Tips for Tackling Fluid Mechanics Assignments
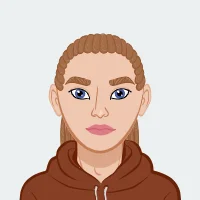
Fluid Mechanics is a fundamental branch of engineering that deals with the behavior of fluids (liquids and gases) and their interactions with forces, encompassing a wide range of applications from hydraulic systems to aerodynamics. Understanding how fluids behave under various conditions and how they interact with their surroundings is essential for designing and optimizing systems in many engineering fields, including mechanical, civil, and chemical engineering. This field covers everything from the flow of air over an aircraft wing to the movement of water through a pipeline, and even the circulation of blood in the human body. Mastering these concepts will be crucial for applying them in practical scenarios and academic challenges alike.
Assignments in fluid mechanics can be particularly challenging due to the complex mathematical and physical principles involved. These principles often require a deep understanding of differential equations, fluid properties, and boundary conditions. The subject involves analyzing various types of flow, such as laminar and turbulent flow, and requires knowledge of both theoretical concepts and practical applications. Additionally, fluid mechanics problems often involve computational fluid dynamics (CFD) simulations, which can be quite intricate and computationally intensive.
However, with the right approach and strategies, you can effectively tackle these assignments and gain a solid grasp of fluid mechanics concepts. By breaking down the problems into manageable parts, utilizing visual aids, and systematically applying fundamental equations, you can simplify the process. Moreover, consistent practice and seeking help from various resources, such as textbooks, online tutorials, and academic forums, can significantly enhance your understanding and problem-solving skills in fluid mechanics. Here are some general tips and strategies to help you solve fluid mechanics assignments effectively.
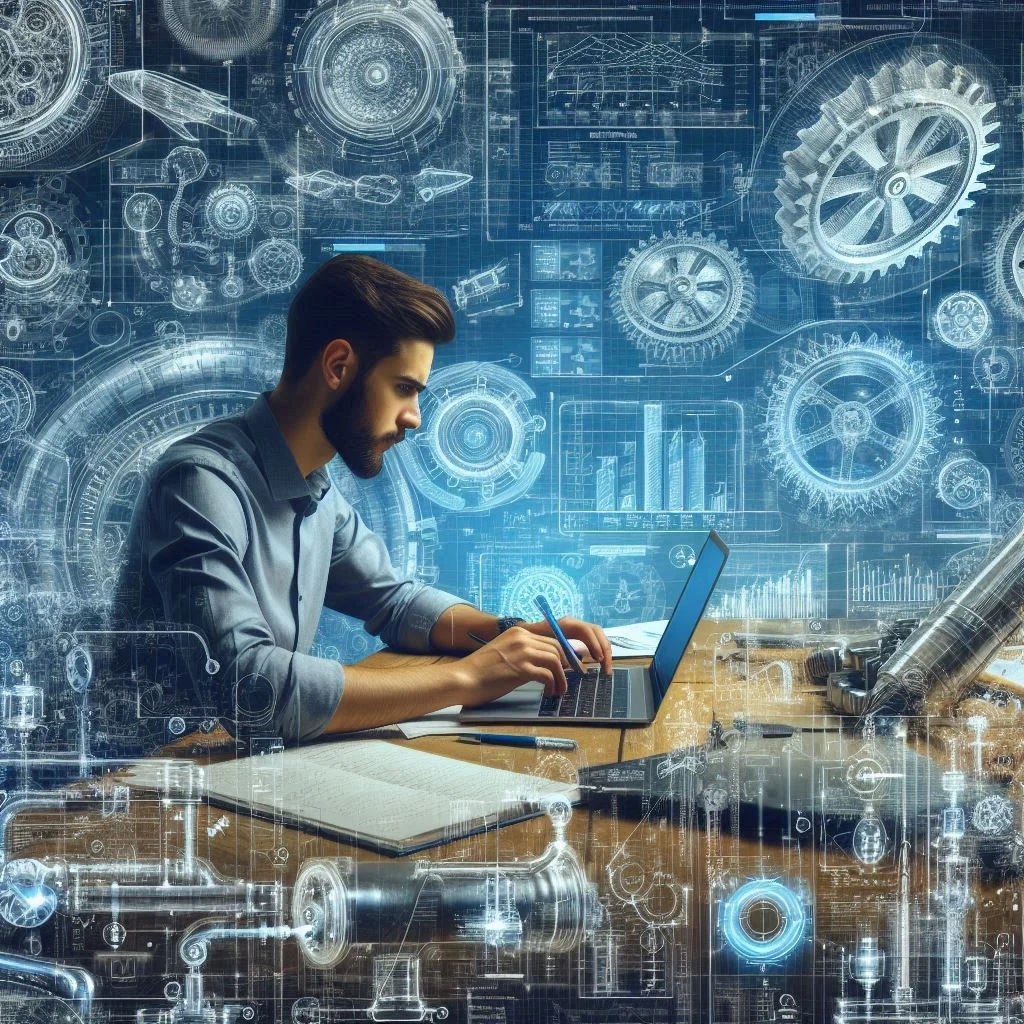
Understand the Basics
Before diving into complex fluid mechanics problems, it is crucial to build a strong foundation by understanding the basic concepts and principles. This foundational knowledge will serve as the backbone for tackling more advanced topics and assignments. Here are some key areas to focus on:
1. Fluid Properties
- Density (ρ): The mass per unit volume of a fluid, typically measured in kg/m³. It's a fundamental property that affects buoyancy and pressure.
- Viscosity (μ): A measure of a fluid's resistance to deformation and flow. Dynamic viscosity (μ) and kinematic viscosity (ν = μ/ρ) are essential for characterizing fluid flow.
