Approaching Welding and Optical Fiber Alignment Assignments in Mechanical Engineering
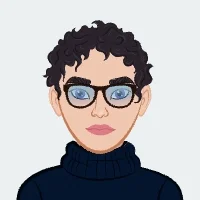
Mechanical engineering students frequently face assignments that demand a thorough understanding of intricate concepts and their application to real-world problems. These tasks not only test their theoretical knowledge but also their ability to translate this knowledge into practical solutions. Two common and critical areas where these skills are often applied are welding and optical fiber alignment. In these fields, students must comprehend the detailed mechanics and underlying principles to effectively solve the given problems.
Welding assignments, for instance, require students to understand the effects of heat intensity on different welding processes, the interaction time, and the feed rate. They must calculate precise parameters to ensure efficient and high-quality welding. Similarly, assignments involving optical fiber alignment necessitate a deep understanding of micromachining techniques, material properties, and geometric tolerances to achieve accurate alignment.
Here, we will outline a comprehensive approach to get help with mechanical engineering assignments, using specific examples to demonstrate the methodology and illustrate the step-by-step processes involved. By mastering these techniques, students can enhance their problem-solving skills and excel in their mechanical engineering coursework. This approach not only helps in completing assignments but also builds a solid foundation for handling complex engineering challenges in their future careers.
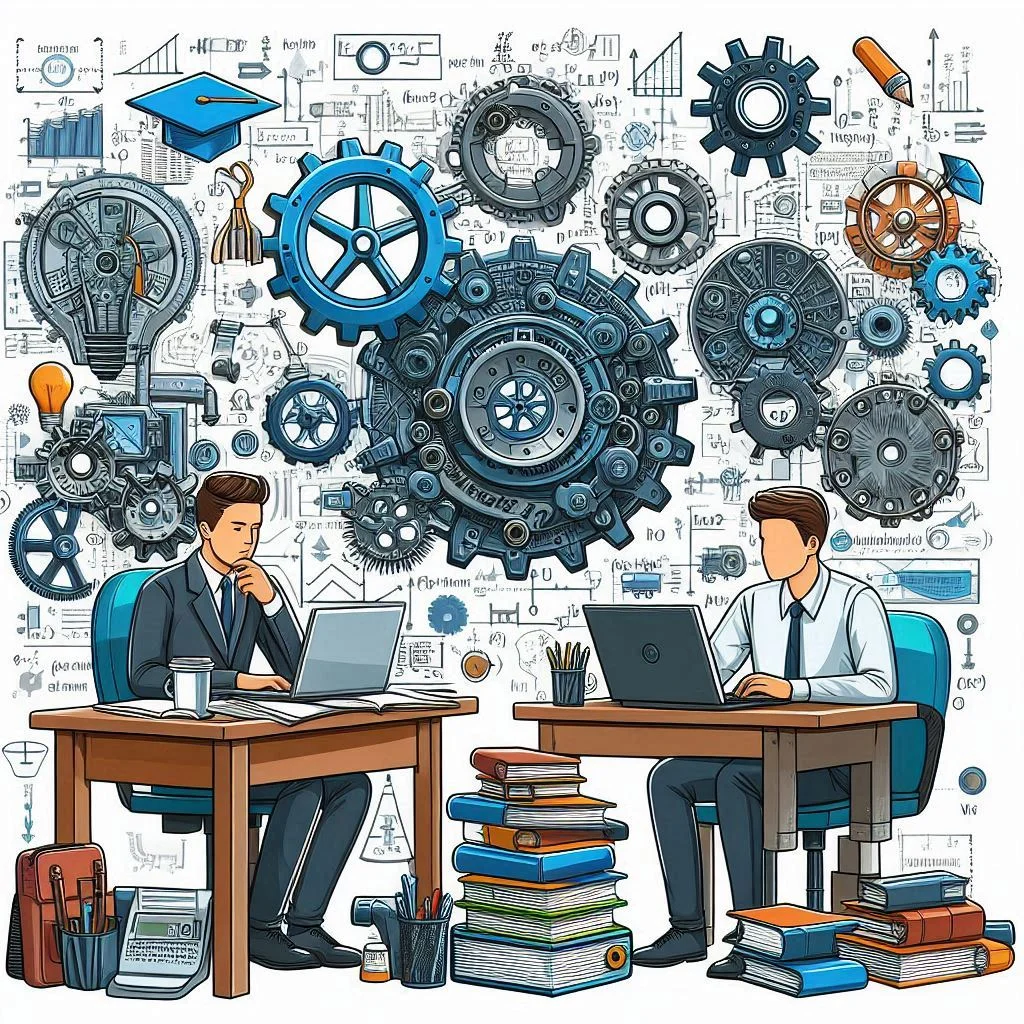
Understanding Welding Heat Sources and Their Effects
Welding is a fundamental process in mechanical engineering, involving the joining of materials, typically metals, by using high heat to melt the parts together and allowing them to cool, causing fusion. Different welding techniques and equipment are used based on the type of materials being joined and the specific requirements of the job. A crucial aspect of welding is understanding the heat sources, as the intensity of heat directly impacts the interaction time, feed rate, and overall quality of the weld. Mastery of these concepts is essential for selecting the appropriate welding method and optimizing the process to ensure structural integrity and efficiency in projects. For those seeking additional support and expertise, mechanical engineering assignment help can provide valuable insights and guidance on mastering these welding principles and other complex engineering tasks.
