Effective Approaches to Solving Manufacturing Systems Assignments
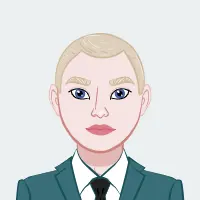
Navigating assignments in manufacturing systems can be challenging, but with the right approach, you can effectively solve complex problems and gain a deeper understanding of the subject. These assignments often involve intricate details and require a solid grasp of various concepts related to manufacturing processes, statistical models, and optimization techniques. By adopting a systematic and analytical approach, you can break down complex problems into manageable parts and address them step-by-step. It is crucial to meticulously analyze the problem statement, identify key information, and apply the appropriate mathematical and engineering principles. By doing so, you ensure that each aspect of the problem is thoroughly understood and accurately addressed. Additionally, practicing these strategies not only helps in completing your mechanical engineering assignments efficiently but also equips you with valuable problem-solving skills that are essential in the field of manufacturing systems. Here are some strategies and tips to help you tackle these types of assignments efficiently, ensuring that you not only complete your tasks accurately but also enhance your overall comprehension of manufacturing systems.
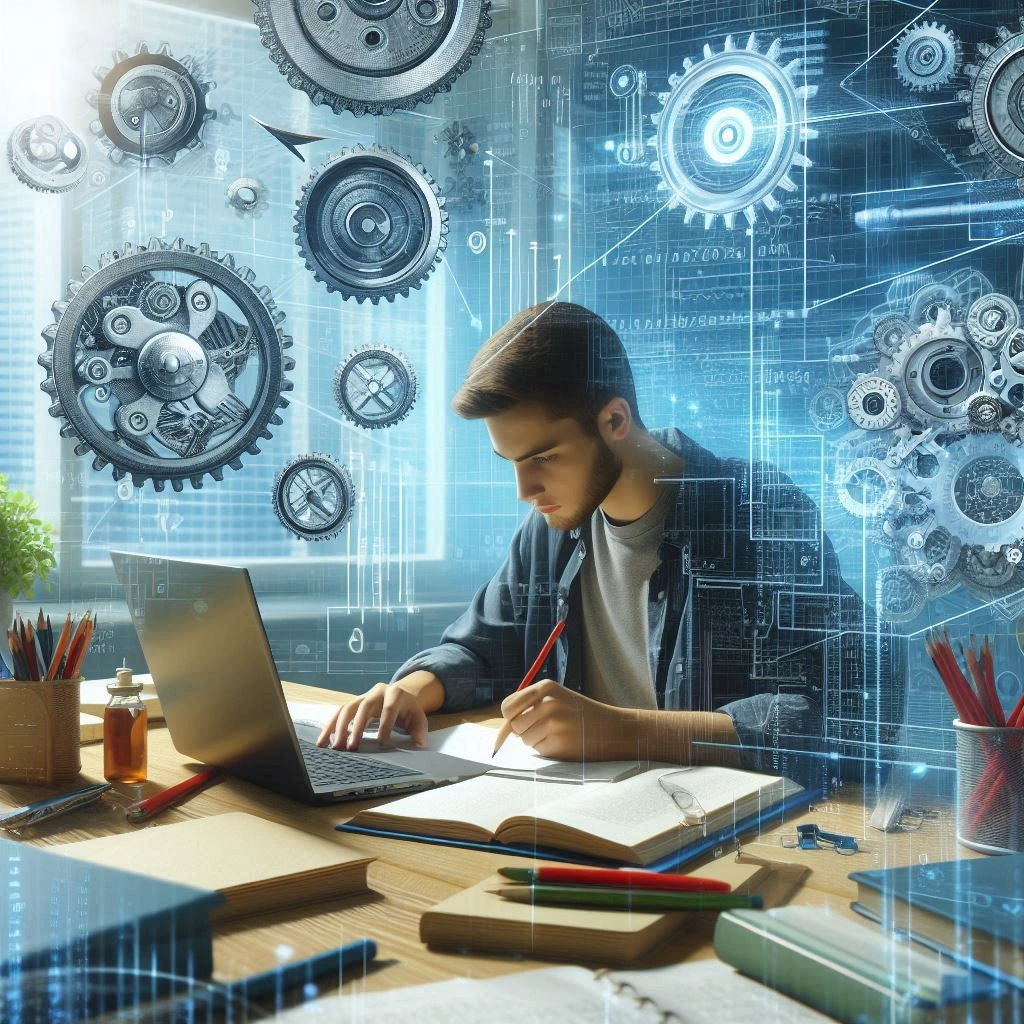
Understand the Problem Statement
The first and most crucial step in tackling any assignment in manufacturing systems is to thoroughly read and understand the problem statement. This involves more than just a cursory glance; it requires a deep dive into the details provided. Identify and highlight key information, such as the specific processes involved, the type of manufacturing system being discussed, and any numerical data related to rates, times, or costs. Understanding these elements is vital because they form the foundation of your analysis and solutions.