- Surface Tension: The cohesive force at the surface of a fluid that causes it to behave like an elastic sheet. This is particularly important in small-scale flows and interfaces between different fluids.
2. Fluid Statics
- Pressure Variation: Understand how pressure changes with depth in a fluid at rest. The basic equation P=P0+ρghP = P_0 + ρghP=P0+ρgh relates the pressure at a depth h to the fluid density (ρ), gravitational acceleration (g), and the pressure at the surface (P₀).
- Buoyancy: The principle that a fluid exerts an upward force on an object submerged in it, equal to the weight of the fluid displaced by the object. This is governed by Archimedes' principle.
3. Fluid Dynamics
- Continuity Equation: This equation expresses the conservation of mass in a fluid flow. For incompressible flows, it simplifies to A1V1=A2V2A_1V_1 = A_2V_2A1V1=A2V2, where A is the cross-sectional area and V is the flow velocity.
- Bernoulli’s Equation: Relates pressure, velocity, and height in a flowing fluid. It is given by P+½ρV2+ρgh=constantP + ½ρV² + ρgh = \text{constant}P+½ρV2+ρgh=constant along a streamline.
- Navier-Stokes Equations: These fundamental equations describe the motion of viscous fluid substances and are used to model the behavior of fluids in various conditions.
4. Dimensional Analysis
- Reynolds Number (Re): A dimensionless number that characterizes the flow regime (laminar or turbulent). It is defined as Re=ρVDμRe = \frac{ρVD}{μ}Re=μρVD, where V is the velocity, D is the characteristic length, and μ is the dynamic viscosity.
- Other Non-dimensional Numbers: Familiarize yourself with other important dimensionless numbers such as Froude number, Mach number, and Prandtl number, which help in analyzing different flow scenarios.
5. Types of Fluids
- Newtonian Fluids: Fluids that obey Newton's law of viscosity, where the shear stress is linearly proportional to the shear rate (e.g., water, air).
- Non-Newtonian Fluids: Fluids that do not follow Newton's law of viscosity. Their viscosity can change with the rate of shear strain (e.g., blood, ketchup, cornstarch solution).
6. Flow Regimes
- Laminar Flow: Smooth, orderly fluid motion characterized by layers of fluid that slide past one another.
- Turbulent Flow: Chaotic fluid motion characterized by eddies and vortices. It is typically associated with high Reynolds numbers.
Having a solid grasp of these basics will make it easier to approach and solve fluid mechanics assignments. By understanding these fundamental concepts, you will be better equipped to handle more complex problems and apply the principles accurately.
