has emerged as a linchpin, bridging theoretical understanding with real-world implementation.
One of the overarching themes that permeates this exploration is the depth of insight that Ansys provides into the mechanical behavior of materials and structures. In the academic arena, this tool has become an invaluable companion for students and researchers alike, offering a virtual laboratory where theories can be tested, hypotheses validated, and innovations germinated. The ability to simulate and analyze stress under various conditions, whether static or dynamic, thermal or mechanical, equips academic institutions with a tool that transcends traditional boundaries, fostering a holistic understanding of material response and structural integrity.
The adaptability and versatility of Ansys are evident in its applications across diverse academic scenarios. From the undergraduate classroom to advanced research endeavors, this simulation software seamlessly integrates with curricula, enabling students to gain hands-on experience in stress analysis. The academic perspective of Ansys extends beyond mere theoretical learning, empowering students to translate their knowledge into practical skills that are increasingly relevant in the professional landscape. By embracing Ansys in the academic journey, students are not only equipped with a tool for understanding the fundamentals of stress analysis but are also prepared for the complex challenges they will encounter in their engineering careers.
The significance of Ansys extends beyond the confines of academic institutions to the broader landscape of research and development. In the academic research sphere, Ansys serves as a catalyst for innovation, facilitating in-depth investigations into complex engineering problems. Whether unraveling the mysteries of microelectronic device behavior, optimizing the structural integrity of power transmission infrastructure, or exploring the thermal dynamics of renewable energy systems, Ansys provides researchers with a powerful and reliable platform to push the boundaries of knowledge. The academic community, with Ansys as its ally, becomes a crucible of ideas and discoveries, nurturing the next generation of engineers and contributing to the evolution of the field.
Moreover, the seamless integration of Ansys into academic settings underscores its commitment to preparing students for the demands of the professional world. As industry standards evolve, the need for engineers adept in simulation tools becomes increasingly pronounced. Ansys, with its widespread usage in academia, ensures that graduates enter the workforce with not only a theoretical foundation but also a practical proficiency in stress analysis. This symbiotic relationship between academic institutions and industry tools like Ansys fosters a continuous loop of innovation, where insights gained from real-world applications inform academic exploration, and academic insights, in turn, shape the future trajectory of industry practices.
Ansys's role in stress analysis is not confined to mere prediction and analysis; it is a key enabler of the design optimization process. The ability to iterate through designs, test hypotheses, and refine models in a virtual environment accelerates the product development lifecycle. In an academic context, this translates to more efficient research timelines and a deeper understanding of the implications of design choices. For students engaged in academic projects or research endeavors, Ansys becomes a trusted companion, guiding them through the intricacies of design optimization and instilling a mindset focused on robustness and efficiency.
Looking ahead, the academic perspective on the role of Ansys in stress analysis underscores the software's evolving significance in shaping the future of engineering education and research. As the complexities of electrical engineering challenges grow, the demand for proficient users of simulation tools like Ansys is poised to escalate. The academic community, in partnership with Ansys, stands at the forefront of cultivating the skills and knowledge required to address these challenges. The software's continuous evolution, incorporating advanced methodologies and features, ensures that academic institutions remain at the cutting edge of engineering exploration.
In the grand tapestry of academic pursuits, Ansys emerges as a thread that weaves together theoretical understanding, practical application, and future innovation. Its role in stress analysis is not just a technical one; it's a transformative force shaping the educational experiences of aspiring engineers and researchers. The academic perspective on Ansys is a testament to its enduring impact on the way we comprehend, analyze, and engineer the world of electrical systems. As we navigate the ever-expanding horizons of technology and innovation, Ansys stands as a beacon, guiding academia and industry alike toward a future where the understanding of stress and its implications is not just a theoretical exercise but a dynamic and integral part of the engineering journey.