For instance, consider a problem involving Automated Guided Vehicles (AGVs) in the semiconductor industry. You need to recognize several critical pieces of information:
- AGV Breakdown Rate: Understand that breakdowns occur randomly and are characterized by a Poisson process. This implies a certain statistical regularity to the occurrences which can be quantified and predicted.
- Repair Time: Note that the repair time follows a negative exponential distribution. This indicates that the probability of a repair taking a certain amount of time decreases exponentially as the time increases.
- Costs: Grasp the dual costs involved – the cost of the repair crew and the cost associated with the downtime of an AGV. These costs must be carefully balanced to minimize total expenses.
Additionally, pay attention to any assumptions or constraints specified in the problem statement. These could include conditions like steady-state operations, buffer capacities, or specific service protocols. Clarifying these elements early on will guide your approach and ensure that your solutions are relevant and accurate.
Taking the time to thoroughly understand the problem statement not only helps in accurately defining the scope of the problem but also prevents misinterpretation that could lead to incorrect solutions. This foundational step sets the stage for effective problem-solving and a deeper understanding of the manufacturing systems at hand.
Break Down the Problem
Once you have a clear understanding of the problem statement, the next step is to break down the problem into smaller, manageable parts. This approach helps in systematically addressing each component and ensures that no aspect of the problem is overlooked. Here’s how to effectively break down a problem:
1. Identify Sub-Problems: Divide the main problem into sub-problems or tasks. Each sub-problem should be a specific part of the overall problem that can be analyzed independently. For example, in an AGV repair service problem, you might identify sub-problems such as determining the service rate, calculating repair costs, and analyzing the downtime costs.
Example:
AGV Repair Service Crew Problem:
- Service Rate Analysis: Determine how the service rate is influenced by the size of the repair crew. This could involve understanding the relationship between crew size and repair efficiency.
- Cost Calculation: Calculate both the fixed costs (repair crew wages) and variable costs (production losses due to downtime).
- Optimization: Combine the above analyses to find the optimal crew size that minimizes total costs.
2. Develop Models and Formulas: For each sub-problem, develop the necessary mathematical models or formulas. This might involve statistical models, optimization techniques, or queuing theory, depending on the problem’s requirements.
Example:
Service Rate Models:
- If the service rate is proportional to the crew size, use the formula μ=k×crew size\mu = k \times \text{crew size}μ=k×crew size.
- If the service rate is proportional to the square root of the crew size, use μ=k×crew size\mu = k \times \sqrt{\text{crew size}}μ=k×crew size.
Cost Calculation Formulas:
- Total cost =Crew cost+Downtime cost= \text{Crew cost} + \text{Downtime cost}=Crew cost+Downtime cost.
- Crew cost =Crew size×Cost per worker per hour= \text{Crew size} \times \text{Cost per worker per hour}=Crew size×Cost per worker per hour.
- Downtime cost =Downtime hours×Cost per hour of downtime= \text{Downtime hours} \times \text{Cost per hour of downtime}=Downtime hours×Cost per hour of downtime.
3. Perform Step-by-Step Analysis: Tackle each sub-problem one at a time. Start with the simplest calculations or models and gradually move to more complex analyses. Ensure that each step logically follows from the previous one and that you keep track of all assumptions and intermediate results.
Example:
- Calculate the service rate for different crew sizes.
- Compute the corresponding repair and downtime costs.