Review the Assignment Requirements
Before you start solving any fluid mechanics assignment, it's essential to thoroughly review the assignment requirements. This step ensures that you understand what is expected and allows you to plan your approach effectively. Here are key aspects to consider when reviewing your assignment:
1. Carefully Read the Problem Statement
- Identify Key Objectives: Determine what the assignment is specifically asking you to do. Are you required to calculate specific parameters like pressure, velocity, or shear stress? Is the focus on theoretical derivations, practical applications, or a combination of both?
- Understand the Context: Recognize the scenario or system being analyzed. For instance, are you dealing with fluid flow in a pipe, around an airfoil, or within a hydraulic system?
2. Determine the Type of Fluid
- Newtonian vs. Non-Newtonian: Establish whether the fluid in question is Newtonian (with constant viscosity) or Non-Newtonian (with variable viscosity). This will affect the equations and assumptions you use.
- Compressible vs. Incompressible: Identify if the fluid is compressible (such as gases at high velocities) or incompressible (most liquids and low-velocity gases). This distinction is crucial for applying the appropriate form of the continuity and momentum equations.
3. Recognize the Flow Conditions
- Steady vs. Unsteady Flow: Determine if the flow conditions are steady (parameters do not change with time) or unsteady (parameters change with time). Steady flows are simpler to analyze but many real-world problems involve unsteady flow.
- Laminar vs. Turbulent Flow: Ascertain whether the flow is laminar (smooth and orderly) or turbulent (chaotic and mixed). This can often be gauged using the Reynolds number and significantly affects the analysis approach.
4. Identify Boundary Conditions and Initial Conditions
- Boundary Conditions: Note the specified conditions at the boundaries of the domain, such as pressure, velocity, and temperature at the inlets, outlets, and walls. Proper application of boundary conditions is crucial for solving the governing equations accurately.
- Initial Conditions: For unsteady flow problems, identify the initial conditions that describe the state of the fluid at the start of the analysis.
5. Specify the Required Outputs
- Quantitative Results: Determine what specific quantities need to be calculated, such as pressure distribution, velocity profiles, shear stress, flow rates, etc.
- Qualitative Analysis: Some assignments may require you to discuss the behavior of the fluid flow qualitatively, explaining physical phenomena and underlying principles.
6. Check for Special Instructions
- Analytical vs. Numerical Methods: Determine if the assignment requires analytical solutions using mathematical derivations or numerical solutions using computational tools like CFD (Computational Fluid Dynamics) software.
- Diagrams and Visualizations: Identify if you need to provide schematics, flow diagrams, or graphs to illustrate your findings. Visual aids often enhance the clarity and presentation of your solutions.
- Units and Conversions: Ensure you understand the units used in the problem statement and any conversions that may be necessary. Consistency in units is vital to avoid errors in calculations.
7. Understand the Grading Criteria
- Weightage of Different Sections: Check if there is any information on how different sections of the assignment are weighted. This can help prioritize your efforts accordingly.
- Clarity and Precision: Pay attention to instructions regarding the presentation of your solutions. Clear, precise, and well-organized answers are usually rewarded.
By meticulously reviewing these aspects, you can clarify the expectations of the assignment, avoid misunderstandings, and ensure that your approach is aligned with the requirements. This thorough preparation step is crucial for efficiently and effectively solving fluid mechanics assignments.
Identify the Governing Equations
Fluid mechanics problems are typically solved using a set of fundamental governing equations that describe the behavior of fluids. Understanding and correctly applying these equations is crucial for analyzing and solving fluid mechanics assignments. Here are the primary governing equations you should be familiar with:
1. Continuity Equation
The continuity equation expresses the conservation of mass in a fluid flow. For an incompressible fluid (where the density ρ remains constant), it is given by:
∂ρ∂t+∇⋅(ρu)=0\frac{\partial \rho}{\partial t} + \nabla \cdot (\rho \mathbf{u}) = 0∂t∂ρ+∇⋅(ρu)=0
For incompressible flows, this simplifies to:
∇⋅u=0\nabla \cdot \mathbf{u} = 0∇⋅u=0
where:
- u\mathbf{u}u is the velocity vector of the fluid.
This equation states that the mass flow rate into a control volume must equal the mass flow rate out of the control volume.