Example Assignment: Welding Heat Intensity and Feed Rate
Assignment Overview: In this example, the task is to understand the effect of heat intensity from various welding heat sources on the interaction time and feed rate. For a planar heat source on steel, the interaction time, tm, is provided by the formula:
where H.I. represents the heat intensity in W/M^2. You are required to weld a straight lap joint with a length of 40 cm.
Steps to Solve:
Identify the Given Parameters:
- Manual oxyacetylene welding equipment: Has a weld pool size of 10 mm and H.I.=10^3 W/cm^2
- SMAW equipment: Has a weld pool size of 5 mm and H.I.=10^4 W/cm^2
- Laser welding system: Has a weld pool size of 1 mm and H.I.=106 W/cm^
Calculate the Interaction Time:
For oxyacetylene welding
tm=(5000/10^3 )^2=25s
For SMAW:
tm=(5000/10^4 )^2=0.25s
Determine the Welding Time for the Job:
Oxyacetylene welding time:
Time=40cm/10mm×25s=100s
SMAW welding time:
Time=40cm/5mm×0.25s=2s
Justify the Equipment Upgrade:
Compare the productivity increase with the cost. In this case, SMAW significantly reduces welding time, which may justify its higher expense due to increased efficiency and productivity.
Assess the Feasibility of Using Laser Welding:
Calculate the Minimum Speed: To avoid over-melting or vaporization.
Consider Automation: Determine if manual handling is feasible or if robotic assistance is required due to the precision and speed needed for laser welding.
By following these structured steps, students can systematically approach welding assignments, ensuring they understand and apply the relevant principles effectively. This approach not only aids in solving the specific problem at hand but also builds a solid foundation for tackling more complex welding challenges in their professional careers.
Aligning Optical Fibers Using Micromachining Techniques
Optical fiber alignment is a critical process in the field of telecommunications and photonics, where precise alignment is essential for efficient signal transmission. Misalignment can lead to significant signal loss, increased attenuation, and overall degraded performance of the optical communication system. The development of advanced micromachining techniques has revolutionized this field, enabling the precise and cost-effective alignment of optical fibers without the necessity for highly skilled labor. One such cutting-edge technique involves the use of V-grooved silicon substrates created through KOH (potassium hydroxide) bulk micromachining. This process takes advantage of the anisotropic etching properties of silicon to form well-defined V-grooves that can accurately position optical fibers in a manner that ensures optimal signal coupling and minimal loss.
These V-grooved substrates have become increasingly popular due to their ability to provide high precision at a relatively low cost. The use of silicon, a material with well-understood properties and widespread availability, further enhances the practicality and scalability of this technique. Additionally, the compatibility of silicon with other semiconductor processing technologies makes V-grooved substrates an attractive option for integrating optical fibers into various photonic devices and systems. Understanding and implementing these micromachining techniques can significantly improve the performance and reliability of optical communication networks, making this knowledge highly valuable for students and professionals in the field.
Example Assignment: Optical Fiber Alignment in V-Grooved Silicon
Assignment Overview: In this example, the task involves aligning an optical fiber to a laser light source with less than 1 µm transverse error using V-grooved silicon substrates. The technology utilizes KOH bulk micromachining of {100} silicon, which provides tight mechanical tolerances and high precision at a relatively low processing cost. This approach leverages the natural crystallographic properties of silicon, allowing for the formation of precise V-grooves that facilitate the accurate placement of optical fibers, thereby enhancing the performance of optical communication systems.
Steps to Solve:
Understand the Etching Process:
The etching process is a fundamental aspect of micromachining, where the anisotropic etching properties of silicon are exploited. In this process, the {100} planes of silicon etch at a much faster rate compared to the {111} planes when exposed to KOH solution. This differential etching rate results in the formation of V-grooves with a specific angle θ\thetaθ, which is crucial for the precise alignment of optical fibers. Understanding the etching process involves knowing the chemical reactions involved, the factors affecting etching rates, and how to control these parameters to achieve the desired groove geometry.
Calculate the Groove Angle θ\thetaθ:
The angle θ\thetaθ between the {111} planes and the wafer surface is a critical parameter in the design of V-grooves. For silicon, this angle is typically around 54.7 degrees due to its crystallographic structure. Calculating this angle involves understanding the geometric and crystallographic principles that govern the formation of the V-groove. This knowledge is essential for ensuring that the groove dimensions are accurate and can accommodate the optical fiber with the required precision. Mastery of these calculations ensures that the etching process results in grooves that meet the high precision standards necessary for effective optical fiber alignment.