- Analyze the total cost for varying crew sizes to find the minimum.
4. Integrate Results: Once you have solved the sub-problems, integrate the results to form a comprehensive solution to the original problem. Ensure that all parts fit together logically and coherently.
Example:
- Summarize the optimal crew size, service rate, and associated costs.
- Validate that the chosen solution minimizes the total cost effectively.
5. Check for Consistency and Accuracy: Review your work to ensure consistency and accuracy. Verify that each sub-problem has been addressed correctly and that the combined results make sense in the context of the entire problem.
Breaking down the problem in this structured manner not only makes complex assignments more manageable but also enhances your understanding of each component, leading to more accurate and effective solutions.
Use Appropriate Models and Formulas
In tackling assignments in manufacturing systems, applying suitable mathematical models and formulas is crucial for accurate analysis and problem-solving. Here’s how to effectively use them:
1. Identify Relevant Models: Depending on the nature of the problem, identify the appropriate mathematical models or frameworks that best fit the scenario. Common models in manufacturing systems include:
- Poisson Process: Used to model the arrival of events over time, such as breakdowns in machinery or arrival of parts.
- Exponential Distribution: Often applied to model the time between consecutive events in a Poisson process, such as repair times or service times.
- Queuing Theory: Utilized to analyze waiting lines and queuing systems, relevant when considering buffer capacities or waiting times for service.
- Markov Chains: Useful for analyzing systems where transitions between states are probabilistic and memoryless, such as in evaluating steady-state conditions.
2. Formulate the Problem: Once the model is identified, formulate the problem using appropriate mathematical expressions and relationships. Ensure that all variables and parameters are clearly defined and understood.
Example Formulations:
- For AGV repair crew sizing:
- Service rate proportional to crew size: μ=k×crew size\mu = k \times \text{crew size}μ=k×crew size
- Repair time distribution: T∼Exponential(μ)T \sim \text{Exponential}(\mu)T∼Exponential(μ)
- For milling machine queueing:
- Arrival rate of parts: λ\lambdaλ
- Service time distribution: T∼Exponential(μ)T \sim \text{Exponential}(\mu)T∼Exponential(μ)
3. Apply Formulas Correctly: Use the formulated models and formulas to perform calculations or simulations relevant to the problem at hand. Ensure that units are consistent and that assumptions made align with the problem’s requirements.
Example Applications:
- Calculate the expected downtime costs based on repair times and crew size.
- Determine the optimal buffer size to achieve desired service levels in a milling machine scenario.
- Solve balance equations in Markov chains to find steady-state probabilities of system states.
4. Interpret Results: After applying the models and formulas, interpret the results in the context of the problem. Discuss the implications of findings and relate them back to the initial problem statement and objectives.
Example Interpretations:
- Discuss how changes in crew size affect overall costs and service efficiency.
- Analyze how varying arrival rates or service times impact system performance metrics like throughput or waiting times.
5. Validate and Refine: Validate the results obtained from applying models and formulas through sensitivity analyses or comparisons with alternative approaches if applicable. Refine calculations as necessary to ensure robustness and accuracy.
By leveraging appropriate models and formulas, you can effectively analyze complex manufacturing systems problems, derive meaningful insights, and propose informed solutions. This approach not only enhances your understanding of theoretical concepts but also equips you with practical skills applicable across various real-world scenarios in manufacturing and operations management.
Perform Calculations and Analysis
Once you have formulated the problem using appropriate models and identified key variables, the next crucial step is to perform calculations and conduct thorough analysis. This process involves applying the formulated models and mathematical techniques to derive quantitative results and draw meaningful conclusions. Here’s how to effectively perform calculations and analysis in manufacturing systems assignments:
1. Execute Mathematical Formulas: Utilize the mathematical models and formulas identified earlier to perform necessary calculations. Ensure that you accurately input all relevant parameters and variables into the equations.
Example Calculations:
- Calculate the expected service rate based on crew size and repair time distributions.
- Compute total costs including repair crew expenses and downtime costs per hour.
2. Numerical Analysis: For problems involving probabilistic models or queuing theory, conduct numerical simulations or analyses to estimate system performance metrics.