2. Navier-Stokes Equations
The Navier-Stokes equations describe the motion of viscous fluid substances. These equations result from applying Newton's second law to fluid motion and considering the effects of viscosity. For an incompressible, Newtonian fluid, the Navier-Stokes equations are:
ρ(∂u∂t+(u⋅∇)u)=−∇P+μ∇2u+f\rho \left( \frac{\partial \mathbf{u}}{\partial t} + (\mathbf{u} \cdot \nabla) \mathbf{u} \right) = -\nabla P + \mu \nabla^2 \mathbf{u} + \mathbf{f}ρ(∂t∂u+(u⋅∇)u)=−∇P+μ∇2u+f
where:
- ρ\rhoρ is the fluid density.
- u\mathbf{u}u is the velocity vector.
- PPP is the pressure.
- μ\muμ is the dynamic viscosity.
- f\mathbf{f}f is the body force per unit volume (e.g., gravity).
These equations represent the conservation of momentum in the fluid.
3. Bernoulli’s Equation
Bernoulli’s equation is a simplification of the Navier-Stokes equations for steady, incompressible, and inviscid (non-viscous) flow along a streamline. It is given by:
P+12ρv2+ρgh=constantP + \frac{1}{2} \rho v^2 + \rho gh = \text{constant}P+21ρv2+ρgh=constant
where:
- PPP is the pressure.
- ρ\rhoρ is the fluid density.
- vvv is the flow velocity.
- ggg is the acceleration due to gravity.
- hhh is the height above a reference plane.
This equation states that the sum of the pressure energy, kinetic energy, and potential energy per unit volume remains constant along a streamline.
4. Energy Equation
The energy equation accounts for the conservation of energy in a fluid flow, considering internal, kinetic, and potential energies. For incompressible flows with no heat transfer and no work done by or on the fluid, the mechanical energy equation is similar to Bernoulli’s equation. However, the full energy equation is used in more complex scenarios involving thermal effects:
∂∂t(ρe)+∇⋅(ρeu+q)=u⋅f−∇⋅J\frac{\partial}{\partial t} (\rho e) + \nabla \cdot (\rho e \mathbf{u} + \mathbf{q}) = \mathbf{u} \cdot \mathbf{f} - \nabla \cdot \mathbf{J}∂t∂(ρe)+∇⋅(ρeu+q)=u⋅f−∇⋅J
where:
- eee is the internal energy per unit mass.
- q\mathbf{q}q is the heat flux vector.
- J\mathbf{J}J is the diffusive flux of internal energy.
5. Equation of State
The equation of state relates the fluid’s pressure, density, and temperature. For an ideal gas, it is given by:
P=ρRTP = \rho RTP=ρRT
where:
- RRR is the specific gas constant.
- TTT is the temperature.
6. Dimensional Analysis and Similarity
Dimensional analysis helps to reduce the complexity of fluid mechanics problems by identifying non-dimensional numbers that characterize the flow. Important dimensionless numbers include:
- Reynolds Number (Re): Re=ρvLμRe = \frac{\rho v L}{\mu}Re=μρvL which indicates whether the flow is laminar or turbulent.
- Froude Number (Fr): Fr=vgLFr = \frac{v}{\sqrt{gL}}Fr=gLv which compares inertial forces to gravitational forces.
- Mach Number (Ma): Ma=vcMa = \frac{v}{c}Ma=cv where ccc is the speed of sound, relevant in compressible flows.
7. Boundary Conditions
Applying the correct boundary conditions is crucial for solving the governing equations. Common types include:
- No-Slip Condition: The fluid velocity at a solid boundary is zero relative to the boundary.
- Free-Slip Condition: The tangential component of the velocity at a boundary is zero, but the normal component is not necessarily zero.
- Inlet/Outlet Conditions: Specify the fluid properties (pressure, velocity, etc.) at the boundaries where the fluid enters or exits the control volume.
Understanding and applying these governing equations correctly is essential for analyzing fluid mechanics problems. These equations form the mathematical foundation for most fluid dynamics analyses and are critical for deriving meaningful solutions to your assignments.
Break Down the Problem
Breaking down a fluid mechanics problem into manageable parts is crucial for systematically analyzing and solving it. This approach not only makes the problem more approachable but also helps in identifying the key steps required to reach a solution. Here’s a step-by-step guide on how to break down fluid mechanics problems:
1. Define the System and Control Volume
- Identify the System: Clearly define the physical system under investigation. This could be a pipe flow, a flow over a wing, a jet exiting a nozzle, etc.