Determine the V-Groove Dimensions:
If the center of the optical fiber core is to be aligned exactly on the surface plane of the silicon, it is necessary to calculate the depth hhh and the width www of the V-groove. This requires a detailed understanding of the geometric relationship between the groove dimensions and the diameter of the optical fiber. For instance, with a fiber diameter of 160 µm, the depth and width of the V-groove must be precisely calculated to ensure that the fiber is correctly positioned and securely held in place. This step involves applying trigonometric principles and considering the etching characteristics of silicon. Ensuring the correct dimensions are critical for achieving the required alignment precision and for maintaining the integrity of the signal transmission through the optical fiber.
Calculate Etching Time:
Given the etching rate of the KOH solution and the thickness of the silicon wafer, the total etching time needed to achieve the desired groove depth can be calculated. For example, if the KOH solution etches the {100} silicon at a rate of 2 µm/min and the wafer thickness is 500 µm, the total etching time can be determined as follows:
Etching time=Wafer thickness/Etching rate=500μm/(2μm/min)=250 min
This calculation ensures that the etching process is carefully timed to achieve the correct depth without over-etching, which could compromise the integrity of the V-groove and the alignment accuracy. Controlling the etching time is crucial for maintaining the precise dimensions required for optimal fiber alignment and signal transmission.
Assess the Alignment Accuracy:
Ensuring that the alignment process meets the required tolerance of less than 1 µm transverse error is crucial for the optimal performance of the optical system. This step involves fine-tuning the etching parameters, verifying the alignment using precision measurement tools, and possibly adjusting the process to account for any discrepancies. High-resolution imaging and alignment verification techniques, such as scanning electron microscopy (SEM) or optical microscopy, may be used to inspect the grooves and the placement of the fibers. Ensuring such high precision not only meets the immediate assignment requirements but also builds a strong foundation for future work in high-precision fields. Achieving this level of accuracy is vital for minimizing signal loss and ensuring efficient data transmission through the optical fiber.
By following these detailed steps, students can effectively approach assignments involving optical fiber alignment using micromachining techniques. Understanding the principles of anisotropic etching, the geometric relationships involved in V-groove formation, and the precision required for optical fiber alignment is crucial. This comprehensive approach not only aids in solving the specific assignment but also equips students with the skills needed to handle similar challenges in their future careers in telecommunications, photonics, and related fields. Mastery of these techniques will enhance their problem-solving capabilities and ensure they are well-prepared for the technical demands of the industry. Moreover, the knowledge gained from these assignments provides a strong foundation for innovation and advancements in the field of optical communications, paving the way for more efficient and reliable optical networks in the future.
Conclusion
Mechanical engineering students often face assignments that require a deep understanding of complex concepts and their practical applications. The examples of welding and optical fiber alignment highlight the importance of mastering theoretical knowledge and applying it to solve real-world problems. In welding, understanding the effect of heat intensity on interaction time and feed rate is crucial for selecting the appropriate welding technique and equipment. This knowledge not only ensures the structural integrity and efficiency of the weld but also enhances productivity and justifies equipment upgrades. Similarly, in optical fiber alignment, the use of advanced micromachining techniques such as KOH etching to create precise V-grooved silicon substrates is essential for achieving the high precision required for efficient signal transmission. By comprehensively understanding the etching process, calculating the groove dimensions and etching time, and ensuring alignment accuracy, students can effectively tackle assignments in this area and contribute to advancements in telecommunications and photonics.
These assignments serve as valuable learning experiences, teaching students how to approach complex engineering problems systematically. They develop critical thinking and problem-solving skills by breaking down the problem into manageable steps, applying mathematical and scientific principles, and verifying the accuracy of their solutions. These skills are not only essential for completing academic assignments but also for succeeding in their future engineering careers.
Moreover, mastering these techniques and concepts prepares students to innovate and address future challenges in the field. In welding, for instance, advancements in welding technology and automation require engineers to continuously update their knowledge and skills. Understanding the principles of heat intensity and feed rate can lead to the development of more efficient welding processes and equipment. In optical fiber alignment, the ongoing demand for higher data transmission rates and more reliable communication networks drives the need for precise and cost-effective alignment techniques. By mastering micromachining techniques and alignment principles, students are well-equipped to contribute to these advancements and improve the performance and reliability of optical communication systems.
In conclusion, assignments that involve welding and optical fiber alignment are critical for developing the skills and knowledge necessary for a successful career in mechanical engineering. By understanding the principles and applying them to practical problems, students not only excel in their coursework but also build a strong foundation for addressing the complex challenges of the engineering profession. These assignments foster innovation, enhance problem-solving abilities, and prepare students to make significant contributions to the field of mechanical engineering and beyond. Through continuous learning and application of these techniques, future engineers will be well-prepared to meet the demands of an ever-evolving technological landscape and drive progress in various industries.