Example Numerical Analyses:
- Simulate the behavior of a queuing system to determine average queue lengths or waiting times.
- Use software tools or programming languages (e.g., MATLAB, Python) to simulate Markov chains and calculate steady-state probabilities.
3. Sensitivity Analysis: Assess the sensitivity of your results to changes in key parameters or assumptions. This helps in understanding the robustness of your solutions and identifying critical factors influencing system performance.
Example Sensitivity Analyses:
- Evaluate how varying repair crew costs or downtime penalties affect the optimal crew size.
- Determine the impact of changes in arrival rates or service times on system throughput or utilization.
4. Interpret Results: Once calculations are completed, interpret the numerical results in the context of the problem statement and objectives. Discuss the implications of findings and relate them back to real-world implications or theoretical expectations.
Example Interpretations:
- Discuss how optimal crew size minimizes total costs and maximizes system efficiency.
- Analyze trade-offs between buffer capacities and waiting times in manufacturing processes.
5. Validate Findings: Validate the accuracy and reliability of your calculations through cross-checks, comparisons with alternative methods, or sensitivity analyses. Ensure that results align with theoretical expectations and practical constraints.
6. Report and Communicate: Present your calculations and analysis clearly and logically. Use tables, charts, or graphs where applicable to visualize results and enhance understanding. Clearly state assumptions made and justify any simplifications or approximations.
By following these steps, you can effectively perform calculations and conduct comprehensive analysis in manufacturing systems assignments. This approach not only helps in deriving quantitative insights but also strengthens your problem-solving skills and analytical abilities in complex operational contexts.
Interpret Results
Interpreting results in manufacturing systems assignments involves extracting meaningful insights from calculations and analyses to address the problem statement effectively. Here’s how to interpret results in a structured and insightful manner:
1. Contextualize Findings: Begin by contextualizing your findings within the framework of the problem statement and the models used. Clearly state the implications of your results in relation to the objectives of the assignment.
Example: Discuss how the calculated optimal crew size minimizes total costs while ensuring efficient AGV repair operations in a semiconductor manufacturing setting.
2. Discuss Impact and Relevance: Analyze the impact of your results on the broader context of manufacturing systems or operations management. Highlight the practical implications and potential benefits of implementing your proposed solutions.
Example: Explain how reducing downtime costs through optimal crew sizing can lead to improved overall production efficiency and cost savings.
3. Compare Alternative Scenarios: If applicable, compare your results with alternative scenarios or solutions. Discuss the advantages and limitations of each approach, and justify why your chosen solution is preferable based on the analysis conducted.
Example: Compare the effects of different buffer capacities on system performance in milling operations, demonstrating how your recommended buffer size meets operational requirements effectively.
4. Evaluate Sensitivity and Robustness: Reflect on the sensitivity of your findings to changes in key parameters or assumptions. Discuss the robustness of your solutions and their reliability under varying conditions.
Example: Evaluate how changes in arrival rates or service times affect system performance metrics, demonstrating the resilience of your proposed solutions.
5. Address Practical Considerations: Consider practical constraints or real-world factors that may influence the implementation of your recommendations. Discuss any trade-offs or operational challenges that stakeholders should be aware of.
Example: Address logistical challenges in implementing optimal crew sizes, such as training requirements or scheduling constraints, to ensure smooth integration into daily operations.
6. Provide Recommendations: Based on your analysis and interpretation of results, provide clear and actionable recommendations for stakeholders. Outline steps for implementation and emphasize the expected benefits of adopting your proposed solutions.
Example: Recommend specific crew sizes and operational practices that optimize system performance and minimize costs, backed by quantitative analysis and theoretical insights.
7. Conclusion: Summarize your interpretations and recommendations succinctly. Reinforce the significance of your findings in advancing understanding or improving efficiency within manufacturing systems.
By effectively interpreting results in manufacturing systems assignments, you not only demonstrate your analytical capabilities but also contribute valuable insights to solving complex operational challenges. This approach ensures that your work is meaningful, actionable, and aligned with the goals of optimizing manufacturing processes and enhancing overall efficiency.