- Control Volume: Select an appropriate control volume (a fixed region in space through which fluid flows). This helps in applying the governing equations to a specific region.
2. List Known and Unknown Variables
- Known Variables: Identify all the given data in the problem statement. This includes fluid properties (density, viscosity), flow characteristics (velocity, pressure), and geometric parameters (length, diameter).
- Unknown Variables: Determine what needs to be solved. These could be pressure drop, velocity distribution, shear stress, etc.
3. Sketch and Diagram
- Draw a Diagram: Create a clear, labeled diagram of the problem. Include the control volume, coordinate system, boundary conditions, and any relevant flow features (inlets, outlets, obstacles).
- Flow Patterns: Indicate the expected flow patterns, such as streamline directions, regions of turbulence, or areas of recirculation.
4. Simplify Assumptions
- Steady vs. Unsteady Flow: Determine if the flow is steady (parameters do not change with time) or unsteady (parameters change with time). Steady flows are easier to handle analytically.
- Incompressible vs. Compressible Flow: Decide if the fluid density changes significantly with pressure changes. Most liquid flows are incompressible, while gas flows at high speeds or high pressures might be compressible.
- Viscous vs. Inviscid Flow: For high Reynolds number flows, viscosity effects might be negligible (inviscid flow). For low Reynolds number flows or near solid boundaries, viscosity must be considered.
5. Apply the Governing Equations
- Continuity Equation: Use this to ensure mass conservation within the control volume.
- Navier-Stokes Equations: Apply these for momentum conservation. Simplify based on assumptions (e.g., incompressible, steady flow).
- Energy Equation: If heat transfer or energy changes are significant, use the energy equation.
- Bernoulli’s Equation: For inviscid, incompressible, and steady flows along a streamline, apply Bernoulli’s equation.
6. Boundary Conditions and Initial Conditions
- Boundary Conditions: Identify and apply the boundary conditions at the control volume’s surfaces. This includes specifying velocity, pressure, or shear stress at inlets, outlets, and walls.
- Initial Conditions: For unsteady flows, define the initial state of the fluid (velocity, pressure, etc.) at the start of the analysis.
7. Solve the Equations
- Substitute Known Values: Plug in the known variables into the governing equations.
- Simplify and Rearrange: Algebraically manipulate the equations to isolate the unknowns.
- Numerical Methods: For complex problems that cannot be solved analytically, use numerical methods and computational tools like CFD software.
8. Validate the Results
- Dimensional Consistency: Check that the units in your equations are consistent.
- Sanity Check: Ensure the results make physical sense. For instance, check if the calculated pressures and velocities are within realistic ranges.
- Compare with Known Solutions: If possible, compare your results with known solutions or empirical data to verify accuracy.
Example Breakdown: Flow Through a Pipe
1. Define the System and Control Volume:
- System: Water flowing through a horizontal pipe.
- Control Volume: A segment of the pipe.
2. List Known and Unknown Variables:
- Known: Pipe diameter (D), length (L), water density (ρ), viscosity (μ), inlet velocity (V_in).
- Unknown: Pressure drop (ΔP), velocity distribution.
3. Sketch and Diagram:
Draw a side view of the pipe, label the inlet, outlet, diameter, and length.
4. Simplify Assumptions:
- Steady flow.
- Incompressible flow (water).
- Fully developed, laminar flow (if Reynolds number < 2000).
5. Apply the Governing Equations:
- Continuity: A1V1=A2V2A_1 V_1 = A_2 V_2A1V1=A2V2.
- Navier-Stokes (simplified for laminar pipe flow): ΔP=32μLVD2\Delta P = \frac{32 \mu L V}{D^2}ΔP=D232μLV.
6. Boundary Conditions and Initial Conditions:
- Boundary: No-slip condition at pipe wall.
- Initial: Not applicable for steady flow.
7. Solve the Equations:
Substitute values into the simplified Navier-Stokes equation to find ΔP.
8. Validate the Results:
Ensure the pressure drop is realistic and within expected ranges.
By systematically breaking down the problem and following these steps, you can tackle complex fluid mechanics assignments methodically and effectively.
Use Proper Units and Conversions
Using proper units and conversions is essential in fluid mechanics to ensure accurate calculations and to avoid errors. Here’s a guide on how to handle units and conversions effectively in fluid mechanics assignments:
1. Understand the SI Units
Fluid mechanics primarily uses the International System of Units (SI). Familiarize yourself with the following common units:
- Length: Meter (m)
- Mass: Kilogram (kg)
- Time: Second (s)
- Velocity: Meters per second (m/s)
- Acceleration: Meters per second squared (m/s²)
- Force: Newton (N), where 1 N = 1 kg·m/s²
- Pressure: Pascal (Pa), where 1 Pa = 1 N/m²
- Density: Kilogram per cubic meter (kg/m³)
- Dynamic Viscosity: Pascal-second (Pa·s)
- Kinematic Viscosity: Square meter per second (m²/s)
- Energy: Joule (J), where 1 J = 1 N·m
- Power: Watt (W), where 1 W = 1 J/s
2. Conversion Factors
When working with different units, you may need to convert between them. Here are some useful conversion factors:
Length:
- 1 meter (m) = 100 centimeters (cm) = 1000 millimeters (mm)
- 1 inch = 0.0254 meters (m)
- 1 foot = 0.3048 meters (m)
Pressure:
- 1 atmosphere (atm) = 101325 Pa
- 1 bar = 100000 Pa
- 1 psi (pound per square inch) = 6894.76 Pa
Volume:
- 1 liter (L) = 0.001 cubic meters (m³)
- 1 gallon (US) = 3.78541 liters (L)
Density:
- 1 gram per cubic centimeter (g/cm³) = 1000 kg/m³
Viscosity:
- 1 Poise (P) = 0.1 Pa·s
- 1 centiPoise (cP) = 0.001 Pa·s
3. Unit Consistency
Ensure all variables in your equations are in consistent units. For instance, if you are using the continuity equation, make sure that the area is in square meters (m²) and the velocity is in meters per second (m/s). Here’s an example of ensuring unit consistency in a calculation:
Example: Calculating Pressure Drop in a Pipe
Given:
- Diameter of the pipe, D=0.1D = 0.1D=0.1 m
- Length of the pipe, L=10L = 10L=10 m
- Flow velocity, V=2V = 2V=2 m/s
- Dynamic viscosity of water, μ=0.001\mu = 0.001μ=0.001 Pa·s
Find: Pressure drop (ΔP\Delta PΔP).
Use the Hagen-Poiseuille equation for laminar flow: ΔP=32μLVD2\Delta P = \frac{32 \mu L V}{D^2}ΔP=D232μLV
Substitute the known values into the equation: ΔP=32×0.001×10×2(0.1)2\Delta P = \frac{32 \times 0.001 \times 10 \times 2}{(0.1)^2}ΔP=(0.1)232×0.001×10×2 ΔP=0.640.01\Delta P = \frac{0.64}{0.01}ΔP=0.010.64 ΔP=64 Pa\Delta P = 64 \, \text{Pa}ΔP=64Pa
Here, all units are consistent, leading to a pressure drop of 64 Pascal.
4. Dimensional Analysis
Dimensional analysis helps check the correctness of equations and conversions. Ensure each term in your equations has the same dimensions. For instance, in Bernoulli’s equation: P+12ρv2+ρgh=constantP + \frac{1}{2} \rho v^2 + \rho gh = \text{constant}P+21ρv2+ρgh=constant
Each term has the dimensions of pressure (force per unit area).
5. Unit Conversion in Calculations
When given different units in a problem, convert all units to the SI system before performing calculations.
Example: Converting and Using Given Data
Given:
- Pressure, P=1P = 1P=1 atm
- Velocity, V=3V = 3V=3 m/s
- Height, h=10h = 10h=10 feet
Convert pressure to Pascals: 1 atm=101325 Pa1 \, \text{atm} = 101325 \, \text{Pa}1atm=101325Pa
Convert height to meters: 10 feet=10×0.3048 m=3.048 m10 \, \text{feet} = 10 \times 0.3048 \, \text{m} = 3.048 \, \text{m}10feet=10×0.3048m=3.048m
Now, all values are in consistent units and can be used directly in calculations.
6. Check and Double-Check Conversions
Always double-check your conversions to avoid errors. Incorrect unit conversions can lead to significant mistakes in your results.