Check and Revise
After interpreting results in manufacturing systems assignments, it's crucial to perform thorough checks and revisions to ensure accuracy, clarity, and coherence. Here’s a systematic approach to checking and revising your work:
1. Review Calculation Steps: Double-check each step of your calculations to verify accuracy. Ensure that all formulas were applied correctly and that numerical inputs were accurately used.
Example: Verify the computation of service rates, costs, and system performance metrics against the formulated models and equations.
2. Validate Assumptions: Revisit the assumptions made during the analysis. Ensure that each assumption is justified and consistent with the problem statement and underlying models.
Example: Validate assumptions about arrival rates, repair times, or system behavior under steady-state conditions.
3. Verify Data and Inputs: Confirm the accuracy of all data inputs used in your calculations. Ensure that numerical values, parameters, and variables are correctly transcribed and utilized.
Example: Cross-check data sources and calculations for consistency and alignment with the problem’s requirements.
4. Sensitivity Analysis: Conduct sensitivity analyses to evaluate the robustness of your results to changes in key parameters or assumptions. Assess how variations in inputs impact your findings.
Example: Analyze how adjustments in crew size, arrival rates, or buffer capacities affect system performance and recommended solutions.
5. Logical Coherence: Ensure that your interpretations logically follow from your calculations and analyses. Verify that conclusions drawn align with the results obtained and are supported by the data.
Example: Confirm that recommendations derived from the analysis logically address the identified issues or opportunities within the manufacturing system.
6. Clarity and Precision: Review the clarity and precision of your explanations and interpretations. Ensure that concepts are explained concisely and that technical terms are defined or clarified as needed.
Example: Clarify technical jargon or complex mathematical concepts to enhance understanding for readers or stakeholders.
7. Peer Review or Feedback: Seek feedback from peers, instructors, or colleagues to gain additional perspectives on your work. Incorporate constructive criticism to refine your analysis and strengthen your conclusions.
Example: Discuss findings with peers to validate interpretations and ensure comprehensiveness in addressing the assignment requirements.
8. Formatting and Presentation: Check the formatting of your report or presentation. Ensure that content is well-organized, properly structured, and visually appealing if applicable.
Example: Use headings, subheadings, and bullet points to improve readability and navigation through complex analyses.
9. Final Proofreading: Proofread your work for grammatical errors, typos, and formatting inconsistencies. Ensure that your final submission is polished and professional.
Example: Edit content for clarity and coherence, paying attention to spelling and grammar to enhance overall presentation.
By following these steps to check and revise your work, you can ensure that your interpretations and recommendations in manufacturing systems assignments are accurate, well-supported, and effectively communicated. This systematic approach not only improves the quality of your analysis but also demonstrates your attention to detail and commitment to delivering reliable insights in complex operational contexts.
Conclusion
In conclusion, navigating assignments in manufacturing systems requires a systematic approach to problem-solving and analysis. By following the steps outlined—from understanding the problem statement to performing calculations, interpreting results, and checking for accuracy—you can effectively address complex challenges in this field.
Throughout this process, it's crucial to:
- Thoroughly Understand the Problem Statement: Clarify key details, assumptions, and objectives to guide your analysis.
- Break Down the Problem: Divide complex tasks into manageable parts for systematic exploration.
- Use Appropriate Models and Formulas: Apply relevant mathematical frameworks such as queuing theory, Markov chains, or probabilistic models to derive insights.
- Perform Calculations and Analysis: Execute computations accurately, validate assumptions, and conduct sensitivity analyses to assess robustness.
- Interpret Results: Extract meaningful insights, discuss implications, and provide actionable recommendations based on your findings.
- Check and Revise: Verify calculations, validate assumptions, and ensure clarity and coherence in your interpretations before finalizing your work.
By adhering to these principles, you not only enhance your understanding of manufacturing systems but also develop critical skills in problem-solving and decision-making that are essential in professional practice. Through rigorous analysis and clear communication of your findings, you contribute to improving efficiency, optimizing processes, and driving innovation within manufacturing operations.
In essence, the journey of solving manufacturing systems assignments is not only about reaching solutions but also about deepening your understanding of the intricate dynamics that govern industrial processes. Each assignment presents an opportunity to refine your analytical abilities and contribute meaningfully to the field of manufacturing engineering.