By ensuring proper use of units and conversions, you enhance the accuracy and reliability of your fluid mechanics calculations. Consistency in units is a fundamental aspect of solving engineering problems correctly.
Visualize the Problem
Visualizing the problem is a crucial step in solving fluid mechanics assignments. It helps you understand the physical scenario, identify key variables and boundaries, and plan your approach. Here’s how to effectively visualize a fluid mechanics problem:
1. Create a Schematic Diagram
A well-drawn schematic diagram is essential for visualizing the problem. Follow these steps:
- Identify the Domain: Clearly outline the boundaries of the fluid flow domain.
- Label Key Components: Include all relevant components such as inlets, outlets, obstacles, and any interfaces.
- Coordinate System: Establish a coordinate system (e.g., Cartesian, cylindrical) to reference positions within the domain.
Example: Flow Through a Pipe
- Draw a pipe with marked inlet and outlet.
- Label the pipe length (L) and diameter (D).
- Indicate the flow direction with arrows.
- Show the coordinate system (e.g., x-axis along the pipe length).
Note: Replace with actual diagram
2. Show Boundary Conditions
Clearly indicate the boundary conditions on your diagram. This includes specifying:
- Inlet Conditions: Velocity, pressure, temperature, etc., at the entry point.
- Outlet Conditions: Pressure, flow rate, etc., at the exit point.
- Wall Conditions: No-slip condition (velocity is zero at the wall), temperature, etc.
Example: Boundary Conditions in Pipe Flow
- At the inlet, label the velocity (V_in) and pressure (P_in).
- At the outlet, label the pressure (P_out).
- Along the pipe wall, indicate the no-slip condition.
3. Depict Flow Patterns and Streamlines
Visualizing flow patterns helps in understanding the fluid behavior. Streamlines can be used to represent the path taken by fluid particles.
- Streamlines: Draw lines that indicate the flow direction and path.
- Flow Separation: Show regions where the flow separates from the boundary (if applicable).
- Recirculation Zones: Indicate any areas where the fluid recirculates.
Example: Streamlines in a Pipe Bend
- Draw a pipe with a bend.
- Indicate the streamlines showing smooth flow along the bend.
- Highlight any regions where flow separation might occur.
Note: Replace with actual diagram
4. Annotate Important Variables
Annotate your diagram with important variables and their units. This includes:
- Geometric Parameters: Lengths, diameters, heights.
- Flow Properties: Velocities, pressures, temperatures.
- Fluid Properties: Density, viscosity.
Example: Annotated Diagram
- Mark the pipe length (L = 10 m).
- Label the pipe diameter (D = 0.1 m).
- Indicate the inlet velocity (V_in = 2 m/s).
5. Include a Legend
If your diagram contains multiple symbols or different line types, include a legend to explain them. This ensures clarity and helps others understand your visualization.
Example: Legend for Pipe Flow Diagram
- Solid Line: Pipe walls
- Dashed Line: Streamlines
- Arrows: Flow direction
- VVV: Velocity
- PPP: Pressure
6. Use Software Tools
For complex problems, use software tools to create detailed and accurate visualizations. Tools like MATLAB, ANSYS Fluent, and SolidWorks can generate precise diagrams, flow patterns, and simulations.
Example: CFD Simulation
- Use ANSYS Fluent to simulate the flow through a complex geometry.
- Generate a contour plot of velocity distribution.
- Create a vector plot showing the direction and magnitude of flow at various points.
Note: Replace with actual simulation result
7. Provide Multiple Views
For three-dimensional problems, provide multiple views (top view, side view, isometric view) to give a complete understanding of the flow domain.
Example: 3D Flow Around an Object
- Top view: Shows the object and flow direction.
- Side view: Highlights the height and vertical flow patterns.
- Isometric view: Provides a 3D perspective of the flow around the object.
Note: Replace with actual 3D visualization
By effectively visualizing the problem, you can better understand the fluid behavior, communicate your approach, and ensure all relevant aspects are considered in your analysis. This step is vital for both solving the problem and presenting your findings clearly.
Validate Your Solution
Validating your solution in fluid mechanics ensures that your calculations are accurate, consistent with physical principles, and correctly applied to the problem at hand. Here are steps to effectively validate your solution:
1. Check Dimensional Consistency
Verify that all terms and equations in your calculations have consistent dimensions. This helps ensure that equations are correctly formulated and that units are properly handled throughout the analysis.
For example, in Bernoulli's equation: P+12ρv2+ρgh=constantP + \frac{1}{2} \rho v^2 + \rho gh = \text{constant}P+21ρv2+ρgh=constant
- PPP, pressure (Pa)
- ρ\rhoρ, density (kg/m³)
- vvv, velocity (m/s)
- ggg, acceleration due to gravity (m/s²)
- hhh, height (m)
2. Compare with Analytical Solutions
If available, compare your solution with known analytical solutions for similar problems. This is particularly useful for standard cases like flow through pipes, flow around objects, or simple boundary value problems.
Example: For laminar flow through a circular pipe, compare your pressure drop calculation using the Hagen-Poiseuille equation (ΔP=32μLVD2\Delta P = \frac{32 \mu L V}{D^2}ΔP=D232μLV) with established pressure drop values for laminar flow.
3. Use Empirical Data or Experimental Results
Refer to empirical data or experimental results from literature or previous studies. Compare your calculated results with experimental measurements to verify accuracy.
Example: Use published data on pressure drop measurements in a pipe for the given flow conditions (velocity, diameter) and compare with your calculated pressure drop.
4. Conduct Sensitivity Analysis
Perform sensitivity analysis by varying input parameters within reasonable ranges to see how sensitive your solution is to changes. This helps identify potential errors or inconsistencies in your calculations.
Example: Vary the viscosity (μ\muμ), flow velocity (VVV), or pipe diameter (DDD) slightly and observe the resulting changes in pressure drop or flow rate.
5. Check for Conservation Laws
Ensure that fundamental conservation laws (mass, momentum, energy) are satisfied by your solution. This involves verifying that mass flow rates, forces, and energy transfers are correctly accounted for throughout the system.
Example: Check mass balance using the continuity equation and ensure that the sum of forces in the momentum equation balances out.
6. Verify Boundary Conditions
Check that boundary conditions applied in your solution match the physical conditions of the problem. Ensure that inlet velocities, pressures, or other specified conditions align with the expected behavior of the fluid flow.
Example: Verify that the no-slip condition at solid boundaries or the specified velocity profiles at inlets are correctly implemented.
7. Compare with Numerical Simulations
If you used numerical methods or computational fluid dynamics (CFD) software, compare your analytical solution with results from the numerical simulation. This provides validation and cross-verification of your approach.
Example: Compare pressure distributions or velocity profiles obtained from your analytical calculations with those from a CFD simulation of the same problem setup.
8. Consult with Peers or Experts
Discuss your solution approach and results with peers, instructors, or experts in fluid mechanics. Getting feedback and discussing alternative methods can help identify errors or areas for improvement.
Example: Present your calculations and assumptions to a professor or colleague experienced in fluid mechanics for review and feedback.
9. Document Assumptions and Limitations
Clearly document any assumptions made and limitations of your analysis. Acknowledge uncertainties or simplifications that may affect the accuracy of your solution.
Example: Note assumptions such as assuming steady-state flow, neglecting heat transfer effects, or assuming ideal fluid behavior.
10. Iterate if Necessary
If discrepancies or errors are found during validation, revisit your calculations, assumptions, or methodologies. Make necessary adjustments and revalidate until you achieve consistent and accurate results.
Example: Re-examine boundary conditions, reconsider numerical methods, or refine assumptions to improve the accuracy of your solution.
By systematically validating your solution using these steps, you can ensure the reliability and accuracy of your fluid mechanics analysis. This process is crucial for engineering applications where precise calculations and adherence to physical principles are essential.
Conclusion
Fluid mechanics problem-solving is a structured process starting with defining the system's boundaries and specifying conditions like inlet velocities and pressures. Equations such as continuity, Navier-Stokes, and energy equations are then applied, ensuring all units are converted to maintain consistency in the International System of Units (SI). Visual representations like diagrams and streamline plots aid in understanding flow patterns and boundary conditions. Validating solutions involves comparing results with known solutions or experimental data, performing sensitivity analyses, and ensuring adherence to conservation laws. This rigorous approach ensures accurate and dependable solutions essential for engineering applications across various industries.